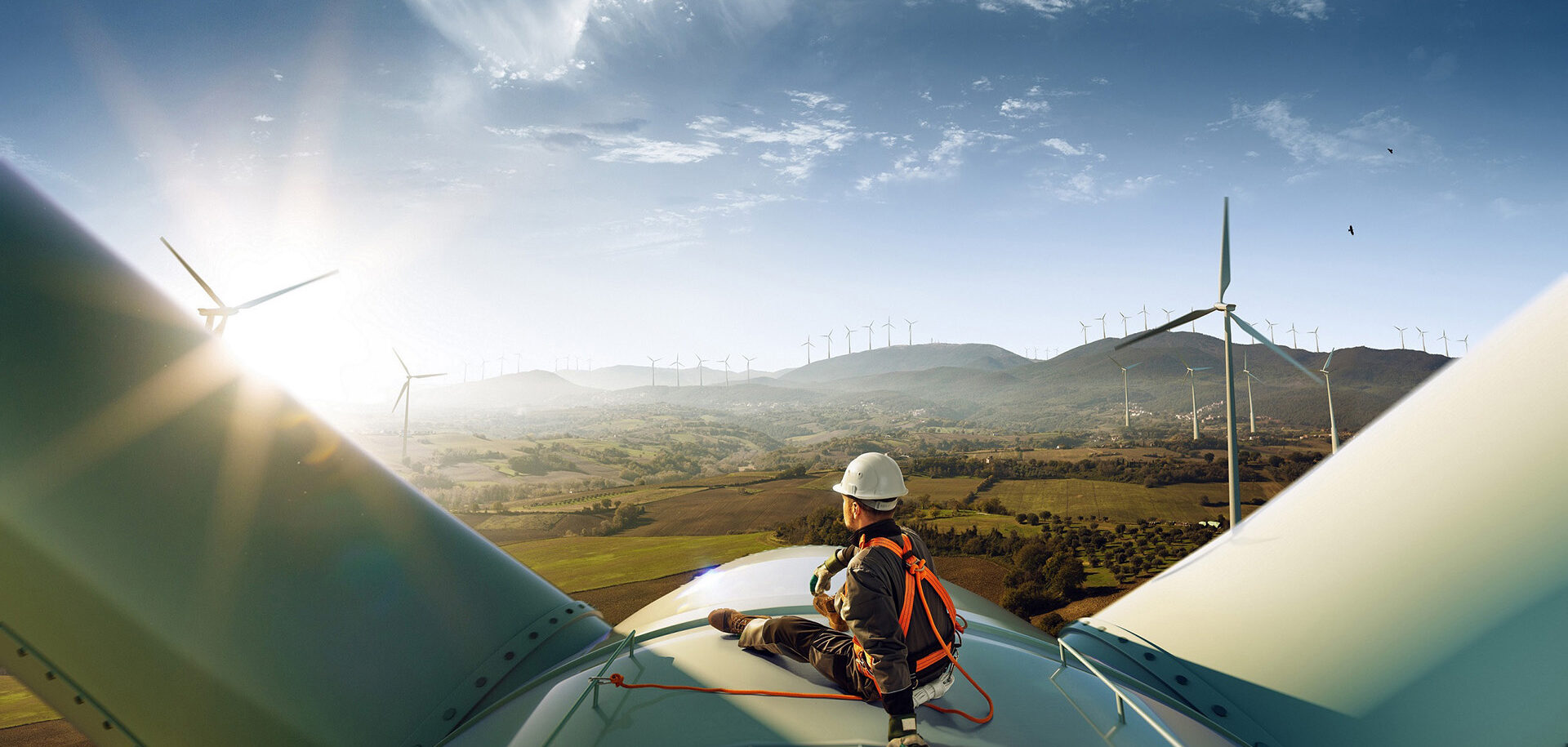
Reducir el costo normalizado de la energía
Las cajas de engranajes y los rodamientos principales son componentes fundamentales de las turbinas eólicas. Cualquier falla de estos componentes puede comportar pérdida de ingresos, costosas reparaciones de urgencia y, en última instancia, un encarecimiento del costo de producción de energía. SKF y el fabricante de cajas de engranajes ZF han aunado fuerzas para llevar el mantenimiento predictivo de las cajas de engranajes de las turbinas eólicas al próximo nivel. Su objetivo es apoyar a los propietarios de parques eólicos, reducir su costo normalizado de la energía (Levelized Cost of Energy, LCoE) y mejorar la rentabilidad de las energías renovables.
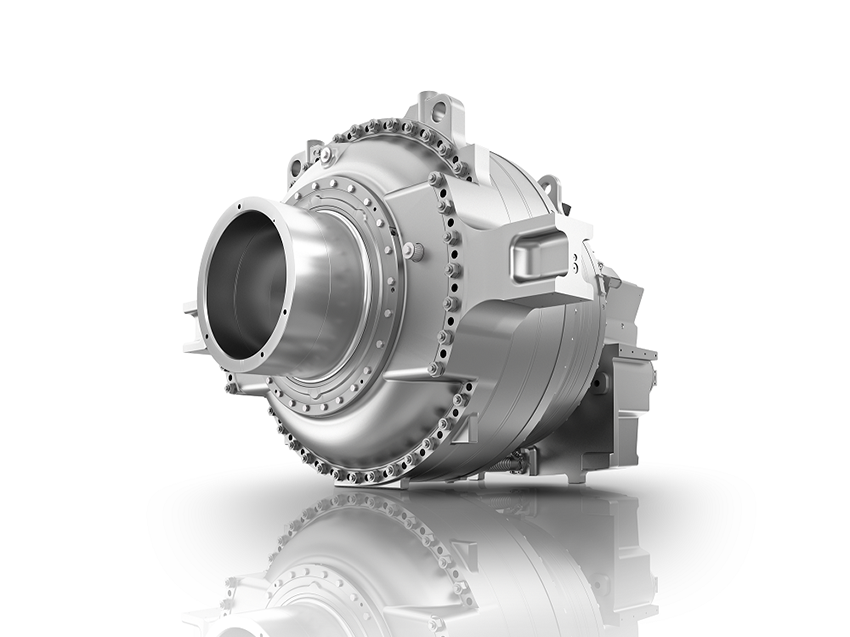
Para garantizar un precio competitivo para la electricidad producida por las turbinas eólicas, es imprescindible que tengan un funcionamiento confiable. Una solución es reducir el costo normalizado de la energía (LCoE) a través del mantenimiento predictivo. El LCoE es un concepto que contempla el costo de la producción de energía a lo largo de la vida útil de la turbina eólica. Reducir el mantenimiento no planificado mejora la rentabilidad pero no necesariamente aumenta la producción ni tampoco garantiza una producción más estable. Sin embargo, evitar fallas recurrentes reduce el costo del ciclo de vida de la turbina a la vez que ayuda a aumentar la cantidad absoluta de energía producida.
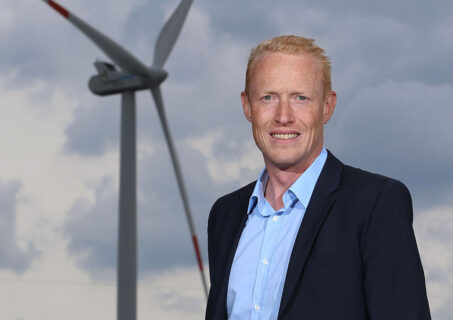
Hemos detectado una necesidad y nos hemos dado cuenta de que juntos podemos crear un valor agregado para el cliente
Joris Peeters, responsable de digitalización de la unidad de negocio de tecnología eólica de ZF
Simplificar procesos para crear valor agregado
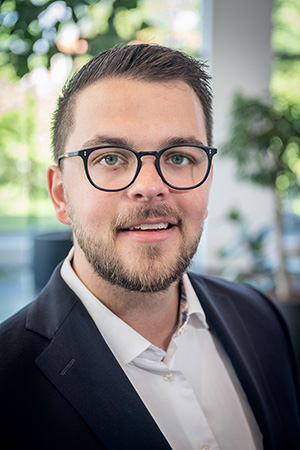
El monitoreo de condición remoto se adapta perfectamente a la industria eólica, ya que permite a los operadores de turbinas evaluar la maquinaria sin que la turbina deje de producir energía. Ahora, SKF y el fabricante de cajas de engranajes ZF han llevado el mantenimiento predictivo a un nuevo nivel, que simplifica enormemente el proceso para todos los actores y acorta más de un 85% el tiempo transcurrido hasta la reparación. El proyecto aprovecha la capacidad de los sensores de detectar anomalías, no solo en los rodamientos sino también en la caja de engranajes.
“Uno de los desafíos siempre ha sido la negativa de las grandes empresas a compartir datos”, explica Dennis Nordmark, gerente de digitalización de industrias energéticas en SKF. “Pero entre las dos empresas, acumulamos 150 años de conocimientos centrales. El hecho de integrar nuestros conocimientos ha supuesto un salto importante”.
Joris Peeters, responsable de digitalización de la unidad de negocio de tecnología eólica de ZF, agrega: “SKF y ZF han utilizado un proyecto piloto real de un año de duración para mostrar a los clientes todo lo que podemos conseguir juntos. Hemos detectado una necesidad y nos hemos dado cuenta de que juntos podemos crear un valor agregado para el cliente”.
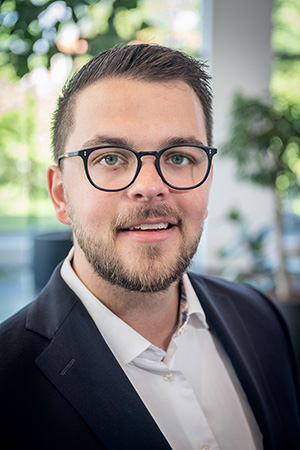
Simplificar procesos para crear valor agregado
El monitoreo de condición remoto se adapta perfectamente a la industria eólica, ya que permite a los operadores de turbinas evaluar la maquinaria sin que la turbina deje de producir energía. Ahora, SKF y el fabricante de cajas de engranajes ZF han llevado el mantenimiento predictivo a un nuevo nivel, que simplifica enormemente el proceso para todos los actores y acorta más de un 85% el tiempo transcurrido hasta la reparación. El proyecto aprovecha la capacidad de los sensores de detectar anomalías, no solo en los rodamientos sino también en la caja de engranajes.
“Uno de los desafíos siempre ha sido la negativa de las grandes empresas a compartir datos”, explica Dennis Nordmark, gerente de digitalización de industrias energéticas en SKF. “Pero entre las dos empresas, acumulamos 150 años de conocimientos centrales. El hecho de integrar nuestros conocimientos ha supuesto un salto importante”.
Joris Peeters, responsable de digitalización de la unidad de negocio de tecnología eólica de ZF, agrega: “SKF y ZF han utilizado un proyecto piloto real de un año de duración para mostrar a los clientes todo lo que podemos conseguir juntos. Hemos detectado una necesidad y nos hemos dado cuenta de que juntos podemos crear un valor agregado para el cliente”.
VER-PENSAR-ACTUAR
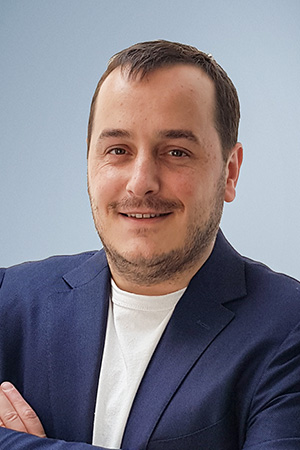
Joris Boeye, ingeniero de análisis de datos en ZF, explica el funcionamiento del sistema, que sigue el principio VER-PENSAR-ACTUAR: “cuando el sistema de monitoreo de condición (Condition Monitoring System, CMS) detecta una desviación, el análisis realizado por SKF genera una alerta. Disponemos de los datos de fabricación y los conocimientos del sistema necesarios para procesar la alerta: en eso consistiría la fase VER. A continuación, averiguamos en qué consiste la falla, localizamos la ubicación de la turbina y determinamos cuánto tiempo falta hasta que falle: es la fase PENSAR. Y por último, tramitamos la orden de trabajo y asignamos los técnicos y repuestos más adecuados. Eso sería la fase ACTUAR”.
Observa Nordmark: “el desafío consiste en combinar nuestros conocimientos centrales de la vibración de rodamientos con los conocimientos centrales de los científicos de datos de ZF. Los datos deben situarse en un contexto; de lo contrario, nunca se transformarán en información”.
El análisis de las desviaciones forma parte de los conocimientos centrales de SKF y ZF en sus campos respectivos, continúa. “Al igual que cuando un automóvil pasa sobre un bache, los sensores del CMS notan un ‘golpe’ cuando hay un problema en alguna parte de la caja de engranajes. Obviamente, detectar pequeñas diferencias de vibración en los rodamientos es mucho más difícil que sentir un bache en la carretera, pero el principio es similar. En el caso del automóvil, podemos detectar una anomalía a través de las ruedas y la suspensión. Nuestra experiencia como conductores nos ayuda a identificar que la causa más probable es un desperfecto de la calzada. Del mismo modo, los patrones de vibración de los rodamientos cambian cuando el eje está desalineado, por ejemplo. Los analistas de SKF y ZF, con sus conocimientos especializados, pueden determinar qué significan los cambios en las vibraciones, qué componente de la caja de engranajes puede causarlos, qué tipo de reparación es necesaria y en qué momento conviene realizarla.
“El objetivo es detectar posibles fallas antes de que provoquen una parada no planificada. Y cada hora cuenta: tomando como base un precio de 60 euros/MWh, las pérdidas de una turbina de 3,5 MW pueden ascender a 1800 euros diarios. Y si la detención dura cuatro semanas, puede suponer una pérdida de ingresos por valor de 55 000 euros”.
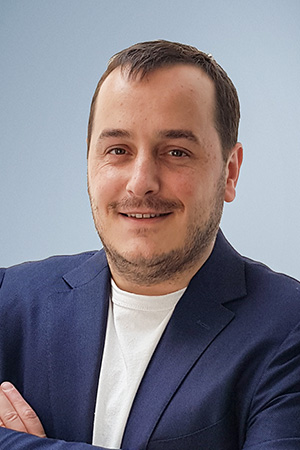
VER-PENSAR-ACTUAR
Joris Boeye, ingeniero de análisis de datos en ZF, explica el funcionamiento del sistema, que sigue el principio VER-PENSAR-ACTUAR: “cuando el sistema de monitoreo de condición (Condition Monitoring System, CMS) detecta una desviación, el análisis realizado por SKF genera una alerta. Disponemos de los datos de fabricación y los conocimientos del sistema necesarios para procesar la alerta: en eso consistiría la fase VER. A continuación, averiguamos en qué consiste la falla, localizamos la ubicación de la turbina y determinamos cuánto tiempo falta hasta que falle: es la fase PENSAR. Y por último, tramitamos la orden de trabajo y asignamos los técnicos y repuestos más adecuados. Eso sería la fase ACTUAR”.
Observa Nordmark: “el desafío consiste en combinar nuestros conocimientos centrales de la vibración de rodamientos con los conocimientos centrales de los científicos de datos de ZF. Los datos deben situarse en un contexto; de lo contrario, nunca se transformarán en información”.
El análisis de las desviaciones forma parte de los conocimientos centrales de SKF y ZF en sus campos respectivos, continúa. “Al igual que cuando un automóvil pasa sobre un bache, los sensores del CMS notan un ‘golpe’ cuando hay un problema en alguna parte de la caja de engranajes. Obviamente, detectar pequeñas diferencias de vibración en los rodamientos es mucho más difícil que sentir un bache en la carretera, pero el principio es similar. En el caso del automóvil, podemos detectar una anomalía a través de las ruedas y la suspensión. Nuestra experiencia como conductores nos ayuda a identificar que la causa más probable es un desperfecto de la calzada. Del mismo modo, los patrones de vibración de los rodamientos cambian cuando el eje está desalineado, por ejemplo. Los analistas de SKF y ZF, con sus conocimientos especializados, pueden determinar qué significan los cambios en las vibraciones, qué componente de la caja de engranajes puede causarlos, qué tipo de reparación es necesaria y en qué momento conviene realizarla.
“El objetivo es detectar posibles fallas antes de que provoquen una parada no planificada. Y cada hora cuenta: tomando como base un precio de 60 euros/MWh, las pérdidas de una turbina de 3,5 MW pueden ascender a 1800 euros diarios. Y si la detención dura cuatro semanas, puede suponer una pérdida de ingresos por valor de 55 000 euros”.
Mejorar el costo normalizado de la energía
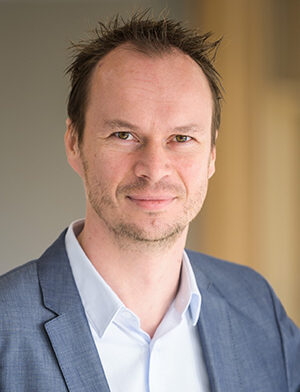
El proyecto piloto, realizado en un parque eólico con un centenar de turbinas eólicas, ha demostrado que es posible. El resultado ha sido una disminución del 60% de las inspecciones en campo no planificadas, una reducción del 85% del tiempo transcurrido hasta la reparación y un aumento del 0,4% de la producción anual de energía. El próximo paso será el lanzamiento comercial del programa durante 2021.
Raf Kerkhofs, gerente de desarrollo de negocios en SKF para la explotación y el mantenimiento de instalaciones eólicas, cree que el potencial es enorme. “Desde su conocimiento del funcionamiento de sus productos, tanto SKF como ZF pueden ayudar a sus clientes a plantear soluciones y mejoras de forma proactiva”, afirma.
Como sugiere Peeters, de ZF: “actualmente, estamos aplicando la nueva solución a sistemas CMS existentes. Más adelante podremos incorporarla en instalaciones nuevas. Podemos mejorar la configuración de las alarmas y, con el tiempo, incluso podríamos tener transmisiones mecánicas autónomas, dotadas desde fábrica con capacidad para activar sus propias reparaciones”.
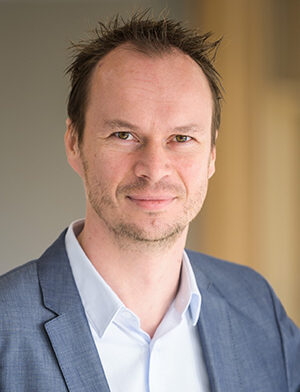
Mejorar el costo normalizado de la energía
El proyecto piloto, realizado en un parque eólico con un centenar de turbinas eólicas, ha demostrado que es posible. El resultado ha sido una disminución del 60% de las inspecciones en campo no planificadas, una reducción del 85% del tiempo transcurrido hasta la reparación y un aumento del 0,4% de la producción anual de energía. El próximo paso será el lanzamiento comercial del programa durante 2021.
Raf Kerkhofs, gerente de desarrollo de negocios en SKF para la explotación y el mantenimiento de instalaciones eólicas, cree que el potencial es enorme. “Desde su conocimiento del funcionamiento de sus productos, tanto SKF como ZF pueden ayudar a sus clientes a plantear soluciones y mejoras de forma proactiva”, afirma.
Como sugiere Peeters, de ZF: “actualmente, estamos aplicando la nueva solución a sistemas CMS existentes. Más adelante podremos incorporarla en instalaciones nuevas. Podemos mejorar la configuración de las alarmas y, con el tiempo, incluso podríamos tener transmisiones mecánicas autónomas, dotadas desde fábrica con capacidad para activar sus propias reparaciones”.
El sistema de monitoreo de condición SKF IMx
SKF IMx es la nueva generación de soluciones potentes y rentables dedicadas al monitoreo de condición de las turbinas eólicas. Se trata de una unidad de medición robusta que puede instalarse en parques eólicos tanto terrestres como marinos.
Las señales dinámicas recibidas desde el sistema se pueden configurar para una diversidad de sensores. Junto con el software SKF @ptitude Observer, el SKF IMx constituye un sistema completo para la detección y prevención temprana de fallas, genera recomendaciones automáticas para corregir condiciones existentes o inminentes, y permite un mantenimiento avanzado basado en la condición para mejorar la confiabilidad, la disponibilidad y el rendimiento de las máquinas.