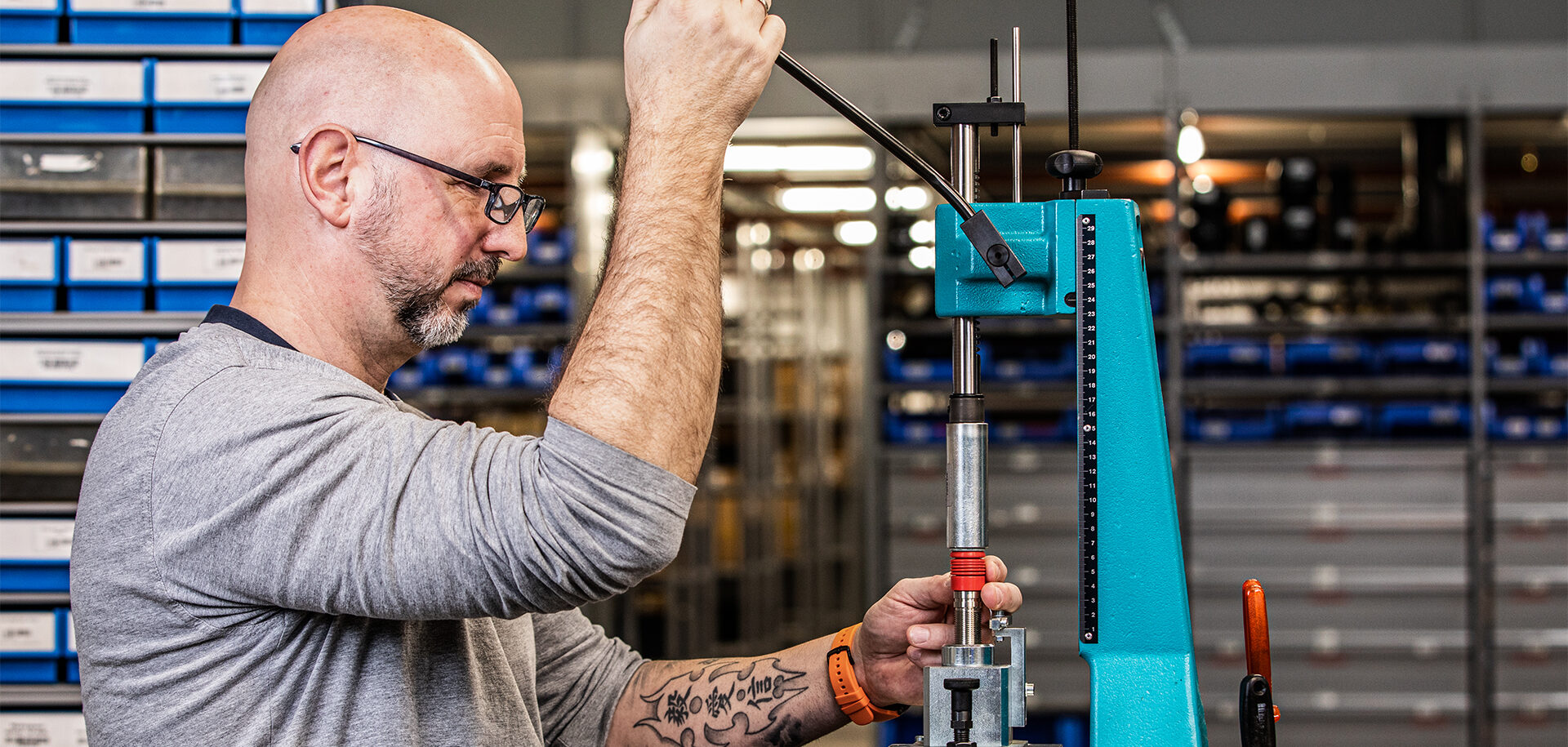
Les amortisseurs tiennent le choc
La technologie d’étanchéité SKF a permis à ACE d’accroître la fiabilité de ses amortisseurs miniatures dans les environnements de service les plus exigeants.
« Les clients choisissent nos produits quand ils ont besoin de contrôler l’arrêt d’une masse en mouvement », explique Christian Alscher, responsable du développement chez ACE. Cette fonction simple est fondamentale pour assurer le fonctionnement en toute sécurité de toutes sortes de machines et de dispositifs : matériel de manutention, systèmes d’automatisation en usine, portes d’écluses sur les canaux ou encore mécanismes de commande des télescopes géants.
Fondée à Detroit, dans le Michigan, en 1963, ACE Stoßdämpfer (connue sous le nom d’ACE Controls aux États-Unis) a conçu le premier amortisseur de choc industriel réglable au monde, dessinant ainsi les contours d’une catégorie de composants que l’on trouve aujourd’hui dans des millions d’applications à travers le monde. L’entreprise fabrique une vaste gamme de produits d’automatisation, de commande du mouvement, d’isolation vibratoire et de sécurité. Le diamètre de ses amortisseurs de choc s’étend sur une plage de 5 à 130 mm, leur longueur de course de 23 mm à plus d’un mètre.
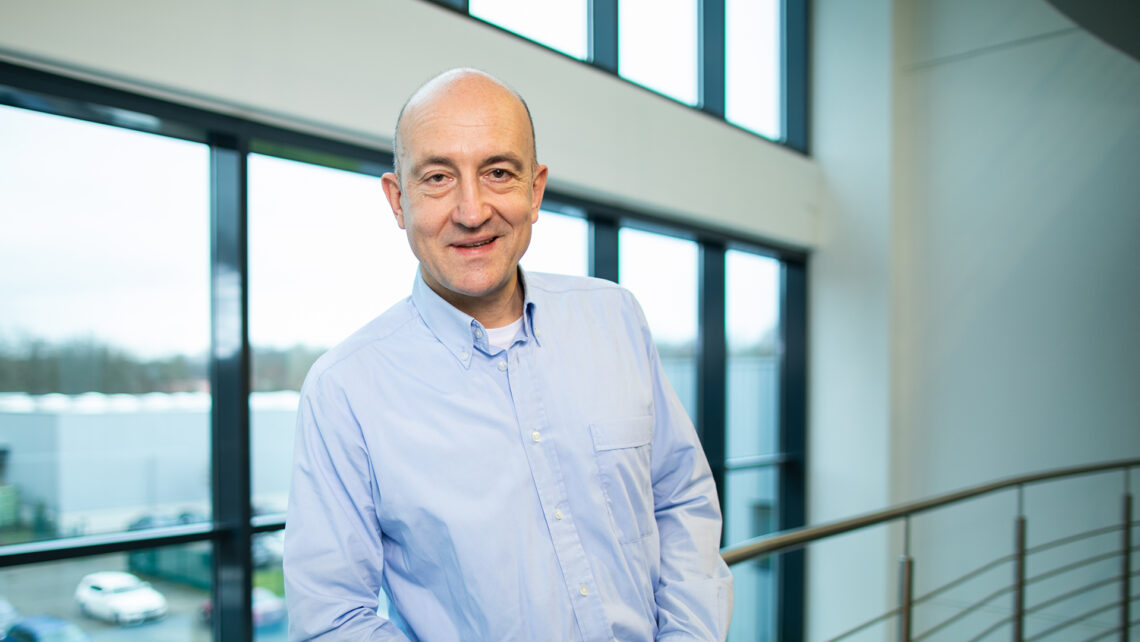
Éviter les dommages
Les produits ACE sont également soumis à des cycles de service parmi les plus divers. Quand les concepteurs d’équipements prescrivent un amortisseur d’urgence ACE, ils espèrent qu’il servira peu, voire pas du tout. En effet, ce produit sert à arrêter la machine en toute sécurité en cas de défaillance majeure du système, évitant ainsi des dommages potentiellement catastrophiques.
D’autres produits ACE ont des journées beaucoup plus remplies. Les amortisseurs miniatures PMCN ACE, par exemple, sont souvent prescrits dans les applications de production en grande série. Dans ce cas, ils servent à récupérer les pièces après leur éjection des machines-outils, ou à arrêter les vérins à grande vitesse en fin de course. Dotés d’une longueur de course de 12 à 25 mm, ils peuvent absorber une énergie pouvant atteindre 136 Nm par cycle, émise par des objets se déplaçant jusqu’à 6 m/s. Ces dispositifs compacts doivent fonctionner avec fiabilité pendant plusieurs millions de cycles sans intervention de réglage ou de maintenance.
Ils sont équipés d’une membrane roulante spéciale qui assure l’étanchéité statique et dynamique entre le piston et le réservoir d’huile. C’est une solution ingénieuse qui demande moins de composants et est beaucoup moins encombrante que les modèles d’amortisseurs classiques. Et comme les produits sont hermétiquement fermés, ils ne nécessitent aucun entretien.
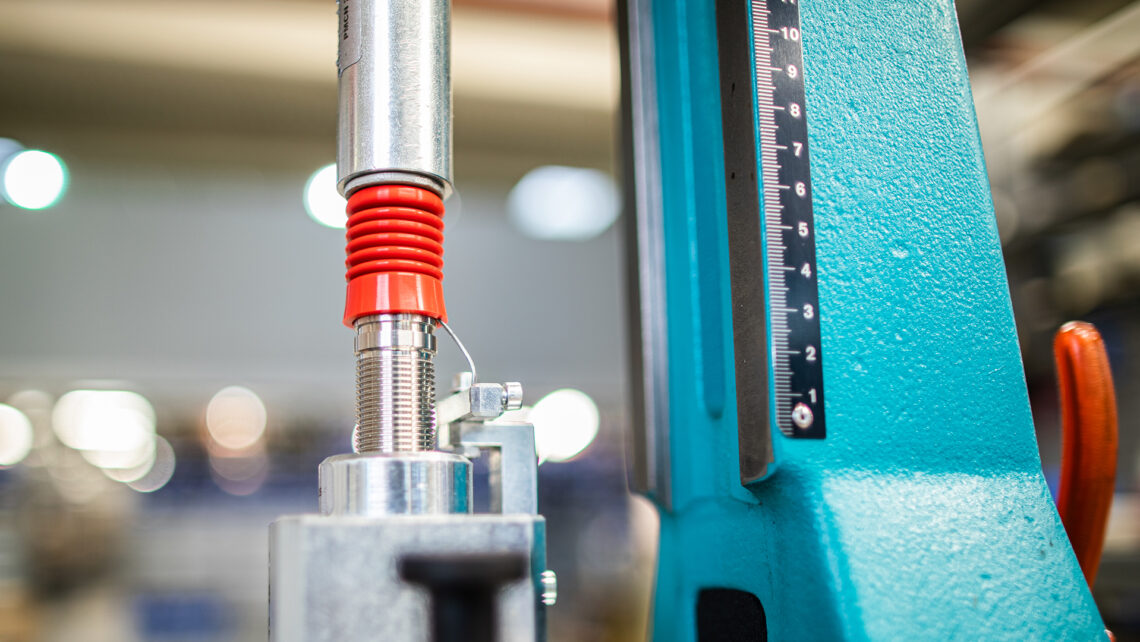
Pour les environnements industriels difficiles
Toutefois, assurer le bon fonctionnement de ces amortisseurs innovants dans des environnements industriels difficiles nécessite une approche multidimensionnelle. L’exposition à des liquides tels que les fluides de refroidissement d’usinage peut entraîner le gonflement et la défaillance de la membrane. Celle-ci doit donc être protégée des impuretés par un capuchon externe. ACE en proposait un en PTFE moulé doté d’un ressort métallique interne qui assurait le retour du piston entre chaque déplacement. Mais cette association métal/polymère s’est avérée peu fiable au fil du temps, car le ressort pouvait déchirer le fragile PTFE, entraînant des défaillances précoces. « Des clients ont commencé à se plaindre que le produit n’atteignait pas la durée de service promise, se souvient Christian Alscher. Dès que nous avons compris qu’il y avait un problème, nous avons commencé à rechercher une meilleure solution. »
Les ingénieurs d’ACE ont découvert que la principale faiblesse du capuchon était sa conception hybride. Le matériau PTFE ne possédant aucune pré-tension inhérente, le ressort interne était indispensable pour assurer le retour du piston de l’amortisseur après chaque déplacement. Le bureau d’étude s’est mis en quête d’un autre matériau capable d’assurer à la fois les fonctions d’étanchéité et de retour du piston.
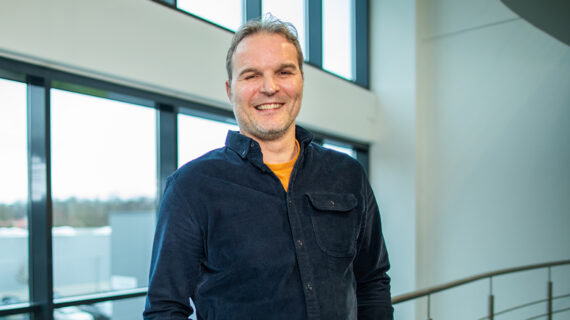
Aujourd’hui, on voit couramment ces unités fonctionner avec fiabilité après un ou deux millions de cycles, voire plus.
Jörg Küchmann
Responsable du bureau d’étude d’ACE
Innovation polymère
Plusieurs matériaux proposés par différents fournisseurs ont été évalués. Au final, cette recherche d’une solution plus simple et plus fiable a mené à SKF. Les ingénieurs des deux entreprises ont commencé à discuter de la conception des capuchons pour la première fois en 2013. Ils ont trouvé la réponse qu’ils cherchaient dans la bibliothèque SKF de matériaux spécialisés TPU H-ECOPUR®, lesquels sont très souvent utilisés dans la production de joints destinés à des applications exigeantes.
Le matériau spécifique identifié par l’équipe SKF est particulièrement résistant aux fluides de refroidissement, aux lubrifiants, aux agents de nettoyage et à la vapeur d’eau. Mieux encore, il est suffisamment résilient pour assurer avec fiabilité le retour du piston de l’amortisseur, sans nécessiter de ressort.
ACE et SKF ont perfectionné ensemble le concept de base, optimisant l’épaisseur de la paroi et la géométrie des capuchons afin d’obtenir les caractéristiques de performance idéales. La conception s’est largement appuyée sur les capacités de fabrication spécialisées de SKF : les prototypes et les capuchons ont été fabriqués à l’aide de son matériel d’usinage CNC de pointe.
Plus simple, plus rapide et plus résistant
La résistance et la résilience du matériau ECOPUR ont également permis à SKF et à ACE d’apporter d’autres améliorations qui ont simplifié le processus d’assemblage. Ils ont ajouté un bourrelet qui permet au capuchon de s’emboîter rapidement et facilement dans une rainure située sur le corps extérieur de l’amortisseur. Cette solution a remplacé le filetage interne, renforcé par une fixation par collage, qui servait à maintenir le capuchon en PTFE.
« Le système d’emboîtement a été un plus pour nous, affirme Jörg Küchmann, responsable du bureau d’étude chez ACE. L’élimination de l’opération de collage des capuchons a supprimé un autre mode de défaillance potentielle, et ce changement a rendu l’assemblage du produit plus rapide et plus simple. » Étant donné que l’équipe SKF avait une grande expérience de la conception d’interfaces pour emboîtage élastique pour d’autres produits ECOPUR, elle a pu suggérer la combinaison idéale de géométrie du bourrelet et de la rainure afin de garantir un ajustement sûr et fiable.
Les nouveaux capuchons ont intensifié la fiabilité de la gamme PMCN d’ACE. « Dans les conditions les plus exigeantes, les clients utilisant les anciens capuchons constataient des défaillances avant moins de 100 000 cycles, explique Jörg Küchmann. Aujourd’hui, on voit couramment ces unités fonctionner avec fiabilité après un ou deux millions de cycles, voire plus. » La combinaison de sa petite taille, de ses bonnes performances et de son excellente fiabilité a fait de ce produit un succès commercial.
L’ajout du capuchon en ECOPUR a également permis à ACE de lancer la gamme PMCN sur de nouveaux marchés. Le matériau du capuchon est conforme aux règlements de l’Union européenne et de la Food and Drug Administration américaine portant sur les applications pharmaceutiques ou alimentaires, par exemple. ACE fabrique désormais à destination de l’industrie agroalimentaire des variantes spéciales de l’amortisseur en acier inoxydable. Celles-ci sont remplies d’une huile de qualité alimentaire sans danger.
Après près de dix ans de collaboration, SKF et ACE continuent de collaborer sur d’autres perfectionnements et nouvelles conceptions, et prévoient, si les clients le demandent, d’installer le capuchon innovant en ECOPUR sur des amortisseurs PMCN de plus grandes dimensions.
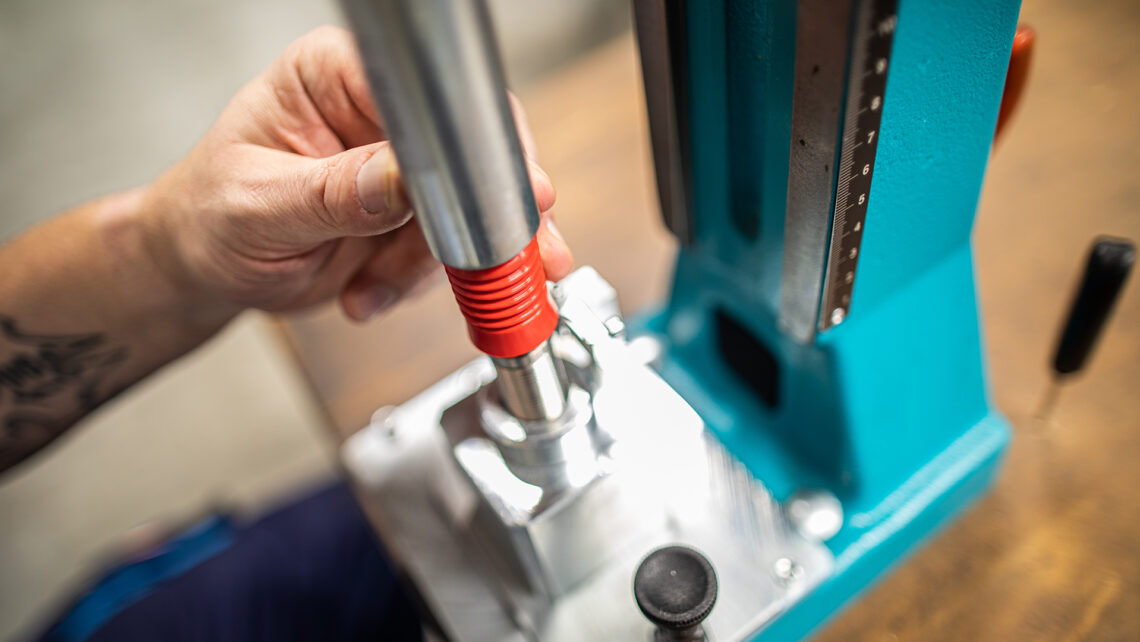