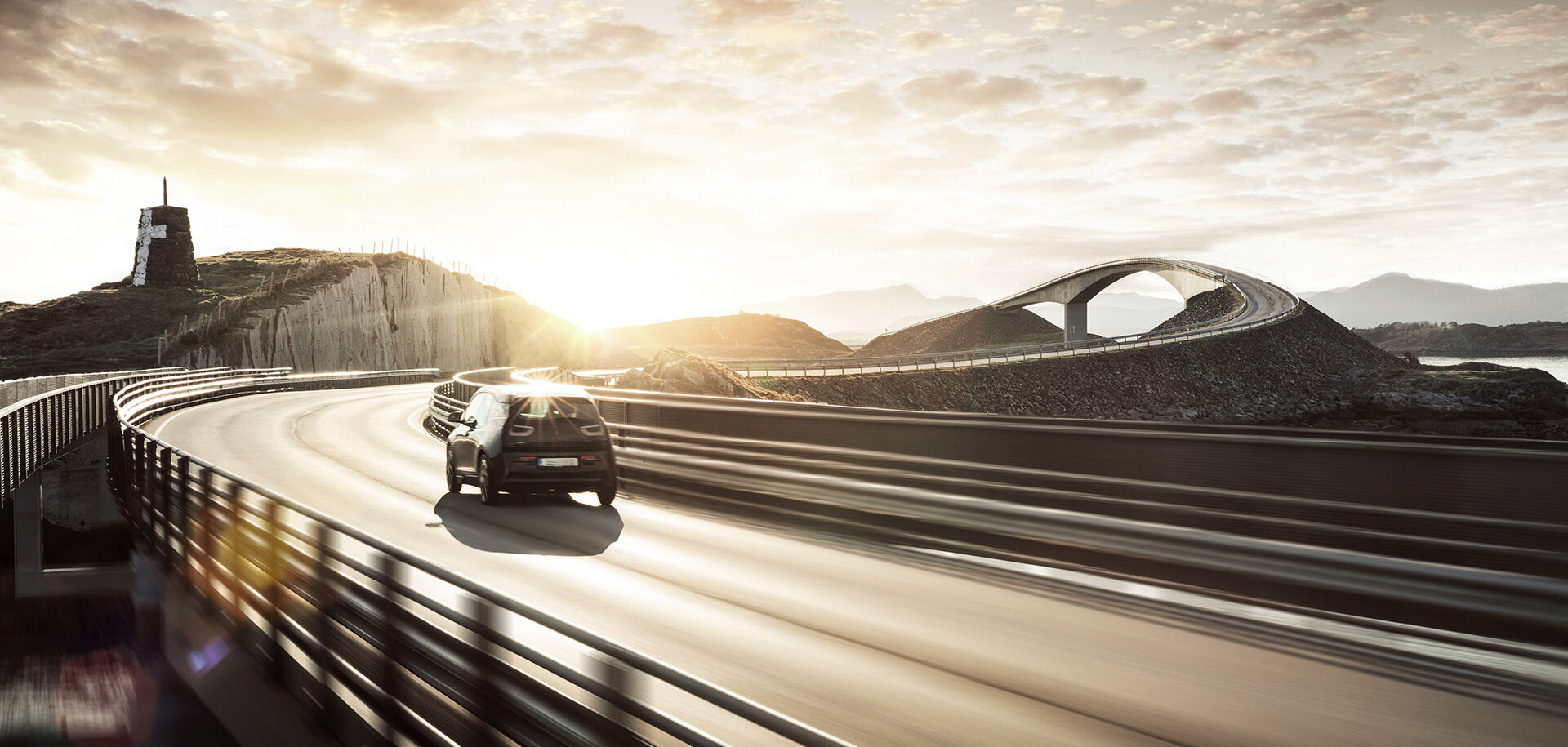
Hybridlager – der Industriestandard der Zukunft
Hybridlager bieten Lösungen für bestehende und neue technische Herausforderungen. Die Kombination von Stahlringen und keramischen Wälzkörpern reduziert Gewicht und Reibung und verhindert Elektroerosion bei gleichzeitiger Steigerung der Zuverlässigkeit und Verbesserung der Drehzahleignung.
Die Welt durchläuft derzeit eine Phase des schnellen Wandels. Globale Megatrends verändern die Art und Weise, wie wir reisen, Geschäfte machen und wie wir leben. Die Urbanisierung führt dazu, dass immer mehr Menschen in die Städte ziehen, die Digitalisierung und Automatisierung beschleunigen unser privates und berufliches Leben, und die Gesellschaft muss sich verschiedenen ökologischen Herausforderungen stellen. Gleichzeitig erleben wir eine rasante Entwicklung im Bereich der Elektrifizierung, insbesondere bei Elektrofahrzeugen, und stellen eine anhaltende Tendenz zur Globalisierung fest.
Diese großen globalen Trends treiben wiederum den Wandel auf dem Gebiet der Wälzlager voran. Viele neue Technologien sind auf spezielle Lagereigenschaften angewiesen, wie z. B. auf eine Eignung für drehzahlvariable Antriebe, einen niedrigeren Wartungsbedarf, eine höhere Leistungsdichte und eine geringere Reibung.
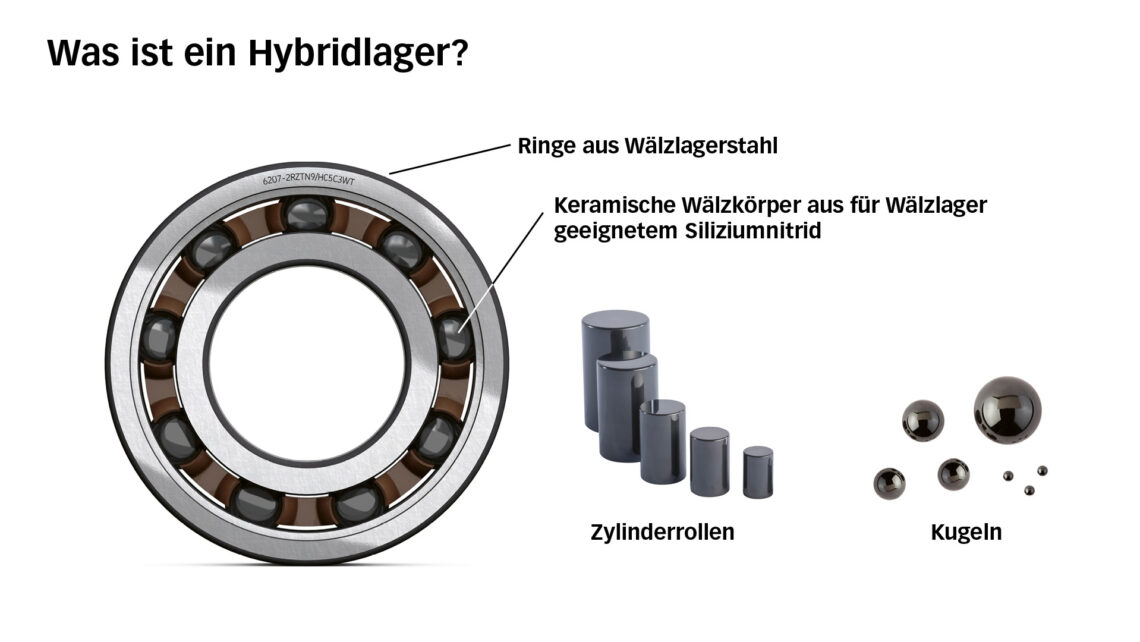
Die Verwendung von keramischen Werkstoffen in Wälzlagern ist nichts Neues. Die globale Luft- und Raumfahrtindustrie war ab den 1960er- bis in die 1980er-Jahre Vorreiter beim Einsatz dieser Werkstoffe, die sich durch ihr geringes Gewicht und ihre Hitzebeständigkeit auszeichnen. Siliziumnitrid wurde allerdings erst in den 1980ern kommerziell genutzt. Seit den 1990er-Jahren werden moderne Hybridlager in zahlreichen Anwendungen eingesetzt, wie z. B. Werkzeugmaschinen, Windkraftanlagen, Fahrmotoren für Schienen- und Elektrofahrzeuge, Maschinen für die Luft- und Raumfahrt sowie Strömungsmaschinen wie Kompressoren, Pumpen und Vakuumpumpen.
Die in SKF Hybridlagern verwendeten Siliziumnitrid-Wälzkörper weisen Eigenschaften auf, die sich deutlich von Standardwälzkörpern aus Stahl unterscheiden. Siliziumnitrid zeichnet sich durch eine viel höhere Druckfestigkeit als Wälzlagerstahl aus, und sein Elastizitätsmodul ist um etwa ein Drittel höher, was zur Reduzierung der Reibung im Wälzkontakt beiträgt.
Ein weiterer wichtiger Punkt ist, dass Siliziumnitrid eine mehr als doppelt so hohe Härte als Wälzlagerstahl aufweist, was es zum idealen Werkstoff für anspruchsvolle Betriebs- und Schmierbedingungen macht. Im Gegensatz zu Wälzlagerstahl ist Siliziumnitrid elektrisch isolierend, wobei seine Dichte erheblich geringer ist. Und schließlich ist sein Wärmeausdehnungskoeffizient weitaus niedriger, was eine genaue Spieleinstellung ermöglicht, aber unter bestimmten Betriebsbedingungen, u. a. Anwendungen bei sehr niedrigen Temperaturen, berücksichtigt werden muss.
Bei der Verwendung in Wälzlagern verbessert Siliziumnitrid die Lagerleistung, beispielsweise durch eine hervorragende elektrische Isolierung und Gewichtsreduzierung sowie durch hervorragende tribologische Eigenschaften und eine hohe Verschleißfestigkeit. Zudem ist die Drehzahleignung deutlich höher.
Wie lösen diese Eigenschaften nun spezifische Anwendungsprobleme? Und warum werden Hybridlager in den nächsten Jahren in vielen Industriezweigen wohl der Standard sein?
Eine Schlüsselanwendung, bei der Hybridlager ihre Vorteile in vollem Umfang nutzen können, sind drehzahlvariable Antriebe, die für eine optimierte Steuerung von rotierenden Maschinen, wie z. B. Pumpen oder Fahrmotoren, eingesetzt werden. Diese pulsweitenmodulierten Antriebe verursachen schädliche hochfrequente Lagerströme. Wenn Strom durch ein Lager fließt, können sowohl die Ringe und Wälzkörper als auch der Schmierstoff Schaden nehmen. Ein höherer Schwingungspegel ist die wohl geringste Schadensfolge, denn Elektroerosion kann sogar die Lebensdauer von Lagern und Schmierstoffen erheblich verkürzen.
Durch den Einsatz von Hybridlagern in solchen Fällen stellt sich dieses Problem nicht. Siliziumnitrid ist ein Isolator und verhindert den Stromdurchgang zwischen den Lagerringen, auch bei sehr hochfrequenten Strömen. So lassen sich spätere Lagerausfälle vollständig ausschließen.
Ein zweiter wichtiger Vorteil von Hybridlagern sind längere Wartungsintervalle und eine längere Lagergebrauchsdauer. Die Verwendung von Keramikwälzkörpern in solchen Lagern erhöht die Lebensdauer des Schmierstoffs erheblich, so dass das jeweilige Lager länger in Betrieb bleiben kann, bevor eine Wartung erforderlich wird. Bei Keramikwälzkörpern wird der Wälzkontakt besser mit Schmierstoff versorgt. Und da die Reibung somit geringer ist und keine Elektroerosion mit nachfolgendem thermischem Abbau stattfindet, bleibt die Schmierfähigkeit länger erhalten.
Bei SKF Tests hat sich gezeigt, dass die Lebensdauer des Schmierstoffs in einem Hybrid-Rillenkugellager mindestens doppelt und bis zu fast siebenmal so lang war als bei einem vergleichbaren Stahllager. Bei ähnlichen Tests mit Zylinderrollenlagern hielt der Schmierstoff im Hybridlager mindestens doppelt und bis zu viermal so lang.
Der dritte Vorteil von Hybridlagern besteht darin, dass sie höhere Betriebsdrehzahlen zulassen und damit eine höhere Leistungsdichte ermöglichen. Die Hersteller von Elektromotoren tendieren generell dazu, die Leistungsdichte zu erhöhen, vor allem bei Fahrzeugen wie Zügen sowie Fahrzeugen für die Straße und das Gelände. Vereinfacht ausgedrückt, ist die Leistung abhängig von Drehmoment und Drehzahl. Wenn die Drehzahl, mit der sich ein Lager dreht, erhöht werden kann, dann nimmt auch die Motorleistung zu.
Warum soll die Leistungsdichte erhöht werden?
• Genauso viel Leistung bei einem kleineren Elektromotor
P = M • n
• Höchstdrehzahl (auch) durch Lager begrenzt
Reduzierung der Reibung
Ein letzter wichtiger Vorteil von Hybridlagern ist die geringere Reibung. Die Reduzierung der Reibung in einem Lager kann zur Senkung des Energieverbrauchs beitragen, was für die heutige Industrie ein wichtiger Aspekt ist. Die keramischen Wälzkörper von Hybridlagern haben einen direkten Einfluss auf die Reibung, die infolge von Roll- und Gleitmomenten entsteht. Bei Hybridlagern sind die durch das Rollmoment verursachten Energieverluste aufgrund der kleineren Kontaktellipse, die sich aus einem höheren Elastizitätsmodul ergibt, geringer. Zudem verringert sich das Gleitreibmoment aufgrund der besseren Oberflächenbeschaffenheit der Keramikwälzkörper.
Hybridlager – vom Problemlöser zum Wegbereiter
Die industrielle Fertigung und der Automobilbau sind dabei, ihr jeweiliges Output zu optimieren, um sich den globalen Herausforderungen der Nachhaltigkeit zu stellen und mit den gesellschaftlichen und technologischen Trends Schritt zu halten. Hybridlager mit Keramikwälzkörpern und Stahlringen können zur Lösung vieler Konstruktions- und Wartungsprobleme beitragen, mit dem Ergebnis einer gesteigerten Zuverlässigkeit. So lösen Hybridlager nicht nur Probleme, sondern sorgen auch für einen wirtschaftlicheren Betrieb und eine höhere Leistung. Es ist daher sehr wahrscheinlich, dass Hybridlager in den nächsten Jahren für viele Anwendungen und Branchen zur Standardlösung werden.