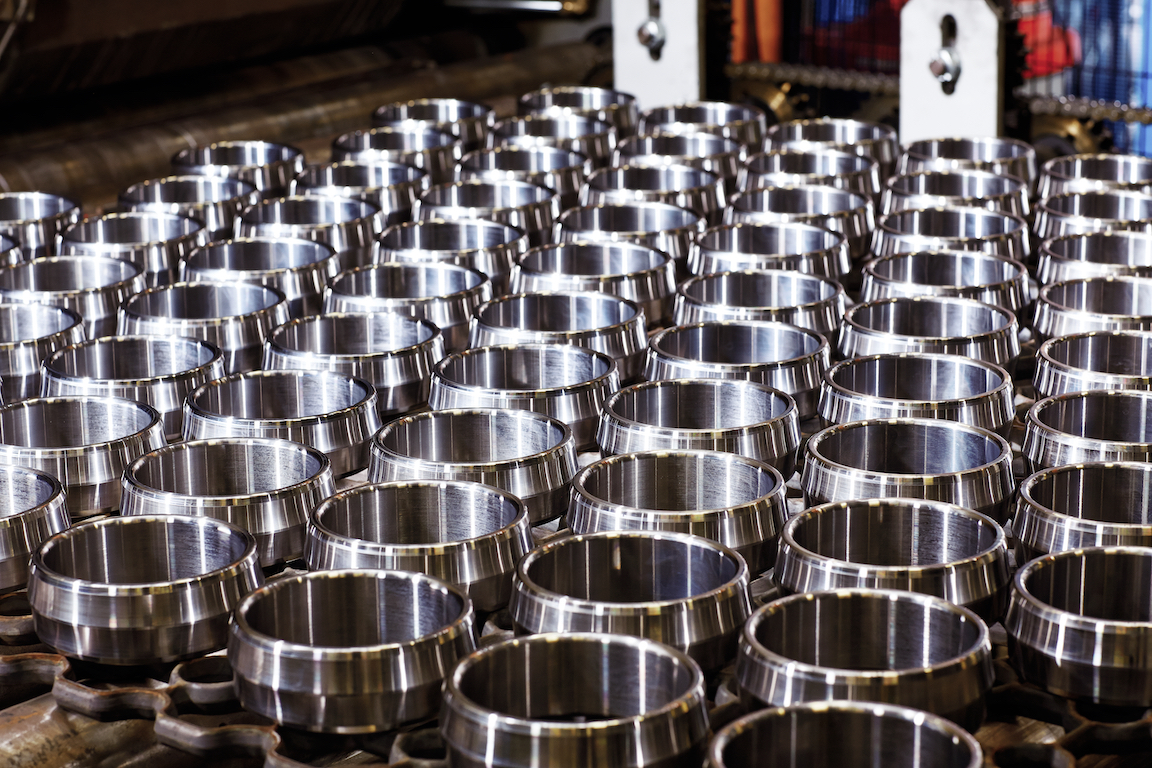
Summary
Technical collaboration
When Finnish design engineer Kimmo Laine came up with the idea of adding a large thrust bearing at the discharge end of the air end rotor to take the axial loads, one of the people who believed it would work was Göran Westerholm, area sales manager for SKF in Tampere, Finland.
SKF encouraged Laine and his team to try the new configuration and helped in calculating the shaft tolerances and designing the assembly tools. SKF also contributed lubrication and filtration know-how to the project.
This development work created the basis for the long-standing partnership that has evolved between Gardner Denver Oy and SKF. Today, SKF supplies the vast majority of the bearings used by Gardner Denver Oy. The main applications are air end rotors and compressor gearboxes.
Technical development work is one area where the two organisations regularly collaborate. At present Gardner Denver Oy and SKF are working on ways to upgrade their logistic functions. Improved logistics would enable Gardner Denver Oy to reduce its bearing stock levels.
SKF has a 50 percent market share for all types of bearing applications in Finland, and a 70 percent share of the market for spherical roller bearings, which are widely used in paper machines and other heavy industrial processes.
Gardner Denver Oy of Finland is a major supplier of screw compressors and compressor components. A cornerstone of this business was laid more than three decades ago with a design engineer’s bold idea to extend the lifetime of a critical bearing.Most industrial plants could not function without a reliable supply of compressed air. Used to power processes, equipment and tools, it has even been called the fourth utility after electricity, water and gas. In the majority of plants this vital utility is provided by a screw compressor.
The “heart” of the rotary screw compressor – the part that does the actual compressing – is the air end. Air ends consist of two precision-engineered rotors contained in an airtight housing. The rotors are driven at up to 10,000 rpm by an electric motor, causing atmospheric air to be sucked in through a filter, passed along the lobes of the rotors, compressed to the required pressure and released through a discharge valve. Oil is continuously injected into the air end to cool and lubricate the rotors and to create an air seal.
Gardner Denver Oy – the Finnish subsidiary of US-based compressor manufacturer Gardner Denver Inc – is one of the world’s leading supplier of screw compressor air ends. The Enduro brand air ends produced at the Gardner Denver plant in Tampere, two hours north of Helsinki, have set the industry standard for reliability and efficiency. In addition to building them into its own integrated compressor units, Gardner Denver Oy also sells the air ends as OEM components to some 70 other compressor manufacturers. More than 100,000 Enduro air ends are already in use around the world.
Increasing reliability
Some of the credit for this success must go to Kimmo Laine for work he did more than 30 years ago. At that time the compressor plant was owned by Tampella Corporation, and Laine was a design engineer. He had the idea of developing a new bearing configuration for air end rotors.
“Everyone knew that the rotor bearings were the weakest part of the air end. Back in the 1960s the rotor bearings had to be changed after about 20,000 hours, or some three years of operation. If a bearing failed, the entire air end had to be scrapped and replaced, which was very expensive,” explains Laine, who is now managing director of Gardner Denver Oy.
“The conventional arrangement was to use tapered roller bearings or angular contact bearings to support both the axial and radial loads. I looked at other machinery and I came up with a way to cut costs and possibly increase reliability. My idea was to add a thrust bearing at the discharge end of the rotor to take the axial loads only.”
Straightforward solution
“We developed a new solution, which added a set of angular contact ball bearings to support the thrust loads. The thrust bearings have a loose fit on the shaft, with the outer ring only axially in contact with the face of the roller bearing. The roller bearing only takes the radial loads.”
Like all the best ideas, the basic concept is straightforward. And like all the best innovators, Laine found his greatest difficulty was in convincing people that the idea was worth trying.
“It was quite a bold – even risky – idea. To be honest, a lot of people thought it was crazy, and they said it wouldn’t work. But it also looked as though it would reduce costs, and so we got the go-ahead to try it. It has turned out to be very successful, but back then we never imagined that it represented such a big advance,” he says.
This bearing configuration – together with other developments, including new steel compositions, advances in lubrication efficiency and more effective surface treatments – has increased the lifetime of rotor bearings to between 50,000 and 100,000 hours, which is more than 10 years of continuous running.
These levels of reliability are important for industrial users, who seek to avoid unscheduled downtime. This is one of the factors that has helped Gardner Denver Oy to win market share in 65 countries around the world and increase its sales to more than 40 million euros. It has been a subsidiary of Gardner Denver Inc since 1997.
The integrated compressor units produced at the Tampere plant are fitted with four to 500 kilowatt electric motors to provide capacities of 0.5 to 73 cubic metres per minute at three to 13 bar. Typical customers include pulp and paper producers and steel mills.
Compressors are everywhere
“The majority of our compressors operate in industrial plants, but they can also be found in some quite exotic locations and applications. Our marine compressors even play a part in bringing fresh bananas to the shops. They power nitrogen generators on board specialised cargo vessels, creating a controlled atmosphere in the holds where the fruit is transported. This controls the ripening process, so the fruit is fresh when it arrives at the shop,” Laine says.
Railway braking systems represent an application where reliability is paramount. The brakes on trains are generally operated by compressed air, in systems that are designed to operate on a fail-safe basis. The compressor holds the brakes off, so if a malfunction were to occur anywhere in the system, the brakes would automatically be applied.
“Compressed air can even give nature a hand in making your skiing holiday a success,” Laine says. “Our compressors power many of the heavy-duty snow cannons operating at Alpine ski resorts.”
Peter Gregory
a business journalist based in Helsinki
photos gardner denver