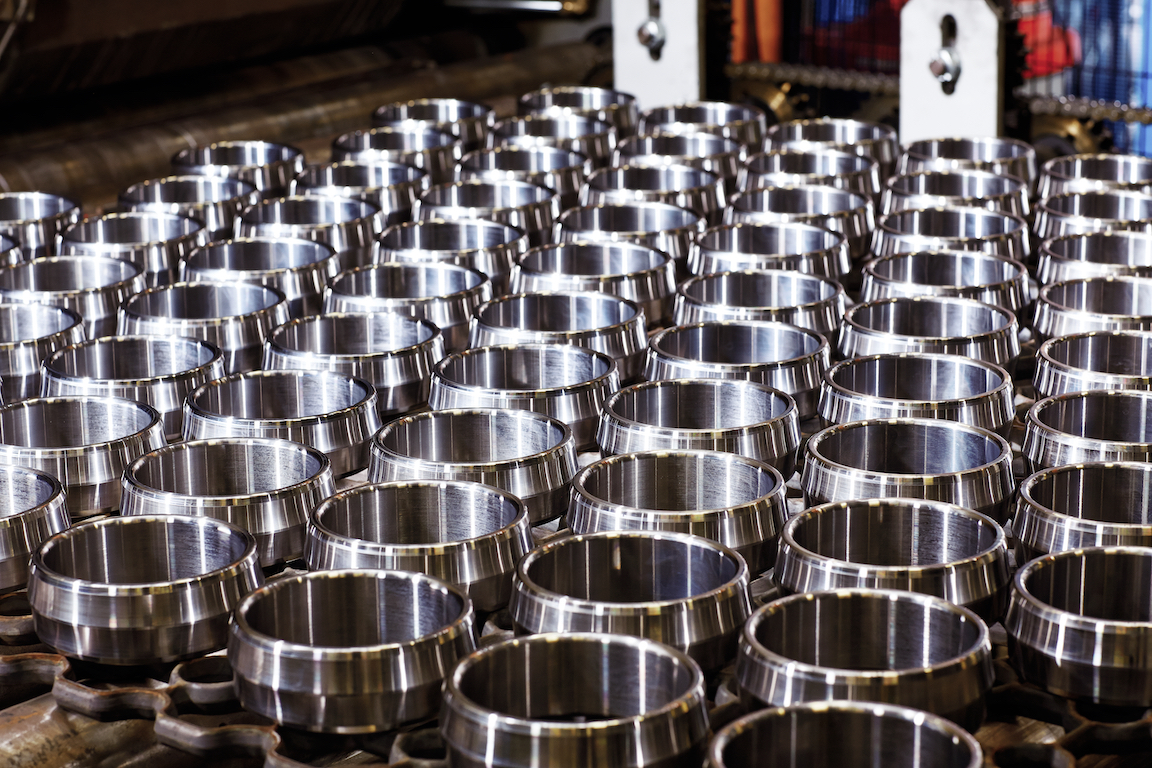
Effektiver Druck
Textilproduzenten im indischen Gujarat zeigen zunehmend Interesse an energiesparender Technik, um ihre Kosten zu senken und die Umwelt zu schonen.
Fakten
Der Sari
Es gibt über 80 Arten, einen Sari zu tragen. Die Vielseitigkeit und Anwendbarkeit dieses südasiatischen Kleidungsstücks ist einer der Hauptgründe, warum es seit der Indus-Zivilisation (2800 bis 1800 vor Christus) bis ins 21. Jahrhundert überlebt hat. Sein lockerer Sitz macht es zur idealen Kleidung für das heiße und feuchte Klima in vielen Teilen Indiens. Außerdem ist ein Sari ganz einfach schön. Obwohl sich indische Frauen vor allem in Städten oft westlich kleiden, ist der Sari immer noch für viele das bevorzugte Kleidungsstück. Die Bollywood-Filmindustrie hat dank Schauspielerinnen wie Aishwarya Raihas stark dazu beigetragen, dass der Sari weltweit bekannt ist.
Links
Ansprechpartner Verkauf
Marcel Soltermann, Marcel.Soltermann@skf.com
Der Textilmarkt im Stadtteil Bhadra der westindischen Metropole Ahmedabad besteht aus vielen engen Gassen mit kleinen Geschäften und Ständen. Hier wird alles feilgeboten, was irgendwie mit Stoff zu tun hat.
Mit einem Anteil von 30 Prozent an der indischen Textilfertigung produziert Gujarat die meiste Baumwolle von allen Bundesstaaten des Landes. Ahmedabad hat sechs Millionen Einwohner ist damit die größte Stadt in Gujarat. Sie ist seit dem 19. Jahrhundert das Zentrum der indischen Textilindustrie, weswegen sie auch als „ Manchester des Ostens“ bezeichnet wird.
Angesichts der wachsenden Sorge um die Erderwärmung – und um die hohen Energiekosten in Indien – stehen Energiesparmaßnahmen ganz oben auf der Tagesordnung der Textilfabriken. Ein Pionier bei der Entwicklung von energieeffizienten Verfahren ist Indian Textile Engineers, ein in Ahmedabad ansässiges Unternehmen, das Textildruckmaschinen für das Bedrucken von Textilien wie Saris oder Bettwäsche herstellt. „Unser Ziel ist es, den Energiebedarf unserer Maschinen kontinuierlich zu senken. Das wirkt sich positiv auf Umweltbelastung und Preisgestaltung aus.“, sagt Geschäftsführer Niki Thakore.
In herkömmlichen Textildruckmaschinen heben und senken Hydraulikzylinder die Druckplatten, die das Muster auf dem Stoff erzeugen. Die hohen Energiekosten sind nicht die einzige Umweltbelastung dieser Anlagen: Jede Maschine von Indian Textile Engineers verbraucht 400 Liter Hydrauliköl pro Jahr für den Betrieb der beiden hydraulischen Antriebe.
Vor einigen Jahren begann das Unternehmen, alternative Lösungen zu entwickeln.
„Mir kam der Gedanke, das hydraulische System durch elektromechanische Stellantriebe zu ersetzen“, erzählt Thakore. „Das erste Unternehmen, das mir dazu einfiel, war SKF.“
Hydrauliksysteme erfordern eine konstante Energiezufuhr, auch wenn die Antriebe nicht arbeiten. Elektromechanische Lösungen dagegen verbrauchen nur Energie, wenn sie in Bewegung sind. Bei der elektromechanischen Kraftübertragung ist kein Öl notwendig – das heißt weniger Ölverbrauch und keine Leckagen in den Maschinen und auf dem Boden. Gleichzeitig sorgt ein geringerer Geräusch- und Schwingungspegel für ein besseres Arbeitsumfeld der Maschinenbediener.
SKF und Indian Textile Engineers untersuchten zusammen eine Reihe unterschiedlicher Aktuatoren. Nach umfangreichen Testreihen fiel die Wahl auf den CASM Elektrozylinder von SKF, der für die im Textildruck benötigten schweren Lasten und hohen Geschwindigkeiten ausgelegt ist und die Produktivität erhöht. In einer Maschine wurden probeweise zwei CASM-Elektrozylinder installiert. Die Energieeinsparung war beträchtlich und wurde auf sieben Megawattstunden pro Jahr geschätzt. Das entspricht einem jährlichen CO2-Ausstoß von 5,3 Tonnen (nach der Berechnung mit den World Power Grid Mix CO2 Faktor von 0,749 kg CO2/kWh).
Als nächster Schritt wurde die Lösung bei einigen Kunden von Indian Textile Engineers getestet. Die Energieeinsparung belief sich auf circa 120 Euro pro Monat und Maschine. Bei rund 5.000 Maschinen, die in Indien im Einsatz sind, sieht das Unternehmen ein gewaltiges Potenzial für Energie- und Kosteneinsparungen. Darüber hinaus steigerte eine Textilfabrik in Ahmedabad nach der Umstellung auf CASM-Zylinder die Produktivität von 600 auf 850 Meter pro Stunde.
Dank der erfolgreichen Installation von 17 CASM Lineareinheiten für Indian Textile Engineers hat SKF 2012 eine Bestellung von weiteren 300 Elektrozylindern dieses Typs erhalten, die teils in neue Druckmaschinen und teils in bereits in Betrieb befindliche Maschinen verschiedener Textilfabriken eingebaut werden sollen.
Ein SKF BeyondZero-Produkt
Der CASM Elektrozylinder ist eines der ersten Produkte, die sich für das SKF BeyondZero-Programm qualifiziert haben. Das Programm umfasst Lösungen mit erheblichen Umweltvorteilen, die den Kunden helfen, ihre Umweltbilanz zu verbessern. Zu den extrem strengen Qualifikationsanforderungen gehören kundenspezifische Analysen und die Genehmigung durch den Vorstand. „An oberster Stelle steht der Umwelteffekt des Produkts, und zwar ohne irgendwelche Kompromisse“, sagt Mats Berglund, Projektleiter Group Manufacturing Development Centre bei SKF. „Das heißt, wenn wir im Laufe des Lebenszyklus eines Produktes etwas verbessern, darf nicht etwas anderes schlechter werden. Ein Beispiel wären negative Auswirkungen auf die Fertigung.“