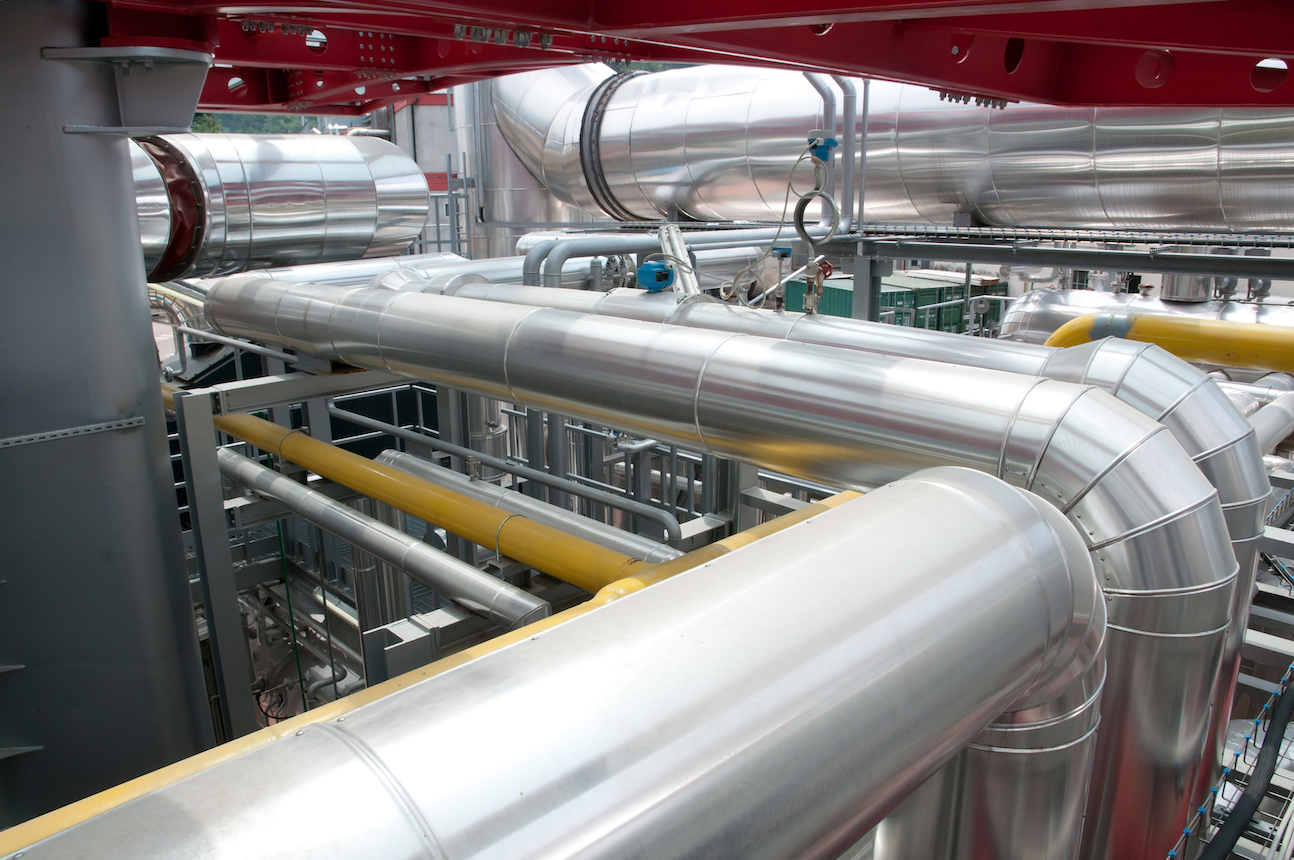
Le plein d’énergie
Volvo Car Corporation explore la possibilité d’installer un système de récupération de l’énergie cinétique sur ses voitures particulières. Une récente étude pilote à laquelle SKF a participé a donné de bons résultats, lesquels pourraient déboucher sur de nouveaux produits.
En bref
Volvo Car Group
Histoire : première voiture fabriquée en série à Göteborg, en Suède, en 1927.
Principaux marchés : USA, Suède, Chine, Allemagne et Grande-Bretagne.
Propriétaire : le Zhejiang Geely Holding, constructeur automobile chinois.
Domiciliation : siège social à Göteborg, représentations à Shanghai et Chengdu, en Chine, depuis 2011.
Liens apparentés
Contact commercial
Jorgen Bokmark, Jorgen.Bokmark@skf.com
Lorsqu’un automobiliste freine, une grande partie de l’énergie créée par l’inertie du véhicule est transformée en chaleur et perdue. On gaspille là une énergie précieuse qui a été produite en grande partie par le moteur. Le grand constructeur mondial Volvo Cars étudie les moyens de récupérer une partie de cette énergie pour que le véhicule la réutilise quand il en a le plus besoin.
Au service de R&D de la division transmission du Volvo Car Group à Göteborg, en Suède, Tomas Hannebäck, responsable systèmes d’ingénierie de transmission, pose à côté d’un prototype étincelant du système de récupération de l’énergie cinétique (KERS) conçu par l’entreprise. Il explique que Volvo est le premier constructeur automobile à développer une voiture à transmission avant, avec moteur thermique, équipée sur l’essieu arrière de la technologie KERS par volant d’inertie, et ce alors que diverses formes de cette technologie sont déjà appliquées sur les monoplaces de Formule 1. « Nous explorons plusieurs options en collaboration avec d’éventuels fournisseurs en vue d’industrialiser le concept sur les voitures particulières Volvo. »
L’équipe de Göteborg a réussi à adapter le système à une Volvo S60 T5 spécialement modifiée pour le projet. La source de propulsion habituelle et celle moins courante sont séparées : le moteur essence entraîne les roues avant, le KERS les roues arrière.
Le volant d’inertie de ce dernier est le cœur du concept. Il pèse 6 kg et tourne à 60 000 tr/min dans un boîtier sous vide. Lorsque le véhicule roule, le volant d’inertie recueille l’énergie générée par le freinage et la stocke pendant 30 minutes au maximum. L’énergie est distribuée pour booster l’accélération si nécessaire. Elle est transmise du freinage au volant d’inertie par l’intermédiaire d’un variateur de vitesse mécanique CVT, lequel la transfère ensuite à l’essieu arrière au moment de l’accélération.
La technologie KERS peut contribuer à hauteur de 60 kW à la puissance du véhicule, soit l’équivalent de deux cylindres supplémentaires pour un moteur en comprenant quatre.
Sur le plan environnemental, le système devrait permettre d’atteindre le seuil fixé par l’Union européenne, soit 95 grammes de CO2 par kilomètre (g/km), pour la moyenne du parc de voitures neuves d’ici 2020, une baisse considérable par rapport au seuil fixé à 158,7 g/km en 2007.
Le développement du volant d’inertie du KERS est le produit d’un travail intensif transversal, qui a impliqué la quasi-totalité des services de Volvo Cars, des systèmes électroniques à la sécurité en passant par le châssis et le moteur. Le projet pilote s’est achevé au bout de deux ans en octobre 2012.
Le constructeur a fait appel à deux partenaires, Flybrid Automotive et Torotrak, pour mettre au point les composants stratégiques du concept, notamment le volant d’inertie en fibres de carbone et le variateur de vitesse mécanique CVT. Les pièces fournies ont ensuite été adaptées à la configuration de la Volvo S60 T5.
Le coût total du projet s’est élevé à 2,2 millions d’euros. Le Volvo Car Group a contribué à hauteur de 1,2 million d’euros et l’agence suédoise pour l’innovation Vinnova, SKF et Volvo Trucks ont investi le reste. Le rôle de SKF a consisté à évaluer les coûts de production du volant d’inertie Volvo à l’échelle industrielle (voir encadré).
Le concept du volant d’inertie mécanique n’est pas une nouveauté chez Volvo. Le groupe avait déjà développé un modèle tout à fait opérationnel en 1979, lequel avait fait l’objet de nombreux essais. Il ne tournait qu’à 12 000 tr/min et n’était pas très efficace. Son poids de 128 kg en faisait un composant volumineux qui avait tendance à déséquilibrer la voiture.
Mathias Jörgensson, l’un des ingénieurs chargés du développement du prototype, précise que depuis, on a fait des progrès spectaculaires sur le plan des composants et mis au point de nouveaux matériaux. Ces innovations permettent au nouveau volant d’inertie en fibres de carbone de tourner à très haute vitesse sans perdre le contrôle de l’effet gyroscopique et sans transiger sur le rendement énergétique et le poids.
L’une des principales difficultés pour Mathias Jörgensson et son équipe a été d’intégrer le volant et le variateur de vitesse mécanique CVT à tous les dispositifs de la Volvo S60 T5, notamment aux freins, à la boîte de vitesses, à l’embrayage et à la transmission.
Les rapports de transmission devaient être coordonnés avec les paramètres du volant d’inertie afin d’obtenir une bonne économie de carburant et le meilleur comportement possible du changement de rapports à chaque démarrage et à chaque accélération à vitesse élevée. « Il nous fallait synchroniser tous ces systèmes pour assurer des engagements tout en douceur. »
Cela n’a pas été facile de trouver le bon emplacement pour le volant d’inertie. En fin de compte, les ingénieurs ont décidé de l’installer dans le coffre arrière près de la roue de secours. « Nous ne voulions pas réduire l’espace disponible », confie Mathias Jörgensson.
Le volant d’inertie sera donc situé sous le plancher et n’empiètera pas sur l’espace réservé aux bagages et à la roue de secours.
Une évaluation signée SKF
Volvo Car Corporation a contacté SKF début 2011 pour lui demander d’évaluer le coût de production d’un système de volant d’inertie KERS à échelle industrielle. Entrepris par le SKF Automotive Development Centre de Nieuwegein, aux Pays-Bas, ce travail consistait à estimer chacun des 90 composants du système.
Les devis portant sur les pièces pouvant être éventuellement fabriquées par SKF ont été fournis par chaque division SKF concernée. Ainsi, SKF Aerospace s’est occupée du devis portant sur la jante en fibre de carbone du volant d’inertie. Pour les composants susceptibles d’être sous-traités, tels que les systèmes hydrauliques, SKF a demandé à ses fournisseurs de lui livrer leurs estimations.
Le devis final incluait la fabrication, l’achat, l’assemblage et les essais.
Selon le chef de projet, Mark Verbakel, les conclusions de l’étude qui ont été présentées à Volvo en avril 2012 ont reçu un accueil favorable.
À sa création, en 1926, Volvo était une filiale du groupe SKF. Devenu indépendant en 1935, le constructeur automobile est resté un fidèle client du fabricant de roulements.