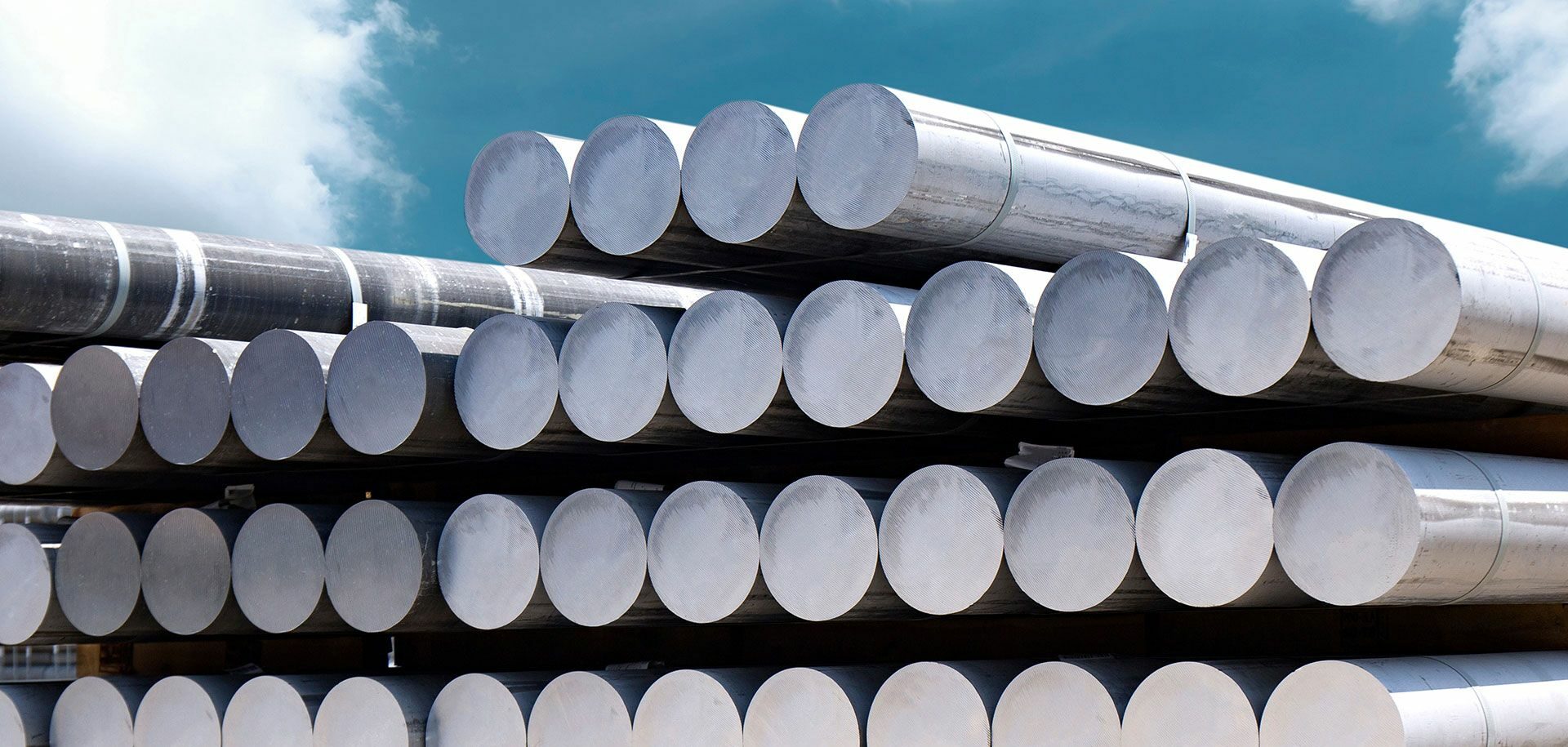
Rhapsodie roumaine
La politique de technologie au service de la fiabilité de SKF s'avère être un bon investissement pour l'un des grands producteurs d'aluminium en Europe.
ALRO (Aluminium Romania) est l’un des plus grands producteurs d’aluminium d’Europe et groupes industriels de Roumanie. Il emploie plus de 3 400 personnes sur trois sites de production dans le pays : les deux usines de Slatina incluent un four, un centre de R&D et des installations de transformation (redresseurs, un atelier d’anodisation, une fonderie, des laminoirs à chaud et à froid, et un atelier de filage) ; quant à la raffinerie d’alumine, elle est située à Tulcea, à proximité du delta du Danube et de la mer Noire.
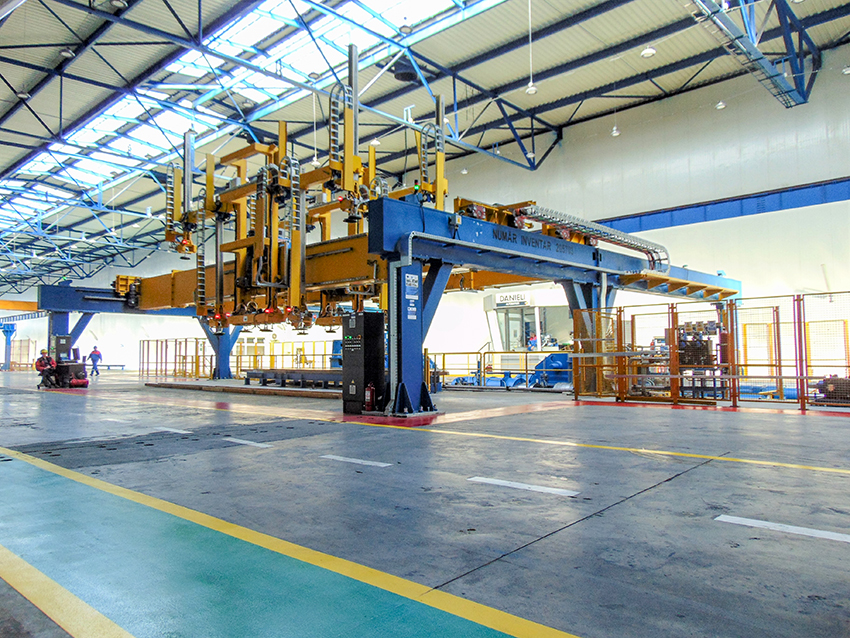
À Slatina, le complexe occupe un périmètre étendu et consomme 5 % de la production d’électricité de la Roumanie pour fabriquer des produits primaires en aluminium – fil machine, billettes et brames – et des produits semi-finis – tôles, feuillards, bobines, bandes et profilés. Par le biais de divers développements et innovations, ALRO a créé une gamme de produits qui répond aux besoins de plus de 300 clients dans les secteurs des câbles et conducteurs, de la construction, de l’automobile, de l’aéronautique et de l’ingénierie dans le monde entier.
SKF a complètement bouleversé notre approche de la maintenance.
Gheorghe Dobra, directeur général d’ALRO
« Grâce aux récents résultats obtenus en matière de contrôle des coûts pour atteindre l’efficacité opérationnelle, ainsi qu’à des programmes dynamiques d’accroissement de la capacité de production, nous avons fabriqué en 2018 210 000 tonnes d’aluminium primaire, 283 000 tonnes d’aluminium moulé, 31 000 tonnes d’aluminium recyclé et 105 000 tonnes de produits en aluminium transformé (notamment des profilés filés), des produits à haute valeur ajoutée, avec l’espoir d’atteindre 120 000 tonnes d’aluminium transformé d’ici 2021. »
L’aluminium est le 13e élément du tableau périodique et représente plus de 8 % de la masse de l’écorce terrestre. Mais l’aluminium pur qui nous est familier n’existe pas à l’état naturel. Il a été isolé pour la première fois par le physicien danois Christian Oersted au 19e siècle en appliquant la réduction électrolytique à divers minéraux riches en aluminium. Aujourd’hui, l’aluminium est principalement fabriqué à partir d’alumine, elle-même tirée de la bauxite, une roche argilacée principalement extraite sous les tropiques. Il faut quatre à cinq tonnes de bauxite pour produire une tonne d’aluminium.
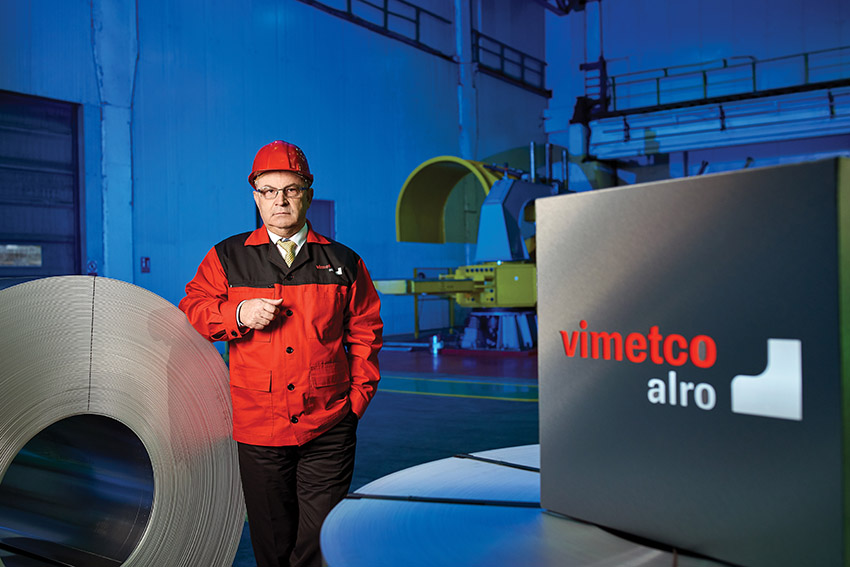
Chacune de ces catégories de produits est une matière première indispensable pour fabriquer des voitures, des trains, des avions, des téléphones, des câbles, des échangeurs de chaleur, des ordinateurs et de nombreux autres produits spécialisés et ménagers.
Le groupe ALRO est un producteur d’aluminium unique car il maîtrise toute la chaîne de valeur, des mines de bauxite aux produits pour l’automobile et l’aéronautique (notamment grâce à un atelier d’anodisation et à des installations de recyclage de l’aluminium). En langage économique, on parle d’intégration verticale : l’entreprise possède et contrôle l’ensemble du processus de production, de la mine de bauxite en Sierra Leone (le minerai arrive au port de Tulcea, sur le Danube en Roumanie, en deux semaines) jusqu’aux installations primaires et de transformation à Slatina.
Pour Gheorghe Dobra, l’entreprise a un avenir viable : « ALRO va longtemps rester un producteur d’aluminium compétitif. »
Dans une large mesure, ce succès continu en tant que producteur d’aluminium privé en Roumanie est dû à ses investissements constants dans les nouvelles technologies et les nouveaux procédés en vue d’augmenter le rendement global (par exemple, 54,8 millions d’euros ont été investis rien qu’en 2018).
SKF Roumanie bénéficie des retombées d’une partie de ces investissements. L’entreprise a conseillé à ALRO une approche basée sur le cycle de vie, l’aidant à déterminer comment utiliser au mieux les roulements et le matériel de maintenance conditionnelle SKF sur des centaines de points de mesure – fours, laminoirs à chaud et à froid, machine à brosser et machines associées. L’idée était d’instaurer une culture « d’ingénierie de la fiabilité » aux termes de laquelle les outils de production d’ALRO sont gérés conformément aux bonnes pratiques en matière de cycle de vie.
« Notre collaboration avec SKF a démarré en 2009 et, à notre avis, ils sont les meilleurs. SKF a totalement bouleversé notre approche de la maintenance, ce qui s’est traduit par une diminution de 15 % des coûts. On a commencé par déployer la technologie SKF Machine Health pour éviter 100 % des pannes accidentelles, et nous sommes près d’atteindre cet objectif. On a investi dans cette technologie, la culture et la modification des processus, et maintenant on va passer à d’autres objectifs, comme la digitalisation de la maintenance et du contrôle des processus. Notre partenariat avec SKF est extrêmement précieux pour nos plans de développement actuels et à venir. »