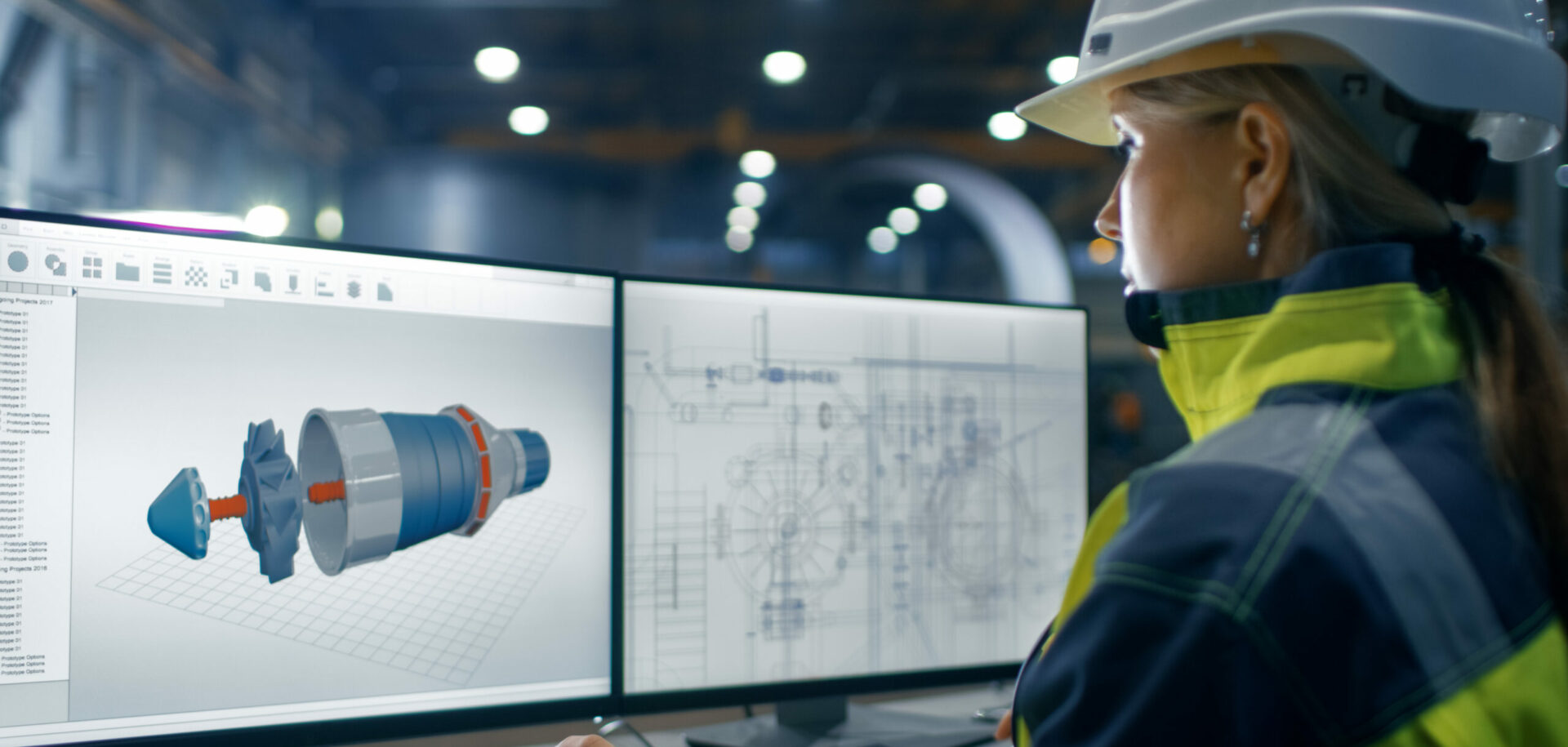
Heat treatment makes tougher bearings
New steel and heat-treatment process improve performance of heavy-duty bearingsSKF has developed and patented a new heat–treatment process for bainite steel. It results in a harder steel, without loss of toughness. The company is now using steel treated by this new process for a wide range of self–aligning roller bearings, as it provides properties required for the type of duty to which these bearings are normally exposed.
In addition the company has combined the heat–treatment process with a novel type of steel that is both harder and tougher than earlier types. Designated 755V, the steel is optimal for use in large–size spherical roller bearings and spherical roller thrust bearings.
The 755V steel is designed for bearings with rings that have a wall thickness in excess of 100 mm. Patents have been applied for.
Until now it has been difficult to create steels that combine high hardness with high toughness. Normally, hardened steel is relatively brittle, and the presence of stresses set up by the cooling or quenching processes during manufacture make it unusable in practical applications without additional heat treatment.
Because of the structural changes that occur within steel during heat treatment, the temperature needs to be accurately controlled. By choosing the appropriate tempering temperature, a wide range of mechanical properties can be achieved in steels.
Generally, in all heat–treatment processes, the steel is heated fairly slowly to a predetermined temperature, and then cooled. It is the rate of cooling that determines the resultant structure of the steel and, as a result, the mechanical properties associated with it. The final structure will be independent of the rate of heating, provided this has been slow enough for the steel to reach structural equilibrium at its maximum temperature. In practice, the subsequent rate of cooling, which determines the nature of the final structure, may vary between a drastic water quench and a slow cooling in a furnace.
Hardening is an attempt to obtain an internal structure that gives the right properties to the material, in relation to the intended application. For example, martensite appears under the microscope as a mass of uniform needle–shaped crystals. It produces high hardness but is not very ductile. Bainite, another microstructure that is important to bearing steel properties, is more laminated in nature and has better wear resistance. These are just two of the steel/heat treatment combinations employed by SKF for its bearings.
Superior hardness
The hardness of the new bainitic steel is at least as high as that obtained with martensite heat treatment or case hardening. This has been obtained without the loss of toughness, crack resistance and structural strength that characterise bainite steel. Wear tests have shown that wear resistance is more than twice that obtained with standard bainite structures. Bainite steel has a high load–carrying capacity and, due to the residual compressive stresses on the surfaces, bearing inner rings can be mounted with a high drive–up on shafts.
The 755V steel has a modified bainite transformation, which helps obtain the best properties of the steel. The hardness increases at the same time as the toughness increases by more than 60 %, compared with standard bainite heat treatment. The combination of new steel and new heat treatment process results in wear resistance that is three times higher than that obtained with the previous standard bainite treatment and steel quality used for rings that have a wall thickness greater than 100 mm.
Tomas Johannisson,
SKF Sverige AB,
Göteborg, Sweden