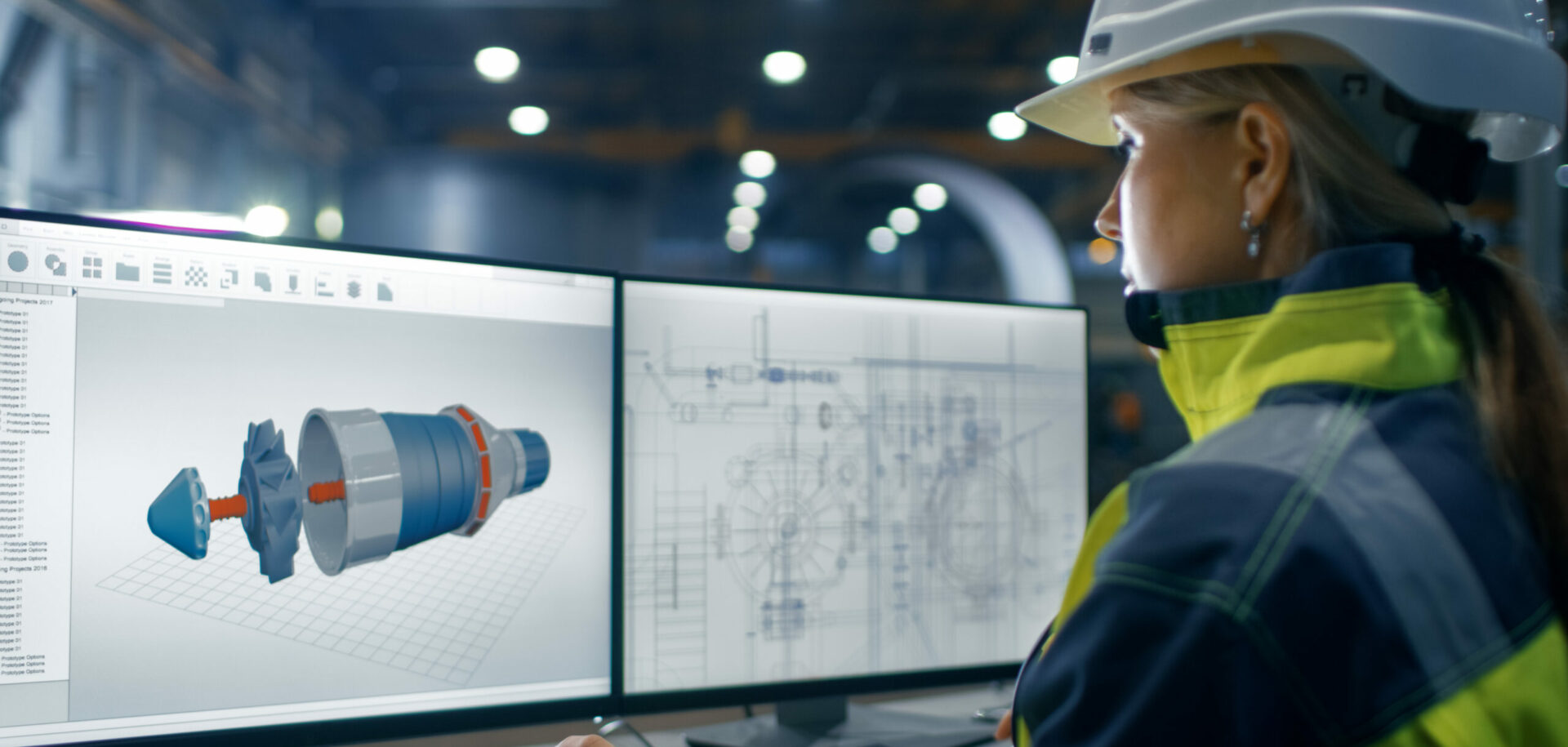
Cool airflow research
Summary
Adjustable test area
The geometry of the European Transonic Wind tunnel test area has to be adjustable to avoid pressure gradients. SKF makes the 36 planetary roller screws that modify the shape of the tunnel, allowing the top and bottom of the test area to be tilted slightly to ensure that pressure remains stable.
The screws vary in size from 15 to 150 millimetres in diameter. Perhaps even more important are the two roller screws, each 120 millimetres in diameter and 4.3 metres long, that move the structure that supports the model. All these screws have to work efficiently at minus 160 °C. SKF made them of maraging steel hardened by gas nitriding, and developed special lubrication for them.
Aircraft designers need to simulate airflow to measure the performance and safety of their models. To get accurate results, the tests must be done at temperatures of minus 160°C.The mood is intense, all eyes fixed on desktop computer screens or hanging video monitors. The only sound is the occasional click of a computer keyboard.
It looks like a small version of the NASA control room in Houston, where flight controllers handle hurtling spaceships tens of thousands of kilometres away. Here, too, the staff is controlling an object in an inhospitable atmosphere – nitrogen gas chilled to minus 160 °C – but the control room is in Köln, Germany, and the object is a stationary model aircraft in the next building.
This is the European Transonic Wind tunnel or ETW. It went into operation in 1993 as a cooperative effort of the governments of Germany, France, Britain and the Netherlands. Its purpose is to simulate the effects of flight for the purposes of aircraft developers.
Wind tunnels are the main method of testing the aerodynamic properties of an aeroplane before it’s built. But conventional wind tunnels, which blow air past a model aircraft, cannot accurately reflect one important parameter, the Reynolds Number (RN). The Reynolds Number is the ratio of inertial forces to viscous forces in the airflow – in essence, a measurement of the friction between air and aircraft.
This is a major influence on drag and handling, and also determines the characteristics of shock waves that occur as aircraft approach the speed of sound.
At ambient temperatures, a wind tunnel produces Reynolds Numbers that are considerably lower than in real operation. Raising the air pressure can raise values, but there’s a limit to how much pressure an aircraft model can stand. More accurate values can be obtained by doing the testing at reduced temperatures. But at the extreme temperatures needed, some components of ordinary air would become liquid, so another gas has to be used.
Luckily nitrogen behaves enough like air to be a good alternative. Luckily, too, the speed of sound goes down with temperature, so less power is needed to drive the fan that circulates the gas.
The ETW is one of two cryogenic transonic wind tunnels in the world. The other is the American National Transonic Facility (NTF) at NASA’s Langley Research Center in Hampton, Virginia, which went into operation eight years earlier.
Uso Walter, head of technical administration at the ETW, says that obtaining realistic Reynolds Numbers is essential for gauging safety and performance. “The McDonnell Douglas MD11 was built before there was reliable RN testing,” he says. “During its flight testing, it performed 9 percent worse than forecast. In my view, the cost associated with this problem after the plane had been built was one of the reasons the company eventually collapsed.”
The closed gas circuit has been designed for high – quality flow. To ensure that the gas flows into the test section as smoothly as possible, it passes first through a chamber with honeycombs and screens to reduce turbulence.
The tunnel is designed so that changes in temperature scarcely affect its geometry. The 2,500 – tonne stainless steel structure has only one fixed support, so that the rest of the tunnel can expand and contract freely in all horizontal directions. The pressure shell is insulated on the inside to minimise the effect of temperature changes on the steel, but most of the internal components are deliberately uninsulated so that they will respond quickly to temperature changes.
The aircraft models are characterless, with no windows or paint. Their surfaces appear shiny and smooth, but closer examination reveals hundreds of tiny holes, which allow assessment of the pressure distribution on the surface of the model. Inside the model and connecting it to the support is a “balance.” The name derives from the days when wind tunnel models were hung from wires, Walter says.
“In those days, the forces applied to the models were literally measured with decimal balances,” he says. “Nowadays, the balance is an electronic measuring device which records the forces exerted on the aircraft model by the flow of gas.”
Being able to calibrate the balance accurately for different temperatures is one of the central advantages of the ETW, and various balances are available to fit into the precise aircraft being tested.
The model is supported these days by one or two “stings,” rods attached to the rear or to the wings. The sting is attached to a movable plate that allows adjustment of the model’s angle of attack. The ETW also offers half – model tests, in which half a fuselage with one wing is fastened to the top wall of the test section.
By doubling the scale of the model, higher Reynolds Numbers can be reached and the new generation of larger planes can be simulated. The assembly is hung from a cart and moved through a dry air hall into a variable temperature room where both the cart and the model can be cooled down and made ready for the tunnel. Between tests, adjustments can be made in a special cold box in the variable temperature room, keeping the model cold while the engineers remain warm.
During a test run, the model is moved through various angles as the temperature, pressure and speed of gas flow are changed by fixed amounts. A test with a change in a single parameter is called a polar. Each polar lasts about a minute, and a model will typically remain in the tunnel for up to 90 minutes. It’s an expensive business: A model costs up to 750,000 euros (USD 670,000) and a series of tests lasting two weeks costs at least another EUR 500,000 (USD 450,000).
Three doors in the control room lead to three suites where data can be processed and the models mounted and adjusted. For the duration of a test series, a suite belongs to the customer. Entry to the suite and access to test data is only available to that customer and chosen ETW staff.
As many as three customers can use the tunnel at one time without any of them knowing what the others are up to. The control door is locked and the slatted blinds covering its window are drawn when a customer is running a test. One of the suites is even designed as a Faraday cage, to ensure that not even electronic snoopers can get at the data.
Walter says competitors haven’t often used the ETW simultaneously, but the design allows ETW staff to work on their own projects while customers are evaluating data or adjusting their models. But it’s important to convey a sense that security concerns are taken seriously.
“When Boeing first came to us,” says Walter, “their first question was not about science but about security.”
Michael Lawton
a business journalist based in Köln
photo Thomas Müller and ETW