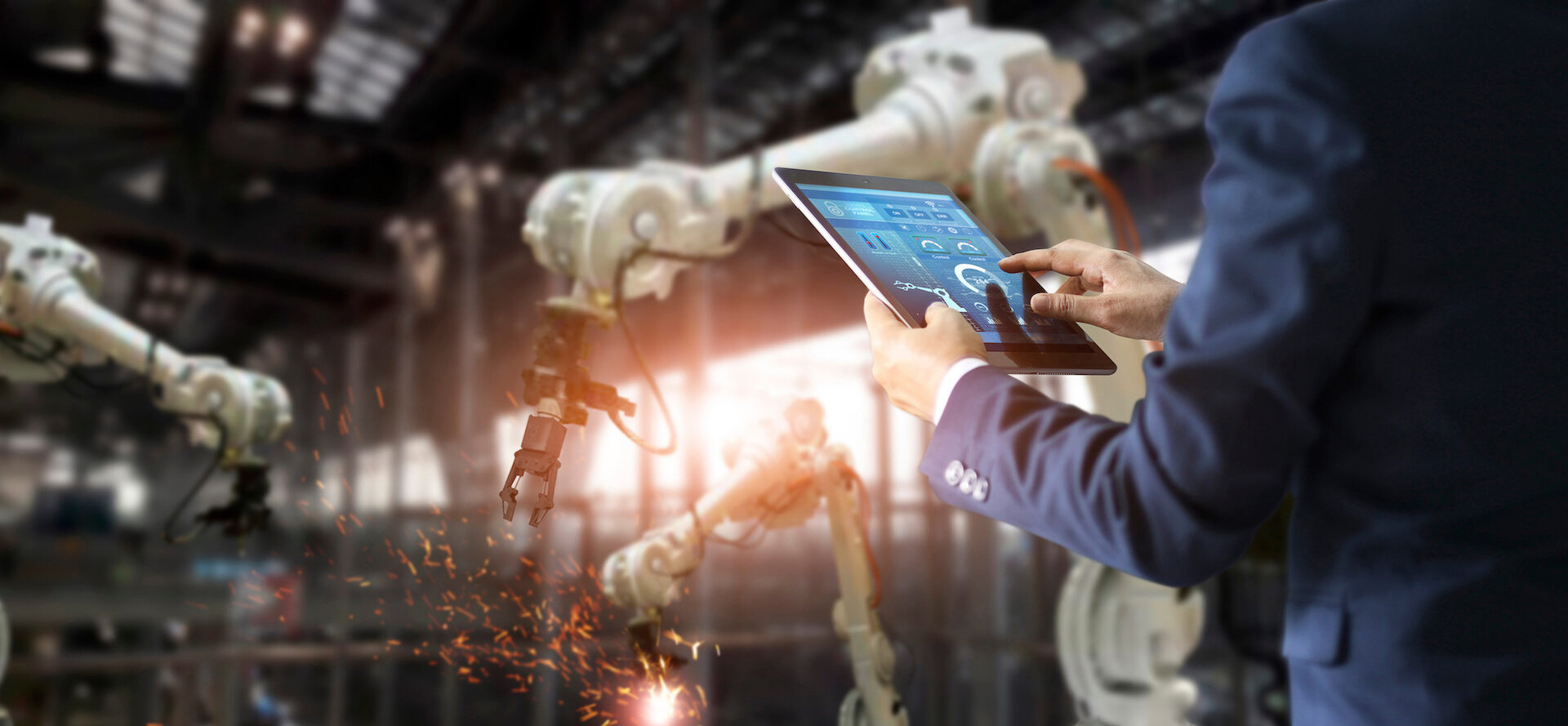
Smooth operator
Pour remplacer les paliers à rouleaux avec un galet-support entre deux paliers de son four rotatif, Argex s’est adressé à son fournisseur de longue date : SKF.
Pour remplacer les paliers à rouleaux avec un galet-support entre deux paliers de son four rotatif, Argex s’est adressé à son fournisseur de longue date : SKF.
Affaires
L’usine Argex est installée sur l’une des rives de l’Escaut, dans la verdoyante campagne flamande, à 10 km au sud d’Anvers, en Belgique. Le site avait été ouvert en 1965 par une cimenterie, située de l’autre côté du fleuve, qui voulait s’essayer à la production de billes d’argile expansée à partir de la roche extraite de la carrière toute proche. La cimenterie a fermé ses portes depuis, mais Argex, créée en 1965, continue d’extraire environ 1 000 tonnes par jour pour une capacité de production de 500 000 m3 de billes d’argile expansée par an. « Les billes Argex sont un matériau de construction léger et polyvalent dont les applications potentielles sont nombreuses, explique Johny Bultheel, directeur d’usine chez Argex. Elles peuvent servir de remblais dans le BTP (routes, parpaings, voies ferrées et cours d’eau) et sont également idéales pour les terrains de sport, les jardins sur terrasse, l’isolation des sols et les produits industriels. »
Argex traite d’entreprise à entreprise : 95 % de sa production va aux applications de BTP, les autres 5 % servent à l’hydroculture et à l’aménagement paysager. Près de la moitié de sa production totale est exportée vers les nations voisines ainsi que quelques pays non européens.
L ’argile brute provient de la carrière avoisinante. « On en extrait un millier de tonnes par jour. On a encore des réserves pour 25 ans, on n’aura donc pas à en faire venir avant quelque temps. » La roche est mélangée à de l’oxyde de fer, et parfois diluée avec de l’eau pour obtenir la consistance recherchée, avant d’être extrudée et découpée, prête à être enfournée.
Les billes sont cuites dans un four rotatif en deux parties. Celui-ci ressemble à un immense tube de 76 mètres de long et tourne nuit et jour, transformant environ 50 tonnes de billes l’heure. Sa capacité de production est de 1 800 m3 par jour. C’est le plus grand four de ce type en Europe et il se détache sans peine sur l’horizon du plat pays. Chauffé au lignite, il sert pendant deux à trois mois d’affilée avant d’être éteint pour une intervention de maintenance qui dure de deux à quatre semaines.
Les billes d’argile sont d’abord acheminées par tapis roulant jusqu’à la partie séchoir du four, qui tourne à la vitesse d’une révolution par minute. Elles y passent environ deux heures et demie à une température de 300 à 800°C. Elles sont ensuite expédiées vers la partie cuisson qui tourne à 5,2 tr/ min. Elles y demeurent pendant 30 minutes à 1 100°C. C’est là que se produit l’expansion. Enfin, elles sont évacuées vers un refroidisseur à lit fluidisé où la température oscille entre 80 et 100°C.
La dessiccation réduit naturellement les billes en tailles de 1 à 25 mm de diamètre. Chaque catégorie a son domaine d’application spécifique. Elles sont triées puis stockées en vrac.
Le four est équipé de huit paliers à rouleaux avec un galet-support entre deux paliers, comprenant chacun deux roulements. À l’origine, il s’agissait de coussinets ou de paliers lisses, mais il y a trois ans, Argex a décidé de remplacer deux des paliers à rouleaux. « On l’a fait principalement pour une question de sécurité résultant du manque de fiabilité des paliers lisses, explique Johny Bultheel. Lorsqu’on remet en route le four après avoir remplacé un ou plusieurs galets-supports, les roulements doivent être parfaitement alignés. Si ce réglage n’est pas fait avec précision, la lubrification ne se fait pas correctement, le lubrifiant peut s’échauffer et s’enflammer. »
Effectivement, les paliers ont été récemment victimes de deux incendies provoqués par un défaut d’alignement des coussinets. Parfois, l’échauffement se produit immédiatement, mais, il peut aussi s’écouler une semaine avant qu’on détecte le problème. Il faut alors arrêter la production pendant qu’on procède aux réglages nécessaires. En outre, les compétences nécessaires au réglage de ces paliers lisses sont en train de disparaître en raison du renouvellement naturel du personnel. « Autre facteur qui nous a incités à passer aux roulements à rouleaux, la consommation d’énergie, que l’on surveille toujours de près. Nous étions en quête d’une solution plus moderne avec système de lubrification plus performant engendrant moins de frottements et permettant de réduire les coûts. »
Argex s’est donc adressé à SKF. « Pour nous, une solution SKF était un choix évident. On était déjà client et, de toute façon, SKF est ce qu’il y a de mieux. On n’a pas éprouvé le besoin d’aller voir ailleurs. »
Le projet a commencé en 2008 sous la supervision de George Cant du service de maintenance. L ’étude a pris quelque temps car SKF devait fournir, en plus des roulements, le galet-support, l’arbre, les paliers et embases, le tout aux mêmes dimensions que la solution précédente afin de faciliter l’installation et de réduire son coût. Les nouveaux paliers à rouleaux de quelque 23 tonnes chacun ont été mis en place en août 2010. Ils sont équipés d’un système de lubrification automatique SKF. « À partir du moment où on a accepté la proposition, tout a marché comme sur des roulettes, témoigne Johny Bultheel. Les roulements fonctionnent parfaitement depuis qu’ils sont en service. Ce qu’on demandait à SKF, c’était une solution plus simple et plus fiable. De surcroît, ce nouveau système réduit la consommation d’énergie de 10 %. Vu l’importance de notre investissement, on espère que la durée de vie des paliers à rouleaux sera la plus longue possible. »
Argex envisage de remplacer deux autres paliers à rouleaux sur son four rotatif et espère conclure très bientôt l’affaire avec SKF.
Argex en chiffres
- Tonnes de billes/heure : 50
- Longueur du four en mètres : 76
- Tonnes d’argile/jour : 1 000
- M3 de billes/jour : 1 800
- Température maximale dans le four (en °C) : 1 200
Les produits
Les billes en argile Argex sont :
-
écologiques (100 % argile)
-
légères (densité de 320 à 750 kg/m³)
-
isolantes (thermique et acoustique), inertes, chimiquement neutres, capables de supporter de fortes charges, incombustibles, insensibles au gel et à la chaleur, très drainantes
Argex en chiffres
Tonnes de billes/heure 50
Longueur du four en mètres 76
Tonnes d’argile/jour 1 000
M3 de billes/jour 1 800
Température maximale dans le four (en °C) 1 200