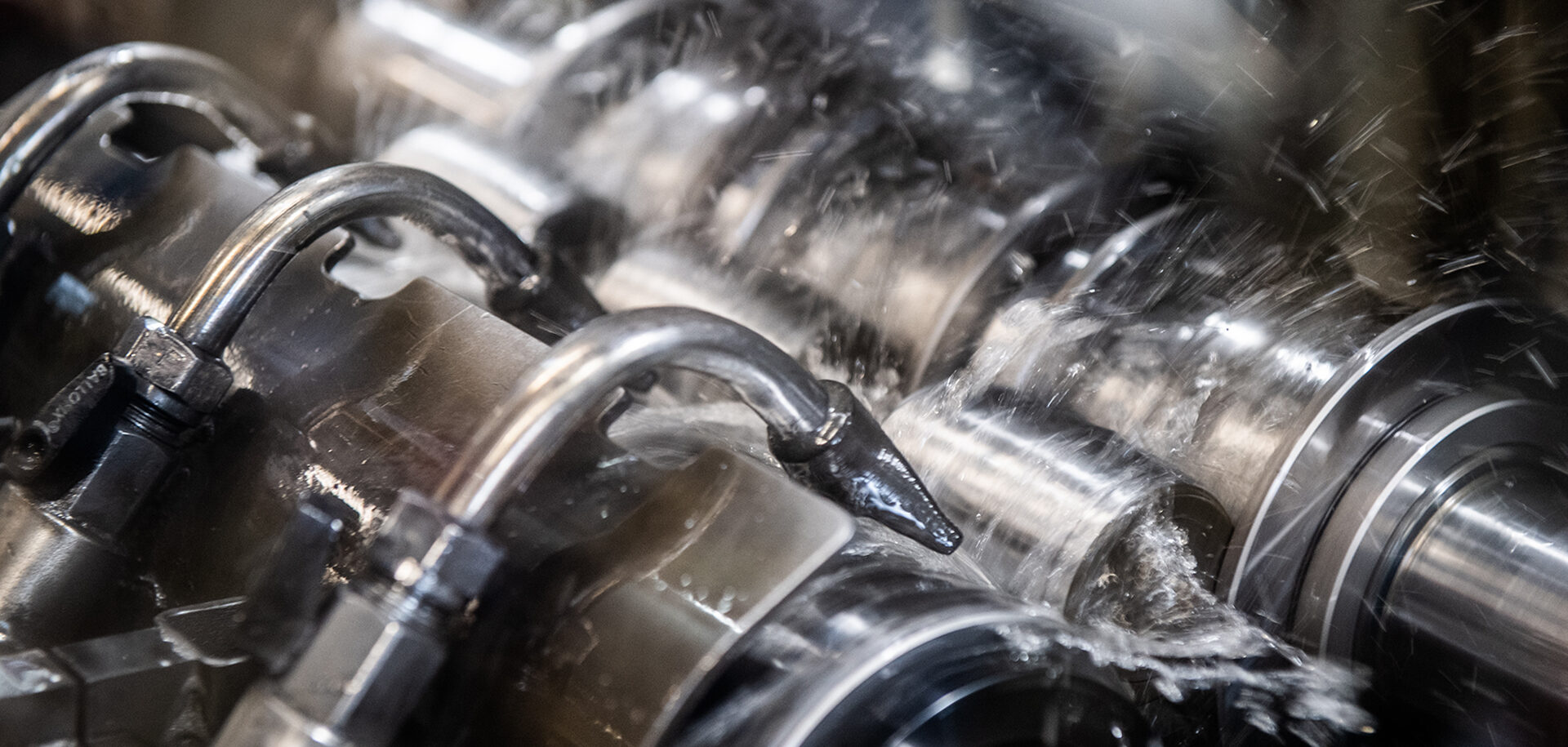
Ein sauberer Start für Hochleistungslager
Sauberkeit ist ein wesentlicher Faktor in puncto Lagerperformance und zuverlässigkeit. Im Kampf gegen Verunreinigungen ist Vorsicht immer besser als Nachsicht. SKF entwickelt seit Jahrzehnten saubere Herstellungsanlagen. Der Innovationsgeist reicht bis in die heutige Zeit: Mit der Übernahme neuer Technologien, die Verunreinigungen im Nanobereich eliminieren, wird die Lebenszeit von Prozessölen deutlich verlängert.
Schmutz ist der Feind aller Hochleistungskomponenten
Im Laufe der Zeit können Ablagerungen von Staub- und Schmutzpartikeln zu Oberflächenfehlern, Abnutzung und vorzeitigem Lagerausfall führen. Schlimmer noch, Verunreinigungen können bereits lange vor der Auslieferung an den Endnutzer Probleme verursachen.
Wenn Komponenten während der Herstellung nicht gründlich sauber sind, kann das die kritischen Hon- und Schleifprozesse in der Produktion beeinträchtigen, was zu mikroskopisch kleinen Oberflächenmakeln führt. Im Zuge einer umfangreichen Studie zu Herstellungsproblemen, die die Zuverlässigkeit und Performance von Lagern beeinflussen, fanden wir heraus, dass Sauberkeit der mit Abstand bedeutsamste Faktor war.
Saubere Prozesse helfen uns, Lager mit einer deutlich längeren und besser vorhersagbaren Lebensdauer herzustellen, die zudem niedrigere Geräusch- und Schwingungspegel aufweisen. Eine saubere Produktion sorgt für ein höheres und stabileres Qualitätsniveau, reduziert Abfall und befreit von unnötigen Herstellungskosten. In einer sauberen Umgebung halten auch die Herstellungswerkzeuge und Prozessflüssigkeiten länger.
Genau deshalb ist die Überwachung, Wartung und Verbesserung der Sauberkeit ein wesentlicher Aspekt des SKF Produktionssystems, neben effizienten Methoden zur Produktivitätssteigerung und rigorosen Prozesskontrollen.
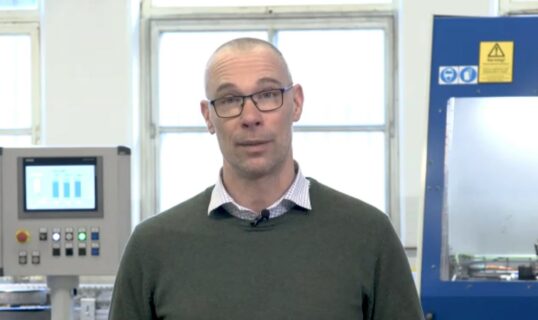
Eine saubere Produktion sorgt für ein höheres und stabileres Qualitätsniveau, reduziert Abfall und befreit von unnötigen Herstellungskosten.
Petter Hägg
Knowledge Area Manager für Clean Manufacturing bei SKF.
Eine saubere Einstellung
Um sicherzustellen, dass die Teile diesen Zielvorgaben entsprechen, müssen wir auf jedes Detail im Produktionsumfeld achten. Eine Komponente, die bis zur Weiterverarbeitung auf einer Werkbank liegt, sammelt beispielsweise nach und nach Staub und Schmutz aus der Umgebung an. Aus diesem Grund müssen wir uns Gedanken über die Bedingungen im Gebäude, die Leistungsfähigkeit des Belüftungssystems und sogar die Qualität des Deckenanstrichs machen. Wir müssen verstehen, wie viel Zeit zwischen den Prozessschritten vergeht und wie die Komponenten indessen gelagert und gehandhabt werden.
Die richtige Denkweise ist also genau so wichtig für eine saubere Herstellung wie alles andere. Die Fertigungsexperten von SKF verbringen viel Zeit damit, sich die kleinsten Details unseres Produktionsverfahrens anzusehen, potentielle Verschmutzungsquellen zu erkennen und nach Wegen zu suchen, diesen entgegen zu wirken. Diese Bemühungen weisen viele Parallelen mit den inkrementellen Techniken der kontinuierlichen Verbesserung auf, die Lean Manufacturing (‚schlanke Fertigung‘) so wirksam machen.
Oft finden wir ganz einfache Lösungen. Beispielsweise wurden in einer Produktionsanlage Komponenten aus einer Werkzeugmaschine auf eine Stahlrutsche ausgeworfen. Bei der Untersuchung entdeckten wir, dass beim Aufprall mikroskopisch kleine Fragmente der Rutsche abbrechen konnten, was zur Verunreinigung der Komponenten führte. Das Untersuchungsteam montierte eine reibungsarme Plastikabdeckung über dem Stahl und beseitigte damit das Problem.
Bei einem anderen Fall bemerkten wir, dass die Förderanlage ‚FlexLink‘, die zum Transport der Komponenten zwischen den Arbeitsstationen genutzt wurde, hohe Mengen an Schmutz aufsammelte. Wir installierten eine einfache Reinigungsstation an jedem Förderband, um diese Schmutzpartikel kontinuierlich abzuspülen. Einmal stellten wir fest, dass Komponenten, die einen Schleifprozess durchlaufen hatten, hohe Mengen Schmutz auf ihren Oberflächen aufwiesen. Wir entwickelten eine Spüleinheit, in der die Komponenten beim Verlassen der Maschine mittels mehrerer Düsen gewaschen werden. Diese simple Modifikation verringerte die Partikelverschmutzung um 80 %. Und weil zum Spülen bereits vorhandene Prozessflüssigkeiten genutzt wurden, waren keine zusätzlichen Kosten oder Ressourcen vonnöten.
Ein systemübergreifender Ansatz
Der häufigste Irrglaube im Bereich saubere Fertigung ist vermutlich: „Es kommt nur auf eine gründliche Reinigung an“. Jede Komponente, die wir produzieren, wird mehrmals gereinigt, während sie die Produktion durchläuft: zwischen kritischen Produktionsschritten und erneut vor der Endmontage.
Doch die Reinigung ist nur ein Teil eines viel breiteren und systematischeren Ansatzes an die saubere Fertigung. Um zu verstehen, warum das so entscheidend ist, muss man verstehen, wie Sauberkeit in der Produktionsumgebung gemessen und bewerkstelligt wird.
Die Internationale Organisation für Normung hat ein Codesystem zur Beschreibung des Grads an partikulärer Verunreinigung in Flüssigkeiten oder auf den Oberflächen von Komponenten entwickelt. Die Sauberkeitscodes beginnen mit 0 für extrem saubere Komponenten und reichen bis 24 und höher für stark verunreinigte Komponenten. Jeder Code ist mit einer Mindest- und Höchstzahl an Partikeln pro Volumeneinheit bzw. Oberflächeneinheit verbunden, je nachdem, ob es sich um Flüssigkeiten oder Komponenten handelt. Ein zusätzlicher Buchstabencode definiert die oberen und unteren Größenbeschränkungen für die Partikelzahlen. Ganz allgemein entspricht die jeweils nächsthöhere Stufe auf der ISO-Skala der doppelten Anzahl an festgestellten Partikeln.
Ein industrieller Reinigungsprozess ist nicht darauf ausgelegt, einen festgelegten ISO-Sauberkeitsgrad zu erreichen. Stattdessen wird die Prozessperformance am Unterschied zwischen der Sauberkeit eingehender und ausgehender Komponenten bemessen. Für die am häufigsten gebrauchten Reinigungssysteme bei SKF liegt dieser Wert „Delta“ bei etwa 75 %, wenn der Prozess ordnungsgemäß abläuft. Das heißt, dass eine Komponente nach der Bearbeitung um zwei ISO-Grade sauberer ist als vorher. Es bedeutet auch, dass die Sauberkeit eingehender Teile genauestens geprüft werden muss, um nach der Reinigung einen bestimmten Sauberkeitsgrad zu erreichen.
Bei der Lagerfertigung bestimmen wir die angestrebten Sauberkeitscodes für Komponenten und Flüssigkeiten für jeden einzelnen Produktionsschritt. Materialien, die im vorgelagerten Produktionsbereich ankommen, haben höhere Codes (ein höherer Grad an Verunreinigung wird akzeptiert) und der Prozess wird schrittweise immer sauberer.
Eine Zukunft im Nanomaßstab
Die saubere Fertigung bei SKF zu optimieren stellte ein mehrjähriges Unterfangen dar. Wie auch bei anderen Arten der kontinuierlichen Verbesserung sind wir davon überzeugt, dass man immer noch ein bisschen mehr erreichen kann. Ein Bereich, in dem wir aktuell besonders aktiv sind, ist die Welt der Sauberkeit im Nanobereich.
Traditionelle Systeme zur Feststellung von Verunreinigungen sind darauf ausgelegt, Partikel bis zu einer Größe von 5 µm zu erkennen, während Spezialausrüstung auch 1 µm kleine Partikel erfasst. Herkömmliche Reinigungs- und Filtrationssysteme sind auf Partikel in ähnlichen Größen ausgelegt.
Wir wissen durch eigene Analysen von verunreinigten Komponenten jedoch, dass ein entgegengesetzter Zusammenhang zwischen Partikelgröße und -häufigkeit besteht. Je kleiner die Partikel, desto mehr davon findet man. Folglich können Komponenten mit einem hohen Grad an extrem kleinen Partikeln verunreinigt sein, die zu klein sind, um sie zu aufzuspüren.
In der Vergangenheit haben Experten für die saubere Fertigung diese Verunreinigung im Nanomaßstab ignoriert, und zwar schlichtweg deswegen, weil sie wenig dagegen tun konnten. Heutzutage sind jedoch neue Technologien verfügbar, mit deren Hilfe hochreine Öle und Maschinenflüssigkeit hergestellt werden können, indem selbst die winzigsten Schmutzpartikel eliminiert werden.
2019 hat SKF das kleine Cleantech-Unternehmen RecondOil übernommen, das ein patentiertes Verfahren zur Reinigung von Ölen im Nanomaßstab entwickelt hat. Dieses Verfahren heißt Double Separation Technology (DST). Dank DST können alle Schmutzpartikel, egal wie groß oder klein sie sind, aus dem Öl entfernt werden. Das Verfahren steckt zwar noch in den Anfängen, doch wir haben bereits Flüssigkeiten aus unseren Fertigungslinien getestet, die mit dem SKF RecondOil DST-System behandelt wurden. Das Ergebnis: Deutlich verbesserte Eigenschaften der Komponentenoberflächen und des Geräusch- und Schwingungspegels bei kompletten Lagern.
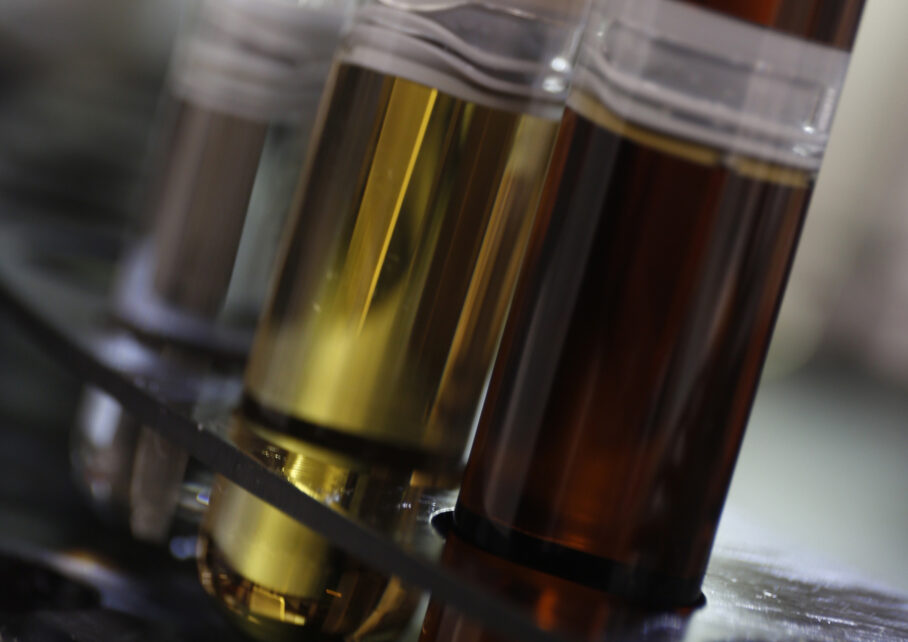