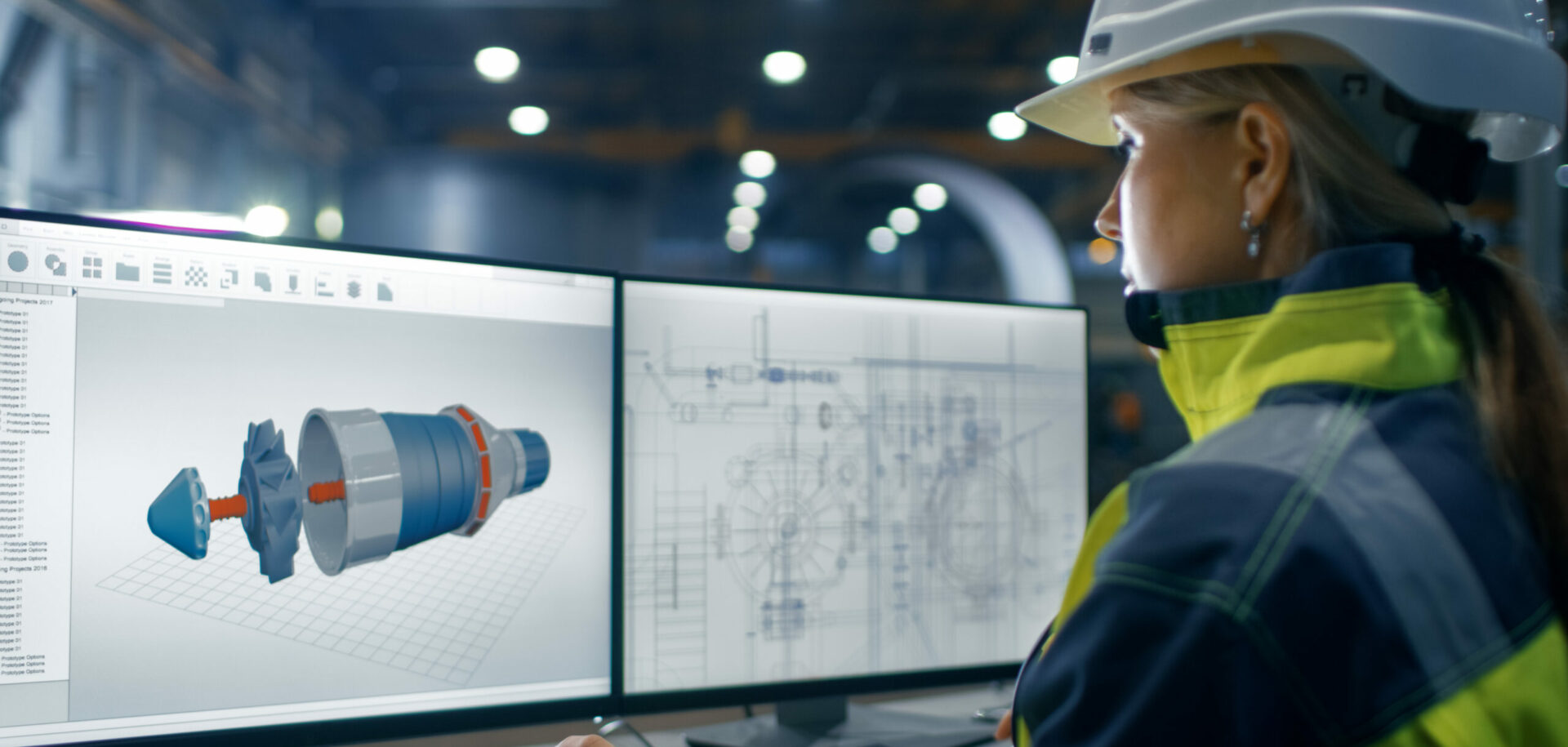
Building a Chinese brand
Guangdong Ganey Precision Machinery is offering customers the total cost advantage of high-quality air compressors with long service life and high energy efficiency.
Guangdong Ganey Precision Machinery is offering customers the total cost advantage of high-quality air compressors with long service life and high energy efficiency.
Situated in a newindustrial park in Shunde, about 50 kilometres from Guangzhou in southern China, Guangdong Ganey Precision Machinery Co Ltd has been propelled to the market by a desire for higher quality and greater innovation.
The private company is the brainchild of chief engineer Zha Shiliang, whose research in the 1980s led to the development in the 1990s of a single screw compressor prototype. But coming from an academic background, he needed financial support to translate his ideas into marketable products.
Entered Yang Guotian, an entrepreneur from the construction industry. With the local building boom reaching its peak, he was looking for a sustainable way to invest. “Many investors were lured by the real estate sector because you could make quick and easy money,” says Yang. “But I was interested in the long term.” Yang was particularly attracted by Zha’s
cutting-edge technology, which has the potential to supply high-end markets in power generation, coal mining, oil and gas, shipbuilding and food processing, as well as general manufacturing.
Compared with double screw compressors, the single screw compressors from Ganey have the advantages of less wear (which means a significant reduction of energy consumption), being more tolerant of harsh working conditions and providing longer service life. But they are more difficult to produce, due to the high precision required for the meshing of the screw and the gate rotor.
With its own new technology, Ganey was able to offer single screw compressors at about the same price as a double screw compressor. The company prides itself on its ability to show customers cost savings from technical innovations that also enhance the reliability of the machines.
“It took three years of product development and customer demonstrations before the market was ripe,” says Yang, who is president and managing director of Ganey, as he looks out from his brand new office toward the workshop in the 50,000-square-metre complex where the company relocated in September 2006.
In targeting themid- to high-end segment of the domestic air compressor market, Ganey was aware of the need to differentiate its products through higher quality. But by 2004 the number of returned compressors for repair was causing great concern.
“Aside from improper use, the most obvious cause was the bearings,” says Zha Qian, head of research and development. He and his father, Zha Shiliang, are part of the management team.
“I remember a surprising discovery,” he continues. “A technician called me one day and said he couldn’t believe the compressor he was servicing after 8,000 hours of operation had ever been used because the SKF bearings were like new, with no traces of wear!”
Ganey had known SKF from the beginning, but the general mindset of the management at the time was to supply a domestic product for the domestic market. Also, the price of an SKF bearing was higher.
“We had to control our product return rate, which was already much lower than our competitors,” explains Zha Qian. “Our reputation was at stake, and taking care of the returned compressors was drawing away our resources at a time when our sales had grown exponentially.”
Harry Li, senior sales engineerof the Guangzhou SKF representative office, was at hand to help. He arranged for a team of experts from SKF China, headed by senior application engineer Freddy Pan, to look at the situation, and he recommended SKF cylindrical roller bearings specifically manufactured for compressor applications.
The result was nothing short of amazing: The return rate dropped dramatically. Meanwhile, Ganey has adjusted its after-sales service with an emphasis on proactive maintenance for its customers. This has led to an increase in repeat orders.
“We send out service experts to all our key customers on a regular basis for early detection and correction of inadequate maintenance because a lot of machine failures are caused by improper use,” says Zha Qian.
“One coal mining customer even apologized to me before placing another urgent order, because his compressor had been abused for 18 months without any maintenance in the most difficult operating conditions!”
With the companyon a healthy growth path, Yang has been approached with the prospect of listing Ganey in the Growth Enterprise Market in China. “But we are not in a hurry at this point,” says he. “We would like to focus on perfecting the reliability of our products as we move from supplying the core machine to the whole system of single screw compressors. Our goal is to build a Chinese brand.”
The world’s largest single screw compressor
Since 2000, SKF China has been supplying various bearings and technical support to the Guangdong Ganey Precision Machinery Co Ltd, whose single screw compressors require a very high precision for the clearance between the shaft and the gate rotor.
The conventional method of measuring and matching each bearing, shaft and housing before assembly is timeconsuming, labour-intensive and costly. The SKF cross-section height method has proved to be a fast and cost-effective solution for matching the bearings for assembly.
In designing the world’s largest single screw compressor (with a capacity of 66 cubic metres per minute), engineers at Ganey applied the latest SKF software as an accurate and cost-effective method of bearing selection. The compressor was completed in July 2005 and has passed the 500-hour running test by the Chinese National Quality Assurance Authorities.