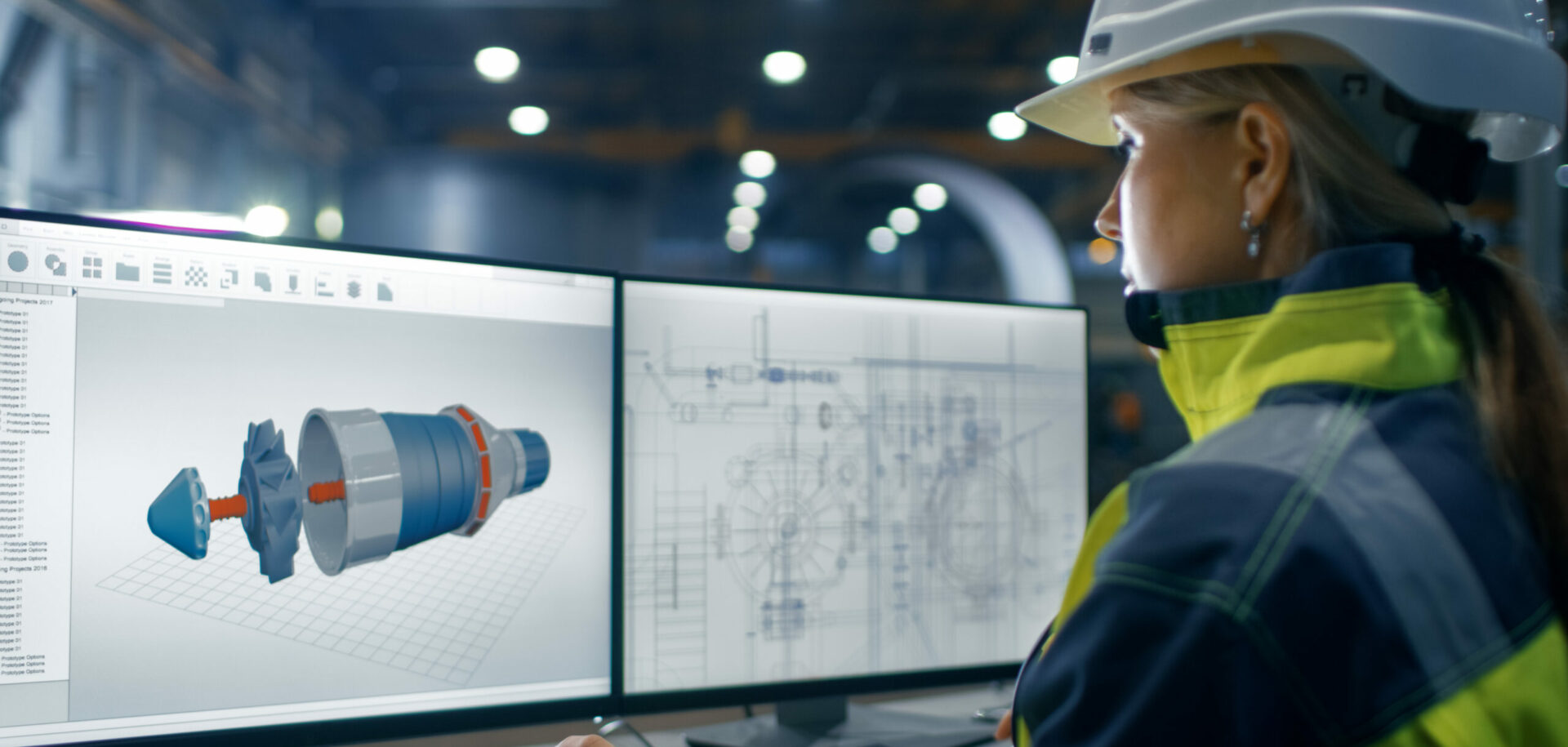
Electrical and fire-safe bearings for ventilator motors
Electrical motors for fan arrangements are increasingly used with power frequency converters for variable-air-volume ventilation systems or in fire safe fan designs. This means bearings must resist electrical erosion under normal operating conditions and high temperatures in case of fire.
New or upgraded variable-air-volume (VAV) ventilation systems enable flexible, reliable and energy-efficient ventilation and replace constant-air-volume systems. Each zone to be ventilated at a controlled level often has its own inlet and outlet fans. The fan blades are directly connected on the electrical motor shaft, and speed control is through a frequency converter. This allows precise airflow control to a specific zone, as required for hospitals, modern manufacturing plants, etc. VAV systems also provide economical and precise ventilation of large building structures with complex layouts, such as airports, commercial shopping centres, office buildings, ferries, naval ships, etc.
Additional system demands can include very high functional reliability, as for operating theatres, or the need to duplicate, as in powered smoke and heat exhaust ventilation systems (SHEVS), which are typically found in large building works and tunnels where fire is a hazard. With such applications, it is also necessary to be in line with the fire-safety requirements of the new EN 12101-3 standard for powered SHEVS, whilst offering long service life during normal use. To fulfil these requirements of low life-cycle cost and reliable function on VAV systems and SHEVS, the use of hybrid bearings and other specific bearings will be of growing importance.
Electrically safe bearings
New VAV systems typically incorporate several hundred electrical motors with high demands on reliability. In fans, the motor bearings are the only highly loaded moving components with possible metal-to-metal contact. The bearings, therefore, are the most critical parts when it comes to high reliability and low service costs. Today, around 50 % of electrical motor failures are related directly to bearing damage. This rate of failure is expected to increase significantly for smaller, continuously used motors in the 0.15–15 kW range, due to the steady increase of incorporating frequency converters. Frequency converters such as pulse-width-modulated (PWM) designs are known to contribute to electrical erosion-related bearing damage in standard all-steel bearings.
Usually, smaller motors are prone to damage because they are equipped with standard bearings that do not have protection against electrical discharges in the raceway-rolling element contact. By contrast, larger motors normally use electrically insulated bearings, SKF INSOCOAT®, or polymeric insulation layers that provide such protection. Hybrid bearings are the most viable solution to give smaller motors the same kind of electrical protection.
Damage signs
The discharges arise because the common mode voltage differs from zero and edge spikes occur, due to the very short switching times of the frequency converters. This can be measured using shaft-to-earth couplings and an appropriate oscilloscope on electrical motor installations ( .1). Typical damage signs are micro-cratering and pitting of raceways, greying of rolling elements and raceways, washboard patterns and blackening of the grease. This results in poor lubrication, high vibration levels and, in the end, seizure of the bearings.
Electrical erosion of bearings in VAV systems reduces the bearing service life. This can be recognised as an increase in early failures and a faster rate of failures. A recent example comes from a four-year-old Swedish hospital with a new VAV system, using PWM frequency converters. By statistical analysis of maintenance data, it appeared that the basic rating life L10h (90 % reliability) was reduced to only 30 % of the expected value ( .3).
The bearings were greased-for-life, and the statistical analysis showed an even sharper decrease in operating hours for the L50h life (50 % reliability), due to the faster failure rate. The presence of electrical currents on the bearings was established directly by diagnostic measurements (shaft-to-earth) on motors and by analysis of damaged bearings (blackening of grease and smelling of ozone). An analysis, similar to the one shown, can be done on a limited number of damaged bearings in larger VAV systems, as the statistical outcome is better with a few system failures on a large population than with many failures in a small one.
The failure intensity of the system, i.e., the likelihood of early bearing damage, in the case of the hospital, will increase rapidly with time after four years ( .4). The risk increase for failure of equipment servicing critical zones such as operating theatres is not acceptable. To avoid such risk increase, it is highly recommended to equip this type of fan motor with two hybrid bearings. Being electrically insensitive, they provide protection against common mode voltage differences, edge spikes and other causes of electrical damage to bearings.
It should be noted that one hybrid bearing, typically on the non-drive-end side, could provide adequate protection. However, the application of electrically insulating bearings such as hybrid bearings should be done in cooperation with experts on motor currents and bearings, and verified by field measurements. It should be stressed that the original equipment manufacturer should always be consulted about any design changes to electrical equipment.
Insulating solution
SKF continues to expand its range of stocked hybrid bearings for the electrical machinery market to allow for rapid deliveries. The stock consists mainly of deep groove ball bearings in the 60, 62 and 63 series with bore sizes ranging from 5 to 70 mm. Larger ones are also available, either from stock or made to order at short notice. Hybrid deep groove ball bearings for VAV motors are typically equipped with low-friction seals (2RZ or 2RSL), an injection moulded cage of glass fibre-reinforced polyamide, roller centred (TN9), ceramic balls (HC5), clearance greater than normal (C3) and a wide temperature grease (WT) with high-performance characteristics for electrical motors. Typical bearing designations are 6004-2RSLTN9/HC5C3WT or 6208-2RZTN9/HC5C3WT.
Fire-safe bearings
Good fire protection of large-scale building works such as tunnels for transports, airports, warehouses, large public buildings, etc., is essential.
Many of these structures are equipped with powered smoke and heat exhaust ventilation systems to provide formation of cooler and cleaner air below hot gases in case of fire. These potentially life-critical, dual-purpose systems (normal ventilation and smoke exhaust ventilation) need to provide reliable emergency function over time.
The recent European standard EN 12101-3 specifies that ventilators for SHEVS and the associated direct-driven fan motors should be classified for use at emergency temperatures in case of fire. Today, the F400 class (400 °C) is the most important applied level, and many European SHEVS for tunnels and buildings are being built to or upgraded to this standard. New motor design developments, however, can be expected to enable fulfilment of the requirements for the F600 class (600 °C). Additionally, SHEVS installations should also give users low operating costs, as these systems are in continuous daily use for comfort ventilation. Reliable comfort ventilation is, in many installations, of critical importance for removal of toxic combustion gases from cars and trucks and to limit disturbances of traffic flows.
It should be noted that the EN standard leaves it up to manufacturers, owners and operators to provide low life-cycle costs for daily comfort operation of dual-purpose ventilators. Also, the ability for emergency running after prolonged daily use is not specified. For further technical developments and large market acceptance, SKF has identified the requirements for bearings to be used in F400 and higher-class equipment, as stated by the EN standard, and also for additional user needs:
- Emergency running capability at 400 °C (two hours) or 600 °C (one hour), according to the standard;
- Shutdown and restart capability, at emergency temperature, according to the standard;
- Reliable emergency function over time;
- Very long service life (grease life) at normal motor temperatures (+ 70 to + 120 °C);
- Satisfactory performance in cold climates;
- Quiet operation of the motor; and
- Re-lubrication possibility for open bearings.
Based on these requirements, SKF has selected and pre-tested bearing variants to support the development of electrical motors to meet the fire class F400 and beyond.
New test rig
SKF has designed and commissioned a new HEAT1 test rig (heat emergency approval test) for screening and emergency testing of bearing concepts to withstand heat up to 600 °C. HEAT1 allows testing under load and running conditions as specified in EN 12101-3 for electrical motors. As a first classification step, a screen test was made on various potential bearing variants with different materials, grease and cage combinations, including bearings with high-temperature greases ( .5).
In the screen test, three variants with SKF-selected electrical motor grease (A, B and C) did show superior emergency performance compared with variants with high-temperature silicone or PTFE greases (D, E, F and G), or with polymeric cage (H). This was due to better material combinations in rings and rolling elements. Subsequent function tests (copying the specific EN 12101-3 schedule for motors regarding time, speed and temperature) went well for the two prime candidates. These two bearing types can be used in motors that need to fulfil the F400 and F600 requirements ( table 1). The function tests showed that the F600 class is achievable for bearings without the need for a bifurcated design. The fire resistance of the electrical windings, however, is the limiting factor, and it is in the range of 400 °C.
SKF bearings used within fire-safe designs will normally be supplied and certified with the electrical motor. Retrofitting of existing fan motors using high-temperature greases is also desirable to reduce operating costs and noise levels, and to allow an increase in safety over time. To assist such work, SKF can offer testing and engineering knowledge within this field to enable recertification without need for retesting of complete ventilator and motor ranges.
Sales contact:
Click on SKF offices worldwide (right hand column)
Then click on go to country site (right hand column)
Select your country to find the contact details