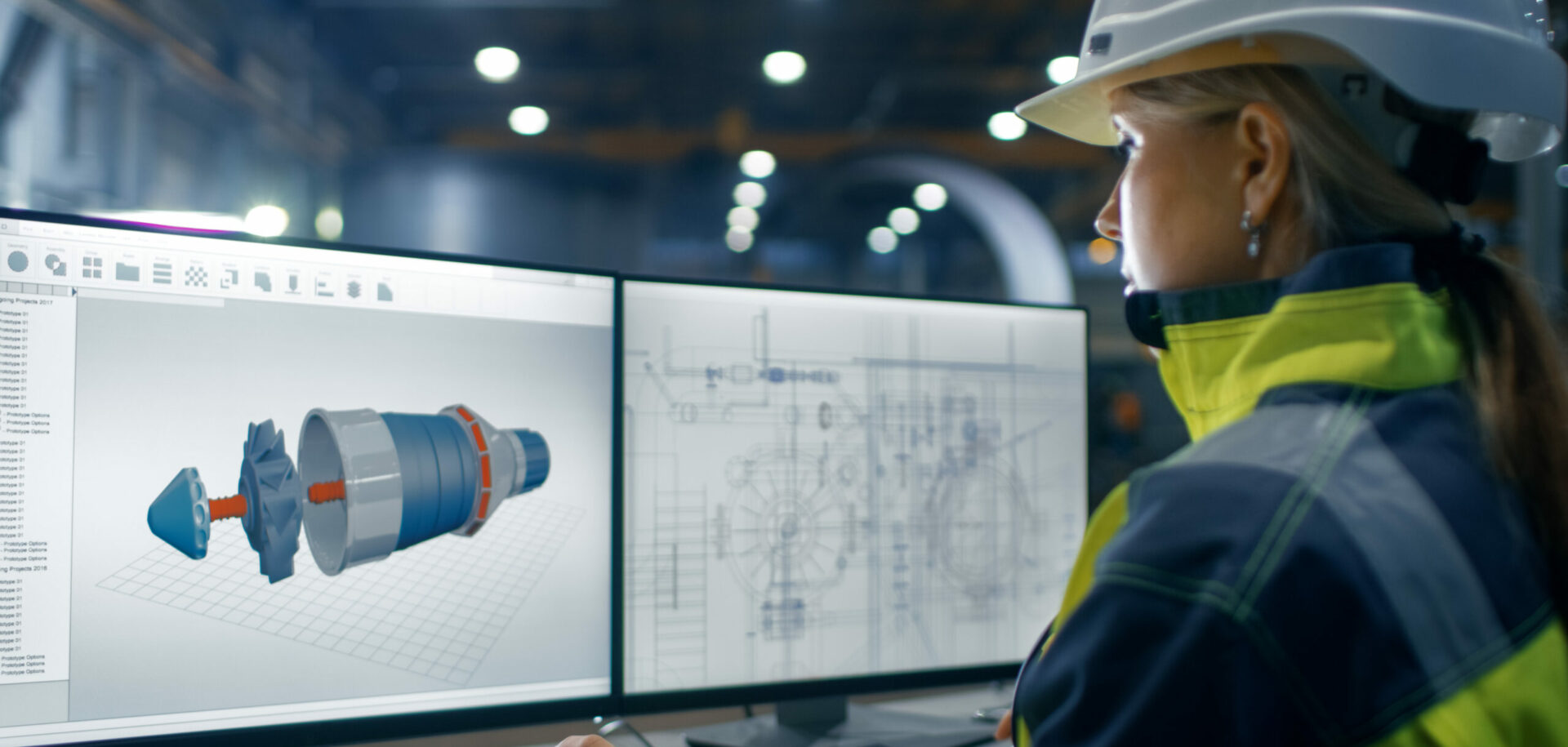
L’aide apportée par la modélisation et la simulation dans la construction de la plus grande roue panoramique du monde
Lorsqu’il s’agit de construire la plus grande roue panoramique du monde, à savoir la High Roller de Las Vegas, mieux vaut être certain de recourir aux meilleurs processus et pièces techniques qui soient. Ainsi, lorsqu’il a fait équipe avec Arup, le concepteur de la roue panoramique, et American Bridge, le maître d’œuvre, pour concevoir les principaux assemblages d’arbres et moyeux, SKF a appliqué les outils d’analyse et de conception les plus récents pour assurer le bon fonctionnement de la roue, de jour comme de nuit.
Résumé
Pour construire et installer le plus gros système de roulements de tous les temps destiné à la plus grande roue panoramique du monde, SKF a rassemblé toute son expertise en matière de conception et d’analyse afin de garantir la conformité du roulement aux exigences opérationnelles extrêmement strictes. Une analyse approfondie de tous les aspects de la conception réalisée avec des outils de modélisation et simulation sophistiqués a permis de définir le système de roulements le plus adapté à la tâche.
Liens apparentés
Contact commercial
Randy A. Greaser, Randy.A.Greaser@skf.com
D’une hauteur de 168 m, la High Roller de Las Vegas est la roue panoramique la plus grande au monde. Chacune de ses 28 nacelles climatisées peut transporter jusqu’à 40 personnes pour un tour de 30 minutes à la découverte de cette ville en effervescence permanente. Elle fait partie d’une zone de commerces, restauration et loisirs en plein air, le Linq, un investissement de 550 millions de dollars qui a transformé le paysage et offre aux visiteurs une nouvelle perspective sur le Strip. La High Roller, dont la conception avait été annoncée en août 2011, est entrée en service en mars 2014.
Derrière l’aspect clinquant de cette nouvelle attraction dans le panorama de Las Vegas se cache une véritable prouesse d’ingénierie, à savoir la construction d’une structure géante répondant à des exigences de sécurité strictes et des conditions de service contraignantes. SKF a été chargé de concevoir, fournir et assembler le système de roulements de l’axe par le maître d’œuvre principal de la structure, American Bridge, qui a installé le système. Dans le cadre de ce projet, SKF a également été amené à travailler en coopération étroite avec les ingénieurs structurels d’Arup qui ont établi les spécifications. Arup avait également participé à la construction de la précédente plus grande roue panoramique du monde, la Singapore Flyer.
La rotation de la High Roller est supportée par une paire de roulements à rotule sur rouleaux SKF sur mesure d’environ 8,8 tonnes chacun. Chaque roulement présente un diamètre extérieur de 2 300 mm, un alésage de 1 600 mm et une largeur de 630 mm. Les roulements intègrent deux rangées de 30 rouleaux chacune. Il s’agit des roulements les plus gros jamais construits par SKF dans son usine de Göteborg. Un modèle de simulation a été utilisé pour déterminer le jeu radial optimal pour cette application. Les caractéristiques techniques spéciales incluent des trous de lubrification W26 dans la bague intérieure, le revêtement SKF NoWear pour les rouleaux et un revêtement de l’alésage en PTFE. En outre, le système intègre des solutions d’étanchéité et de lubrification automatique de pointe.
La structure repose sur une roue de tension de 143 m de diamètre. Outre les deux ensembles-roulements SKF, la structure comporte quatre jambes de force en acier, une seule jambe haubanée, un axe fixe, un moyeu tournant, une jante en tube de 2 m de diamètre et 112 ensembles de câbles clos en guise de rayons. Les cabines sont montées à l’extérieur de la jante et tournent individuellement, entraînées par des moteurs électriques, de manière à maintenir leur plancher parfaitement horizontal pendant toute la rotation.
Critères de conception
Lors de l’étude du système de roulement de l’axe (Fig. 1), un certain nombre de difficultés se sont posées, en particulier la nécessité de fournir une solution sûre et fiable. Concernant l’ensemble axe et roulement, il était nécessaire de tenir compte des charges élevées et des déformations importantes du logement induisant des fluctuations d’alignement pour l’axe. D’après les forces spécifiées concernant la roue panoramique, les charges sont de 1 350 tonnes à chaque extrémité. Pour chacun des 56 câbles radiaux inférieurs, la tension est de 132 tonnes et pour les 56 câbles supérieurs, elle est de 47 tonnes. La tension totale des câbles radiaux s’élève à 4 600 tonnes.
Pour les travaux de conception, une vitesse théorique de rotation autour de l’axe Z de 0,033 tr/min a été prise en compte. Le modèle reposait sur une charge du vent constante exercée sur chaque roulement. Cette charge est appliquée sur la bague extérieure de chaque roulement dans la direction Z. Différentes charges du vent ont été utilisées dans les différentes simulations de cas de service. Le défaut d’alignement des roulements déterminé par calcul inclut les effets de charges du vent constantes associées à différentes conditions de service, par conséquent les simulations ne tiennent pas compte des charges du vent fluctuantes.
Le chargement des roulements lors de l’installation était un autre facteur clé à prendre en compte. Une défaillance de roulement peut s’avérer extrêmement coûteuse et paralysante. C’est ce qui a incité SKF à appliquer une approche Six Sigma pour ce projet, dès la conception jusqu’à la fabrication et l’assemblage. Comme il s’agit d’une pièce clé dans cette attraction si prestigieuse, il était important que le critère de conception relatif à une longue durée de service du roulement soit respecté. À cet effet, SKF a utilisé des outils d’analyse sophistiqués et coûteux, basés sur des principes d’ingénierie de pointe, afin de garantir une conception de l’ensemble roulement et axe conforme au cahier des charges strict et aux exigences de performance.
Approche du projet
La partie conception et analyse du projet a été divisée en quatre phases au cours desquelles des logiciels de modélisation et d’analyse ont été largement utilisés pour garantir une adéquation de la conception finale avec les conditions de service réelles. L’objectif consistait à évaluer les interactions complexes de tous les composants au sein du système et à identifier les indicateurs clés de performance. En substance, le projet avait pour objet d’étudier les interactions du système, incluant l’effet des déformations du logement, la distribution des charges exercées sur les contacts, et les pressions de contact sur les pistes de roulement. Une attention particulière a été accordée à l’évaluation des effets des charges et déformations sur les performances du roulement en termes de forces et de mouvement.
SKF dispose d’outils de simulation de pointe spécialement conçus pour l’étude des applications de roulements et pour évaluer les nombreux facteurs qui influent sur le comportement du système, comme le jeu lors de l’assemblage, les défauts d’alignement, la flexibilité de la structure portante, dans différentes conditions limites.
Les phases du projet ont été menées comme suit :
Phase 1 : définition du projet à l’aide de Design for Six Sigma.
- Définition du projet.
- Documents de base DfSS.
- Collecte des données de conception.
Phase 2 : analyse de simulation des roulements.
- Modèle de roulement rigide avec charges ponctuelles.
- Flexions et déformations comme données d’entrée.
- Modèle flexible incluant les éléments moyeu et axe.
- Charges prises en compte sous forme de tension des câbles (4 cas de simulation).
Phase 3 : analyse de sensibilité des roulements.
- Effets des modifications des conditions limites.
- Revue de la conception interne des roulements.
- Étude paramétrique de la géométrie interne des roulements.
- Analyse EF de la cage.
Phase 4 : analyse EF des forces d’enfoncement sur le manchon lors de l’installation.
- Création du modèle EF.
- Analyse EF des forces d’enfoncement sans les charges des câbles.
- Analyse EF des forces d’enfoncement avec les charges des câbles.
La phase 1 a consisté à établir une définition claire du projet et identifier toutes les informations et tous les documents requis pour la mise en œuvre d’une approche Design for Six Sigma (DfSS). Une partie de la méthodologie DfSS repose sur le recours à l’Analyse des modes de défaillance et de leurs effets (AMDE) pour conduire le développement des activités d’ingénierie et des solutions. L’AMDE a permis à l’équipe de conception d’identifier les causes de défaillance potentielles à partir de précédentes expériences similaires et a servi de référence pour la sélection des caractéristiques de conception, activités de simulation et recommandations. L’AMDE a été élaborée par une équipe constituée de représentants de Arup, American Bridge et SKF.
Concernant l’aspect pratique, le point de départ pour la création des documents de base DfSS a consisté notamment à identifier les paramètres influant sur la durée en fatigue du roulement (Fig. 2) dans le but de produire un diagramme de limite qui définisse les interactions du système de roulement avec son environnement, y compris les données d’entrée et le résultat souhaité. Un autre diagramme, appelé diagramme P, est utilisé pour identifier l’ensemble des paramètres de conception qui déterminent le résultat souhaité, autrement dit les performances, ainsi que les facteurs de bruit qui ont un impact négatif sur ces dernières.
SKF est ensuite passé à la génération du concept et à la sélection lors de la Phase 2. Avec une configuration de roulement à l’esprit, une analyse des performances du roulement a été réalisée à l’aide des modèles de simulation mentionnés ci-dessus. Pour ce faire, la suite logicielle SKF Simulator (Orpheus), développée sous forme de système complet intégré pour les recherches sur les applications de roulements, a été utilisée. Orpheus est capable d’analyser le comportement statique et modal de l’application de roulement. Pour commencer, un modèle est construit en reliant tous les types de pièces mécaniques, comme les roulements, arbres, engrenages et paliers. Une combinaison arbitraire de forces, déplacements prescrits et vitesses de rotation peut être utilisée pour définir les charges s’exerçant sur les composants. Les composants eux-mêmes peuvent être des éléments spéciaux (non linéaires) définis dans SKF Simulator (les roulements par ex.), ainsi que des éléments arbitraires comme des arbres et des paliers. Ces derniers doivent présenter un comportement linéaire. Leur rigidité et leurs propriétés d’amortissement peuvent être déterminées grâce à la méthode par éléments finis. Des méthodes de réduction spéciales sont appliquées (aux modèles originaux par éléments finis) pour réduire le nombre de degrés de liberté et minimiser ainsi le temps de calcul dans les analyses. Pour ce projet, quatre conditions de charge ont été retenues pour l’analyse.
Pour les simulations de modèle (statique) rigide, le roulement est modélisé sous forme d’un roulement à rotule sur rouleaux dont la bague extérieure est soumise à quatre combinaisons de charge radiale et axiale différentes. En ce qui concerne la bague intérieure, tous les degrés de liberté sont bloqués, tandis que la bague extérieure peut au contraire se déplacer selon tous les degrés de liberté. Une valeur de défaut d’alignement a été appliquée pour tenir compte du défaut d’alignement relatif entre la bague intérieure et la bague extérieure dans les deux sens (positif et négatif) (Fig. 3).
Suite à cette analyse, la modélisation s’est ensuite intéressée à l’impact de la flexibilité structurelle sur les performances du roulement. Pour ce faire, le moyeu et l’axe ont été ajoutés au modèle sous forme d’éléments parfaitement flexibles avant de procéder à de nouvelles simulations basées sur les quatre options de conditions.
L’un des aspects essentiels du projet de conception a consisté à s’assurer que l’ensemble-roulement soit capable de supporter les conditions réelles attendues. Lors de la Phase 3, la sensibilité du roulement aux fluctuations des conditions limites et la géométrie interne ont été étudiées. Ces analyses servent à évaluer la conception du roulement dans les conditions de l’application. SKF a mené d’autres analyses pour étudier cet aspect. L’une d’elles a porté sur l’évaluation de la sensibilité du roulement aux fluctuations des conditions limites et de la géométrie interne. Une analyse par EF de la cage a également été réalisée. L’analyse de la géométrie interne du roulement a conduit à une révision du profil initial des rouleaux.
Les premiers cycles d’optimisation ont permis d’identifier la possibilité d’améliorer la durée de vie en modifiant le profil des rouleaux et la rigidité de l’ensemble arbre/moyeu. La conception optimale a été retenue et d’autres simulations avec les différentes conditions de charge ont ensuite été évaluées.
Analyse de la durée de service des roulements
Comme mentionné précédemment, les roulements destinés à la High Roller doivent offrir une fiabilité élevée et une longue durée de service. C’est pourquoi SKF a employé deux méthodes clés de calcul de la durée de vie des roulements. La première est la méthode DIN ISO 281. La deuxième est la méthode SKF de calcul avancé de la durée de vie en fatigue (AFC) [voir page suivante].
Les valeurs de référence de cette méthode de calcul de la durée de vie en fatigue sont L2.53 et L10. La durée de vie L10 correspond à la durée nominale qui sera dépassée par 90 % des roulements avec 10 % de probabilité de défaillance. La durée en fatigue avec une probabilité de défaillance inférieure peut être calculée en utilisant une distribution de Weibull avec un facteur de forme de 1,5 et un facteur de forme soigneusement choisi. La durée L2.53 a été choisie pour renforcer la fiabilité du système.
Tous les calculs de durée dans le cadre de ce projet ont été réalisés avec le programme de simulation de pointe, SKF Simulator. Pour une application donnée, la durée réelle de service des roulements modernes haute performance s’avère parfois très différente de la durée nominale. En effet, la durée de service pour une application particulière dépend de toute une série de facteurs déterminants comme la lubrification, le niveau de contamination, le défaut d’alignement, le montage, l’environnement, les mouvements structuraux, les vibrations lorsque le roulement est immobile, et les décharges électriques.
La méthode AFC SKF tient compte de l’intégration totale des contraintes de contact des éléments roulants sur toute la longueur des rouleaux et évalue le nombre total de cycles de contrainte jusqu’à la fin de la durée de vie dans l’ensemble du volume chargé. La durée AFC SKF tient également compte de l’état du lubrifiant à partir de l’épaisseur du film lubrifiant et du niveau de contamination pour chaque contact individuel.
Suite au processus DfSS et aux analyses de simulation qui en ont résulté, SKF a augmenté de manière significative la durée L2.53. Modification du profil standard des rouleaux de roulements, amélioration de la rigidité du moyeu, ajout du revêtement à faible frottement SKF NoWear, revêtement au carbone anti-usure pour les rouleaux et spécification d’un système de lubrification automatique, toutes ces mesures se sont traduites par une augmentation de la durée théorique de plus de 10 %. Le roulement a été conçu spécialement pour l’application, contrairement à la grande majorité des roulements qui sont conçus dans l’objectif de couvrir une grande variété d’applications. SKF a modifié le profil des rouleaux pour l’adapter aux conditions particulières de faible vitesse combinée à des charges élevées.
Plusieurs simulations ont permis à SKF de formuler des recommandations concernant la rigidité optimale de l’ensemble moyeu et arbre, en tenant compte des aspects techniques et financiers. Les pressions de contact des éléments roulants sont directement liées à la rigidité du moyeu et de l’arbre. Le coût de l’amélioration de la rigidité du moyeu et de l’arbre a été mis en parallèle avec l’amélioration escomptée de la durée de vie L2.53. À l’issue de ces études, la décision a été prise d’améliorer la rigidité des éléments moyeu et arbre. Les exigences de durée ont été surpassées dans toutes les conditions.
Pour finir, les résultats des simulations ont été exploités pour déterminer les procédures et équipements requis pour l’installation. Les simulations de procédures d’installation ont donné des résultats quasiment identiques à ceux du montage réel sur le terrain. Comme prévu, l’installation a nécessité l’utilisation d’une assistance hydraulique pour un montage correct des roulements. L’enfoncement axial requis pour obtenir le jeu interne souhaité après montage correspondait à la valeur calculée avec 2 % de marge. Il s’agit d’une précision impressionnante, compte tenu de la complexité de la conception du moyeu.
Conclusion
La gestion du projet selon l’approche Six Sigma ainsi que les outils de simulation ont permis à SKF de concevoir une solution de moyeu qui réponde aux exigences techniques du projet, tout en tenant compte des contraintes de fabrication, transport, mise en œuvre et coûts. La solution d’axe fournie par SKF a été livrée dans le respect des délais et du budget convenus.
NoWear est une marque déposée du Groupe SKF.