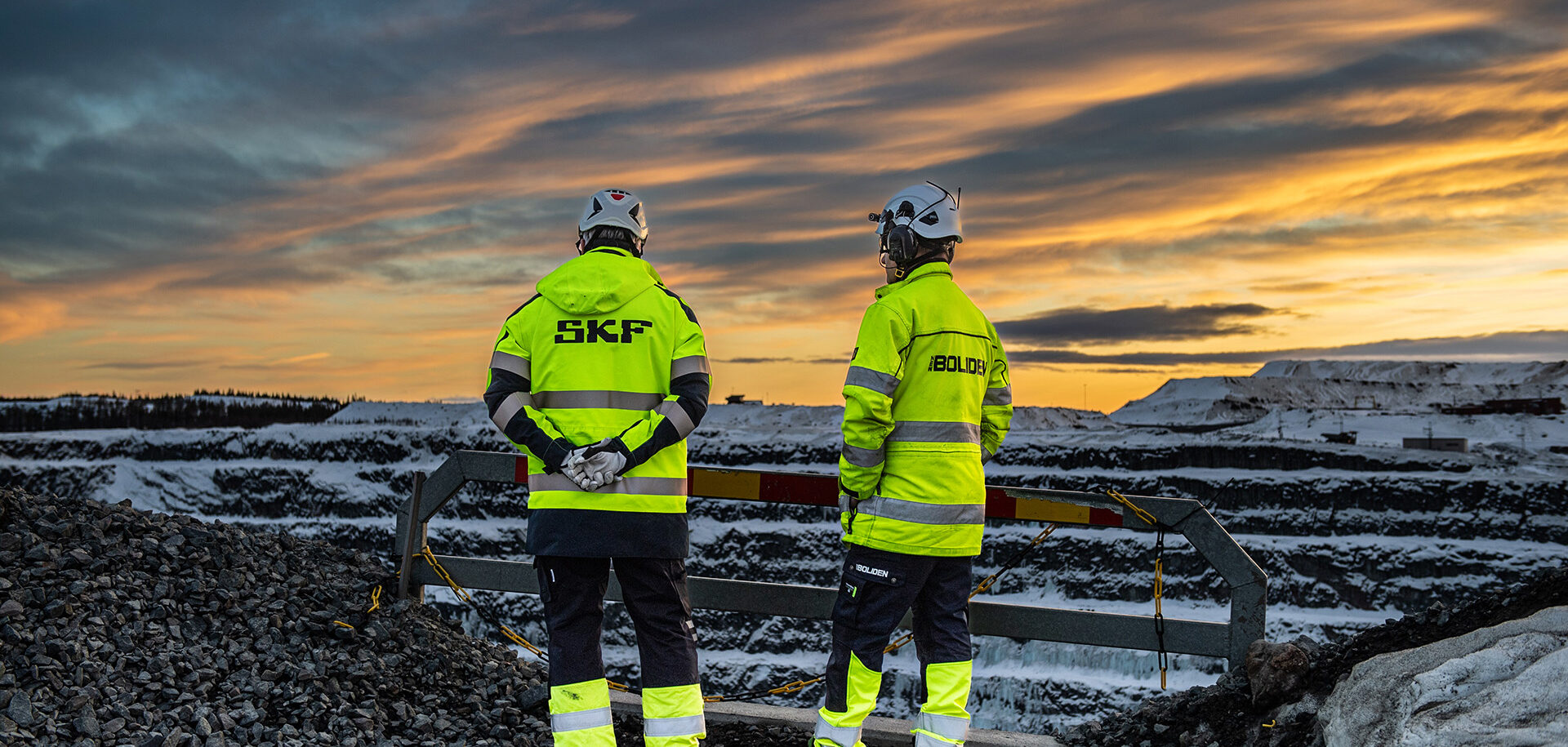
Neue Zusammenarbeit erhöht die Zuverlässigkeit der Förderbänder
Bei den kilometerlangen Förderbändern der Aitik-Kupfermine von Boliden traten immer wieder Probleme und Störungen auf. Ein neues Schwingungsüberwachungssystem und eine Partnerschaft mit SKF brachten die Lösung.
Die Aitik-Kupfermine von Boliden liegt rund 1 000 Kilometer nördlich von Stockholm, oberhalb des Polarkreises unweit des nordschwedischen Orts Gällivare. „Früher hatten wir jede Woche ungeplante Betriebsunterbrechungen. Heute dagegen sind die meisten Stillstände geplant“, sagt Stefan Johansson, Leiter der vorbeugenden Wartung in der Abteilung Crushing & Conveying (Zerkleinern & Fördern) der Aitik-Kupfermine von Boliden.
Die meisten Stillstände sind geplant.
Stefan Johansson, Leiter der vorbeugenden Wartung in der Abteilung Crushing & Conveying der Aitik-Kupfermine von Boliden
Transporte sind in dem Kupfer-Tagebau von entscheidender Bedeutung. Um einen Eisenerzanteil von 0,2 Prozent zu gewinnen, müssen gewaltige Gesteinsmengen abgebaut und transportiert werden – zunächst mit Lastwagen zu den Brechern und von dort aus weiter mit Förderbändern zum Konzentrator. Seit seiner Inbetriebnahme im Jahre 2010 war das sieben Kilometer lange Förderband eine Schwachstelle in der Produktionskette.
Jonas Fjellner, der die Abteilung Crushing & Conveying im Aitik-Tagebau leitete, kannte diese Schwierigkeiten nur allzu gut: „Wir wussten, dass die Lager in den Antriebsscheiben und -trommeln das Problem waren.“ Das vorhandene Schwingungsüberwachungssystem hatte gewisse Mängel. Hinzu kam, dass es im Unternehmen nicht genügend Know-how gab, um die Messwerte entsprechend zu analysieren.
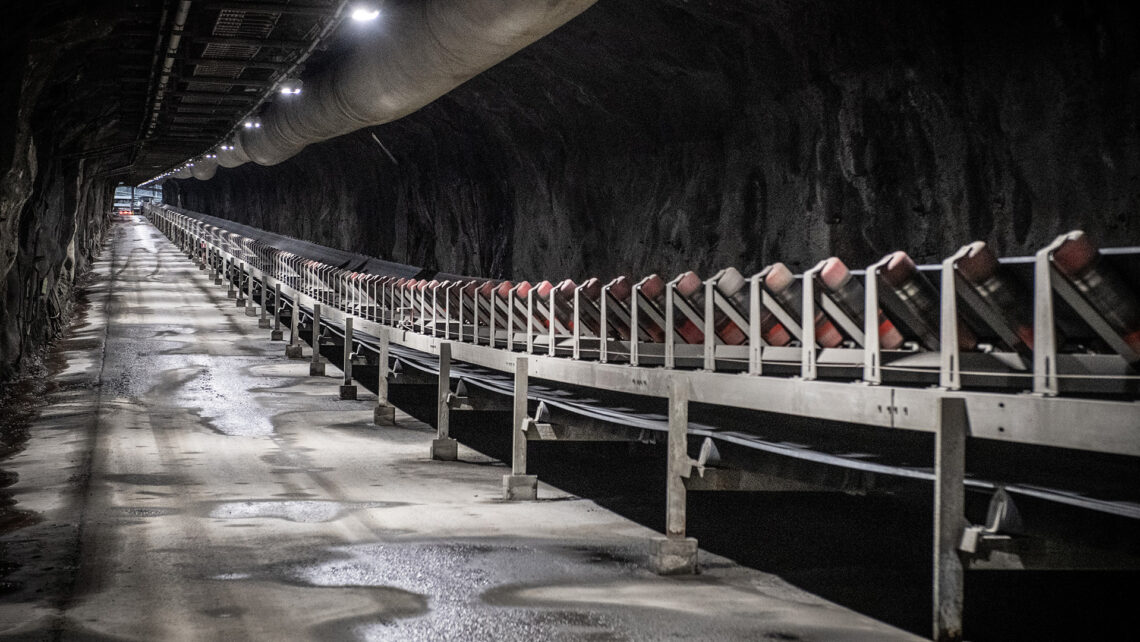
Komplettlösung
Ein völlig neues System wäre das Beste. Boliden suchte nach einer ganzheitlichen Lösung sowie nach einem Partner vor Ort, der dem Bergbauunternehmen über den gesamten Prozess hinweg – von der Installation über Messungen und Analysen bis zur Problemlösung und kontinuierlichen Verbesserung – zur Seite stehen könnte.
2018 beschloss die Unternehmensleitung, das Schwingungsüberwachungssystem auszuwechseln und die Arbeitsmethode zu ändern. 2019 unterzeichnete Boliden einen Partnerschaftsvertrag mit SKF. Im ersten Schritt wurde die gesamte Hardware ausgetauscht und durch die Schwingungsüberwachungslösung von SKF ersetzt. Ferner wurde entschieden, gänzlich auf SKF Lager und Lagergehäuse umzusteigen.
Mitte 2020, als das neue System in allen Bereichen des Bergwerks installiert war, zeigten sich schon erste Ergebnisse. „Die Verfügbarkeit hat sich definitiv erhöht“, meint Johansson. „Seit 2019 haben wir keinen einzigen ungeplanten, durch Lagerausfälle verursachten Stillstand gehabt. Alle Wartungs- und Instandhaltungsmaßnahmen sind inzwischen geplant.“
Gemeinsame Besprechungen
Johansson sagt, ein wesentlicher Faktor für den Erfolg sei die neue, auf enger Zusammenarbeit mit SKF basierende Organisation. „Wenn beispielsweise ein Lager ausgetauscht werden muss, führen wir mithilfe von SKF eine Ursachenanalyse durch, um herauszufinden, was passiert ist. Bei unseren Projektgruppenbesprechungen diskutieren wir, ob Lager ausgewechselt, Dichtungen ausgetauscht oder andere Lösungen getestet werden sollen“, erklärt er.
SKF hat auch Schulungen mit dem Personal von Boliden durchgeführt und weitere sind in Planung.
Zurzeit übernimmt SKF die Analyse der im Zuge der Schwingungsüberwachung erfassten Messdaten. Das geschieht oft in direktem Kontakt mit dem Personal der Abteilung Crushing & Conveying. „Falls bei den Messungen ein Warnsignal ertönt, können wir zum Beispiel von SKF einen Anruf erhalten mit der Aufforderung, etwas zu überprüfen. Das kann auch freitagnachts oder samstags sein“, so Johansson.
Weniger Emissionen durch Rekonditionierung
Die neue Arbeitsmethode hat zu zahlreichen bedeutenden Veränderungen geführt, die nicht nur die Maschinenverfügbarkeit erhöht, sondern auch die Wiederverwertung von Werkstoffen durch Rekonditionierung von Lagern und Lagergehäusen ermöglichen.
„Durch die Messungen bekommen wir viele Informationen. Wenn wir sehen, dass ein Lager ausgetauscht werden muss, holen wir SKF mit ins Boot“, fährt Johansson fort. Im Zusammenhang mit dem Austausch prüft SKF das Lager vor Ort und beurteilt, ob es aufgearbeitet werden kann.“
2022 konnten 22 Komponenten – Lager und Lagergehäuse – aufgearbeitet werden. Weitere zehn Komponenten wurden bis März 2023 zur Rekonditionierung geschickt. Abgesehen von den Einsparungen in Höhe von circa sechs Millionen SEK (umgerechnet etwa 514 000 Euro) bewirkte die Rekonditionierung auch eine drastische Senkung der CO2-Emissionen verglichen mit der Herstellung neuer Produkte.
Boliden und SKF unterzeichneten 2022 einen neuen dreijährigen Partnerschaftsvertrag. „Damit vertiefen wir unsere Zusammenarbeit und gehen auf dem eingeschlagenen Weg weiter. Wünschenswert wäre, wenn auch andere Boliden-Werke so arbeiten würden. Es ist ein sehr gelungenes Konzept. Wir arbeiten im Team auf ein gemeinsames Ziel hin und schaffen ein großartiges Gemeinschaftsgefühl in der Gruppe“, schließt Johansson.