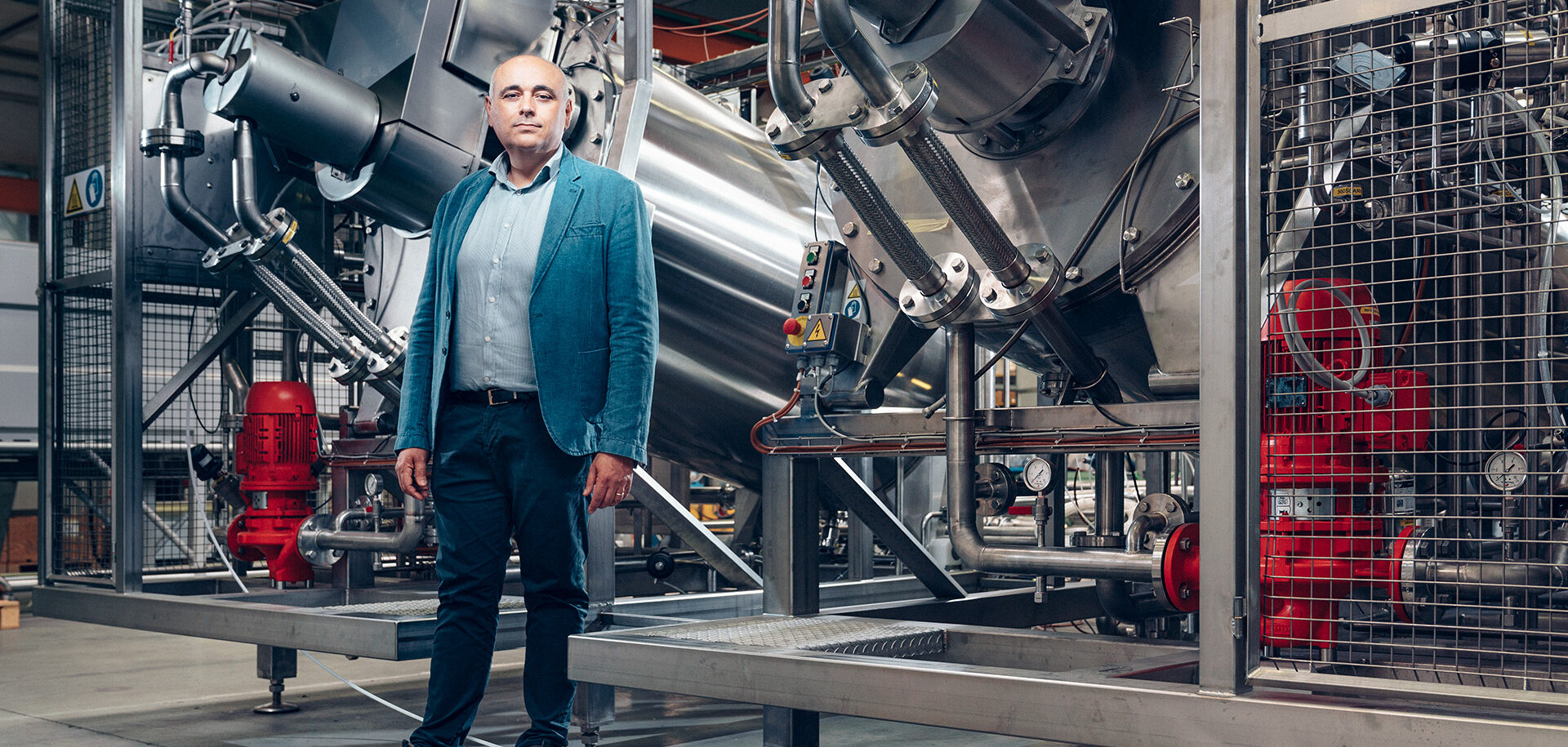
Chestnuts and flexibility – a winning recipe
Food processing is a competitive industry. A machine manufacturer must not only design top-notch equipment but must also adapt to new government regulations, changing consumer tastes and increased societal attention to health and hygiene.
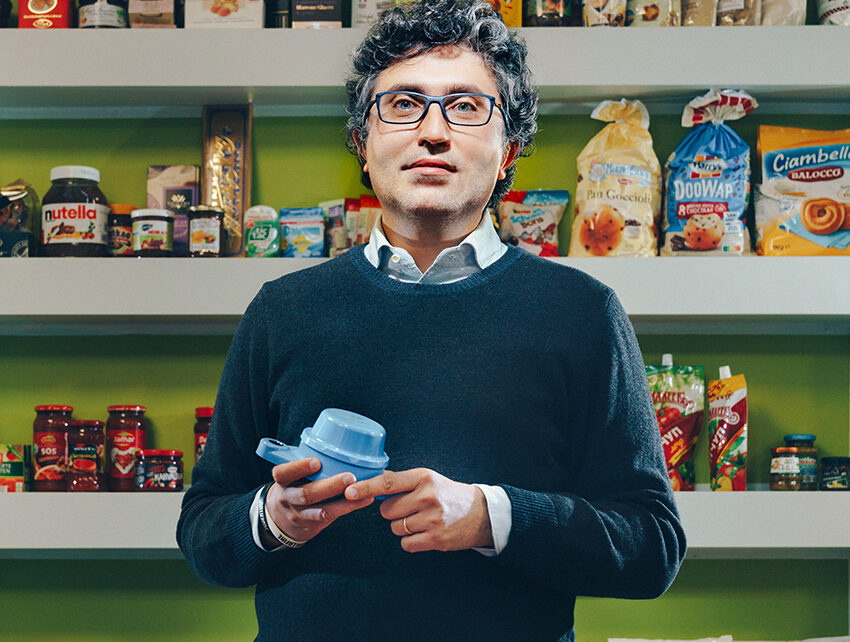
World leader in the sector
Bosio and Ponzo adopted a winning strategy from the outset, perhaps inspired by a line in the Act Two opening chorus of the opera: Caldi i marroni! (hot chestnuts!). They decided to focus on the peeling and processing of chestnuts, a heretofore ignored niche market, and invented machinery specifically for chestnuts. It became their calling card, and their designs for this machinery are still used today. “We are recognized as the world leader in this sector,” observes Marco Bosio, son of the co-founder and sales manager for the company.
However, chestnuts are seasonal, and seasonality limits growth, so the founders gradually expanded to non-seasonal secondary products such as purees, jams, frozen and fresh-cut food and baby food. To compete effectively, they offered not only technical skills, but also the ability to meet client expectations. “That is our ‘value-added’ today – knowledge of mechanical processes plus creativity plus intuition plus attention to the needs of clients in a variety of food sectors,” says Bosio.
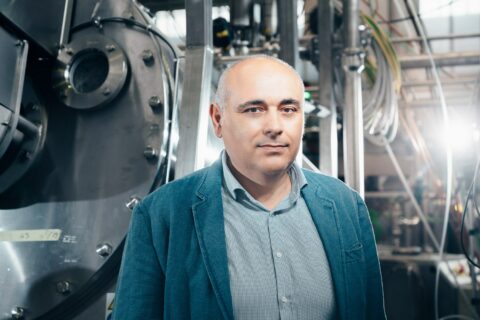
With these positive confirmations, we began to propose SKF Food Line ball bearing units to other clients.
Giovanni Icardi, technical manager, Boema
A more delicate handling of the product
Another step forward came when the company introduced steam peeling. Boema wasn’t the first to use steam in potato and vegetable processing, but the company’s solution allowed for a more delicate handling of the product, a competitive advantage for fruit.
In 1994 Boema opened a commercial office in Poland. It became a production centre in 2006 and has expanded several times, as has the original centre in Neive.
Bosio is optimistic about Boema’s future prospects. “People have to eat, so our market will continue,” he says. He cites the company’s strategy of ad hoc customized projects, calling it an advantage. “We mould every project to the specific needs of that client,” he says. “Our focus is not a single piece of machinery but a complete production line.”
He predicts that food-processing machinery in coming years will be more flexible, more hygienic and cleaner. It will be more automated and require less maintenance. And it will call for flexibility and creativity, exactly the qualities that have characterized Boema since the beginning. The applause will continue for this Italian opera.
Collaboration with SKF
One of the new products presented was the SKF Food Line ball bearing units, a series of bearing units launched that year designed specifically for the food industry. Its innovations were appealing to Boema: the bearings are completely sealed and certified to offer food protection as well as being maintenance-free and high-performing even in the toughest cleaning environments, and no relubrication is needed. No lubrication means that no worker is exposed to potentially dangerous situations working in wet, slippery environments while doing the lubricating. The chances for food contamination are also lowered.
Icardi appreciated the maintenance-free feature. “Today’s market wants only programmed maintenance,” he says. Another advantage of the relubrication-free bearings was greater freedom in designing machinery. Boema didn’t have to ensure access to apply a lubricant, and the client wouldn’t see grease dripping out in an unsanitary fashion.
Boema was guided during the maintenance-free solution implementation by Simona Allio of Application Engineering Italy. SKF application engineers, with their extensive technical knowledge, support the technical office to achieve projected targets.
In 2018 Boema tried SKF Food Line ball bearing units, sourcing through Crosa to ensure a trouble-free supply. They were used on a client’s peach-processing equipment. Peaches require delicate handling and frequent washings; a field test would show how well the line worked under the stress of real factory conditions.
After the first year, the client was pleased. For verification, Boema supplied line data and field samples to SKF that confirmed the performance of these bearings in operation. In another field test, bearing consumption was reduced by half.
“With these positive confirmations, we began to propose SKF Food Line ball bearing units to other clients,” Icardi says. “In this way we could transfer our validated know-how to our customers. Some of our clients then opted for this solution.”
At present, SKF’s Food Line ball bearing unit may be the only one of its kind in Italy. It has helped secure Boema’s position as a leader in the food-processing market and is a point of pride for the company.
For more on SKF Food Line ball bearing units visit: https://www.skf.com/group/industries/food-and-beverage/skf-food-line-ball-bearing-units
Download the PDF product catalogue here.