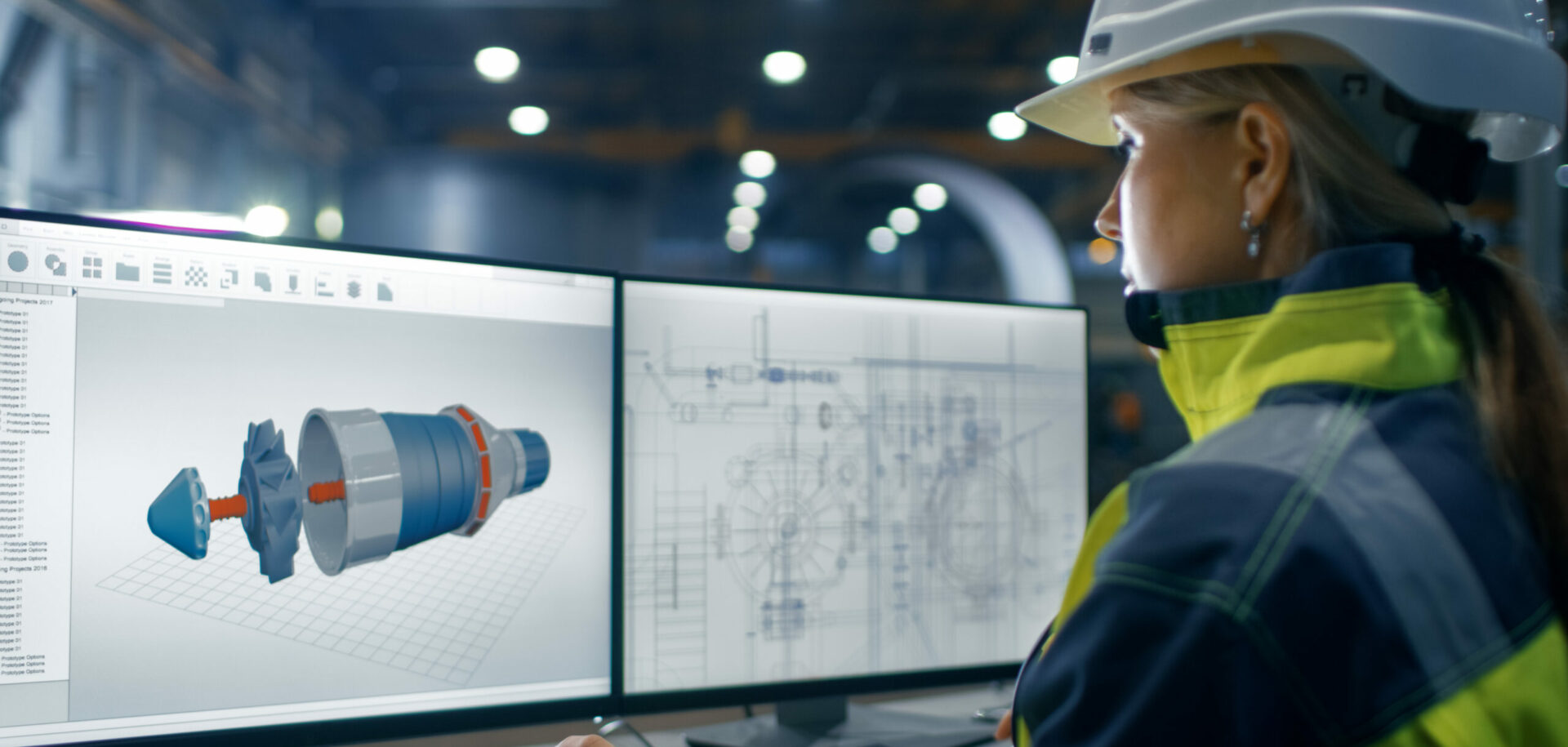
L’évolution des billes en céramique
Les éléments roulants en céramique pour roulements ont été conçus à l’origine afin d’offrir des solutions pour des applications haute performance dans le domaine des turbines à gaz de pointe. D’autres applications comme les broches de machines-outils, les moteurs et les génératrices électriques ont accéléré leur progression.
Résumé
Il y a plus de 400 ans, les premières billes produites étaient des billes en marbre utilisées comme boulets de canon. L’apparition de nouveaux matériaux céramiques techniques dans les années 1960 et 1970 a transformé ces billes en billes de roulements en céramique haute performance utilisées au départ dans des moteurs à réaction puis commercialisées pour équiper des broches de machines-outils, les moteurs électriques, la Formule 1 et l’industrie en général (pompes, compresseurs…).
Plus récemment, les roulements hybrides sont apparus au sein d’applications ferroviaires et dans le domaine des énergies renouvelables, au sein de génératrices d’éoliennes. SKF reste à l’avant-garde en matière de développement, de production, d’application et de normalisation des billes de roulements en céramique. Des travaux de développement sont en cours dans le domaine des billes de grande taille. Des billes de roulements en nitrure de silicium jusqu’à 47,625 mm de diamètre sont déjà disponibles sur le marché. Du côté des matériaux céramiques, il est possible de mettre au point de nouveaux matériaux adaptés à des applications spécifiques. Ces recherches visent à réduire les coûts de fabrication et à mettre au point des procédés moins consommateurs d’énergie, deux contraintes importantes.
Contact commercial
Oscar Schöppl, Oscar.Schoeppl@skf.com
Les roulements hybrides intégrant des éléments roulants en céramique sont utilisés dans de nombreuses applications complexes. L’industrie ferroviaire et le secteur des énergies renouvelables, avec les génératrices d’éoliennes (photo ci-contre), font partie des domaines d’application récents.
Le nitrure de silicium (Si3N4) constitue actuellement le matériau standard pour application dans les roulements et répond à des normes internationales. Des méthodes d’essai et d’inspection (Fig. 1, à gauche) ont par ailleurs été définies. La tendance est aux billes en céramique de plus en plus grandes. Des billes pour roulements jusqu’à 47,625 mm de diamètre (Fig. 1, à droite) sont actuellement disponibles sur le marché.
Des billes en céramique, en pierre et en verre sont utilisées depuis longtemps comme boulets de canon et comme lest, sans oublier bien sûr les jeux pour enfants. Le développement de céramiques techniques de synthèse dans les années 1960 et 1970 a permis aux billes en céramique en nitrure de silicium haute performance de s’imposer comme technologie de pointe dans les roulements pour des applications aussi diverses que les moteurs à réaction, les broches de machines-outils, les moteurs électriques, les voitures de Formule 1, les pompes, etc.. Des travaux de développement sont toujours en cours, notamment sur les billes de grande taille.
Développement et applications des billes en céramique pour roulements
Le rêve de mettre au point un turboréacteur d’avion (appelé aussi moteur à réaction et constituant l’application principe des turbines à gaz) à très haut rendement a donné un élan majeur au développement des céramiques techniques modernes. Les conditions de service auxquelles sont soumis les roulements de l’arbre principal au sein de telles turbines sont extrêmement exigeantes : vitesses de rotation dépassant les 30 000 tr/min et températures supérieures estimées à 650°C [1]. À des températures de gaz supérieures à 1 100°C, seuls des matériaux céramiques haute performance, qui offrent une dureté supérieure à celle des aciers pour roulements voire même des stellites à haute teneur en cobalt et des alliages d’acier à outils à forte teneur en tungstène, peuvent être envisagés. Cette application nécessite des matériaux qui sont légers (faible densité), très résistants et capables de supporter des températures élevées, et qui répondent à de nombreuses autres exigences comme la rigidité, la facilité de mise en œuvre et la disponibilité sur le marché.
Les matériaux céramiques étaient connus pour satisfaire aux deux premières exigences (résistance aux températures élevées et faible densité), mais ils étaient également réputés peu résistants et cassants. Des efforts de recherche ont été menés dans les secteurs de l’aérospatiale et de la défense pour comprendre les causes de cette fragilité. Les théories, méthodes et procédés qui en ont découlé ont permis d’améliorer certains matériaux céramiques et de développer de nouvelles céramiques de synthèse comme le nitrure de silicium. Le Centre de recherche SKF (ERC) aux Pays-Bas a beaucoup travaillé sur les matériaux céramiques depuis les prémices de leur développement.
Le nitrure de silicium est un type de matériau céramique particulier qui offre des propriétés d’auto-renforcement. Ses deux phases céramiques, le nitrure de silicium alpha et le nitrure de silicium bêta, présentent des formes cristallines différentes, parmi lesquelles des aiguilles allongées (Fig. 2). Lors de l’élaboration, l’équilibre entre les deux phases peut être ajusté de manière à obtenir un matériau résistant. Le premier nitrure de silicium du marché à offrir une résistance et une dureté adaptées aux applications de roulements était un nitrure de silicium pressé à chaud ou pressé isostatiquement à chaud (HIP).
Durant les années 1960 et 1970, l’entreprise SKF Marlin Rockwell Corp. (MRC) a mis au point les premiers roulements en céramique. Ce roulement hybride, doté d’une bague intérieure en deux parties, était fabriqué par MRC dans le cadre d’un programme d’essai financé par le gouvernement américain. L’aptitude du nitrure de silicium à l’utilisation prolongée dans un roulement lubrifié avec des lubrifiants solides sous des températures de service supérieures à 500°C a été démontrée en 1984 [1] par SKF.
Au début des années 1990, en marge des programmes d’essais aéronautiques, l’industrie des machines-outils a commencé à exploiter les propriétés de légèreté et de capacité de vitesse élevée des billes en céramique. Au milieu des années 1990, pour le pilotage des moteurs électriques, sont apparus des convertisseurs de fréquence utilisant des composants électroniques dits « à commutation rapide », qui avaient l’inconvénient de causer des dommages dans les roulements standard du fait de la présence de courants électriques, parasites, de hautes fréquences. Les roulements hybrides offraient alors une alternative très robuste pour des solutions d’isolation électrique. C’est à cette même période que les roulements hybrides ont été introduits à plusieurs niveaux sur les voitures de Formule 1, en raison de leur robustesse eu égard aux conditions difficiles d’utilisation (lubrification insuffisante, fortes charges). Le recours aux roulements hybrides dans des applications industrielles, telles les pompes et les compresseurs, date des années 2000 et a permis de surmonter des conditions de lubrification insuffisante et d’envisager l’utilisation, comme lubrifiant, de fluides avec de très faible viscosité, tels les gaz liquides réfrigérants. De plus, l’excellente résistance à la corrosion des matériaux céramiques a conduit à leur utilisation dans des applications de compresseurs de gaz sulfureux. Plus récemment, dans le secteur des énergies renouvelables, ils ont trouvé des applications dans les génératrices d’éoliennes. On utilise dans ce cas des billes en céramique de 47,625 mm de diamètre (Fig.1). Un autre domaine d’application en plein essor est l’industrie ferroviaire qui utilise des éléments roulants en céramique pour les moteurs de traction (Fig. 3). Dans ce type d’application, l’isolation électrique et les performances supérieures des éléments roulants en céramique sous des charges relativement faibles (moins de frottement et d’échauffement) ont pour effet d’augmenter la durée de la graisse.
Qualification des billes en céramique haute performance pour roulements
Afin de s’assurer que les matériaux céramiques offrent des performances optimales pour l’application dans les roulements, il convient de procéder à une évaluation approfondie des matériaux utilisés grâce à des procédures d’essai établies.
Une première évaluation du matériau peut être effectuée en contrôlant la macrostructure (Fig. 4, en haut), la microstructure et l’homogénéité (Fig. 4, au centre) sur des échantillons en coupe de matériaux de billes bruts ou finis (après préparation et polissage). De même, la dureté (Fig. 4, en bas) et la résistance à la rupture par indentation d’un matériau, candidat potentiel, peuvent être déterminées de manière rapide.
De nouvelles méthodes pour tester la résistance des billes en céramique, dans leur état « fini », ont été développées. Notamment sur les matériaux hautement résistants, on a constaté que l’état de la surface avait une influence significative sur la résistance. Et l’état de surface d’une bille est bien meilleur que celui d’un échantillon de référence, normalisé sous forme de barre. L’essai sur des « billes entaillées » (Fig. 5) offre l’avantage de permettre l’évaluation de la résistance sur des billes de roulement « réelles » et non sur des barres de flexion tel que c’est actuellement spécifié dans la norme ISO 26602:2009. Les billes sont entaillées et chargées verticalement. Le chargement sur les billes est alors comparable à celui de l’essai sur barres de flexion. Des détails concernant cet essai ont été publiés [2, 3]. Il a été montré [4] que des défauts de surface comme des fissures hertziennes en « C » ont une influence significative sur la résistance d’une bille.
Une première idée de la fatigue de contact roulant cyclique peut être obtenue à l’aide d’un disque Polymet sur une machine à tige (Fig. 6). Une tige est chargée entre deux disques en acier en rotation. L’essai de réception implique généralement 40×106cycles à des pressions de contact de 3 ou 4,8 GPa. La fatigue de contact roulant cyclique peut être également évaluée sur des billes polies grâce à une machine d’essai à quatre billes modifiée. La bille supérieure en céramique entraîne les trois billes inférieures en acier maintenues dans une cuvette, simulant un roulement simplifié (Fig. 7). Un essai similaire peut être effectué avec cinq billes, en utilisant quatre billes inférieures. Une autre possibilité pour l’évaluation de la fatigue de contact de roulement sur des billes en céramique consiste à procéder à un essai de roulement dans des rainures « en V » (Fig. 8). Une bille est chargée entre deux bagues avec pistes de roulement rainurées « en V », à des pressions de contact comprises entre 1,5 et 5,5 GPa. Dans les conditions standard de vitesse de rotation des bagues, en une heure, des billes de 28,6 mm de diamètre subissent environ six millions de cycles de contraintes.
L’endurance des roulements hybrides est testée dans différentes conditions de lubrification. Le roulement généralement utilisé pour les tests d’endurance est un roulement à billes à contact oblique 7209 doté de billes de 12,7 mm de diamètre. La Fig. 9 montre un test d’endurance pour roulement hybride lubrifié à la graisse réalisé sur un roulement à billes à contact oblique 7318 de taille supérieure doté de billes de 31,7 mm de diamètre.
Références
[1] Pallini R.A. : « Turbine engine bearings for ultra-high temperatures », SKF Ball Bearing Journal 234 (septembre 1989).
[2] P. Supancic, R. Danzer, S. Witschnig, E. Polaczek, R. Morrell : « A new test to determine the tensile strength of brittle balls – The notched ball test », Journal of the European Ceramic Society 29 2447–2459 (2009).
[3] P. Supancic, R. Danzer, W. Harrer, Z. Wang, S. Witschnig, O. Schöppl : « Strength Tests on Silicon Nitride Balls », Key Engineering Materials Vol. 409 pp 193-200 (2009).
[4] P. Supancic, R. Danzer, Z. Wang, S. Witschnig, O. Schöppl : « The Notched Ball Test – A New Strength Test for Ceramic Spheres », 9e symp. sur matériaux céramiques de Shanghai (2008).