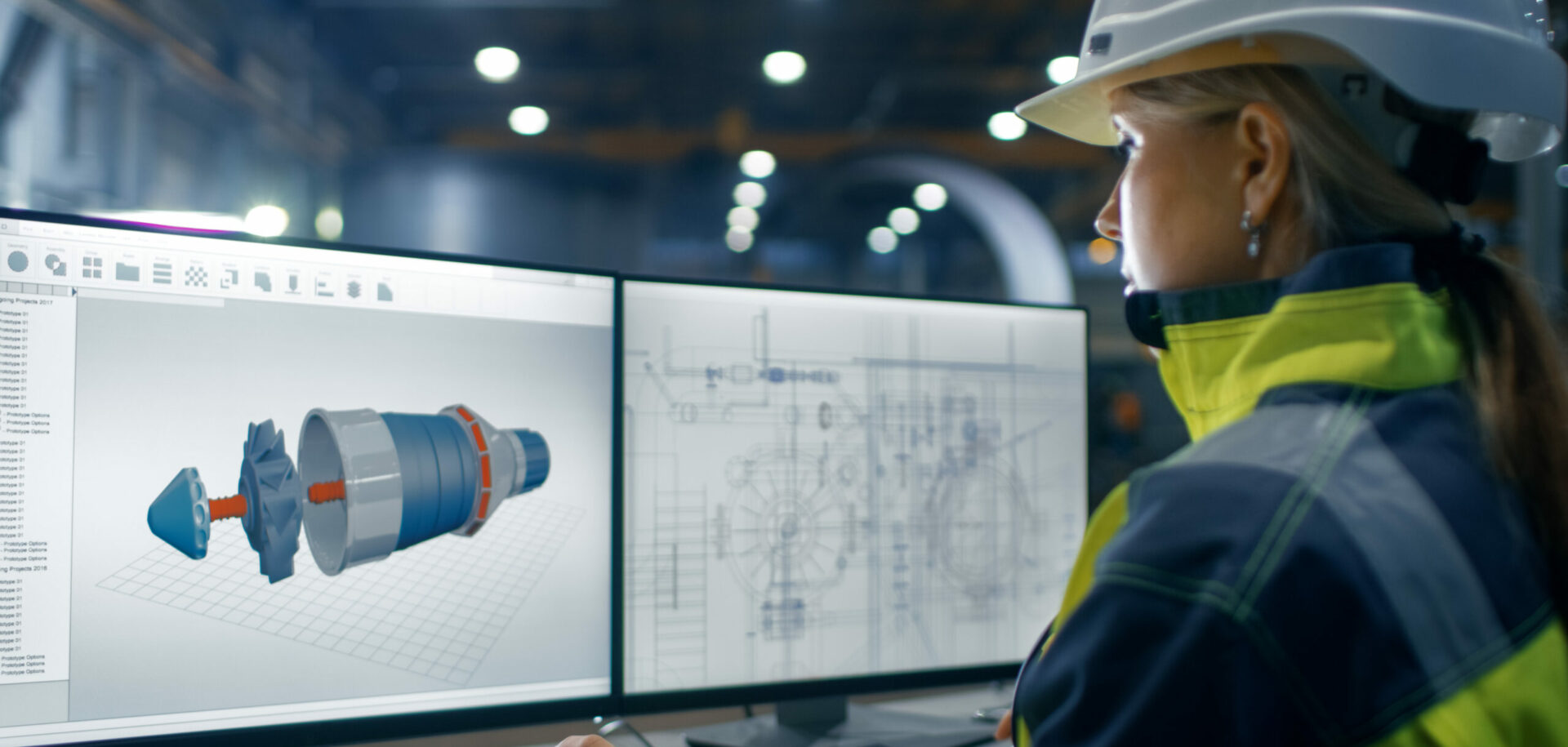
Microlubrification éco-énergétique pour broches à grande vitesse
L’apport de microdoses précises d’un lubrifiant approprié est l’une des exigences essentielles pour un fonctionnement optimal et une longue durée de service des roulements de précision. C’est ce qui a conduit SKF à mettre au point un système innovant de microdosage de l’huile.
Résumé
Le Système de microdosage SKF offre une alternative aux inconvénients de la lubrification air+huile et répond aux besoins croissants de l’industrie des machines-outils en termes d’amélioration du rendement, d’allongement de la durée de service et de réduction de la consommation d’énergie. Ce système est capable de générer quatre débits volumétriques pratiquement continus et de haute précision avec une surveillance qualitative constante sur une plage qui s’étend de 0,5 à 5 mm³/min.
Liens apparentés
Contact commercial
Dietmar Seidel, Dietmar.Seidel@skf.com
Dans le cas de broches de précision à grande vitesse utilisées à des facteurs de vitesse supérieurs à 2 millions n×dm (ce qui équivaut à plus de 30 000 tr/min sur des broches de machines-outils classiques), une lubrification fiable avec des quantités de lubrifiant soigneusement dosées apportées en un flux constant est essentielle pour garantir un fonctionnement optimal des roulements. Une quantité de lubrifiant comprise dans la plage optimale assure le frottement le plus faible possible à l’intérieur des roulements, sans frottement mixte et, par conséquent, sans augmentation de l’usure (Fig. 1).
En plus des systèmes de broches intégrant des roulements lubrifiés à vie, des systèmes de relubrification sont généralement utilisés, notamment en cas de facteurs de vitesse élevés. Ces systèmes apportent aux roulements une quantité définie de lubrifiant à des intervalles définis, en fonction de la configuration du montage, du type de roulement, des charges et des conditions de service. Des intervalles de lubrification plus courts et des quantités plus faibles de lubrifiant contribuent à un cycle de lubrification plus continu et plus fiable.
Problème actuel
La lubrification air+huile est une méthode couramment employée pour lubrifier les broches. Elle consiste à apporter aux roulements des quantités définies d’huile par des tuyaux dans lesquels circule un flux continu d’air comprimé. Ce flux d’air assure le transport du lubrifiant et permet de délivrer des petites quantités sous forme d’un filet d’huile de manière à accroître la continuité de l’apport en huile (Fig. 2). Le débit d’air et la temporisation requis pour générer la quantité d’huile sont ajustables en fonction de la tâche et de l’application de lubrification pour une utilisation très souple du système.
Ces systèmes présentent cependant un certain nombre d’inconvénients. Parmi ceux-ci, il convient de mentionner des longs temps de réponse après une modification du dosage, une précision limitée du dosage et une consommation d’air comprimé en hausse constante (indépendamment de la temporisation).
La solution : le système de microdosage SKF
SKF a mis au point un nouveau système de lubrification – le Système de microdosage SKF – comme alternative aux inconvénients de la lubrification air+huile et afin de répondre aux besoins croissants de l’industrie des machines-outils en termes d’amélioration du rendement, d’allongement de la durée de service et de réduction de la consommation d’énergie. Ce système est capable de générer quatre débits volumétriques pratiquement continus et de haute précision avec une surveillance qualitative constante sur une plage qui s’étend de 0,5 à 5 mm³/min, soit entre un centième et un dixième de goutte d’huile à la minute. Il est constitué de microvannes de précision qui, associées à un capteur de débit et des commandes complexes, permettent de délivrer de faibles quantités de lubrifiant de l’ordre de quelques nanolitres (Fig. 3).
Les microvannes sont ouvertes pendant une durée définie, de l’ordre de la microseconde, ce qui génère une impulsion de dosage d’une quantité définie de lubrifiant qui pénètre alors dans le tube capillaire raccordé. De nombreuses impulsions de dosage sont générées en une succession très rapide (intervalles de quelques millisecondes), ce qui entraîne un débit quasi continu dans le tube capillaire menant au point de lubrification (Fig. 4).
Comme les microvannes ne peuvent générer de pression à elles seules, une pression d’amorçage doit être appliquée pour l’alimentation en lubrifiant du système de lubrification. Cette opération s’effectue par le biais d’un réservoir spécial. Dans le premier système, cette pression d’amorçage est générée de manière quasi-statique et linéaire en injectant de l’air comprimé dans le réservoir. Avec une vanne d’étranglement en amont, l’air comprimé agit comme un excellent ressort linéaire. Le système de microdosage est ainsi constitué d’un doseur et d’un réservoir. Ces deux éléments sont reliés à l’unité de commande de la machine par le biais de laquelle ils peuvent être commandés et surveillés (Fig. 5). Il est ainsi possible par exemple d’ajuster la quantité de lubrifiant pratiquement en temps réel (avec un programme de la machine).
La conception modulaire permet en outre une installation décentralisée des différents modules. Le doseur, qui bénéficie d’un niveau de protection IP67, est installé sur ou à proximité des broches et le réservoir peut être positionné à l’extérieur de la machine, par exemple dans l’armoire avec les autres fluides (Fig. 6).
Surveillance et auto-étalonnage en continu
La précision élevée et constante des débits minimes repose sur de nombreux paramètres. Outre les temps d’ouverture des microvannes, la viscosité de l’huile, la température ambiante et d’autres facteurs influent sur la quantité de lubrifiant délivrée. Des fluctuations de la pression d’amorçage dues au système d’air comprimé sont également possibles et les tolérances de fabrication (des vannes par exemple) peuvent aussi avoir un impact. Pour gérer tous ces paramètres, une autosurveillance et un autoétalonnage du système sont réalisés en continu. Le capteur de débit intégré relève les quantités délivrées à travers chacune des vannes et compare ces mesures aux valeurs cibles et valeurs de référence enregistrées. En cas de dépassement de tolérances pré-
définies, le système ajuste la durée d’ouverture des vannes par impulsion. L’étalonnage est effectué séparément et consécutivement pour chaque sortie (vanne) active (Fig. 7).
Enfin, chaque vanne fait l’objet d’un paramétrage spécifique avec, par exemple, une durée d’ouverture par impulsion qui lui est propre. Les quantités mesurées au niveau du capteur de débit ou des sorties correspondent alors à la valeur cible (Fig. 8).
Par ailleurs, le processus d’étalonnage est déclenché par des événements, comme la mise en route du système après une période d’arrêt ou une variation de température de ± 5 kelvins détectée par un capteur de température intégré. Ces événements sont enregistrés par le micrologiciel du doseur. Le système lance également un étalonnage automatique toutes les quatre heures de fonctionnement.
Premiers résultats d’application
Afin de démontrer les effets du microdosage sur les roulements de broches sur la totalité de la plage de vitesse, SKF a réalisé des essais comparatifs sur un roulement équipant une broche simplifiée à entraînement par courroie sans contrôle de la température. La température du roulement relevée sur la bague extérieure a été retenue comme valeur de comparaison, car elle est relativement simple à mesurer et fournit des informations élémentaires sur le niveau de lubrification. Le lubrifiant était introduit par la bague extérieure du roulement. L’ensemble de la plage de vitesse, de 0 à 2,4 millions n×dm a été balayé par incréments de 3 000 tr/min. Chaque palier de vitesse a été maintenu pendant 30 minutes pour permettre au système de se stabiliser. La vitesse résultante du roulement, d’un diamètre moyen de 54 mm, s’est établie entre 0 et 45 000 tr/min. Le système de microdosage a été utilisé avec des réglages de la quantité différents de ceux d’un système air+huile classique.
Résultats : pour de faibles facteurs de vitesse, compris entre 0,5 et 1 million n×dm (avec une quantité minimale de lubrifiant de 30 mm³/h), la température du roulement relevée était inférieure d’environ 2 à 3 kelvins. Pour des facteurs de vitesse supérieurs, entre 1,8 et 2,4 millions n×dm (avec des doses ajustées en conséquence), les roulements présentaient une température jusqu’à 8 kelvins inférieure grâce au système de microdosage (Fig. 9).
Économies potentielles
La lubrification en continu basée sur la demande avec le système de microdosage SKF peut offrir bien d’autres avantages que la simple réduction des quantités de lubrifiant consommées. Elle permet notamment de supprimer les besoins importants en énergie liés à la production de l’air comprimé requis dans les systèmes air+huile classiques. La compression, le filtrage et le séchage de l’air comprimé consomment environ 0,1 kWh par Nm³. Sur la base des tarifs de l’électricité domestique pratiqués en Europe centrale, par exemple, l’utilisation du Système de microdosage SKF peut permettre d’économiser jusqu’à 130 euros par an et par point de lubrification. Les broches de machines-outils étant généralement équipées de trois ou quatre roulements, les économies peuvent s’élever à 390 ou 520 euros par an.
De plus, l’absence d’air comprimé offre des avantages significatifs en termes de réduction des émissions. Pour des facteurs de vitesse jusqu’à environ 2 millions n×dm, les mesures sur le banc d’essai ont révélé une diminution des émissions sonores pouvant atteindre jusqu’à 10 dB(A) par rapport à des systèmes air+huile conventionnels.