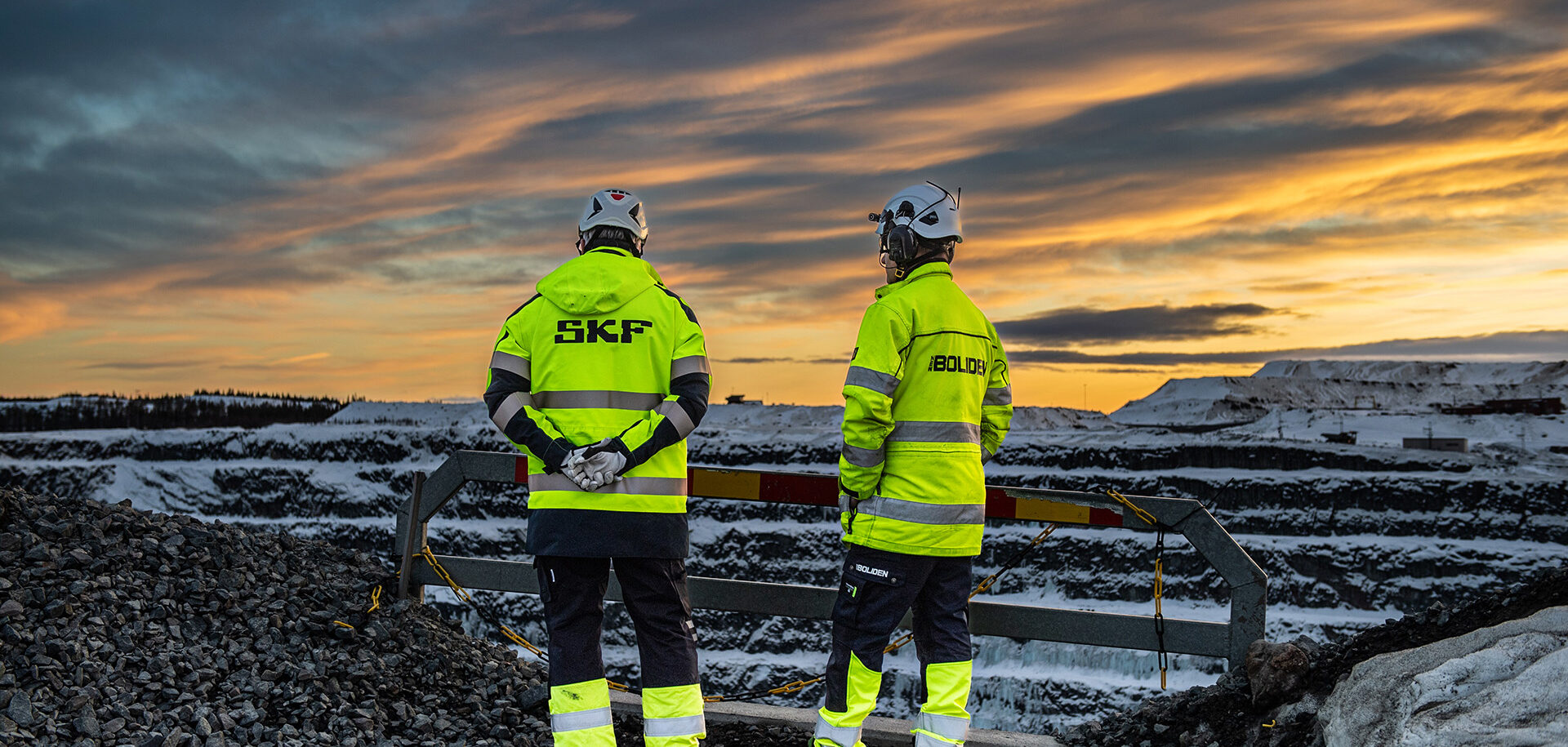
Des convoyeurs plus fiables grâce à une nouvelle coopération
L’interminable ligne de convoyage de la mine de cuivre Aitik de Boliden rencontrait des problèmes et perturbait l’activité. Un nouveau système de surveillance des vibrations et un partenariat avec SKF y ont remédié.
La mine de cuivre Aitik de Boliden, dans le nord de la Suède, maîtrise désormais sa maintenance préventive grâce à un nouveau système de surveillance des vibrations et à un partenariat avec SKF.
« Chaque semaine, l’activité était perturbée de manière imprévisible. Maintenant, il n’y a guère plus que des arrêts planifiés », explique Stefan Johansson, chef de la maintenance préventive du service Concassage & Convoyage de la mine Boliden Aitik, située non loin de la ville de Gällivare.
Aujourd’hui, nous n’avons guère plus que des arrêts planifiés
Stefan Johansson, chef de la maintenance préventive du service Concassage & Convoyage de Boliden Aitik
Le transport est un rouage essentiel du site minier. Afin d’extraire un minerai d’une teneur d’environ 0,2 % en cuivre, d’énormes quantités de roche doivent être abattues et transportées, d’abord par tombereau vers les concasseurs de la mine à ciel ouvert, puis par convoyeur jusqu’au concentrateur. Depuis l’ouverture du site en 2010, la ligne de convoyage longue de 7 km est l’un des maillons faibles de la chaîne.
« Nous rencontrions énormément de difficultés, l’activité était perturbée chaque semaine, indique Jonas Fjellner, ancien chef de section du service Concassage & Convoyage chez Boliden Aitik. Nous savions que le problème provenait des roulements situés dans les poulies motrices et les tambours d’entraînement. » Le système de surveillance des vibrations installé présentait certains défauts et la mine ne disposait pas des compétences nécessaires pour analyser les valeurs mesurées.
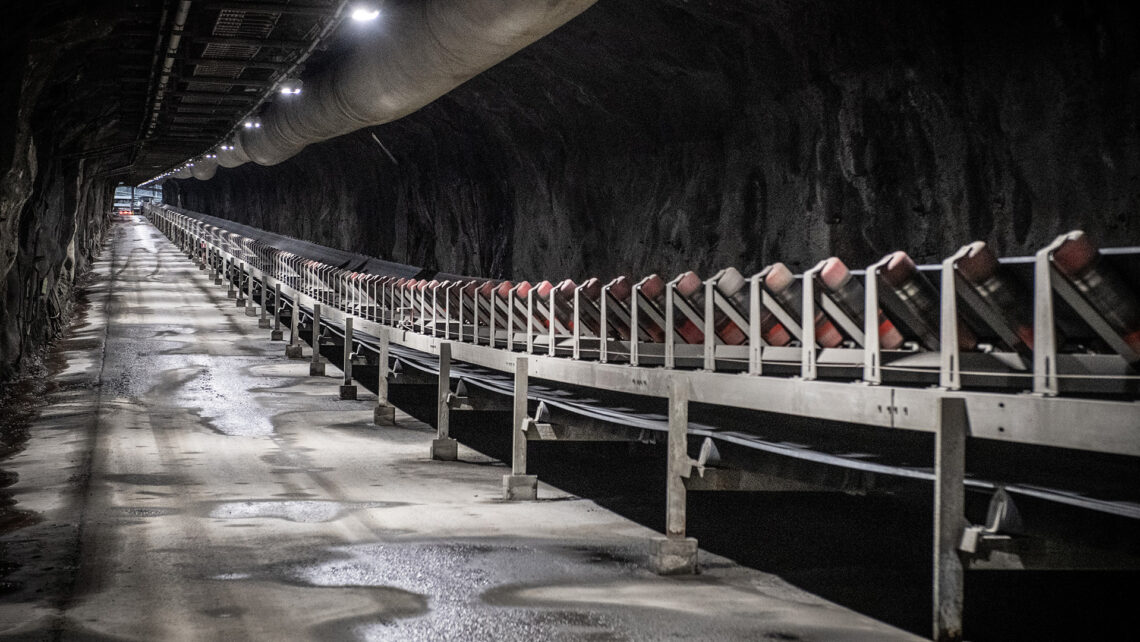
Une solution intégrale
On envisage alors de repartir de zéro avec un système entièrement nouveau. On recherche une solution intégrale et un partenaire local avec lequel Boliden peut collaborer tout au long du processus, de l’installation, des mesures et analyses jusqu’à la résolution des problèmes en passant par l’amélioration continue.
En 2018, on décide de changer le système de surveillance des vibrations et la méthode de travail. L’année suivante, un accord de partenariat est conclu avec SKF. Première étape : remplacer l’ancien matériel par le système SKF de surveillance des vibrations. Décision est également prise de n’installer que des roulements et des paliers SKF. À la mi-2020, le nouveau système est opérationnel sur l’ensemble du site et les résultats sont déjà perceptibles. « La disponibilité s’est nettement accrue, affirme Stefan Johansson. Depuis 2019, nous n’avons pas subi d’arrêts non planifiés dus à la défaillance de roulements, et aujourd’hui, toute notre maintenance est planifiée. »
Réunions conjointes
Selon lui, l’un des principaux facteurs de réussite est la mise en place d’une nouvelle organisation collaborant étroitement avec SKF : « Si, par exemple, nous remplaçons un roulement, SKF nous aide en réalisant une analyse des causes pour comprendre ce qui s’est passé. Lors des réunions du groupe de projet, nous discutons de la nécessité de changer des roulements et des joints ou de tester une solution différente. »
SKF a également organisé quelques sessions de formation avec le personnel de Boliden. D’autres sont en préparation.
Désormais, SKF gère l’analyse des données de mesure provenant de la surveillance des vibrations, souvent en contact direct avec le personnel du service Concassage & Convoyage. « Si une alerte se déclenche pendant les mesures, SKF peut nous appeler pour qu’on en vérifie l’origine, même si c’est un vendredi soir ou un samedi. »
Moins d’émissions grâce à la réparation
La nouvelle méthode de travail a entraîné de nombreux changements importants qui ont permis d’accroître, d’une part la disponibilité, et, d’autre part le recyclage des matériaux grâce à la réparation des roulements et des paliers.
« Les mesures nous livrent beaucoup d’informations et si on constate que l’heure est venue de remplacer un roulement, nous faisons appel à SKF. À l’occasion de ce remplacement, SKF vérifie l’ancien roulement sur place et procède à une première évaluation pour déterminer s’il peut être réparé. »
En 2022, 22 roulements et paliers ont été réparés. Fin mars 2023, 10 autres avaient été expédiés vers le centre de remise en état. En plus de réaliser des économies d’environ six millions de couronnes suédoises, la réparation a permis de réduire considérablement les émissions de CO2 comparativement à la fabrication de nouveaux produits.
En 2022, Boliden et SKF ont signé un nouvel accord de partenariat de trois ans. « Nous approfondissons notre coopération et nous poursuivons sur la voie que nous avons tracée, se félicite Stefan Johansson. J’aimerais vraiment que nous procédions de la même manière sur un plus grand nombre de sites de Boliden. C’est une démarche formidable. Nous travaillons sous la même bannière, nous œuvrons pour atteindre des objectifs communs et il règne un grand sentiment d’unité dans le groupe. »