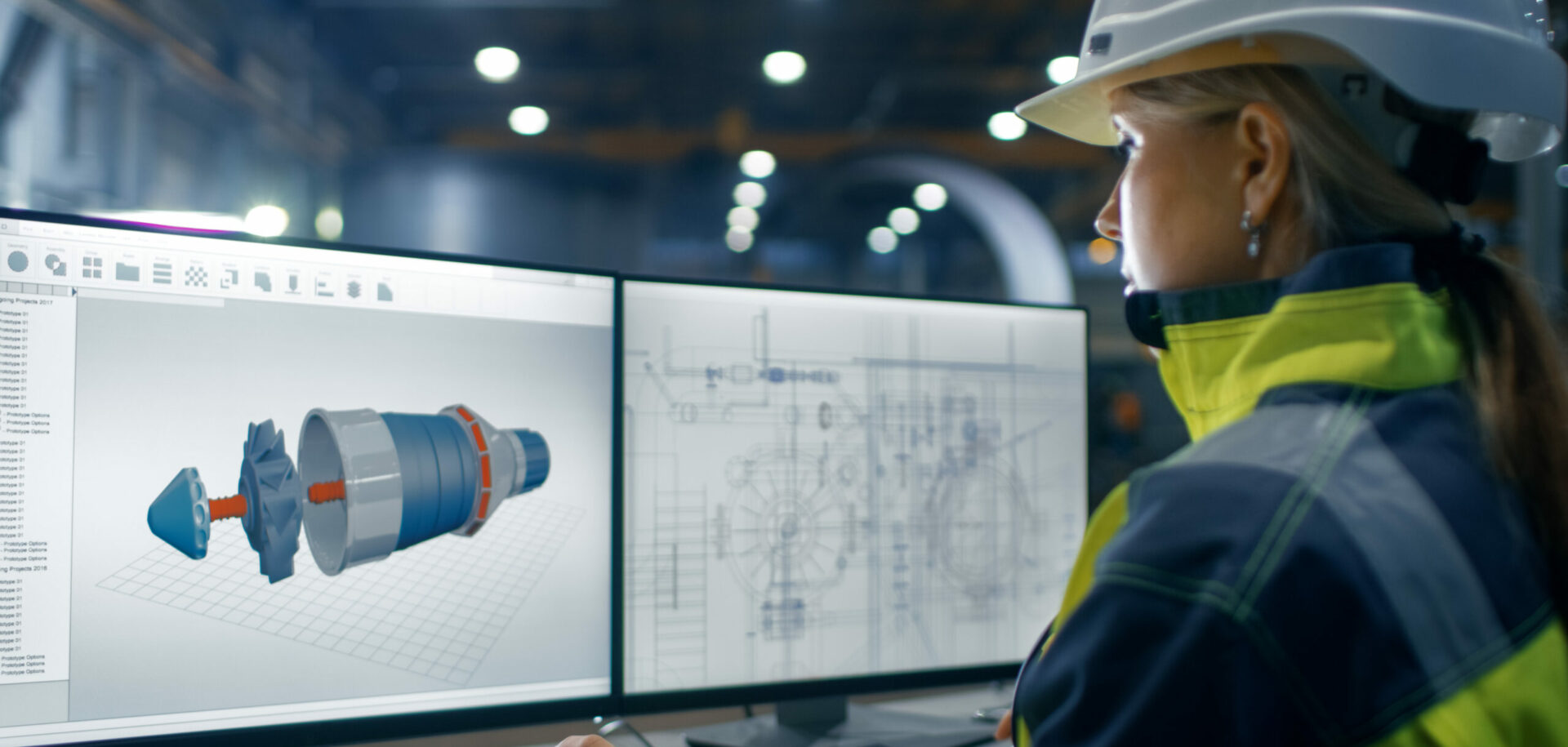
Breath of fresh air for automobile air conditioners
Customer demand has led to the development of a range of double row angular contact ball bearings for clutches in automobile air-conditioning systems.SKF has developed a new generation of air-conditioner double row angular contact ball bearings aimed at automotive applications. Designed for use in General Motors, Ford and Chrysler vehicles, these bearing arrangements have been designed for improved efficiency.
The double row angular contact ball bearing is located at the front of the air-conditioner compressor, where it supports an electromagnetic clutch that engages the compressor. The compressor processes the refrigerant required for cooling the vehicle. Currently SKF produces 2.6 million units at its plant at Altoona, Pennsylvania, in the U.S.
Typical operating requirements for these clutch bearings are speeds in the range 3,000 to 6,000 r/min and a radial load of between 450 N and 700 N. In many accessory belt-drive layouts, the air-conditioner compressor is situated low in the configuration. This means it is often subject to high ambient temperatures and high levels of contamination.
In 1994 SKF began collaborating with Harrison Thermal Systems, a division of Delphi – part of General Motors. The result was a new bearing type, the BA2-6508 clutch bearing. This is based on a double row angular contact ball bearing configuration because of this bearing’s ability to perform well with offset radial loads and the high-impact axial loading during engagement of the clutch. Another consideration in the choice of the design was the ability to control radial clearances to within very tight tolerances. The need to control tight internal radial and axial clearances is important in the reduction of pulley and compressor noise.
Customer approval
The SKF product team, which included the Automotive Division, the North American Technical Center and Altoona staff, completed its initial competitive analysis, prototype development and internal SKF lab testing in about 18 months. Field operating tests were undertaken by Delphi and took an additional 18 months.
Delphi approved the bearing in early 1997, certifying the BA2-6508 for direct use in new GM vehicles. To obtain this approval, the bearing had to pass a series of rigorous durability tests that included grease life and seal performance – dust intrusion, grease leakage, cold squeal and corrosion.
A particularly difficult challenge was Delphi’s high-speed durability test. This measures the bearing’s performance under extreme conditions. In this test, the outer ring spins at 9,000 r/min for 200 hours at an ambient temperature of 107 ºC. This simulates extreme operating conditions under the car bonnet, where temperatures often exceed 90 ºC. Another, longer-term performance assessment was the four-season test in which GM runs 50 air-conditioner compressors for a 12-month field test. The individual components as well as the entire bearing had to pass the GM test.
Selecting the appropriate grease was an important part of the design process. In particular, one of the key issues was to maintain compatibility with a new environmentally friendly refrigerant in the compressor. SKF designers opted to have Delphi field test more than one type of grease. The greases performed well and were approved. This approval became important when the first grease selected for the production bearing system exhibited stiffness and noise-related problems. The SKF Altoona plant was able to switch to the other approved grease and maintain its production schedule.
Broadening the range
Following its experience in developing air-conditioner clutch bearings for GM, SKF took the opportunity to further exploit its expertise in the compressor/fluid machinery areas. For example, to fully develop the market potential represented by the three largest U.S. automakers, SKF needed to develop specific bearing solutions for other vehicles. This resulted in three bearing types, the BA2-6508, BA2-6515 and the BA2-6517.
The BA2-6508 was designed in close cooperation with the vehicle manufacturer, but the two other bearings were designed to satisfy the application requirements of suppliers to automotive manufacturers. The result of this work means that SKF now offers bearings for three of the most popular air-conditioner clutches.
In addition, these new bearings are also competitive in a broad variety of air-conditioning rebuild operations and automotive aftermarket applications. Marketing channels include Chicago Rawhide and authorised SKF distributors as well as OE service companies. SKF plans to vigorously support the air conditioner clutch bearing market with an extensive communications campaign that highlights the fact that Europe now has a technically correct solution available.
At the same time, development of the product continues. As a sealed unit, the current design has an expected useful life in the range of 160,000 km. In future, the aim is to extend that to 240,000 km, while incorporating a smaller bearing arrangement to fulfil the needs of the trend towards smaller front-wheel-drive vehicles.
Art Mattson,
SKF USA Inc., Altoona, Pennsylvania, USA