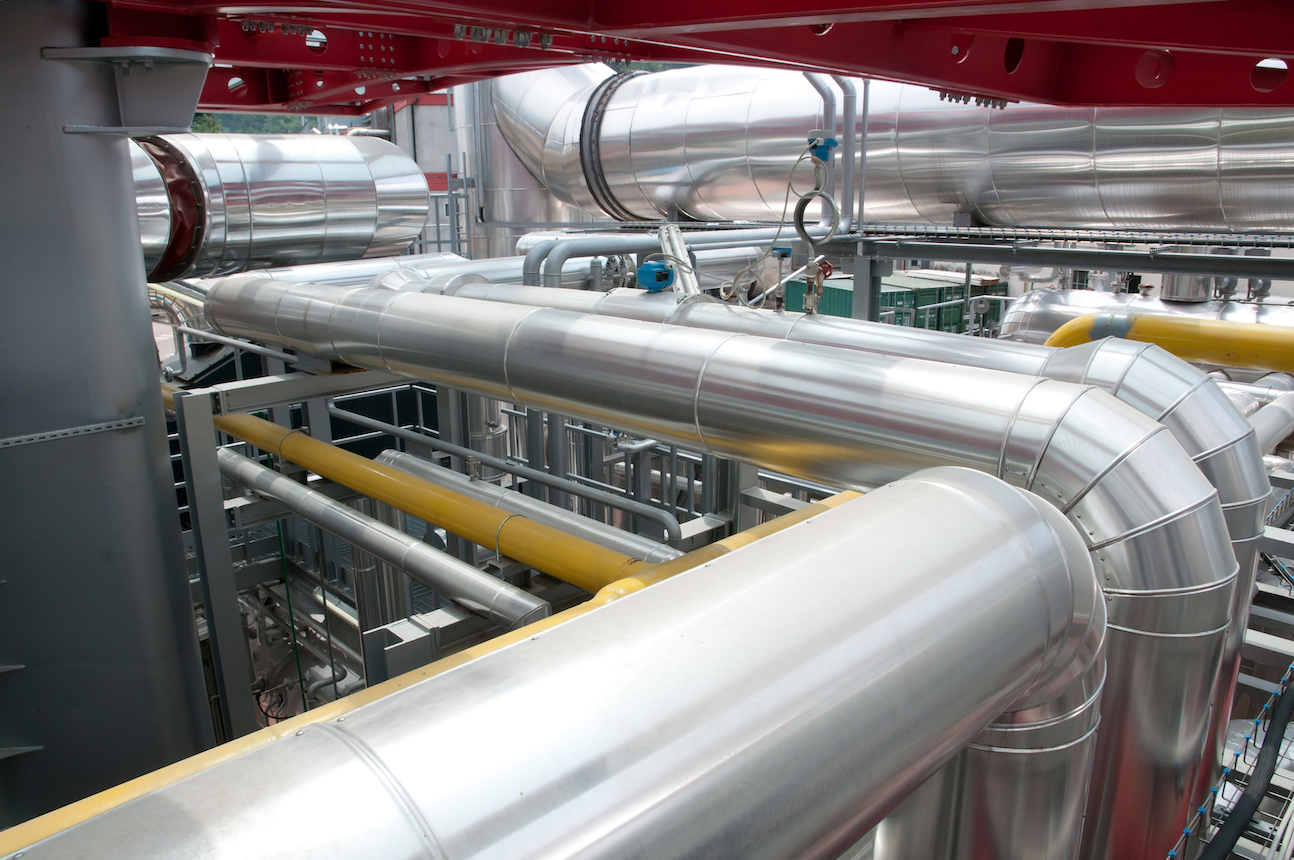
Capturing lost energy
Volvo Car Corporation is exploring the potential for using Kinetic Energy Recovery System (KERS) technology in its passenger vehicles. A recent pilot study involving SKF has yielded encouraging results that could lead to new consumer products.
When a driver applies the brakes in a conventional passenger car, much of the energy from the vehicle’s inertia is converted to heat and lost. It’s a waste of valuable energy that has been built up, largely by the engine. Now global carmaker Volvo Cars is exploring ways to recover some of the energy expended during braking so that it can be reused within the vehicle when it’s most needed. At the Volvo Car Group transmission division’s R&D department just outside Gothenburg, Sweden, Tomas Hannebäck is standing beside a shiny prototype of the Kinetic Energy Recovery System (KERS) that the company has developed. While various forms of KERS technology are currently used in Formula 1 racing cars, Hannebäck, the Group’s director of Transmission Engineering, explains that Volvo is the first automobile manufacturer to develop a front-wheel-driven, combustion-engine car with the KERS flywheel technology fitted to the rear axle. “We are now exploring various options with potential suppliers to industrialize the concept for Volvo cars,” he says. The team in Gothenburg has successfully adapted the system to a Volvo S60 T5, which was specially rebuilt for the project. The vehicle’s conventional and unconventional power sources are located separately. The petrol engine powers the front wheels, while the KERS unit drives the rear wheels. The KERS flywheel is the heart of the project. It weighs six kilograms and rotates at up to 60,000 rpm in a vacuum-sealed container. When the vehicle is being driven, the flywheel captures energy generated by braking and stores it for up to 30 minutes. This energy can be released – when required – to boost acceleration. Power is transferred from the brakes to the flywheel via a continuously variable transmission (CVT), which then transfers the power to the rear axle during acceleration. The KERS technology can effectively add up 60 kilowatts, or the equivalent of another two cylinders of power to a four-cylinder engine.
On the energy-reduction side, the KERS technology is expected to help meet the EU’s reduced passenger car emissions target of 95 grams of CO2 per kilometre (g/km) by 2020 for a fleet average – a significant drop from 158.7 g/km for a 2007 fleet average. The development of the KERS flywheel was the result of an intensive cross-functional effort, involving just about every department within Volvo Cars, from electronics and safety to engine and chassis. The pilot project was completed in October 2012, after two years of work. Outside partners Flybrid Automotive Ltd. and Torotrak were called on to develop a range of critical parts for the concept, including the carbon-fibre flywheel and the CVT. The supplied parts were then adapted to the requirements of the Volvo S60 T5. The total cost of the project was 20 million Swedish kronor (2.2 million euros). Volvo Car Group contributed some 11 million kronor (1.2 million euros), and the remaining costs were met by Swedish innovation agency Vinnova, SKF and Volvo Trucks. SKF’s role in the project was to evaluate the cost of producing the Volvo KERS flywheel on an industrial scale (see sidebar). Mechanical flywheel concepts are not entirely new to Volvo. The Group developed a fully operational flywheel in 1979 that was used in several tests. It spun at just 12,000 rpm and was not very efficient, and its 128-kilogram weight meant it was bulky and tended to destabilize the car. Mathias Jörgensson, a lead engineer in the development of the prototype, says that since then there have been dramatic improvements in components and new materials have become available. Such innovations enable the new, lightweight, carbon-fibre flywheel to spin at its high speed without sacrificing energy capacity and weight or losing control over gyro forces. A major challenge for Jörgensson and his team was to integrate the flywheel and CVT with all of the Volvo S60 T5 systems, including the brakes, gears, clutch and transmission. The gear ratios had to be coordinated with the parameters for the flywheel. This was to make sure the most-efficient fuel economy and performance of gearshifts were realized during transitions from standstill and acceleration while driving at higher speeds. “We had to synchronize all these systems to provide smooth engagement,” Jörgensson says. Finding an unobtrusive location for the flywheel proved a challenge. Eventually, the engineers settled on placing it in the trunk where the spare tyre was located.“We did not want it to interfere with baggage space,” Jörgensson says. A position under the rear floor has subsequently been identified where the flywheel can be positioned without conflict with the trunk area or spare wheel. SKF was approached by Volvo Car Corporation in early 2011 and asked to evaluate the costs of producing the KERS flywheel system on an industrial scale. The evaluation work was undertaken by the SKF Automotive Development Centre at Nieuwegein in the Netherlands and involved assessing each of the 90 components used by the system. Estimates for parts that could potentially be made by SKF were supplied by the relevant SKF unit. SKF Aerospace, for example, provided the estimate for the carbon-fibre flywheel rim. For parts likely to be outsourced, such as hydraulics, SKF requested quotations from suppliers. The final system cost estimate included component manufacturing, purchasing, assembly and testing. Project manager Mark Verbakel says the final results of the study were presented to Volvo in April 2012 and met with a positive reaction. Volvo started life in 1926 as a subsidiary automobile company within the SKF Group. Although Volvo was spun off from SKF in 1935, SKF has long been a supplier to the automobile company. Evaluation by SKF