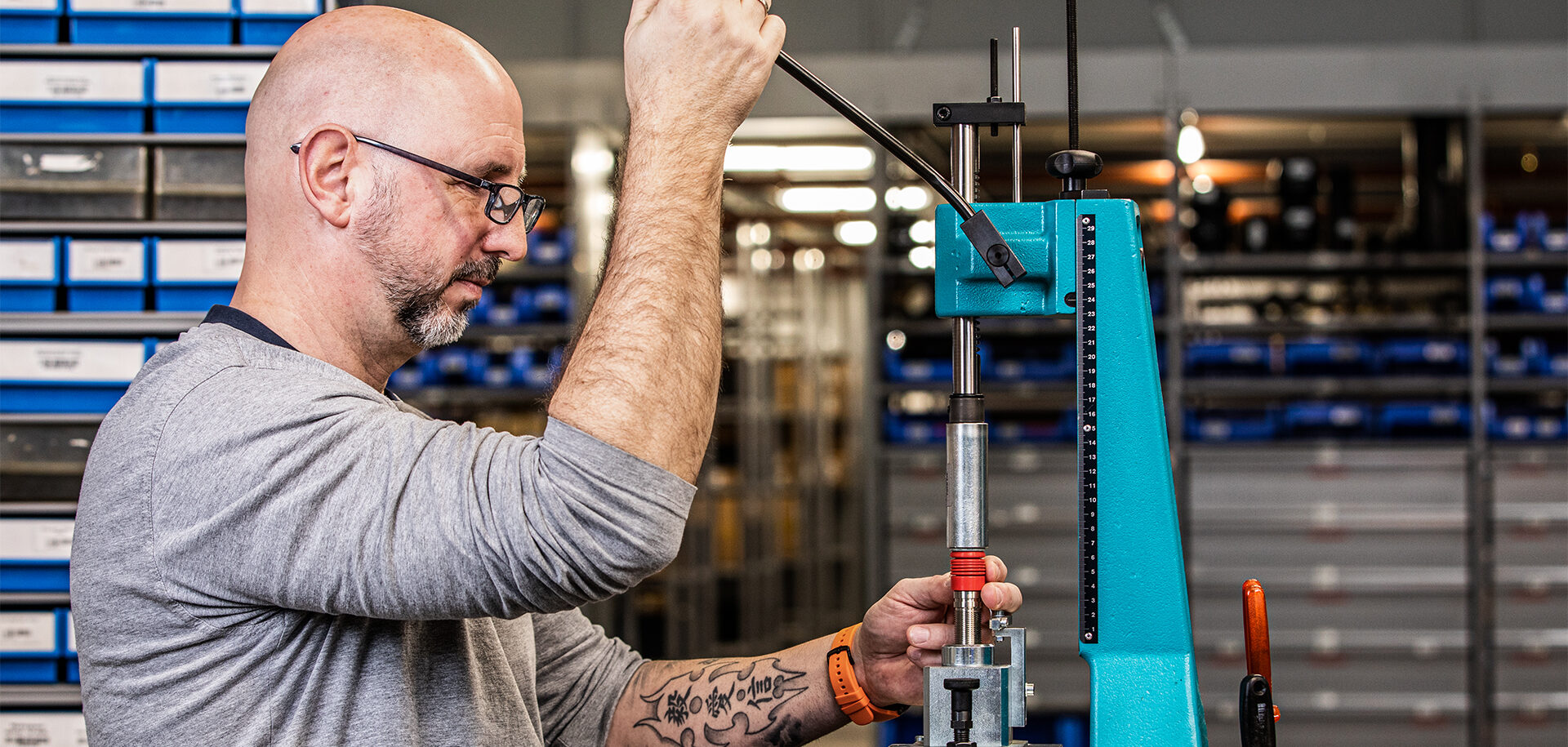
Asombrados pero no sorprendidos
La tecnología de sellado de SKF ha ayudado a ACE a transformar la confiabilidad de sus amortiguadores en miniatura en los entornos de trabajo más exigentes.
“La finalidad de nuestros productos es asegurar la parada controlada de una masa en movimiento”, explica Christian Alscher, gerente de desarrollo de ACE. Esa tarea sencilla es imprescindible para el funcionamiento seguro de cualquier tipo de máquina y dispositivo, desde equipos de manejo de materiales y sistemas de automatización de fábricas hasta las compuertas de las esclusas de canales o los mecanismos que controlan los gigantescos telescopios astronómicos.
Fundada en Detroit, Michigan, en 1963, ACE Stoßdämpfer (denominada ACE Controls en los Estados Unidos) desarrolló el primer amortiguador industrial regulable del mundo y definió una categoría de componentes, actualmente integrados en millones de aplicaciones en todo el mundo. Hoy, la empresa fabrica una amplia gama de productos que se utilizan en los ámbitos de automatización, control de movimientos, aislamiento de vibraciones y seguridad. Sus amortiguadores se suministran con diámetros entre 5 y 130 mm, y longitudes de carrera entre 23 mm y más de 1 m.
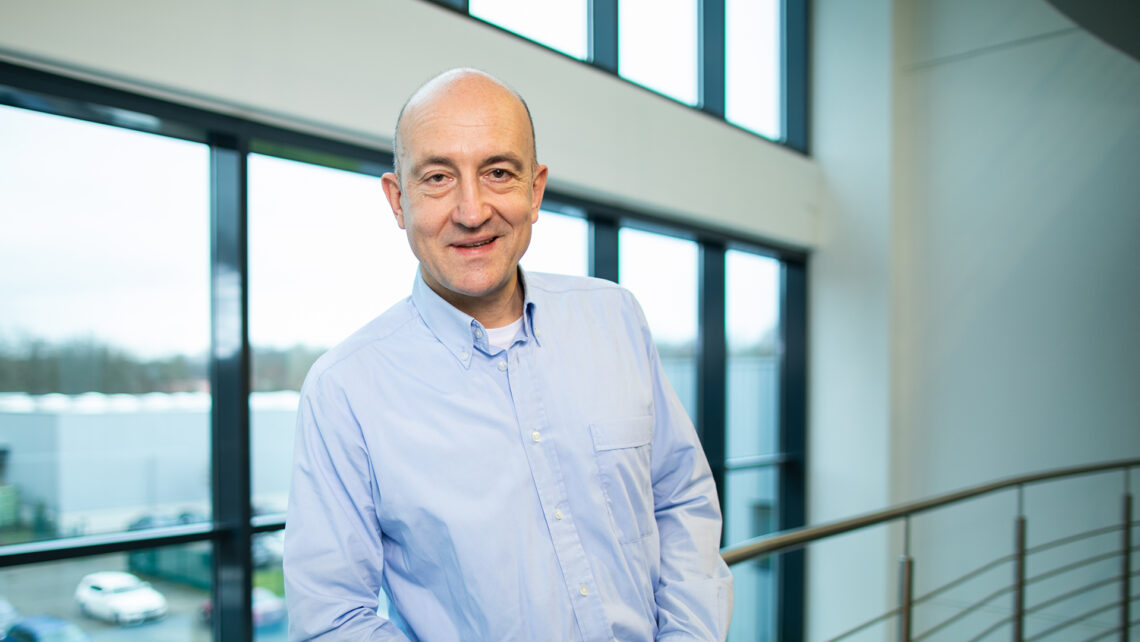
Para prevenir daños
Los productos de ACE también admiten una amplitud extraordinaria de ciclos de trabajo. Cuando el diseñador de equipos especifica un amortiguador de emergencia ACE, lo hace con la esperanza de que raras veces se tenga que utilizar. Su función es parar la máquina de forma segura en el caso de producirse una falla global del sistema para evitar daños potencialmente catastróficos.
Otros productos de ACE son esenciales para el funcionamiento diario de las máquinas. Los amortiguadores PMCN en miniatura, por ejemplo, suelen especificarse para aplicaciones de producción de gran volumen, para apresar componentes expulsados de las máquinas herramienta o para detener actuadores de alta velocidad al final de su carrera. Con longitudes de carrera de entre 12 y 25 mm, las unidades PMCN pueden absorber hasta 136 Nm de energía por ciclo, generada por objetos que se desplazan a velocidades de hasta 6 m/s. Estos dispositivos compactos deben funcionar sin fallar durante varios millones de ciclos, sin precisar ajustes o intervenciones de mantenimiento.
Las unidades PMCN utilizan una membrana rodante especial que proporciona un sellado estático y dinámico entre un pistón y un cilindro lleno de aceite. Es una solución ingeniosa que requiere menos componentes y ocupa mucho menos espacio que los diseños convencionales de amortiguadores. Y como las unidades están selladas herméticamente, no necesitan mantenimiento.
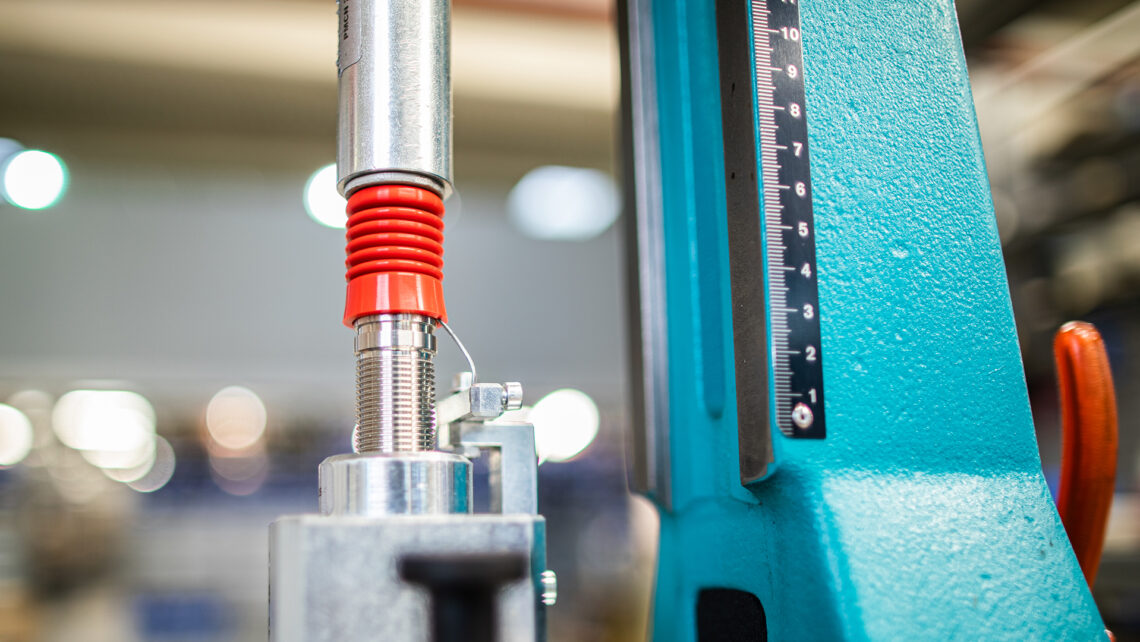
Para entornos industriales exigentes
Sin embargo, mantener estos innovadores amortiguadores en funcionamiento en entornos industriales exigentes requiere varios niveles de protección. La exposición a líquidos, como los refrigerantes utilizados para el mecanizado, puede hacer que la membrana se hinche y deje de funcionar. Por lo tanto, debe protegerse de la contaminación con un fuelle externo. Inicialmente, ACE ofrecía un fuelle de PTFE moldeado provisto de un muelle metálico interno que devolvía el pistón a su posición inicial entre accionamientos. Sin embargo, la combinación de metal y polímero resultó problemática en el uso a largo plazo; el muelle podía rasgar el delicado PTFE y provocar fallas prematuras.
“Empezamos a recibir quejas de los clientes, que nos decían que el producto no alcanzaba la vida útil que habíamos prometido”, recuerda Alscher. “En cuanto comprendimos que existía un problema, nos pusimos a trabajar en una solución mejor”. El equipo de ACE entendió que el mayor punto débil del fuelle original residía en su diseño híbrido. Como el PTFE carecía de pretensión intrínseca, el muelle interno era necesario para devolver el amortiguador a su posición inicial después del accionamiento. El equipo de diseño se puso a buscar un material alternativo capaz de ejecutar simultáneamente las funciones de sellado y de retorno a la posición inicial.
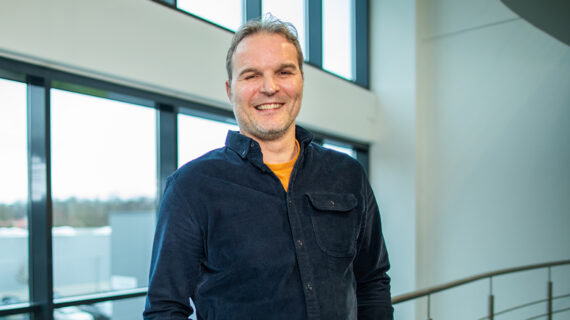
Ahora, lo habitual es que estas unidades sigan funcionando sin fallas tras uno o dos millones de ciclos, o incluso más.
Jörg Küchmann
Gerente de diseño de ACE
Innovación en polímeros
Tras evaluar varios materiales de diferentes proveedores, la búsqueda de una solución más sencilla y más confiable guió al equipo de diseño de ACE hacia SKF. Ingenieros de las dos empresas se reunieron por primera vez en 2013 para abordar el problema del fuelle. Encontraron la solución en la biblioteca de materiales especializados TPU H-ECOPUR® de SKF, muy utilizados en la producción de sellos para aplicaciones exigentes.
El material específico identificado por el equipo de SKF es especialmente resistente a los refrigerantes, lubricantes, medios de limpieza y vapor de agua. Y lo que es mejor, es lo suficientemente elástico como para devolver el amortiguador a la posición inicial sin necesidad de un muelle adicional.
ACE y SKF trabajaron juntas para perfeccionar el concepto básico, optimizando el grosor de las paredes y la geometría del fuelle para garantizar un rendimiento ideal. El diseño se apoyó sustancialmente en las capacidades de fabricación especializadas de SKF, y se utilizaron los avanzados equipos de mecanizado CNC de la empresa para producir tanto los prototipos como los fuelles definitivos.
Más sencillo, más rápido y más duradero
Gracias a la resistencia y resiliencia del ECOPUR, SKF y ACE también pudieron implementar otras mejoras que agilizaron el proceso de ensamblaje. Crearon un reborde que permite al fuelle encajar rápida y fácilmente en una ranura del cuerpo exterior del amortiguador. Este cambio sustituyó a una rosca interna, reforzada con adhesivo, utilizada hasta entonces para sujetar el diseño original de PTFE.
“La posibilidad de encajar el fuelle a presión fue un plus inesperado para nosotros”, admite Jörg Küchmann, gerente de diseño de ACE. “Al poder prescindir del adhesivo para unir el fuelle, se consiguió eliminar otro posible modo de falla. Por otra parte, el producto ahora es más rápido y fácil de ensamblar”. Desde su amplia experiencia en el diseño de uniones encajadas a presión para otros productos ECOPUR, el equipo de SKF pudo sugerir la combinación ideal de geometrías de reborde y ranura para garantizar un ajuste seguro y confiable.
Los nuevos fuelles han transformado la confiabilidad de la gama PMCN de ACE. “Bajo las condiciones más difíciles, los clientes que utilizaban los fuelles antiguos reportaban fallas después de menos de 100 000 ciclos”, afirma Küchmann. “Ahora, lo habitual es que estas unidades sigan funcionando sin fallas tras uno o dos millones de ciclos, o incluso más”. Por su tamaño reducido, alto rendimiento y excelente confiabilidad, el producto se ha convertido en un éxito de ventas.
La incorporación del fuelle ECOPUR ha ayudado a ACE a llevar la gama PMCN a mercados nuevos. El material del fuelle cumple las exigencias europeas y de la FDA de los EE. UU. para aplicaciones que están en contacto con productos farmacéuticos o con alimentos y bebidas, por ejemplo, y ACE ahora produce versiones especiales del amortiguador hechas con acero inoxidable para los fabricantes de alimentos, rellenadas con un aceite apto para el contacto con alimentos.
Tras casi diez años de colaboración, SKF y ACE siguen trabajando juntos en desarrollos y diseños nuevos, y proyectan incorporar el innovador fuelle ECOPUR en amortiguadores PMCN de mayor tamaño y ponerlos a disposición de los clientes que los necesiten.
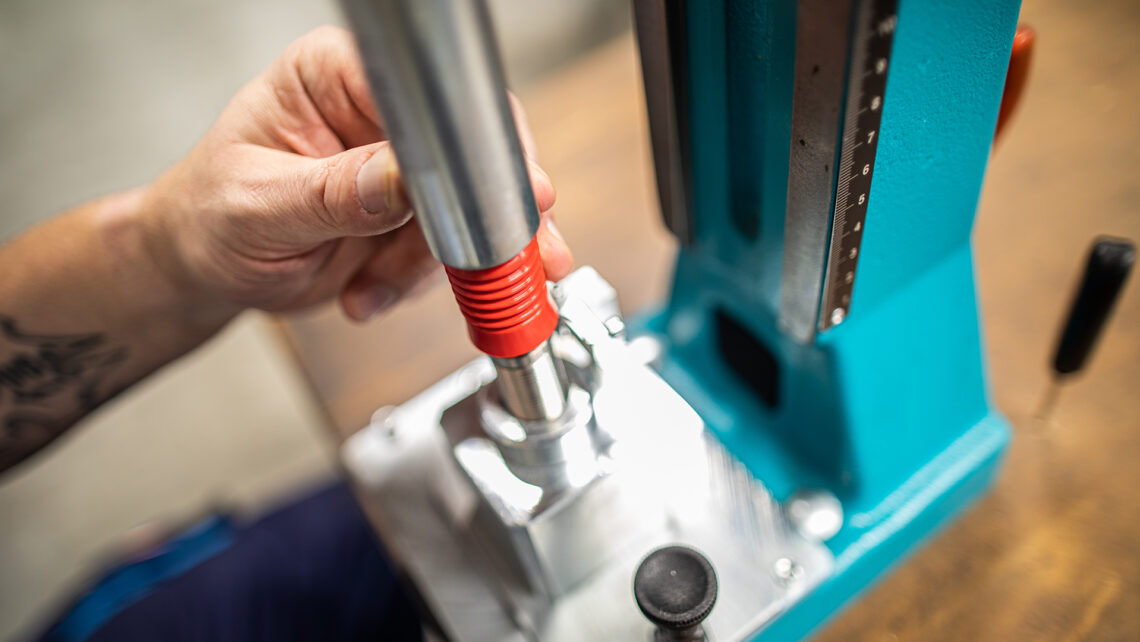