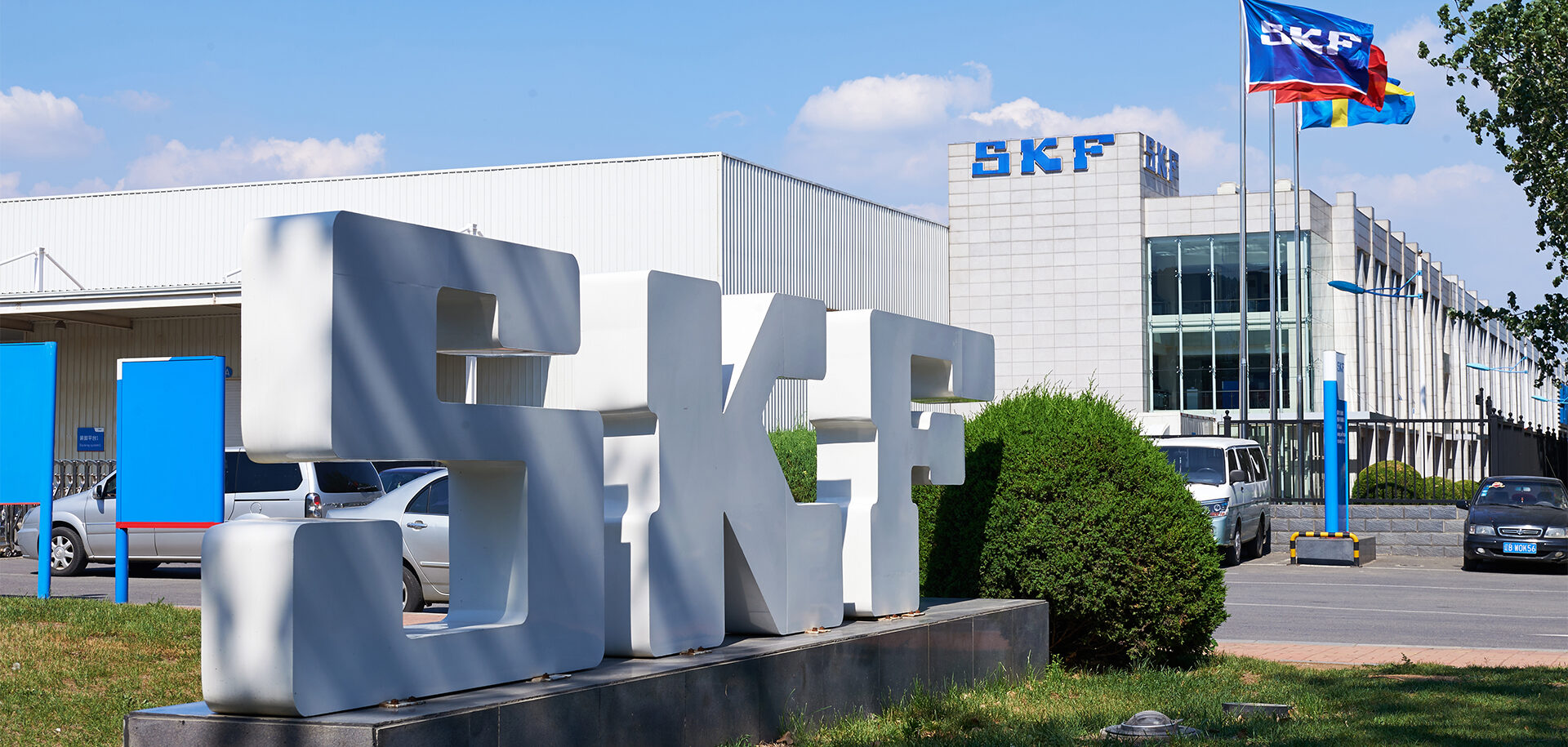
Collaboration to build a smart energy and carbon management system in China
A collaboration between Goldwind and SKF is pushing the frontiers of low-carbon manufacturing in Dalian, China.
The Beijing-based wind turbine manufacturing company Goldwind is one of the world’s major manufacturers of wind energy systems. More than 44,000 of its turbines are in operation around the world, with a combined generation capacity of more than 89 GW. Since the company was established in 1998 it has relied upon SKF as a supplier of critical components and expertise for those turbines.
The two companies share much more than a common interest in making reliable, efficient and cost-effective wind turbines, however. Goldwind is on track to become carbon-neutral at the operational level in 2022 and aims to make its core wind energy products 100 percent recyclable by 2024.
Both Goldwind and SKF are also committed to the idea that industry has a key role to play in addressing the global climate crisis. “We are striving to achieve net zero emissions in our own operations by 2030, and across our entire supply chain by 2050,” says Rob Jenkinson, net zero programme manager at SKF
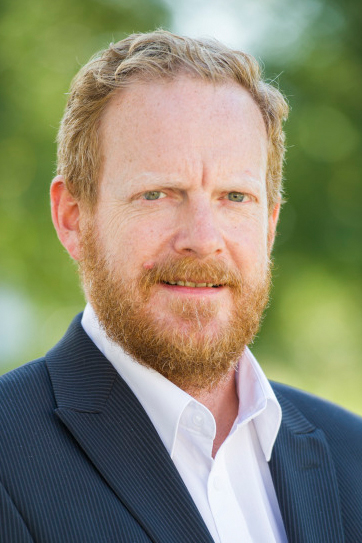
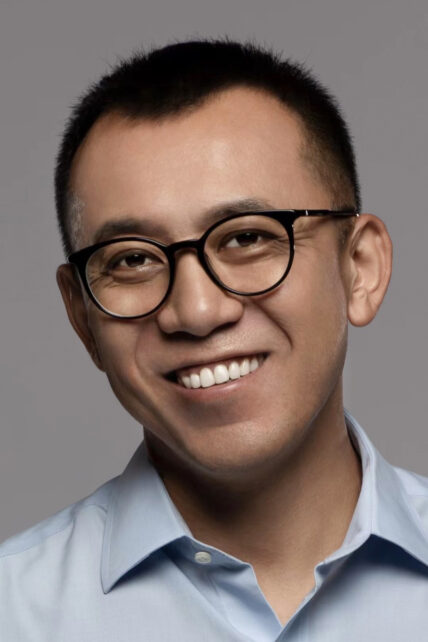
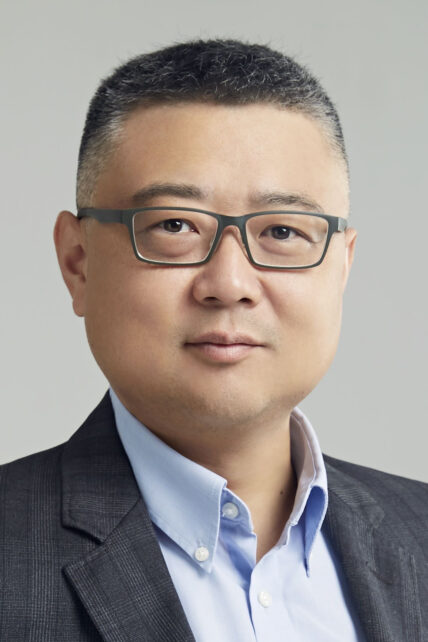
A centre for low-carbon production
Over the years, that alignment of interests has led Goldwind and SKF to develop an ever closer and more collaborative relationship, with each viewing the other as a long-term strategic partner. “SKF continues to help us improve the performance and competitiveness of our products, and we are helping SKF to transform its Dalian production site in China into a centre for low-carbon manufacturing,” says Hu Jiang executive director and general manager of Beijing Etechwin Electric Co. Ltd., a wholly owned subsidiary of Goldwind.
The journey towards carbon-neutral manufacturing at SKF’s factory in Dalian, in northeast China, is a large-scale effort, involving the purchase of renewable energy to power the plant, reconfiguration of its supply chain and adoption of energy-efficient production processes across its operations.
It is the third of those elements – energy- and carbon-efficient production – that is the focus of SKF’s latest collaboration with Goldwind. The Dalian plant already has a strong foundation in the principles and practice of energy-consumption monitoring; for many years the plant has operated an ISO50001-compliant energy management system. But the site’s managers recognized that its ambitious goals for continuous energy-efficiency improvement called for more detailed, accurate and timely data on energy consumption at the site.
More data, more insight
Monitoring and managing energy flows in complex and changeable environments is something the wind energy industry does every day, and Goldwind has developed sophisticated software designed for the purpose. “We believe that our approach could have applications well beyond the wind-power sector and have agreed with SKF to explore its potential in a manufacturing setting, using the SKF Dalian site as a pilot for a new energy and carbon management system,” says Hu Jiang.
We have agreed with SKF to explore its potential in a manufacturing setting, using the SKF Dalian site as a pilot for a new energy and carbon management system.
Hu Jiang, executive director and general manager of Beijing Etechwin Electric Co., Ltd.
The development of the system was a truly collaborative effort, involving staff from the Dalian plant, teams from SKF’s Environmental Health and Safety (EHS), IT and digital manufacturing departments, and technology specialists from Goldwind. The system they created is designed to provide continuous, real-time tracking of energy consumption within the plant. More than 300 data collection points across the site enable the system to calculate energy use at the machine, process and whole-plant levels, while an array of analysis and diagnostic systems provide the tools to track energy consumption and carbon emissions, evaluate improvement initiatives and maintain high-efficiency production operations.
Implementation of the new energy and carbon management system was conducted under extremely difficult conditions. With the Covid-19 pandemic in full swing, city-wide lockdowns made travel between Goldwind’s Beijing headquarters and Dalian impossible for much of the time. SKF staff had to spend many hours online with their Goldwind counterparts, dealing with issues and solving problems.
Despite those challenges, the data collection hardware was installed successfully during March 2022, and the system went live at the middle of the year. It now operates continuously, collecting real-time data that is stored in a secure cloud-database. SKF personnel can access that data in multiple ways, from a high-level dashboard at HQ that displays overall consumption and improvement performance to machine-level alerts that inform operators if energy consumption increases beyond pre-set levels.
From reactive to proactive
“The introduction of the new system has transformed the Dalian plant’s approach to energy management from reactive to proactive,” says Thomas Zhao, director, Legal & Compliance and EHS at SKF in China. “Traditionally, for example, plant managers would only learn about abnormal consumption when they reviewed their monthly energy reports. They then had to spend time tracking down the root cause of the issue. Today, real-time alerts allow operators to intervene immediately, adjusting machine settings or performing maintenance to keep equipment operating at optimum efficiency.
The energy and carbon management system is also helping the Dalian site to plan and prioritize its ongoing efforts towards efficiency improvement. By auditing the energy data, the company can see exactly which processes and machines are the most carbon-intensive, allowing them to work on improvement projects with the highest potential to reduce emissions. Over time, SKF plans to use all this data to transform Dalian into a “zero carbon campus”.
“Further expansion of the system is already underway,” says Zhao. “As a next step, we have built digital links between the energy and carbon management system and the Dalian plant’s digital manufacturing system. That will allow us to calculate the precise energy use – and carbon footprint – of every product it makes.”
Following the successful launch of the energy and carbon management system at the Dalian plant, SKF and Goldwind are now planning to extend the approach to other SKF sites in China and beyond. The two companies are also exploring ways to extend their partnership in other areas. SKF will adopt carbon-neutral principles for the future production sites, which may rely on the collaboration experience with Goldwind.
“Our expertise includes experience of green energy trading and sustainable purchasing as well as knowledge of other low-carbon technologies, such as on-site solar energy generation and energy storage,” says Hu Jiang.
For its part, SKF is helping Goldwind to improve the life-cycle assessments of its products and to develop a cleaner, greener supply chain. And the two companies are working together to formulate new standards for the evaluation of carbon neutrality in wind energy supply chains and the development of industrial parks.
A fruitful partnership
SKF and Goldwind both want to play a role in addressing the global climate crisis. Together they have created a system that is designed to provide continuous, real-time tracking of energy consumption within SKF’s factory in Dalian, in northeast China.
The plant originally opened in 2006 and was expanded in 2009. The 50,000-square-metre facility specializes in the production of medium and large-sized bearings and is the company’s most energy-intensive production site in China.
Xinjiang Goldwind Science & Technology Co., Ltd., is in the sustainability business. The Beijing-based company, usually known simply as Goldwind, is one of the world’s major manufacturers of wind energy systems.