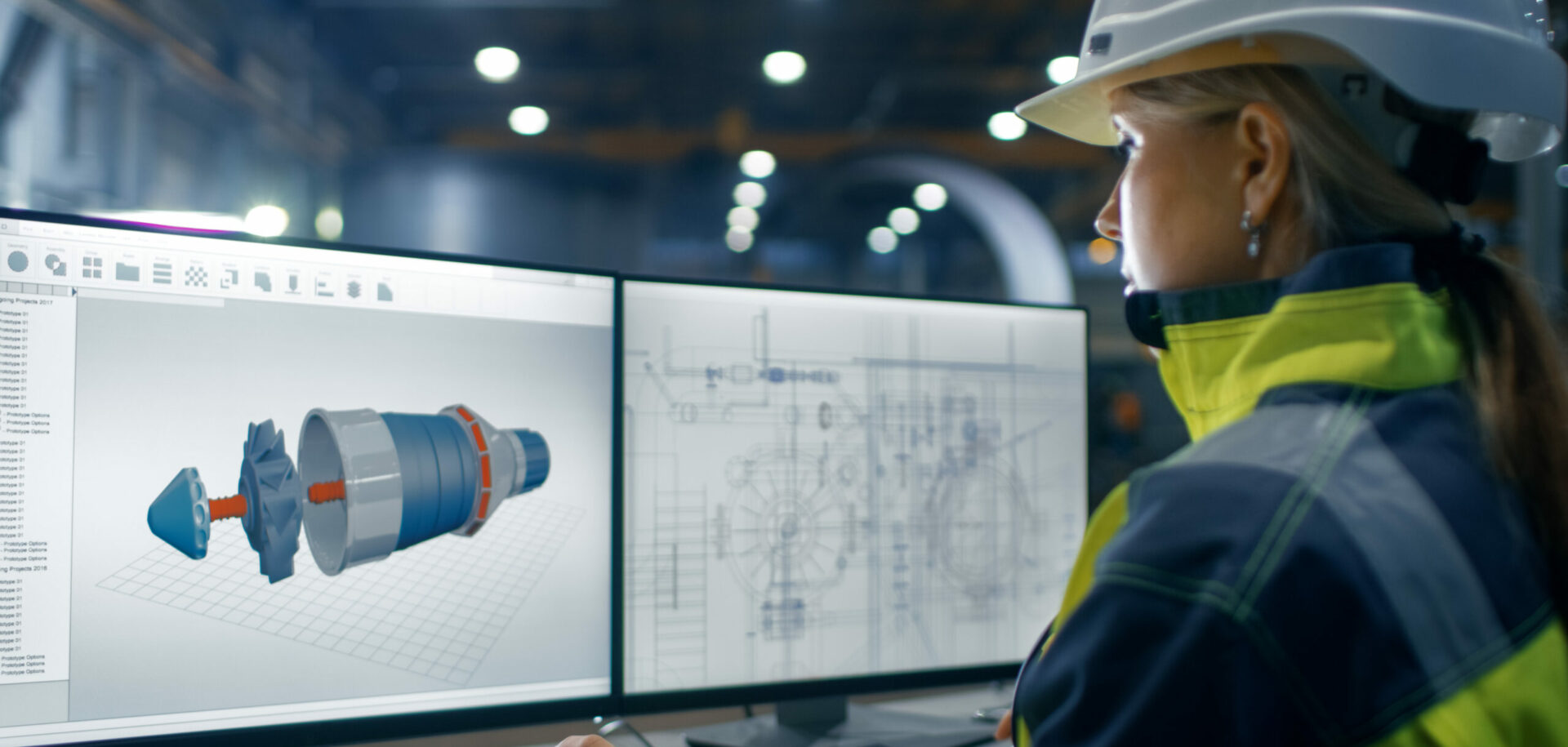
Drive-by-wire systems are forecast to replace many of the traditional hydraulic and mechanical systems in vehicles. The Bertone-SKF Filo gives us a hint of what the cars we will be driving in the not-too-distant future may be like.In by-wire systems, direct mechanical control of a machine is replaced by electronic control. The drive-by-wire system follows closely the fly-by-wire concepts used successfully by the aerospace industry for many years. In conventional control, the movements the driver makes with the steering wheel are transmitted mechanically via the steering column to the steering rack and then to the front wheels. In a by-wire system, the driver’s physical movement on the steering wheel is sensed and converted into a digital electronic signal that is transmitted to a smart electro-mechanical actuation unit (SEMAU) that controls the wheels. The same principle can be applied to the braking and gearbox systems. SKF has had more than 15 years’ experience in the production of mechatronic controls and actuating units for the civil aerospace industry through its French subsidiary, SARMA.
SKF has a long history of cooperation with the automotive industry and is a major supplier globally. The collaboration between Bertone and SKF marks an important step in the development of drive-by-wire systems. Other companies who provided expertise included Brembo S.p.A, which collaborates with SKF in brake-by-wire developments, Bose and Nokia. TTTech supplied aspects of the car’s network architecture control.
Considerable SKF input
All of the Filo’s by-wire systems were developed and manufactured by SKF. The electro-mechanical actuation units were specially developed for specific by-wire sub-systems. The computerized control units were developed on a common base, but the programming and power stages were specific to each sub-system. The Filo employs two power supply levels, the conventional 14 volt and the emerging 42 volt. Clutch and gearshift are on the conventional supply level and the systems with higher power requirements, steering and braking, are 42 volt.
The individual actuation control units are sophisticated computer-controlled power-switching units that interpret the signals coming in from the many sensors and control inputs and provide electrical power to the SEMAU’s prime mover, a brushless electric motor. The actuation control units (ACU) incorporated TTTech’s time-triggered protocol, the robust and fault-tolerant network operating system that runs the data backbone within the Filo’s complete by-wire architecture. The complete braking arrangement was a joint development between SKF and Brembo, with Brembo developing custom calliper bodies into which the SKF SEMAUs fitted. Filo’s driver’s control – the Guida – incorporates an active feedback system within the yokes of the steering arrangement. This system gives the driver “feel.” Running in a closed loop with the steering SEMAU and sensors on the yokes, a high-torque motor provides to the Filo’s driver tactile feedback on steering-angle and road-surface changes.
Difference in appearance
For the driver, the most striking aspects of the interior design of the vehicle are the absence of pedals and steering column. This creates considerably more space inside the car. Drive-by-wire technology eliminates heavy, space-consuming hydraulic and mechanical components, and it has positive environmental implications through the elimination of brake fluids, as well as significant safety benefits.
Electro-mechanical control could allow the steering column and pedals to be removed, a significant potential for improving passive safety for the driver in case of a crash.
In this concept vehicle, the driver’s control system, the Guida, combines all the controls that the driver needs in a single unit. Throttle, braking and steering are presented as hand controls. Gear selection is made by a button system that is familiar from the world of motor racing.
Lights, windshield wipers, audio, heating and air conditioning are all located within the driver’s immediate reach. The right and left steering control yokes, which are linked, have a travel of +/- 20 degrees. The amount of “feel” experienced by the driver is fully programmable, as is the relationship between the movement of the yokes and the movement of the front wheels. For the Filo, the steering actuator fits into the original platform’s sub-frame assembly.
Handling the signals
The signals for today’s complex industrial machines, aerospace applications and by-wire systems are all digital. The complexity of automotive by-wire systems, which is greater than industrial applications but considerably lower than aviation systems, requires a network. Due to the nature of the systems used in a vehicle, the network has to be robust and fault-tolerant. Conventional office networks and those networks currently used in multiplexed signal applications on some cars rely on an event-driven protocol. An event-driven protocol is essentially reactive – passive until a request is made to handle an exchange of information. With such a system, if the network is faulty, the driver may only discover this when he or she tries to operate something controlled via the event-driven network, such as the sunroof or windows.
For complex, safety-critical applications such as brakes or steering, such an arrangement is not robust enough to ensure the level of reliability demanded. For such systems a time-triggered protocol is used. This protocol allocates specific blocks of time to each of the connected computers. On each allocated time block, the specific computer must respond and acknowledge it is there and functioning correctly. If it wishes to have a specific operation carried out, it signals this wish and transfers the appropriate messages via the network to the actuator’s controller. The network checks continually that the nodes (the computers) are connected and making the appropriate responses when polled. In this way the fault-tolerant protocol ensures the well-being of the complete network structure and can take appropriate action in cases of failure. With a time-triggered arrangement, a failure would be detected at the next time block that was not answered appropriately – a matter of milliseconds.
Now let’s look at the next layer of activity, the example taken is gear selection.
Assuming the Filo is running in first gear, the driver wishes to engage second gear. The driver presses the plus button on the Guida. What follows is a complex series of messages. The initial request goes to the clutch actuator control unit (ACU, a computer), which carries out the instruction to disengage the clutch. Signals go to the power-stage of the clutch ACU, which in turn provides the appropriate current for the appropriate duration to disengage the clutch. With this operation completed correctly, a signal is sent to the gearshift ACU, giving it permission to carry out the up-shift. Again, once completed successfully, the gearshift ACU sends a signal to the clutch ACU that the clutch may be re-engaged. There are many more checks and exchanges taking place between the ACUs even for this apparently simple operation, but this is a reasonable simplification of the sequence.
The Filo employs a conventional “H-pattern” manual shift gearbox and, consequently, precise linear and rotational movement is required by the actuation unit. All the actuators used in the Filo are “dry” systems. They are purely electro-mechanical in operation. The units operate in the following basic manner: Power is supplied to the actuator’s electric motor. Through some form of gearing arrangement, dependent on the type of operation the actuator must perform, a ball screw converts the rotary motion into linear motion. This causes the front wheels to turn, the brake callipers to engage on the discs or the gears to shift, depending on the specific actuator.
Braking-by-wire
For Filo’s novel braking system, SKF has combined forces with Italian brake manufacturer, Brembo. The system is based on Brembo’s knowledge of calliper design and braking systems and SKF’s electro-mechanical actuating units and hub-bearing designs. The braking-system control is mounted on the Guida and is activated by squeezing handgrips. The mechanical design of the driver’s braking controls incorporates a progressive resistance and a small, but clearly discernible, free play at the beginning of the movement. This provides the driver with a tactile indication that the brakes are starting to operate. Each brake is controlled as an individual sub-system under an overall control arrangement for the complete vehicle braking system.
The braking performance of the Filo brake-by-wire system is already better than that of conventional hydraulic arrangements. System response times are below those of the conventional arrangement and maximum clamp loads across the calliper are higher. As the Filo project progressed, engineers were able to reduce the overall weight and size of the braking system so that the complete calliper assembly is compact and comparable in weight to conventional hydraulic designs. SKF and Brembo are working on the development of a brake-by-wire system that is expected to go into production in 2004.
Software aspects
The control software was developed by SKF as three separate suites – one for the brake-by-wire system, one for the clutch- and gearshift-by-wire systems and the third for the steer-by-wire system. The software interfaces between the control input signals from the Guida and the sensors mounted on and about the smart electro-mechanical actuation units. In addition to this single system relationship between brakes and steering, among other factors, there is an over-arching aspect to the software – provided primarily by the time-triggered protocol arrangement – that continually looks after the complete system’s well-being. Being fault-tolerant ensures that the necessary level of safety, error recovery and fail-safe performance is in place.
Gianluca Oberto,
SKF Drive-by-Wire business unit, Italy