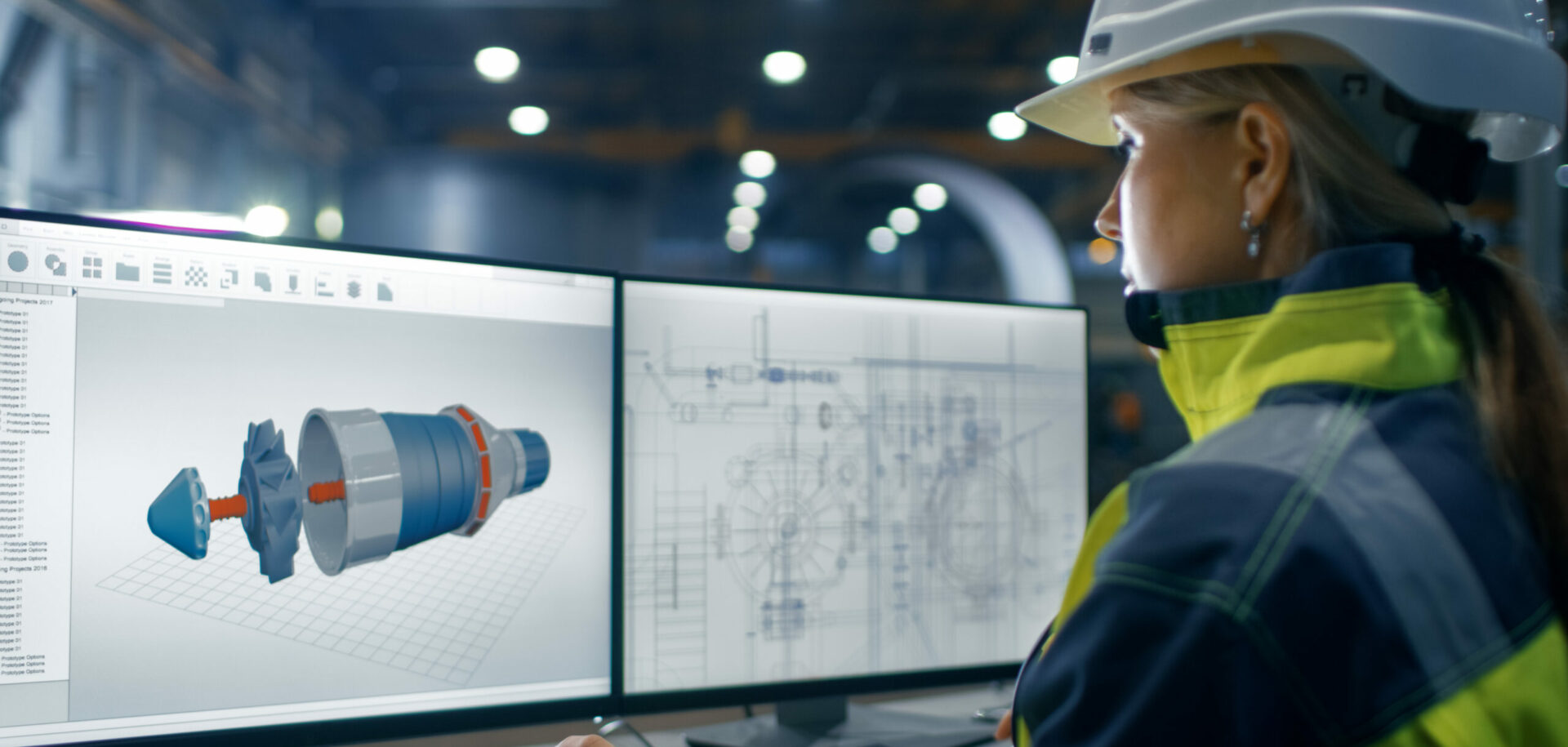
Comment réduire les coûts d’exploitation et de maintenance des éoliennes grâce aux roulements revêtus d’oxyde noir
Les producteurs d’énergie éolienne sont constamment à la recherche de moyens de réduire les coûts d’exploitation de leurs éoliennes. Les roulements revêtus d’oxyde noir constituent une des solutions. SKF propose un procédé d’oxydation noire amélioré pour des roulements utilisés aussi bien dans des installations neuves qu’existantes.
Résumé
Les éoliennes sont de plus en plus souvent installées dans des environnements hostiles et les constructeurs et exploitants doivent trouver des moyens de réduire les coûts d’exploitation et de maintenance tout en améliorant la fiabilité des machines. SKF apporte sa contribution à l’amélioration des performances des éoliennes grâce à un procédé exclusif de revêtement par une couche d’oxydation noire qui procure une protection supplémentaire aux roulements utilisés sur des systèmes clés dans ce secteur exigeant.
Liens apparentés
Les producteurs d’énergie éolienne sont constamment à la recherche de moyens de réduire les coûts d’exploitation de leurs éoliennes. Les roulements revêtus d’oxyde noir constituent une des solutions. SKF propose un procédé d’oxydation noire amélioré pour des roulements utilisés aussi bien dans des installations neuves qu’existantes.
Les coûts d’exploitation et de maintenance peuvent représenter une part importante, jusqu’à 25 %, du coût total de possession d’une éolienne sur l’ensemble de sa durée de service1. C’est ce qui incite SKF à promouvoir un traitement de surface basé sur un procédé de brunissage à chaud amélioré (revêtement par une couche d’oxydation noire) pour les roulements utilisés dans les applications d’éoliennes.
Des roulements revêtus d’une couche d’oxydation noire peuvent être installés en remplacement de roulements standard dans le cadre des routines de maintenance des parcs éoliens, ou spécifiés pour de nouvelles installations. Autrement dit, l’ensemble du secteur éolien peut bénéficier des avantages offerts par l’oxydation noire.
En tant que principal fournisseur de roulements pour l’industrie de l’énergie éolienne, SKF dispose d’une vaste expérience dans ce secteur, de la conception des roulements aux services complets couvrant la maintenance conditionnelle, les systèmes de lubrification, la gestion des équipements et l’approvisionnement en pièces détachées. SKF a identifié un certain nombre d’opportunités d’amélioration de la fiabilité opérationnelle par le biais de nouveaux produits et procédés, dont le traitement de brunissage à chaud (oxydation noire) mis au point spécialement pour les applications évoquées.
Des exigences croissantes relatives aux installations
Les éoliennes sont soumises à des températures, des vitesses et des charges extrêmement variables. À ces conditions défavorables s’ajoutent la contamination, l’humidité et les réactions chimiques engendrées par des huiles à forte teneur en additifs AW, autant d’éléments susceptibles de réduire considérablement le cycle de vie des roulements en l’absence de mesures préventives. L’augmentation des dimensions et de la capacité des éoliennes fait, en outre, peser des contraintes supplémentaires sur des systèmes clés comme le multiplicateur.
Le traitement de brunissage à chaud employé par SKF offre une protection renforcée des roulements, en particulier pour les conditions de service difficiles engendrées par un passage de l’exploitation sur terre à l’exploitation au large, ou encore pour les équipements implantés dans des environnements de plus en plus hostiles à travers le monde.
Bien que les taux de défaillances et d’endommagements des multiplicateurs d’éoliennes varient selon les sources, l’étude de marché Reliawind financée par l’UE a fourni comme référence le chiffre de 6 % par an. Ce rapport mentionne également des données sur le taux de défaillance et les arrêts-machines, qui font état de taux de défaillance tournant autour de 10 %. Ces chiffres peuvent certes sembler faibles en comparaison d’autres causes de pannes dans ce secteur, comme les systèmes électriques, mais ces défaillances sont susceptibles de lourdes conséquences. Des entraînements mécaniques endommagés ou défaillants peuvent engendrer des coûts élevés induits par des arrêts-machines prolongés.
Par exemple, une défaillance de roulement sur un arbre à grande vitesse d’éolienne terrestre peut entraîner des coûts de réparation de l’ordre de plusieurs milliers d’euros, sur la base d’une intervention de remplacement en haut de l’éolienne. En revanche, si la défaillance provient d’un roulement de roue planétaire, c’est l’ensemble du multiplicateur qui doit être remplacé et les coûts totaux peuvent alors facilement se chiffrer par centaines de milliers d’euros.
Les principaux mécanismes de défaillance
Les types de dommages contre lesquels aide à lutter le traitement à l’oxyde noir de certains éléments du roulement, comme les bagues et rouleaux, se classent généralement dans les catégories suivantes : fissures, glissement (grippage) et fatigue de surface, sans oublier les répercussions de facteurs environnementaux, comme l’humidité et les agressions chimiques.
1. Fissures
De nombreuses avaries prématurées de roulements de multiplicateurs résultent d’un mode de défaillance qui n’est pas causé par les mécanismes classiques de fatigue de contact roulant (FCR). Ces mécanismes classiques mêlant fatigue en sous-couche et fatigue de surface peuvent être prédits grâce à des méthodes normalisées de calcul de la durée des roulements, tandis que les défaillances prématurées occasionnées par la propagation de microfissures à partir de phase blanche – dite White Etching Crack (WEC) – qui touchent les roulements d’éoliennes ne sont pas couvertes (Fig. 1a). Le terme de « phase blanche » fait référence à l’aspect de la microstructure altérée de l’acier après polissage et attaque métallographique d’une section. Ces défaillances peuvent être observées en différentes positions de roulements : roulements des roues planétaires, de l’arbre intermédiaire et de l’arbre à grande vitesse.
Les défaillances prématurées dues aux fissures WEC sont l’objet de nombreux débats au sein de l’industrie éolienne et de recherches menées de façon indépendante par les fabricants d’éoliennes, les fabricants de multiplicateurs et les fabricants de roulements, sans oublier les universités et organismes tiers. Les hypothèses actuelles se concentrent sur les développements de fissures WEC amplifiés par la présence d’hydrogène ou sur les développements de fissures WEC liés principalement aux charges/contraintes, notamment dans les zones d’inclusions et en surface, ou à une combinaison de plusieurs causes.
2. Grippage (usure par adhérence)
Dans des roulements à rouleaux faiblement chargés, un glissement pur peut se produire entre les éléments roulants et la bague intérieure en cas d’écart important entre la vitesse de rotation de la bague intérieure et celle du jeu de rouleaux. Dans des applications exigeantes, comme les arbres à grande vitesse des multiplicateurs d’éoliennes, un fonctionnement au ralenti ou une modification des zones de charge peut parfois entraîner un risque élevé de glissement.
Dans les roulements à rouleaux soumis à des charges radiales, la zone la plus critique en termes de glissement correspond à l’entrée des rouleaux dans la zone de charge. En rotation, les rouleaux ralentissent dans la zone non chargée du roulement en raison du frottement et doivent donc brusquement accélérer lorsqu’ils pénètrent dans la zone de charge. De telles conditions favorisent le grippage (Fig. 1). La microstructure des rouleaux et des pistes est altérée et cette altération génère des contraintes locales conduisant à un écaillage et une défaillance du roulement.
Dans les roulements à rouleaux cylindriques jointifs, la formation d’un film lubrifiant séparant les rouleaux est parfois empêchée par la vitesse de la surface opposée. Un film mince, voire une lubrification mixte, sous des pressions de contact élevées conduit à un contact métallique entre des rouleaux adjacents qui a pour effet d’augmenter le frottement, entraînant un grippage et, au bout du compte, une destruction de la surface.
3. Fatigue de surface/micro-écaillage
De nombreuses pièces mécaniques qui présentent des contacts de roulement et glissement (roulements, engrenages et galets de came) sont sujettes à différents types de détériorations, parmi lesquels l’usure par abrasion légère et le micro-écaillage. La fatigue de surface, ou micro-écaillage, est due à une épaisseur du film d’huile insuffisante pour séparer des éléments en contact mobile ; cette forme de détérioration localisée de la surface apparaît à la fois sur les dentures d’engrenages et dans les roulements et constitue un phénomène couramment observé au niveau des multiplicateurs d’éoliennes. Les dentures d’engrenages y sont généralement plus sujettes que les roulements. Néanmoins, si les roulements sont touchés, les répercussions peuvent être particulièrement dommageables. La géométrie des rouleaux et des pistes est altérée et cette altération augmente le jeu interne et génère des contraintes locales qui conduisent à un écaillage et une défaillance du roulement (Fig. 1c). La contamination par l’eau dans les multiplicateurs d’éoliennes peut également contribuer au phénomène.
4. Corrosion humide
La teneur en eau des huiles de lubrification des multiplicateurs d’éoliennes est souvent sous-estimée. Les écarts de température importants combinés à une teneur en eau élevée (selon le type d’huile) peuvent entraîner un risque d’« eau libre » et de corrosion « à l’arrêt » (Fig. 1d). Tandis que les risques importants engendrés par l’eau libre pour l’application sont bien connus, le risque lié à des quantités diverses d’eau dissoute dans l’huile des multiplicateurs reste flou. Les recherches menées par SKF révèlent un impact négatif de la présence d’une certaine quantité d’eau dissoute sur les performances du roulement.
5. Corrosion de contact
Lorsque l’interface du roulement avec l’arbre (alésage de la bague intérieure/portée de l’arbre) ou l’interface du roulement avec le logement (surface extérieure de la bague extérieure/portée du logement) est soumise à des micro-mouvements sous des charges variables, l’oxyde natif des surfaces en acier peut se détériorer. En outre, des aspérités de surface peuvent se corroder et s’effriter. Les particules viennent alors se loger dans le contact et si des agents oxydants, comme l’humidité, sont également présents, une corrosion de contact supplémentaire se produit à la surface (Fig. 1e). Sous charge, l’air et l’humidité piégés dans le contact corrodent davantage la surface, ce qui peut parfois se traduire par l’apparition de nouvelles particules. Celles-ci forment une sorte de pâte abrasive qui donne lieu à des pertes de serrage supplémentaires, à une augmentation du roulage des bagues ou, dans le pire des cas (si les particules corrosives restent coincées dans le logement), à la fissuration de la bague en raison de l’intensification des contraintes locales.
Le procédé de brunissage à chaud (oxydation noire) employé par SKF
L’application d’un revêtement composé d’oxydes noirs spécialement mis au point sur les surfaces fonctionnelles du roulement apporte un degré de protection significatif contre tous ces modes de défaillance potentiels. Cette couche confère des propriétés avantageuses pour le fonctionnement du roulement comme l’amélioration de la phase de rodage, par exemple, et se traduit par des propriétés de surface après rodage également améliorées, de meilleures performances dans des conditions de lubrification médiocres (insuffisance κ), une meilleure adhérence du lubrifiant ainsi qu’une résistance au grippage supérieure. Le risque de corrosion de contact, de micro-écaillage et de fissures peut être réduit. En outre, la couche d’oxydes noirs procure une résistance à la corrosion rudimentaire ainsi qu’une résistance chimique supérieure par rapport à des surfaces non traitées. La résistance à la corrosion modérée de la couche d’oxyde noir suffit pour éviter la corrosion « à l’arrêt » et la corrosion de contact, et la résistance chimique réduit les effets néfastes de certaines substances agressives contenues dans les huiles. Elle améliore le comportement au frottement et réduit l’usure, en particulier dans des conditions de lubrification mixte. Des résultats récents de R&D indiquent que la couche d’oxyde noir agit comme une barrière à la perméation de l’hydrogène dans l’acier.
Pour illustrer l’amélioration potentielle des taux de défaillance, évoquons le cas d’un fabricant de multiplicateurs d’éoliennes qui avait relevé sur un échantillon de 1 000 roulements à rouleaux cylindriques des taux de défaillance allant de 40 à 70 % (après deux ans). Par la suite, sur un échantillon de 1 150 roulements à rouleaux cylindriques brunis à chaud utilisés dans une application similaire, le taux de défaillance a été de 0,1 % sur la même période2.
En résumé, par rapport à des roulements non traités, les roulements revêtus d’oxyde noir SKF dans les applications de multiplicateurs d’éoliennes (Fig. 4) peuvent offrir les avantages suivants :
- amélioration du comportement au rodage ;
- amélioration de la résistance à la corrosion ;
- amélioration de la résistance au grippage ;
- amélioration des performances dans des conditions de lubrification médiocre ;
- amélioration de l’adhérence de l’huile ou la graisse ;
- réduction de l’attaque chimique de l’acier des roulements par des additifs de l’huile agressifs ;
- réduction de la perméation de l’hydrogène dans l’acier des roulements ;
- réduction du risque de corrosion de contact au niveau des ajustements.
Avec plus de 50 000 roulements revêtus d’oxyde noir en service, SKF a accumulé de nombreuses preuves indiquant que ce procédé économique offre au secteur de l’énergie éolienne des améliorations des performances appréciables qui peuvent se traduire par une diminution des défaillances précoces et contribuer ainsi à réduire les coûts totaux d’exploitation et de maintenance.
Le brunissage à chaud
Le procédé de brunissage à chaud (ou revêtement d’oxydation noire) est un traitement de surface basé sur une réaction chimique qui s’opère au niveau de la couche d’acier superficielle des roulements. Le procédé consiste à immerger des pièces dans une solution aqueuse de sels alcalins à une température d’environ 150 °C. La réaction entre le fer de l’alliage ferreux et les agents chimiques produit sur la surface extérieure des éléments de roulement une couche d’oxyde composée d’un mélange défini de FeO, Fe2O3, produisant du Fe3O4. On obtient ainsi un revêtement noir foncé d’environ 1-2 μm d’épaisseur.
Les avantages du traitement de brunissage à chaud doivent être évalués au regard de l’application en question, mais aucun effet indésirable n’a jusqu’ici été démontré concernant ce traitement. Il est appliqué avec succès à des roulements utilisés dans d’autres industries confrontées à des défis opérationnels particuliers (roulements de rouleaux de machines à papier, de machines-outils et de ventilateurs industriels).
Le procédé d’oxydation noire intègre une grande variété de paramètres. Le procédé consiste au total en une quinzaine d’étapes d’immersion différentes. Pour bon nombre de ces étapes, il est possible de paramétrer les substances chimiques, la concentration, la température, la durée de l’immersion et le comportement du fluide à l’intérieur du réservoir.
SKF consacre à ce procédé de nombreuses recherches depuis 2006 afin de définir les spécifications optimales pour un traitement de brunissage à chaud et d’étendre celui-ci aux roulements de grandes dimensions. Développés sur mesure pour chaque type de roulement et application afin d’en optimiser les performances, les procédés d’oxydation noire SKF couvrent une gamme étendue de tailles de roulements pour éoliennes, jusqu’à 2,2 m de diamètre extérieur actuellement et un poids maximal pour les composants de roulements de 1 000 kg. La méthode de traitement et la plage de dimensions et poids couverts sont exclusives à SKF.
SKF recommande que les deux bagues, intérieure et extérieure, ainsi que les éléments roulants soient revêtus pour des performances optimales. L’oxydation noire peut être appliquée à tous les types de roulements utilisés dans les systèmes clés des éoliennes. Des roulements à rouleaux cylindriques et coniques notamment ont été traités avec succès selon ce procédé et mis en service ces dernières années (Fig. 2 et 3).
Le procédé de traitement de brunissage à chaud utilisé par SKF repose sur des spécifications rigoureuses et fait l’objet d’un suivi précis. Il en résulte des roulements de haute qualité accessibles par le biais du réseau mondial de l’entreprise qui permet ainsi aux fabricants, comme aux exploitants et aux prestataires de services de l’industrie éolienne de bénéficier partout dans le monde des avantages des roulements revêtus avec une couche d’oxydation noire.
Fig. 1 : types d’avaries de roulements pouvant survenir dans les multiplicateurs d’éoliennes.
a) fissures/écaillage.
b) glissement/grippage.
c) fatigue de surface/micro-écaillage.
d) humidité/corrosion « à l’arrêt » sur une piste.
e) corrosion de contact sur l’alésage d’une bague intérieure.
Notes
1. Pour une éolienne neuve, les coûts d’exploitation et de maintenance peuvent facilement représenter jusqu’à 20-25 % du coût global actualisé du kWh produit sur la durée de service de l’éolienne. Si l’éolienne est neuve, cette part peut être limitée à 10-15 %, mais elle augmente jusqu’à atteindre au minimum 20 à 35 % en fin de vie de l’éolienne. Chiffres issus de Wind Energy – The Facts (WindFacts), un projet européen financé par le programme Énergie intelligente pour l’Europe de l’Agence exécutive pour la compétitivité et l’innovation.
2. J.Luyckx : Hammering Wear Impact Fatigue Hypothesis WEC/irWEA failure mode on roller bearings, atelier NREL, Broomfield, Colorado, USA (novembre 2011).