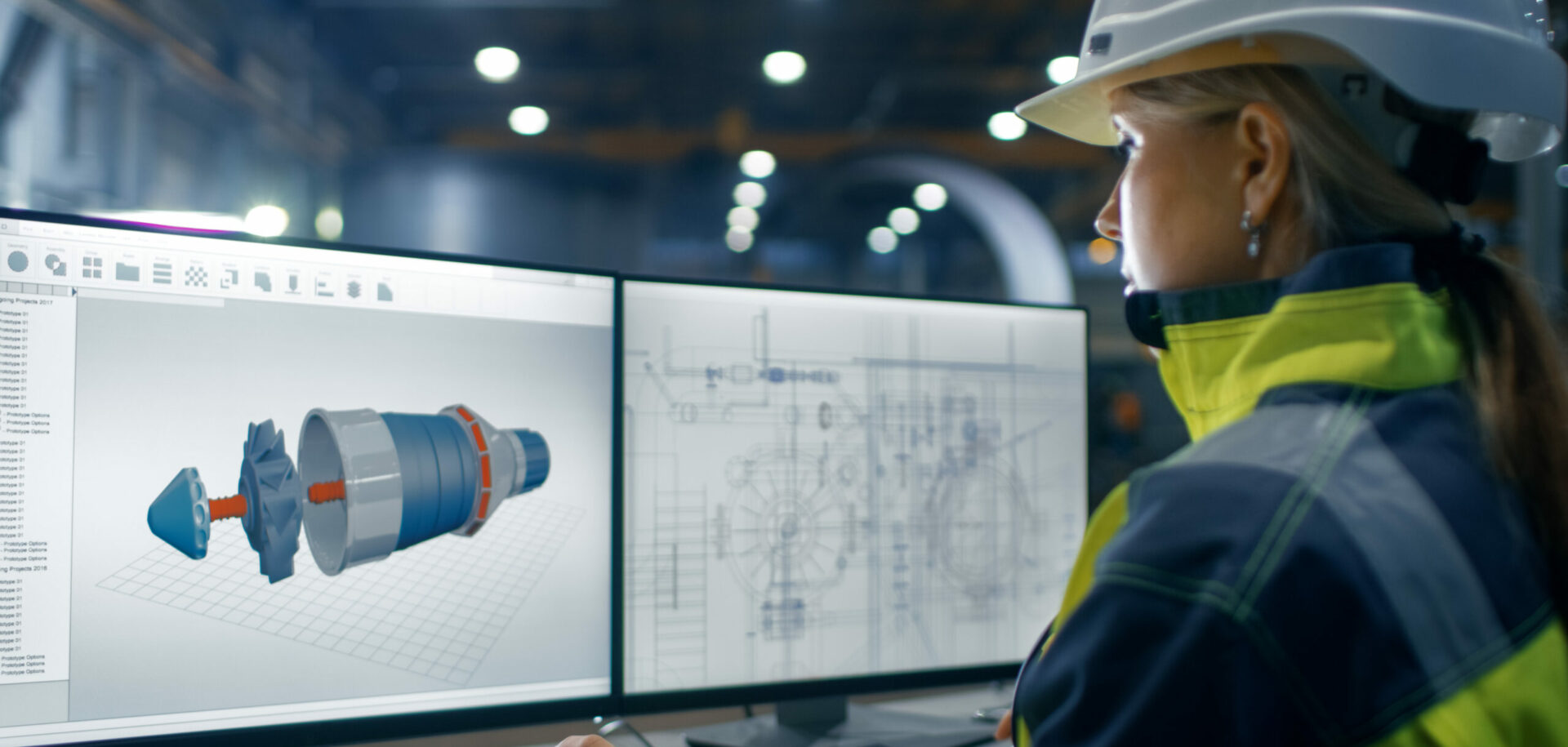
Une nouvelle génération de techniques de modélisation et simulation
SKF s’oriente vers des nouvelles techniques de modélisation et simulation pour utiliser les outils logiciels à des fins d’analyse et non plus seulement de calcul. Cette évolution permettra aux ingénieurs SKF d’explorer plus facilement des possibilités de conception plus vastes pour une application particulière de client, en tenant compte d’une multitude de facteurs et de conditions de service variées.
Résumé
SKF adopte une nouvelle génération de techniques de modélisation et simulation pour l’analyse des composants et systèmes de roulements au sein des applications des clients. Ces techniques à la fois puissantes et simples d’utilisation ont été développées pour aider les ingénieurs d’application SKF dans l’exécution des tâches d’analyse les plus complexes visant à déterminer la solution optimale pour une amélioration des performances dans les applications des clients.
SKF jouit d’une longue expérience dans le domaine des outils de simulation. Ces outils sont améliorés en continu et de nouvelles fonctionnalités et possibilités apparaissent qui permettent de simuler toutes les pièces principales (roulements, arbres, joints, engrenages et paliers) au sein d’un système complet sous forme de modèles très proches de la réalité.
Les dernières avancées en matière de modélisation et de simulation visent à relever des défis majeurs, notamment la prise en charge des tendances et besoins fluctuants des clients.
Parmi ces besoins figure, en premier lieu, la possibilité d’évaluer plusieurs options de conception pour une application donnée. Une telle demande vient accentuer la complexité de la tâche de simulation. Par exemple, pour un système de roulements destiné à une éolienne, SKF a d’abord formulé plusieurs propositions de conception avant de restreindre la sélection à seulement quelques alternatives soumises à la réflexion du client. Les nouvelles techniques mises en œuvre au sein des outils SKF permettent d’effectuer des centaines de simulations concernant les solutions de roulements proposées dans le but d’identifier la plus appropriée pour l’application du client.
En second lieu vient la question de la robustesse et de la sensibilité. Elle se rapporte à la manière dont les roulements et d’autres pièces supportent les conditions réelles au sein d’une application, conditions qui peuvent parfois s’éloigner considérablement des critères de conception. Pour certaines applications, les clients souhaitent en savoir plus sur les performances de la solution proposée dans différentes conditions de service. Si la plage de valeurs est extrêmement étendue pour certaines variables difficiles à contrôler, quel sera l’impact sur les performances du roulement ? Pour garantir un fonctionnement stable du roulement au sein de la machine du client, il est important de savoir quelles conditions de service doivent être contrôlées avec la variation la plus faible.
Le troisième point concerne la modélisation simultanée de plusieurs variables. S’il est relativement courant d’utiliser de nombreux facteurs comme variables dans la modélisation et la simulation, l’analyse de l’effet combiné de facteurs multiples simultanés constitue une tâche complexe. À partir d’une seule variable, des ingénieurs peuvent facilement effectuer plusieurs simulations entre les valeurs minimales et maximales de la plage, puis, à l’issue de ces simulations, établir une belle courbe. Lorsque trois ou quatre facteurs sont impliqués, on distingue deux difficultés majeures : la première réside dans la conception des simulations, l’autre concerne l’analyse des résultats de calcul ou du moins la visualisation des résultats. Pour surmonter ces difficultés, il est possible de faire varier un seul paramètre à la fois en gardant tous les autres paramètres constants, puis, une fois exécutées les simulations prévues, de faire varier les autres paramètres à tour de rôle. Les ingénieurs sont ainsi en mesure d’obtenir des informations sur le fonctionnement du système dans des conditions données, ce qui est mieux que rien. Toutefois, il peut leur manquer une vue d’ensemble des performances du système, notamment en ce qui concerne l’effet combiné de l’ensemble des facteurs.
Avantages offerts par les nouvelles techniques
Les outils internes SKF de modélisation et simulation de dernière génération sont conçus pour s’adapter à ces tendances et faciliter la tâche des ingénieurs en permettant, par exemple, de varier les paramètres et de réaliser plus facilement un certain nombre de simulations.
À cet égard, une caractéristique importante de cette nouvelle génération de logiciels de modélisation et simulation est l’intégration de la méthodologie Six Sigma. Cette méthode s’appuie sur une boîte à outils pour faciliter de nombreuses tâches d’ingénierie comme la conception des simulations, les études de sensibilité, les analyses de robustesse et l’optimisation des résultats. Ces outils sont également importants sur le plan de la modélisation et de la simulation. Chez SKF, toutes ces fonctions sont désormais intégrées dans la nouvelle génération d’outils de modélisation et de simulation. Elles sont accessibles par le biais d’une interface graphique interactive extrêmement simple et intuitive qui dissimule toute la complexité des formules mathématiques et autres éléments de Six Sigma. Les résultats sont également présentés de manière plus intuitive et plus visuelle par les nouveaux outils logiciels.
Dans la pratique, une telle intégration de la méthodologie Six Sigma facilite grandement la tâche aussi bien des ingénieurs SKF que des clients. Pour SKF, ils permettent à un plus grand nombre d’ingénieurs de réaliser ces analyses complexes qui étaient jusqu’ici réservées à quelques personnes disposant des connaissances et de l’expérience spécifiques nécessaires.
Quant aux clients, ils ont plus de chances de pouvoir choisir entre plusieurs options de conception. En outre, ils peuvent obtenir plus d’informations sur chacune de ces options : impact plus ou moins important de la fluctuation des paramètres ou robustesse par rapport à une autre option.
Un autre avantage offert aux utilisateurs par l’intégration de Six Sigma est que les outils ne sont pas cloisonnés : il n’y a pas un outil pour concevoir les simulations, un autre pour les réaliser et un troisième pour analyser les résultats. Tous ces outils sont intégrés au sein d’un seul environnement logiciel cohérent et facilement utilisable via une interface graphique interactive simple et intuitive après une formation sommaire.
Cas concret illustrant les avantages offerts
L’objectif était d’améliorer les performances globales d’un réducteur industriel à travers le contrôle de l’échauffement généré. Outre le logiciel de modélisation, un modèle physique a également été utilisé. Les essais ont été réalisés sur un banc d’essai FZG constitué de deux réducteurs à denture droite à un seul étage disposés dos à dos (Fig. 1). Les arbres étaient supportés par des roulements radiaux rigides à billes. Dans cette configuration, la température au niveau de la bague extérieure des roulements est utilisée pour évaluer le comportement thermique global (Fig. 2).
Quatre facteurs ont été identifiés pour contrôler la température de la bague extérieure comme indiqué dans le Tableau 1.
Chacun de ces quatre facteurs (émissivité, conductivité, vitesse de l’air ambiant et paramètres rhéologiques) a ensuite été modélisé dans le but de déterminer son influence sur la température de la bague extérieure. La Fig. 3 correspond au point de départ de la simulation avec la configuration actuelle connue de l’application en ce qui concerne la température de la bague extérieure et les quatre facteurs, présentée sous forme d’un graphique en coordonnées parallèles. Après 100 simulations avec des données d’entrée variables (Fig. 4), les résultats relatifs à la température de la bague extérieure présentent des fluctuations importantes. Un aspect notable du nouvel outil de modélisation et simulation est la possibilité pour les ingénieurs d’exécuter plusieurs centaines de simulations ; dans ce cas précis, elles ont été conçues selon la méthode Monte Carlo. De simples curseurs de valeurs maximum et minimum dans l’interface graphique du logiciel permettent d’appliquer des filtres et d’analyser les effets de chaque facteur individuel.
La solution optimale théorique représentée sur la Fig. 5 a été obtenue par filtrage et exécution d’une série de nouvelles simulations. Il apparaît clairement qu’en ce qui concerne l’émissivité, la marge d’amélioration entre la situation de départ et la situation optimale est faible. Concernant la vitesse de l’air ambiant, la température de la bague extérieure est sensible à ce facteur : l’augmentation de la vitesse se traduit par une diminution de la température de la bague extérieure. En revanche, la sensibilité à la conductivité et aux paramètres rhéologiques n’est pas significative.
Une nouvelle modélisation de la solution définie avec une vitesse de l’air ambiant optimale montre clairement la réduction de la température de la bague extérieure qui en découle (Fig. 6). L’analyse de la simulation a confirmé que le contrôle de la vitesse de l’air ambiant constituait la meilleure solution pour réduire la température de la bague extérieure du roulement dans cette application spécifique. D’après les simulations, la plage de température de la bague extérieure du roulement serait abaissée de 74–81 °C à 69–75 °C.
Le résultat concret pour le client est que le simple ajout d’un ventilateur lui permettra d’obtenir une amélioration considérable des performances.