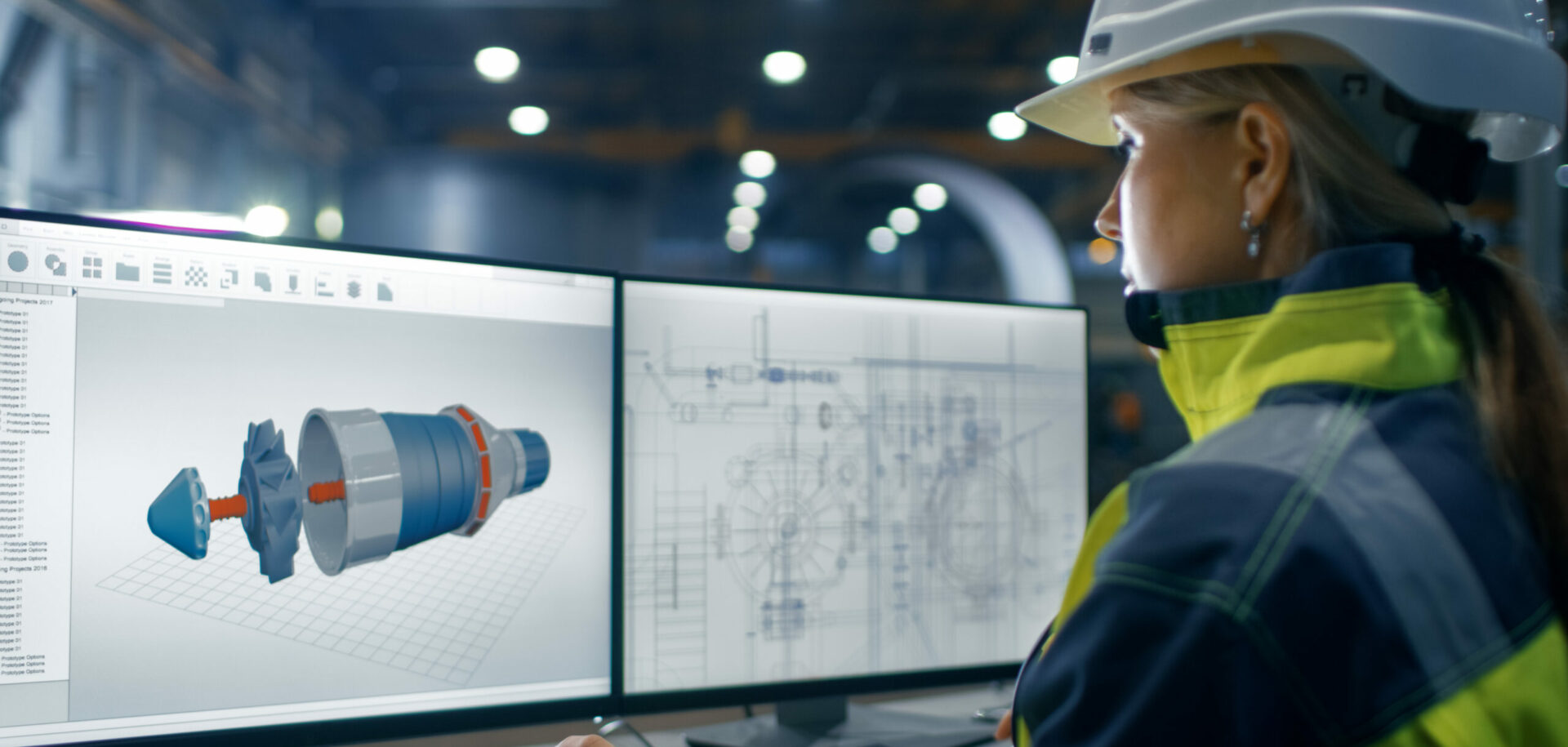
Bearings for high speed operations
Machine tool spindles should run with minimal runout, at high speeds with low temperature rise and have a high stiffness. Rolling bearings for machine tool spindles are made specifically for these requirementsThe never-ending pursuit of improved performance of machine tools leads to further development of the bearings. The requirements may in some cases be conflicting but, by carefully studying the behaviour of the rolling elements within the bearings, solutions may be found for simultaneous improvement of each performance parameter. Improved performance of the bearings will give higher machine tool productivity and more cost-efficient production.
Machine tool spindles should run with minimal runout, at high speeds with low temperature rise and have a high stiffness. Rolling bearings for machine tool spindles are made specifically for these requirementsThe never-ending pursuit of improved performance of machine tools leads to further development of the bearings. The requirements may in some cases be conflicting but, by carefully studying the behaviour of the rolling elements within the bearings, solutions may be found for simultaneous improvement of each performance parameter. Improved performance of the bearings will give higher machine tool productivity and more cost-efficient production.
Centrifugal loads
The rolling elements in a rolling bearing will be subjected to considerable centrifugal loads when the bearing is rotating at high speed. The load on the outer ring raceway will increase and on the inner ring raceway it will decrease. In the case of an angular contact ball bearing this will moreover result in a decreased operating contact angle at the outer ring and an increased angle at the inner ring. As the contact angles on the rings have thus become different, ball sliding must take place against one of the rings. As the outer ring ball load is heavier than the inner ring ball load the balls become outer-ring guided and the sliding takes place on the inner ring. The bearing stiffness will normally suffer at increased speeds due to this change in contact angles. The difference in contact angles is also influenced by the raceway radii and therefore these radii and their inter-relationship need to be evaluated. The centrifugal load and the contact angles in an angular contact ball bearing running at high speed are illustrated in figure 1.
Lighter rolling elements
In order to keep the centrifugal loads at a low level the balls of an angular contact ball bearing should have a small mass. A small mass can be obtained either by using smaller balls or by making the balls of a material with lower density or by a combination of both options. By reducing the diameter of a ball to 75 % (a real case) the mass will be reduced to 42 %.
Example
Bearing 7014 CD having a ball diameter of 12,7 mm is running at 15,000 r/min. The centrifugal load from each ball is then 174 N. If the ball diameter is reduced to 7,938 mm (62.5 %) the centrifugal load from each ball is 79 N, a reduction to 45 %.
The advantage of using small balls has been considered when designing the new series of SKF angular contact ball bearings, 719 CE and 70 CE. Figure 2 shows a comparison of the cross sections of angular contact ball bearings with ‘normal size’ balls, series 70 CD and the new ‘small ball’ series 70 CE.
Ceramic material for the rolling elements
By using a suitable material with lower density than bearing steel the same advantages can be gained as with using smaller steel balls. In actual fact there are additional advantages too. A material offering several interesting benefits in bearings for demanding tasks is silicon nitride. Silicon nitride is a ceramic material with the chemical formula Si3N4 and is today the ceramic material most commonly used for rolling bearings for both technical and economical reasons.
Bearings with only the rolling elements made of ceramics are mainly used for high speed applications.
Typical properties of silicon nitride are:
- low density, 40 % of that of steel
- small thermal expansion, 29 % of that of steel
- high modulus of elasticity, 151 % of that of steel
- great hardness, HV10 at 20 °C is 1,700 compared with 700 for bearing steels
- low friction
- withstands high temperatures without loss of hardness
- resistant to chemicals and corrosion
- non magnetic
- electrical insulator
These properties offer many performance advantages and will in many cases compensate for the higher initial cost of hybrid bearings compared with all steel bearings.
Rolling elements of silicon nitride will be subject to considerably lighter centrifugal loads than rolling elements of steel having the same size.
Example
Looking at the same bearing as in the previous example, having a ball diameter of 12.7 mm and running at 15,000 r/min, the ball centrifugal load with balls made of silicon nitride will be 71 N. This is a reduction to approximately 40 % compared with the steel ball design. It is evident that the centrifugal load is somewhat lighter than the load when using smaller size steel balls. It can then be anticipated that the ceramic balls will have about the same dynamic behaviour as the previously used smaller steel balls.
To further decrease the mass of the balls, the ceramic balls can be made with a smaller diameter. It is then natural to select the same diameter as the previously used smaller diameter steel balls. With the same bearing size and speed as in the previous examples the ball centrifugal load will now be 32 N, a reduction to 18 % of the original value 174 N. The magnitude of these centrifugal loads is illustrated in figure 3.
Practical tests have verified the gain in speed and reduction in running temperature that can be obtained by using lighter balls (either smaller steel balls or ceramic balls or smaller ceramic balls). The diagram in figure 4 shows the temperature increase of a spindle fitted with the same basic bearing arrangement û two bearings in tandem at each side of the spindle and a light preload.
The bearings are in the four cases:
- 71912 CD ‘normal size’ steel balls
- 71912 CE small size steel balls
- 71912 CD/HC ‘normal size’ ceramic balls
- 71912 CE/HC small size ceramic balls
The results with the small size steel balls and the ‘normal size’ ceramic balls are about the same, which was also expected considering the mass of the balls. However, if it can be supposed that there is a risk of preload increase due to increased temperatures, ‘normal size’ ceramic balls may prove to be superior to small size steel balls.
Considerable speed/temperature improvements can also be made with double direction angular contact thrust ball bearings containing ceramic balls. This type of bearing was originally designed for very high stiffness and is used in combination with cylindrical roller bearings. Therefore they already incorporate small balls and have traditionally had a steep contact angle of 60°. By decreasing the contact angle and using ceramic balls the bearing can better match the speed capability of cylindrical roller bearings usually found in combination with these bearing types.
The diagram in figure 5 compares the speed-temperature rise of different designs of the double direction angular contact thrust ball bearing under the same test conditions.
Stiffness and elasticity of the material
When a bearing is loaded, elastic deformations will take place in the contacts between raceways and rolling elements. The magnitude of these deformations depends on the material, the load, the type, size, form and number of rolling elements and the raceway form. Factors that are favourable for high stiffness are: large number of rolling elements, large contact area and high modulus of elasticity of the material.
The improved dynamic behaviour of bearings with lighter balls running at high speeds also has a positive influence on the stiffness of the bearing. The bearing stiffness will normally decrease with increasing speeds but this decrease is smaller when the bearing is fitted with lighter balls. The example in the diagram, figure 6, shows a comparison of bearings for a high speed internal grinding spindle. At a speed of 40,000 r/min the radial stiffness of a particular hybrid bearing has been reduced to 70 % of the static stiffness, while for a comparable bearing with steel balls the stiffness has been reduced to 61 %. The greater static stiffness of a bearing with ceramic balls is also apparent from this diagram.
The higher modulus of elasticity of silicon nitride than that of steel will give a bearing with ceramic rolling elements higher stiffness than a geometrically identical bearing with steel rolling elements. The increase of stiffness under static loading is about 10 %. With angular contact ball bearings running at high speeds the increase of stiffness will be greater due to the improved dynamic behaviour of the balls, i.e. the smaller change in contact angles.
The smaller deformation in the contact zone of the ceramic rolling element and the steel ring also means that the contact area will be smaller. Under the same external load, stresses will be higher and the fatigue life of the ring will be decreased. The basic dynamic load rating of a hybrid bearing is about 70 % of that of a steel bearing, provided that all dimensions are equal and that the same theory for fatigue of steel-to-steel raceway contacts can be used. To offset this reduction the raceways of a hybrid bearing could be made with closer conformities to obtain a larger contact area but this would then have a negative influence on the speed capability. For high speed bearings the reduction in centrifugal loading will more than compensate for the lower dynamic load rating, see figure 7.
A further performance improvement that has been shown in practical operation is that the service life of grease lubricated bearings with ceramic rolling elements is longer than that of the corresponding bearings with steel rolling elements.
Temperature differences and influence of material
In most applications the operating temperatures of inner and outer rings are different. Normally the inner ring is warmer than the outer ring. This means that the installed clearance will be reduced in operation. If the bearing is mounted with a preload, which is normal for a spindle bearing, the preload will increase in operation. Excessive preload will give high friction and high temperature which may further increase the preload.
When rolling elements having a smaller thermal expansion than the rings are used the increase of the preload will be smaller. If the temperature increase is above a certain level there may even be a decrease of the preload. Bearings with ceramic rolling elements having a thermal expansion only 29 % of that of steel rolling elements are thus much less sensitive to temperature differences between the rings.
Applications
Bearings with smaller and lighter rolling elements are today’s answer to the never-ending pursuit of higher spindle speeds, cooler running and even higher stiffness. These bearings are increasingly used in high performance CNC lathes, machining centres and high frequency internal grinding spindles. Bearings for internal grinding spindles are usually of a somewhat different design to bearings for lathes and machining centres as the operating conditions differ considerably.
Some examples of spindles are shown in figures 8 to 10.
The spindle in figure 8 is fitted with a set of two angular contact ball bearings with small steel balls at the work side, series 70 CE, and a single row cylindrical roller bearing at the drive side, series N 10 AK, allowing for thermal expansion of the spindle.
The spindle in figure 9 is fitted with a double direction angular contact thrust ball bearing with ceramic balls, series BTA A/HC, together with single row cylindrical roller bearings offering excellent stiffness.
The spindle on page 22 has a tandem set of angular contact ball bearings at each side. These bearings of series 70 CD/HC have ceramic balls.
Leif Lewinschal,
SKF Sverige AB,
S-415 50 Göteborg