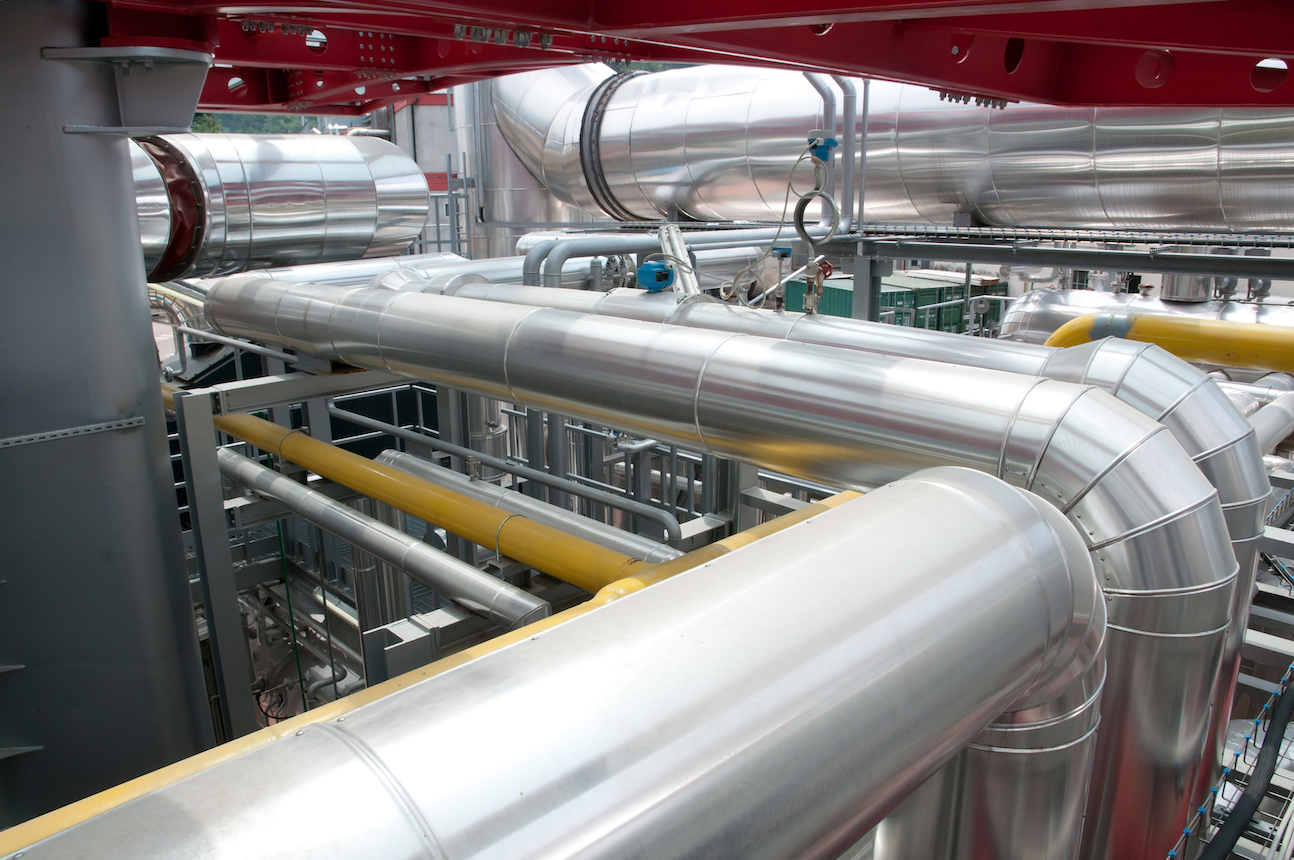
Capturar la energía perdida
Volvo está valorando implantar la tecnología KERS (Sistema de recuperación de energía cinética) en sus turismos. Un estudio piloto reciente, en el que ha participado SKF, ha obtenido resultados prometedores que podrían materializarse en productos nuevos.
Datos
Volvo Car Group
Historia: El primer coche Volvo en serie se fabricó en Gotemburgo, Suecia, en 1927.
Mercados más importantes: Estados Unidos, Suecia, China, Alemania y Reino Unido.
Propiedad de: Zhejiang Geely Holding (Geely Holding), China.
Oficinas: Sede central en Gotemburgo. Oficinas en Shanghái y Chengdu, China, desde 2011.
Enlaces relacionados
Contacto de venta
Jorgen Bokmark, Jorgen.Bokmark@skf.com
Cuando un conductor pisa el freno en un turismo convencional, gran parte de la energía producida por la inercia del vehículo se convierte en calor y se pierde.
Esto supone desperdiciar una energía gestada, en gran medida, por el motor. Ahora, la multinacional del sector de la automoción Volvo Cars está estudiando cómo recuperar parte de la energía generada durante el frenado para que el vehículo pueda utilizarla cuando más la necesite.
En el departamento de I+D de la división de transmisiones del grupo Volvo, a las afueras de Gotemburgo, Suecia, Tomas Hannebäck nos presenta el reluciente prototipo del sistema de recuperación de energía cinética (KERS) que ha desarrollado la empresa.
Aunque en los coches de Fórmula 1 se utilizan distintas modalidades de tecnología KERS, Hannebäck, director de ingeniería de transmisiones del Grupo, explica que Volvo es el primer fabricante de automóviles que ha desarrollado un coche de tracción delantera y motor de combustión interna que lleva un volante de inercia KERS ajustado al eje trasero.
“Ahora estamos barajando distintas opciones con potenciales proveedores para comercializar esta aplicación en coches Volvo”, continúa.
El equipo de Gotemburgo ha conseguido adaptar el sistema a un Volvo S60 T5, reconstruido especialmente para el proyecto. Las fuentes de potencia convencionales y no convencionales del vehículo están situadas en lugares distintos. El motor de gasolina impulsa las ruedas delanteras, mientras que la unidad KERS acciona las ruedas traseras.
El pilar del proyecto es el volante de inercia KERS. Pesa 6 kilos y gira a velocidades de hasta 60.000 rpm en un recipiente sellado al vacío. Durante la conducción, el volante de inercia captura la energía que se genera en el frenado y la almacena hasta un máximo de 30 minutos. Esta energía puede liberarse cuando se necesite para aumentar la aceleración.
La energía se transfiere desde los frenos al volante a través de una transmisión continuamente variable (CVT), que luego la transfiere al eje trasero durante la aceleración.
La tecnología KERS puede sumar 60 kilovatios, o el equivalente a otros dos cilindros de potencia, a un motor de cuatro cilindros.
Se cree que la tecnología KERS ayudará a cumplir el objetivo de la UE de reducir las emisiones de la flota de turismos hasta un valor medio de 95 gramos de CO2 por kilómetro en 2020, bastante menos que la media de 158,7 g/km en 2007.
En el desarrollo del volante de inercia KERS participaron casi todos los departamentos de Volvo Cars, desde los de electrónica y seguridad pasiva, hasta los que se dedican al motor y al chasis. El proyecto piloto finalizó en octubre de 2012, tras dos años de trabajo.
Se pidió a los colaboradores externos Flybrid Automotive Ltd. y Torotrak que desarrollaran una serie de componentes críticos, incluyendo el volante de fibra de carbono y la CVT. Luego éstos se adaptaron a las necesidades del Volvo S60 T5.
El coste total del proyecto fue de 20 millones de coronas suecas (2,2 millones de euros). Volvo Car Group aportó unos 11 millones de coronas (1,2 millones de euros). El resto lo pusieron la agencia de innovación sueca Vinnova, SKF y Volvo Trucks. A SKF se le encomendó evaluar el coste de producción del volante de inercia KERS de Volvo a escala industrial (ver recuadro).
Los conceptos mecánicos del volante no son nada nuevo para Volvo. El Grupo ya desarrolló un volante de inercia totalmente operativo en 1979, que se utilizó en varias pruebas. Su velocidad de rotación no pasó de las 12.000 rpm y no fue muy eficiente. Además, con un peso de 128 kilos, ocupaba mucho espacio y tendía a desestabilizar el coche.
Desde entonces, dice Mathias Jörgensson, ingeniero jefe responsable del desarrollo del prototipo, los componentes han mejorado mucho y han aparecido nuevos materiales. Estas innovaciones permiten al nuevo volante ligero de fibra de carbono girar a altas velocidades, sin que esto afecte a su capacidad energética, a su peso, o le haga perder perder el control de las fuerzas giroscópicas.
Uno de los grandes retos a los que se enfrentaron Jörgensson y su equipo fue integrar el volante de inercia y la CVT con los demás sistemas del Volvo S60 T5, incluyendo los frenos, la caja de cambios, el embrague y la transmisión.
Las relaciones de transmisión de la caja de cambios debían coordinarse con los parámetros del volante de inercia. El objetivo era asegurar la máxima eficiencia en el consumo de combustible y los cambios de marcha durante las transiciones y en la aceleración.
“Tuvimos que sincronizar todos estos sistemas para obtener un engranaje suave”, explica Jörgensson.
No fue fácil encontrar un lugar idóneo para el volante de inercia. En un primer momento los ingenieros pensaron colocarlo en el maletero, donde se encuentra la rueda de recambio. “No queríamos que interfiriera con el espacio para las maletas”, dice Jörgensson.
Finalmente se le encontró una nueva ubicación bajo la superficie trasera, apartada del maletero y de la rueda de recambio.
La evaluación de SKF
Volvo Car Corporation se puso en contacto con SKF a principios de 2011 y le pidió que evaluara los costes de producción del sistema KERS a escala industrial.
Esta labor corrió a cargo del Centro de Desarrollo de Automoción de SKF en Nieuwegein, Holanda, y supuso el estudio de cada uno de los 90 componentes utilizados por el sistema.
Los presupuestos para los componentes que podían fabricarse dentro de SKF fueron elaborados por las unidades de SKF pertinentes. SKF Aerospace, por ejemplo, elaboró el presupuesto para la llanta del volante de fibra de carbono. En el caso de los componentes susceptibles de externalizarse, como los sistemas hidráulicos, SKF pidió presupuestos a sus proveedores.
El presupuesto final del coste del sistema incluyó la fabricación, compra, montaje y prueba de los componentes.
Según Mark Verbakel, jefe del proyecto, los resultados finales del estudio se presentaron a Volvo en abril de 2012 y fueron bien acogidos.
Volvo inició su andadura en 1926 como filial automovilística del Grupo SKF. Aunque Volvo se escindió de SKF en 1935, SKF es proveedor de la compañía automovilística desde hace mucho tiempo.