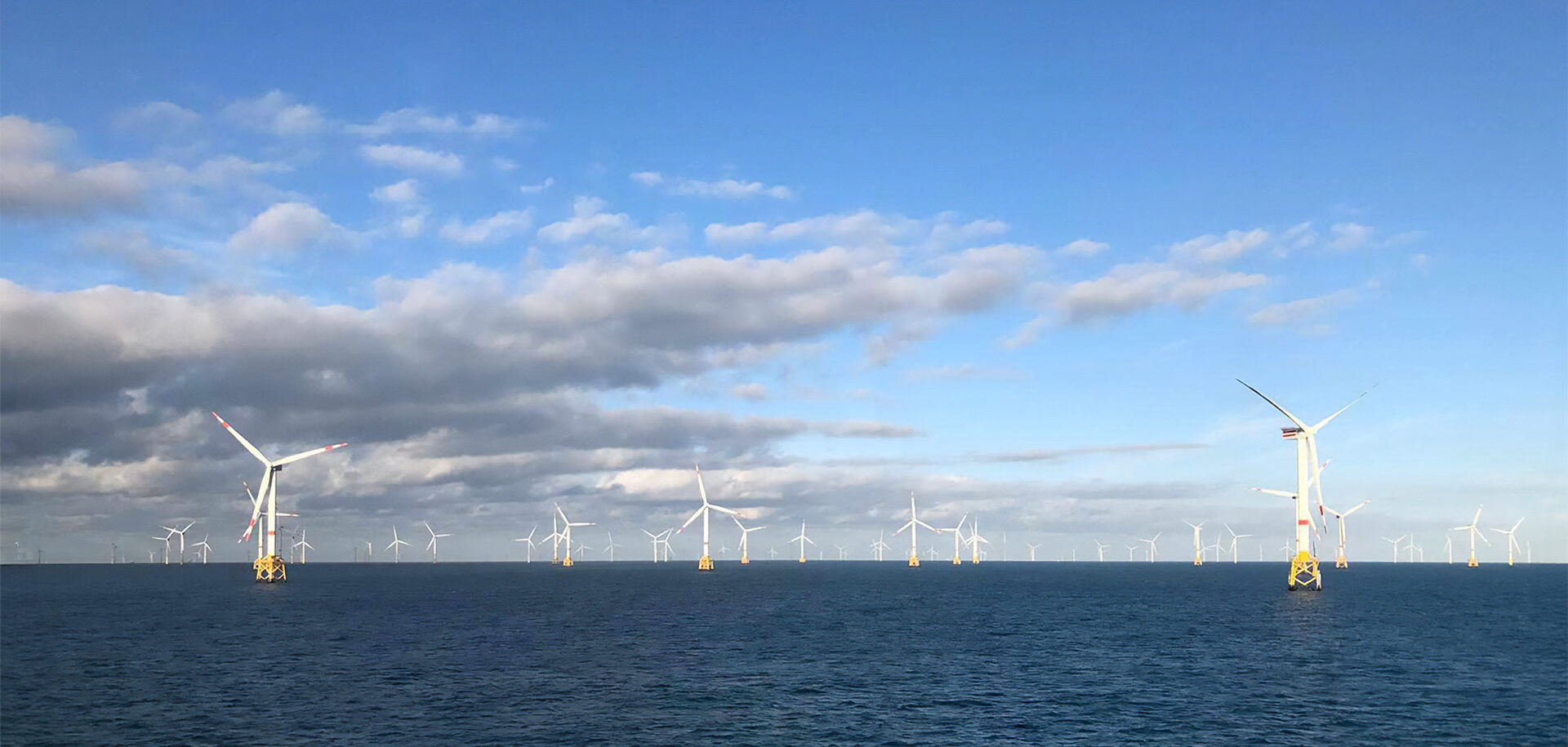
Maintien d’un parc éolien vieillissant grâce à la collaboration
Les solutions de maintenance et d’assistance innovantes de SKF contribuent à maintenir en service l’un des premiers parcs éoliens offshore d’Europe qui a déjà atteint la moitié de sa durée de vie.
Sur le banc de sable de Thornton, à 30 km des côtes belges, 54 éoliennes tournent dans l’air venteux de la mer du Nord. D’une capacité de 325 MW, le parc éolien C-Power est l’une des neuf installations d’énergie renouvelable offshore de la région. La capacité totale actuelle est de 2,2 GW auxquels on prévoit d’ajouter 3 GW supplémentaires.
En 2009, à la mise en service de la première série de six éoliennes, C-Power était le premier projet commercial d’énergie renouvelable offshore de Belgique. Il était constitué de deux réseaux séparés par un chenal pour le passage de l’électricité et d’un gazoduc. Même si les éoliennes de 5 et 6 MW sont deux fois moins imposantes que celles installées actuellement, elles n’en sont pas moins impressionnantes. Leurs trois pales de 61,5 m tournent sur un moyeu à 95-96 m au-dessus des vagues. Les éoliennes doivent leur hauteur à un mât en acier de 68 m ancré sur des fondations de 45 m. Si celles des premiers modèles étaient en béton et pesaient jusqu’à 3 000 tonnes, elles se composent désormais d’une tour-treillis d’acier tubulaire plus légère, reposant sur quatre pieux de 2 m de diamètre chacun, enfoncés dans le fond marin.
Au sommet de chaque mât, une nacelle de 320 tonnes accueille les roulements du rotor, le multiplicateur, le système de contrôle du tangage et le dispositif de conversion d’énergie. Selon C-Power, ses éoliennes et le transformateur offshore à l’écart du parc sont « 55 usines qui ont besoin de maintenance et d’entretien. »
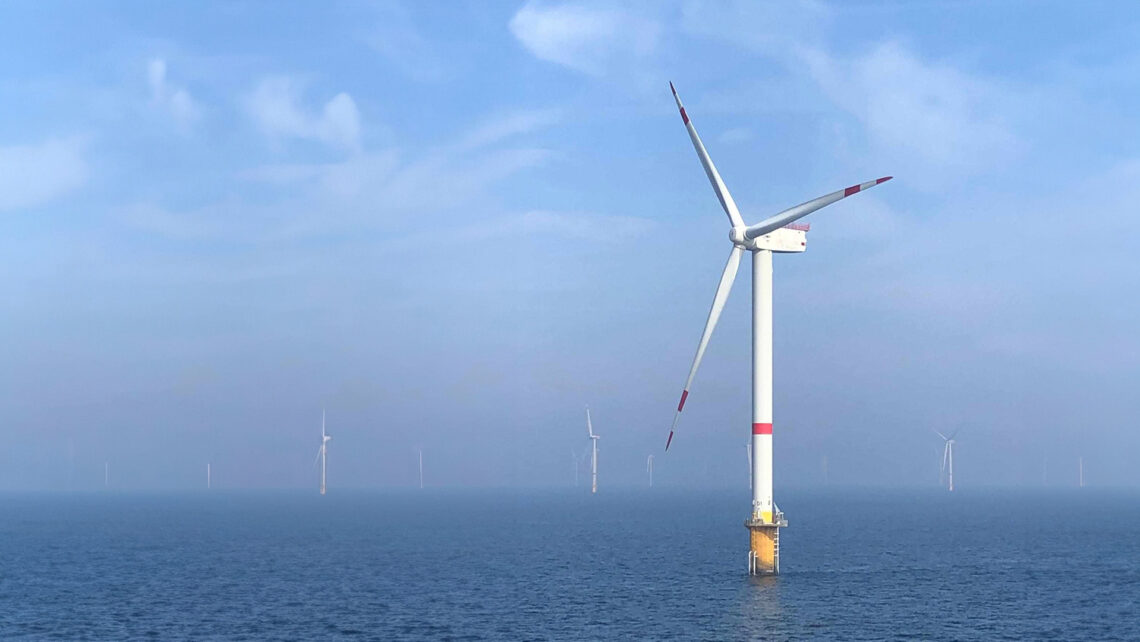
Pas de répit
Les éoliennes les plus anciennes affrontent depuis 14 ans les conditions rigoureuses de la mer du Nord. Elles ont atteint la moitié de leur durée de vie nominale qui est de 25 ans. Les plus récentes ont déjà fêté leur dixième anniversaire.
Comme toute personne confrontée aux défis de l’âge mûr, elles ont besoin d’un peu plus de soins et d’assistance pour rester en parfait état. Chose rare pour un parc éolien offshore, c’est C-Power qui s’occupe en interne de son exploitation et de sa maintenance.
Presque chaque jour, des équipes de maintenance quittent Ostende en bateau pour intervenir sur les éoliennes. Le régime de maintenance de ces dernières repose sur un programme complet de tâches de maintenance préventive annuelles et semestrielles. En moyenne, la maintenance préventive de chaque éolienne totalise 11 jours par an. Les équipes peuvent également être sollicitées pour solutionner des pannes et, si nécessaire, procéder à des réparations.
Les navires de servitude reviennent à quai chaque soir, mais C-Power veille attentivement sur les équipements depuis un centre de surveillance à distance opérationnel 24h/24, 7j/7 dans le port d’Ostende. Si les conditions météorologiques sont trop mauvaises pour se rendre sur place par voie maritime, chaque éolienne est équipée d’une plateforme d’hélitreuillage permettant son accès en cas de réparation urgente.
C-Power a beau gérer la maintenance en interne, elle ne le fait pas toute seule. L’entreprise a conclu un partenariat pluriannuel avec SKF. Les deux organisations collaborent étroitement pour améliorer la fiabilité des éoliennes et concevoir des solutions innovantes pour le secteur de l’énergie offshore. Les équipes des deux entreprises s’entretiennent chaque semaine de l’état d’avancement des projets en cours et de nouvelles possibilités de collaboration.
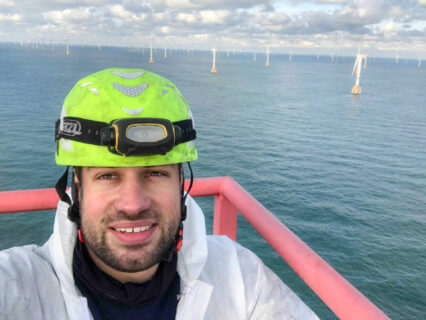
Nous utilisons la technologie de maintenance conditionnelle pour comprendre ce qui se passe dans nos éoliennes.
Bryan Uyttersprot, ingénieur d’exploitation et de maintenance chez C-Power
Commande à distance
Toutes les cinq semaines, Bryan Uyttersprot, ingénieur d’exploitation et de maintenance chez C-Power, est en charge de la salle de commande du parc éolien C-Power. Le reste du temps, il chapeaute un large éventail de projets de réparation et d’amélioration de la fiabilité. « Il m’arrive de partir en bateau et de travailler sur site avec nos équipes de maintenance, en particulier lorsqu’on teste quelque chose de nouveau. Mais je passe le plus clair de mon temps dans un bureau à développer des projets à plus long terme. »
Ces périodes passées au centre de commande sont un parfait exemple de la profondeur des liens étroits noués entre SKF et C-Power. « Nous utilisons la technologie de maintenance conditionnelle pour comprendre ce qui se passe dans nos éoliennes, poursuit Bryan Uyttersprot. Les roulements de leurs génératrices et leurs multiplicateurs sont équipés d’environ 14 capteurs de vibrations, et des capteurs supplémentaires sont installés dans les roulements d’arbre principal du rotor. »
Les données sont collectées à partir de ces capteurs à l’aide de dispositifs de surveillance des machines SKF Multilog IMX et transmises par une liaison sécurisée au Centre de services de diagnostic à distance (RDC) SKF à Hambourg, en Allemagne. Là–bas, les spécialistes SKF de la maintenance conditionnelle pour l’énergie éolienne analysent les spectres vibratoires à la recherche de signes avant-coureurs de problèmes dans les composants stratégiques. « Je travaille en étroite collaboration avec les ingénieurs du RDC, reprend Bryan Uyttersprot. Leur analyse peut nous indiquer s’il y a un problème : par exemple, une bague de roulement cassée ou des éléments roulants endommagés. »
Sur la base des rapports envoyés par SKF, l’ingénieur détermine les mesures à prendre pour remettre l’éolienne en service. « Si le problème provient d’un roulement du générateur ou du multiplicateur, le remplacer est assez simple – même si nous devons envoyer une équipe de spécialistes pour remplir cette mission. » La nacelle de chaque éolienne est munie d’une grue hydraulique, qui sert aux équipes pour déplacer les composants les plus lourds en toute sécurité.
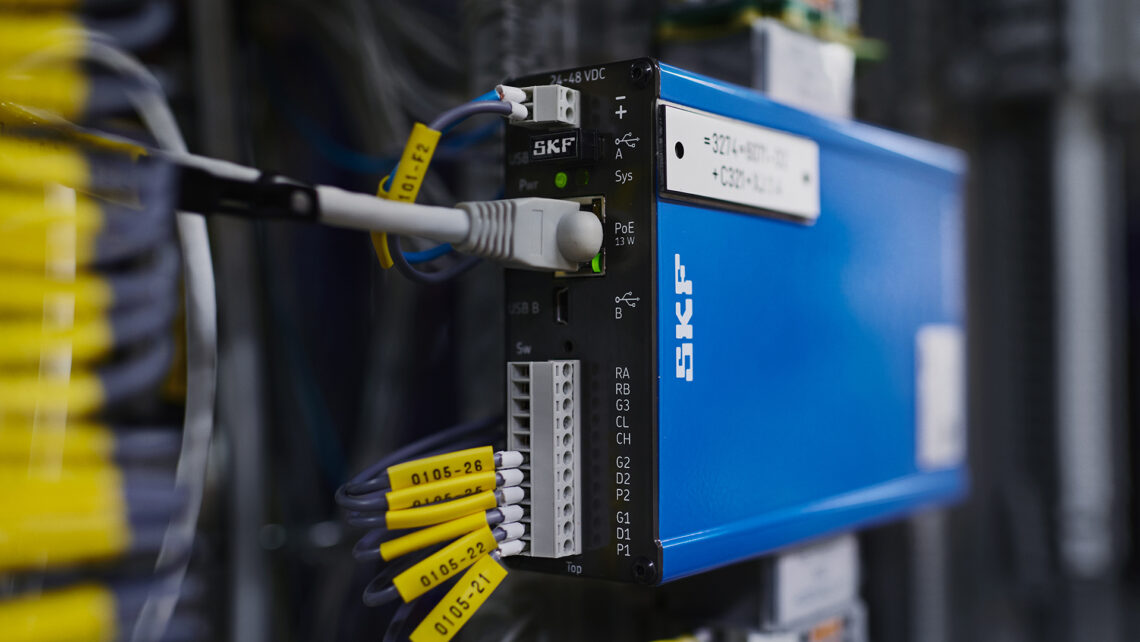
Interventions à grande échelle
Si le problème survient au niveau des roulements du rotor principal, les réparations sont beaucoup plus complexes. « Il nous faut alors retirer le montage d’arbre principal, qui pèse environ 70 tonnes. Pour accéder à ce montage, il faut démonter les rotors et le moyeu, dont le poids total est de 130 tonnes. » Ces travaux nécessitent des équipements de levage de charges lourdes hautement spécialisés. Ils sont effectués à l’aide d’une barge autoélévatrice équipée d’une grue lourde et de jambes qui peuvent être descendues vers le fond marin pour stabiliser le tout. Les montages d’arbres de rotor usés ou endommagés sont transférés vers une usine SKF pour y être réparés.
Le coût élevé et la complexité des réparations des roulements d’arbre principal font de leur fiabilité un sujet de préoccupation majeur pour tous les exploitants de parcs éoliens. C’est depuis longtemps une question prioritaire pour SKF et C-Power. « Nous avons procédé à de nombreuses modifications au fil des années. Nous avons changé la graisse de ces roulements pour améliorer les performances de lubrification et, avec le temps, nous avons sélectionné d’autres caractéristiques afin d’améliorer leur durée de service. »
SKF et C-Power sont d’ailleurs en plein milieu d’un programme d’essais pluriannuel portant sur une technologie innovante de maintenance conditionnelle. « Nous avons équipé certaines de nos éoliennes de roulements d’arbre principal dont les éléments roulants comportent des capteurs, indique Bryan Uyttersprot. Cela nous permet de mesurer les charges à l’intérieur des roulements et de voir comment celles-ci varient en fonction des conditions de fonctionnement et selon leur position autour de la circonférence. » La collecte de données sur les roulements équipés de capteurs est toujours en cours, mais Bryan Uyttersprot espère que les résultats des essais permettront d’améliorer encore la fiabilité de ces composants stratégiques.
En attendant, d’autres innovations SKF simplifient déjà la vie des équipes de maintenance de C-Power. Exemple : une nouvelle conception de joint fendu pour les roulements du rotor principal. Conçue à la base pour le pionnier belge de l’éolien, cette solution est non seulement plus robuste, mais elle permet également de réduire le temps de montage.
Une production de puissance
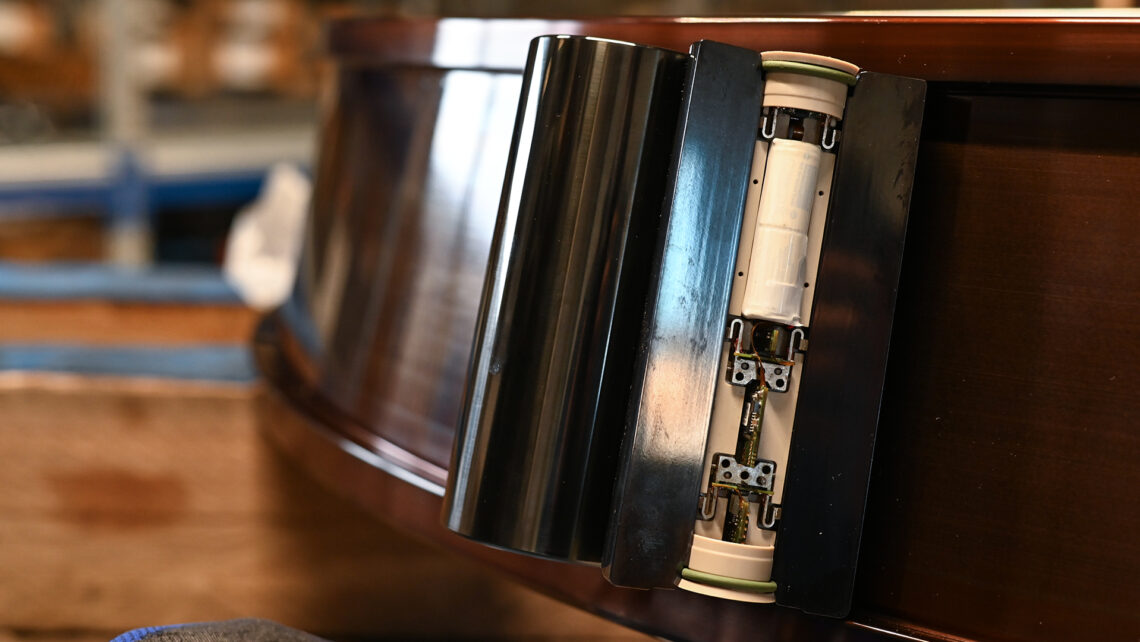