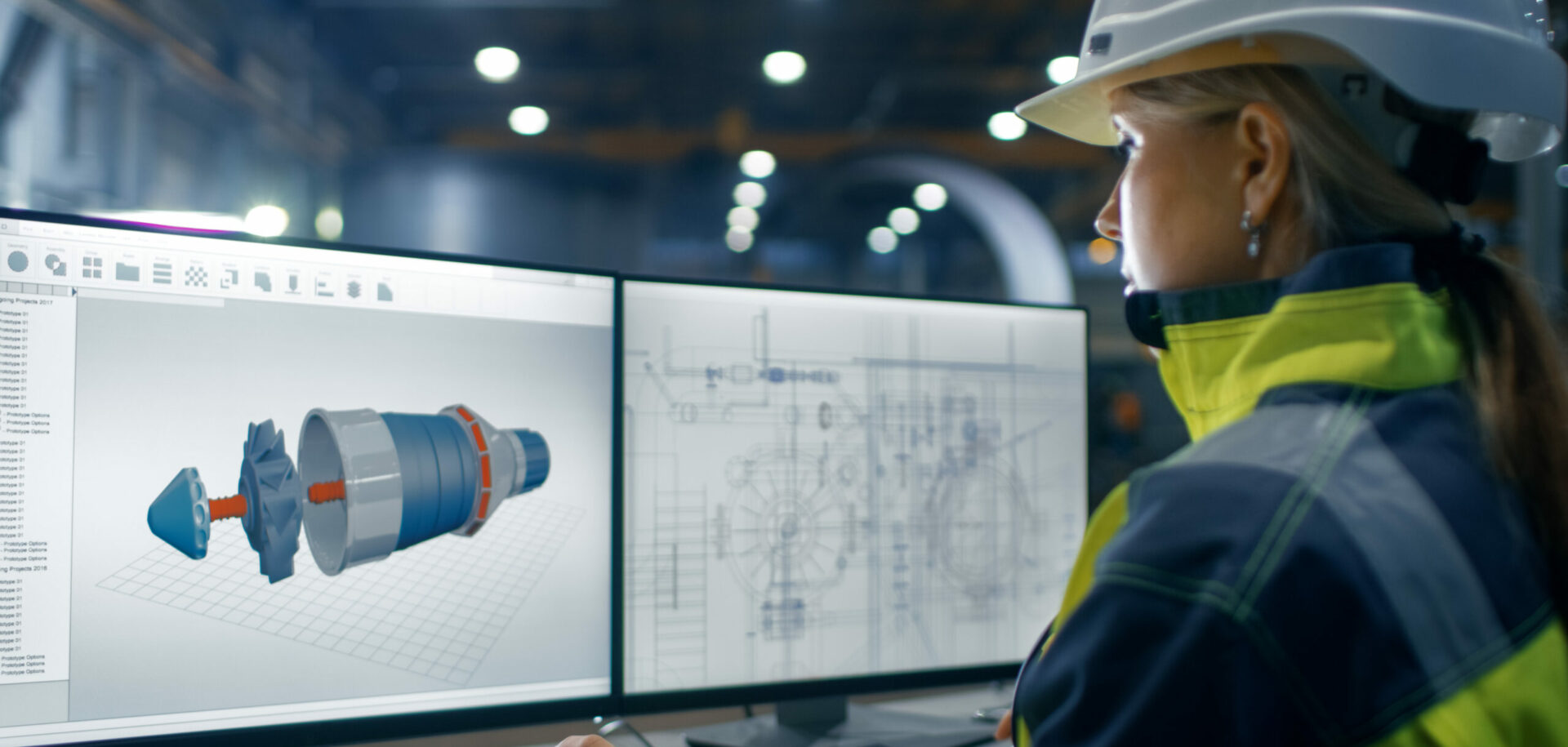
Höhere Zuverlässigkeit dank automatischer Schmierung
Automatische Zentralschmieranlagen für Baumaschinen im Hoch- und Tiefbau sowie im Mining-Bereich zahlen sich schnell aus. Eindeutige Vorteile sind das geringere Ausfallrisiko und die höhere Produktivität der Maschinen.
Automatische Zentralschmieranlagen für Baumaschinen im Hoch- und Tiefbau sowie im Mining-Bereich zahlen sich schnell aus. Eindeutige Vorteile sind das geringere Ausfallrisiko und die höhere Produktivität der Maschinen.
Technik
Die exakte Termineinhaltung der Projekte in einem engen Zeitfenster wird im Hoch- und Tiefbau immer entscheidender. Deshalb müssen Baumaschinen sommers wie winters „topfit“ sein, um jederzeit zuverlässig ein hohes Maß an Produktivität zu erzielen. Andernfalls droht der Termin plan aus den Fugen zu geraten, meist mit dem Ergebnis unkalkulierbarer Folgekosten. Das ist besonders unerfreulich, wenn der Ausfall der Baumaschine auf Mangelschmierung oder schadhafte Dichtungen zurückzuführen ist.
Reibungsbedingter Verschleiß sowie Korrosion und Schmutz setzen den mechanischen Komponenten erheblich zu. Dagegen gibt es aber ein probates Mittel: Perfekt angepasste Zentralschmieranlagen, die mit dem richtigen Schmierstoff in der richtigen Dosierung zur richtigen Zeit die richtige Stelle automatisch schmieren und schützen. Welches System sowohl ökonomisch als auch ökologisch die besten Ergebnisse liefert, hängt nicht zuletzt vom Maschinentyp und den jeweiligen Umgebungstemperaturen und Einsatzbedingungen ab. Idealweise kommen deshalb maßgeschneiderte Lösungen zum Einsatz.
Die von SKF entwickelten Zentralschmieranlagen für Baumaschinen verfügen dank ihrer robusten Bauweise über eine hohe Funktionssicherheit. Eingesetzt werden Kolbenpumpen der Baureihe KFG(S) mit integrierter Steuerung (Bild 1). Die Schmierstoffverteilung erfolgt über so genannte Progressivverteiler. Sie führen die jeweils erforderliche Schmierstoffmenge den zu schmierenden Stellen nacheinander zu und stellen dabei sicher, dass jede Schmierstelle optimal mit Schmierstoff versorgt wird.
Einfaches Überwachungsverfahren
Damit sich der Betreiber jederzeit einen Überblick über den aktuellen Füllstand des Pumpenbehälters verschaffen kann, hat SKF den quasi analogen Füllstandsschalter entwickelt. Er erfasst die Veränderung des Füllstands digital und zeigt sie in analogen Schritten an, z.B. in Abstufungen von 0,5 l. Diese Technik ermöglicht es dem Baumaschinenführer rechtzeitig und bei passender Gelegenheit, beispielsweise in den Arbeitspausen zwischen den Maschineneinsätzen, für das Nachfüllen des Behälters zu sorgen. Bei konsequenter Signalauswertung kann sogar der Schmierstoffverbrauch ermittelt werden. Treten starke Abweichungen vom Normalverbrauch auf, kann eine Serviceaufforderung aktiviert werden.
Zur Steuerung von Progressiv-Zentralschmieranlagen hat SKF mit dem Basisgerät IG502 ein universelles und doch einfaches Steuerungskonzept entwickelt. Zur Fachmesse Bauma 2010 stellte SKF nun das neue Steuergerät LC502 vor, das sich durch eine Reihe neuer und verbesserter Funktionen auszeichnet (Bild 2). Obwohl das IG502 als Standardgerät nach wie vor angeboten wird, wird sich das neue LC502 mit seiner Vielzahl an neuen Optionen ein breites Einsatzfeld erschließen. Hervorzuheben sind die neuen Steuermöglichkeiten anhand verschiedener Parameter. Die Steuerung kann jetzt auch in Abhängigkeit von der Pumpendrehzahl erfolgen und nicht mehr nur zeitabhängig nach Minuten. Dies hat den Vorteil, dass Drehzahlschwankungen der Pumpe und die damit verbundenen Änderungen der Fördermenge nun berücksichtigt werden können, was bisher bei der rein zeitabhängigen Steuerung nicht möglich war.
Drehzahländerungen können sich aufgrund von thermischen oder viskosen Vorgängen, Spannungsschwankungen und aus anderen Gründen ergeben. Eine genaue Verteilung des Schmierstoffs ist besonders wichtig bei Schmierstellen mit geringem Fettbedarf und entsprechend geringen Dosiermengen.
Ebenso punktet das neue Gerät auch hinsichtlich der Zuverlässigkeit der Schmierung, da es bis zu drei Schmierkreise überwachen kann. Es verfügt außerdem über eine Drahtbruchüberwachung und einen internen Überlastschutz.
Für große Baumaschinen, bei denen das Schmiersystem in mehrere voneinander unabhängige Schmierkreise aufgeteilt werden muss, haben die SKF Techniker auch ein neues 5/4-Wegeventil entwickelt (Bild 3). Es besitzt einen Eingang, der zu jeweils einem von vier Ausgängen geschaltet werden kann. So können bis zu vier Schmierkreise voneinander unabhängig mit Schmierstoff versorgt werden und mittels einer separaten Steuerung überwacht werden. In Verbindung mit der CAN (Controller Area Network)-Bus-Technologie ist eine weitere Optimierung der Schmierung von Baumaschinen möglich, da sich das Zentralschmiersystem in das bordeigene Kommunikationsnetz der Baumaschine einbinden lässt. Hierzu sind natürlich entsprechende Vorbereitungen seitens der Hersteller erforderlich, eine einfache Nachrüstung vorhandener Maschinen ist nicht praktikabel.
Um den hohen Anforderungen bei der Schmierung von Großmaschinen, wie sie etwa im Bergwerks-Bereich eingesetzt werden, hinsichtlich Schmierstoffvorrat, -verbrauch und großen Leitungslängen gewachsen zu sein, hat SKF das Pumpenaggregat vom Typ FK entwickelt. Dieses ist modular aufgebaut, verfügt über eine robuste Konstruktion und zeichnet sich durch eine hohe Funktionssicherheit aus, selbst bei Verwendung von hochviskosen Schmierstoffen. Es ist ausgelegt für einen Betriebsdruck von bis zu 400 bar (40 MPa). Das Besondere an dem Pumpenaggregat FK ist, dass der Kunde sich bei der Bestellung sein Aggregat so zusammenstellen kann, dass es dem gewünschten Einsatzzweck optimal gerecht wird. Der Schmierstoffbehälter wird in den Größen 15 kg, 30 kg oder 60 kg geliefert. Die Schmierstoff-Fördermenge kann stufenweise von 12 bis 74 cm3/min gewählt werden. Die elektrische Versorgung in VAC oder VDC ermöglicht es, das Pumpenaggregat FK in alle gängigen mobilen oder stationären Systeme einzubinden.
Einfache Nachrüstung
Baumaschinen ohne Zentralschmieranlagen können mit relativ geringem Aufwand nachgerüstet werden, wenn die dazu notwendigen Bausätze zum jeweiligen Maschinentyp passen. Diese Anforderung erfüllen die Nachrüst-Kits von SKF. Sie wurden nach den Vorgaben der jeweiligen OEMs gefertigt und erfüllen deren Anforderungen sowie deren Wartungsvorschriften. Die Bausätze sind in verschiedenen Ausführungen erhältlich; dies gilt auch für die Reparatursätze. Damit das Nachrüsten oder die Reparatur ohne Komplikationen durchgeführt werden kann, liefert SKF nicht nur den kompletten Bausatz mit allen erforderlichen Bauteilen, sondern auch die Pläne und Installations- bzw. Wartungsanleitungen zur Montage eines Zentralschmieranlagen für den jeweiligen Baumaschinentyp. Auf Wunsch kann die Montage auch durch die SKF Servicetechniker erfolgen.
Autonome Schmieranlage für Hydraulikhämmer und andere Anbaugeräte
Hydraulikhämmer benötigen einen anderen Schmierstoff als die übrigen Schmierstellen eines Baggers. In der Praxis verwenden die Kunden dieses Anbaugerät unabhängig vom Trägergerät. So hatten die SKF Techniker die Aufgabe ein Pumpenaggregat zu entwickeln, das nicht nur autonom und platzsparend, sondern auch wartungsarm ist. Das Ergebnis ist die HS04, eine hydraulisch betriebene autonome Schmieranlage zur zuverlässigen Versorgung mit Spezialschmierstoffen, so genannten Meißelpasten, mit hohem Feststoffanteil, die die Hydraulikhämmer benötigen. Die Schmieranlage wird direkt auf das Werkzeug montiert und in das vorhandene Hydrauliksystem der Maschine eingebunden. Sobald das Werkzeug zu arbeiten beginnt, d. h. das Hydrauliksystem aktiviert ist, versorgt die Pumpe die angeschlossenen Schmierstellen mit Schmierstoff. Die Menge des geförderten Schmierstoffs ist einstellbar. Anstelle des herkömmlichen Fettbehälters ist die Schmieranlage HS04 mit einer praktischen Einschraub-Kartusche ausgestattet, die leicht ausgewechselt werden kann. Auch werden verschiedene Adapteroptionen von SKF angeboten.
Das technische Highlight dieser Schmieranlage ist ihr patentiertes hochentwickeltes Antriebssystem. Die Montage auf einem Hydraulikhammer stellt sehr hohe Anforderungen an eine Schmieranlage. Neben dem beim Betrieb anfallenden Schmutz und Staub muss die Anlage auch harte Stöße und extreme Schwingungen wegstecken können. Bei der Konstruktion der Schmieranlage HS04 hat man sich gegen eine mechanische Antriebstechnik, und für eine rein hydraulische Lösung entschieden, um den auftretenden Belastungen höchstwirksam entgegenzuwirken. Dieses Konzept hat seine Zuverlässigkeit inzwischen in zahlreichen Feldversuchen unter Beweis gestellt.
Diese Schmieranlage kann nicht nur bei Hydraulikhämmern eingesetzt werden, sondern auch bei anderen Anbaugeräten, denn wir haben es hier mit einem hydraulisch betriebenen autonomen, platzsparenden und wartungsarmen Pumpenaggregat zu tun. Viele Anbaugeräte und zusätzliche Werkzeuge für Baumaschinen verfügen über keine eigene Stromversorgung, sind hydraulisch betrieben und haben Schmierstellen, die unbedingt geschmiert werden müssen. Hierunter fallen Abbruchzangen, Sieblöffel etc. Die Schmieranlage HS04 ist eine hervorragende Lösung, um die Produktivität auch dieser Ausrüstungsteile sicherzustellen und zu steigern, da zur Schmierung nicht nur Meißelpaste, sondern natürlich auch Standardfette der NLGI-Klasse 2 verwendet werden können.
Praxiserfahrungen eines Kunden
Zentralschmierung trägt erheblich zur Reduzierung der Umweltbelastung bei
Wie groß ist denn der Nutzen für die Umwelt, wenn man eine Maschine mit einer Zentralschmieranlage ausrüstet? Um die Antwort auf diese Frage mit zuverlässigen empirischen Daten belegen zu können, hat sich Thilo Standhardt von der SKF an Andreas Englisch, den Technischen Direktor der Fa. Albert Weil AG in Elz (Hessen) gewandt. Die Fa. Weil, deren Flotte weit mehr als 50 Baumaschinen mit Einsatzgewichten von 3 bis 87 Tonnen zählt, ist seit vielen Jahren Kunde von SKF (Bild 4).
Dank der Praxiserfahrungen der Fa. Weil und der vorhandenen Parameter zum Fördervolumen von Zentralschmieranlagen konnte SKF die Schmierstoffeinsparungen bei zwei Referenzmodellen sehr genau bestimmen. Ausgewählt wurden ein kleiner Atlas 82E Radlader (Bild 5) und ein 45-Tonnen Hitachi ZX 470 Kettenbagger (Bild 6). Die Flotte der Fa. Weil umfasst 20 der kleinen Radlader und 28 Kettenbagger mit einem Einsatzgewicht von 15 bis 87 Tonnen.
Bei täglicher vorschriftsmäßiger Wartung beläuft sich die errechnete jährliche Schmierstoffersparnis durch automatische Zentralschmieranlagen auf ca. 28 % bzw. 668 kg für die betrachteten Maschinen innerhalb der gesamten Flotte.
Diese Berechnung basiert auf folgenden praxisnahen Annahmen:
-
8 Betriebsstunden pro Tag
-
5 Tage pro Woche
-
1 Hub aus der manuellen Fettpresse entspricht ca. 2 cm3
-
1 cm3 = 1 Gramm
-
Vorschriftsmäßige manuelle Fettschmierung = Fettpresse betätigen, bis sichtbar sauberes Fett an den Schmierstellen austritt.
Die Berechnung wurde wie folgt durchgeführt:
Fettverbrauch bei manueller Schmierung:
-
20 Radlader 1.132.800 cm3
-
28 Bagger 1.236.500 cm3
-
Pro Jahr: 2.369.300 cm3 (ca. 2.369 kg)
Fettverbrauch bei Zentralschmierung:
-
20 Radlader 752.600 cm3
-
28 Bagger 948.900 cm3
-
Pro Jahr: 1.701.500 cm3 (ca. 1.701 kg)
Unterschied zwischen manueller Schmierung und Zentralschmierung: 667.800 cm3 (rund 668 kg)
Bei der Zentralschmierung beträgt die Verbrauchsersparnis ca. 28 % im Vergleich zur manuellen Schmierung (668/2.369).
In der Realität ist die tatsächliche Schmierstoffersparnis bei den Baumaschinen der Fa. Albert Weil sogar noch größer, denn in der Praxis neigen die Baumaschinenführer dazu lieber einen Hub Fett mehr (weitere 20 %) als zu wenig in einen Schmiernippel zu pressen.