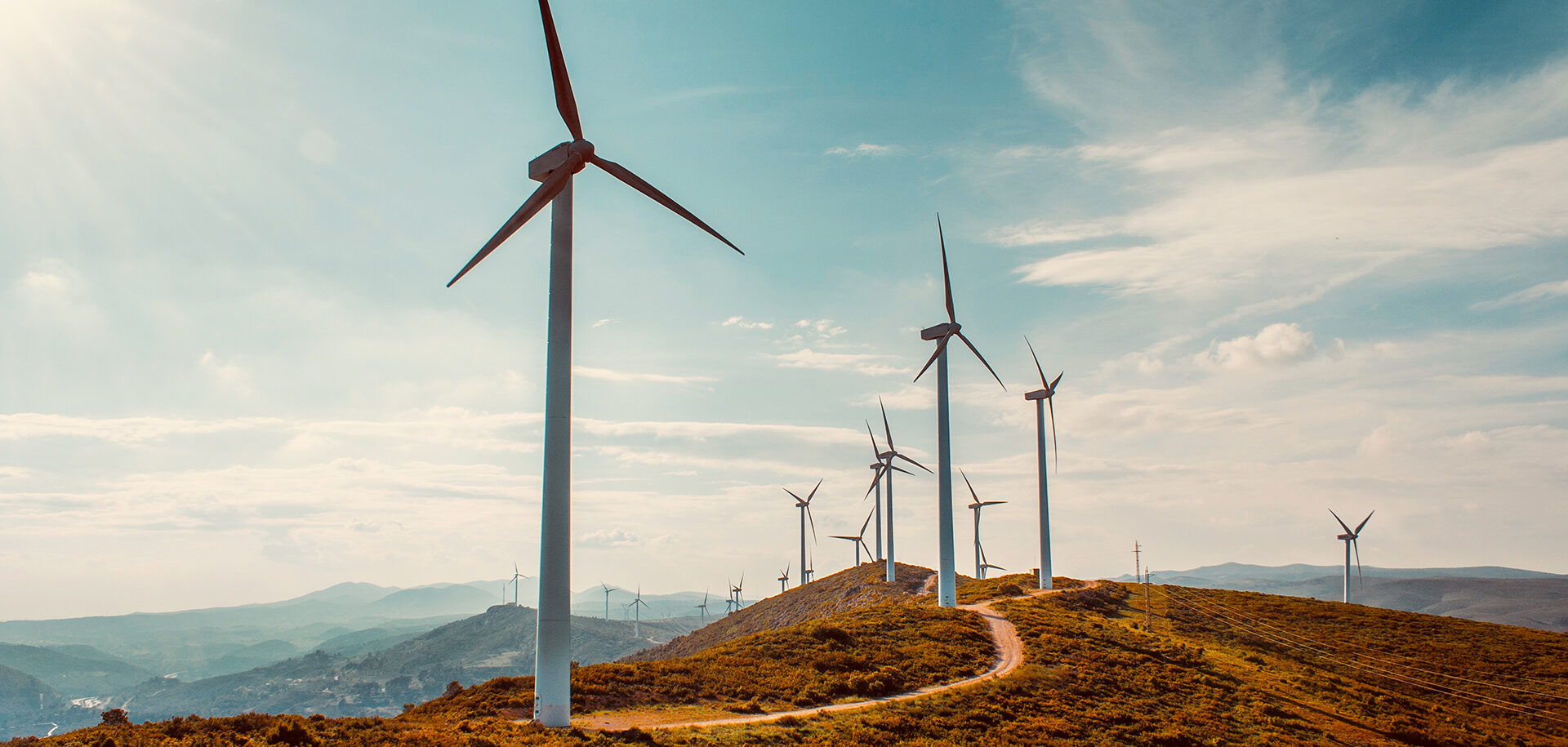
Improving wind turbine monitoring accuracy
Monitoring wind turbine operation is extremely challenging. Each turbine is subject to constant change due to the vagaries of the weather. As a result, a condition that might cause high stress on some of the components could be mistakenly attributed to a defect. SKF has made a significant step forward with the development of a new diagnostic tool to reduce the possibility of false alarms when monitoring wind turbine drivetrains.
Protean, a new diagnostic tool, has been developed to reduce the incidence of false alarms by discriminating temporary stress from defect conditions. The Protean Diagnostic feature is designed to work with SKF’s @ptitude Observer condition monitoring system (CMS) software for wind turbine drivetrain monitoring which is widely used in the wind power industry. It helps O&M and CMS technicians concentrate on potential real-performance issues, mitigating the risk of false alarms. For large wind turbine fleets, this can represent considerable time savings and make the CMS more efficient and effective.
How Protean works
In essence Protean identifies what the running conditions of the machine are and “learns” the normal behaviour with respect to different condition indicators. After a learning period of approximately one week, Protean will set threshold levels automatically for the various condition indicators, defined by the operator. Condition indicators are designed to detect various kinds of defects such as bearing and gear defects and imbalance. These condition indicators are then configured for each machine component, meaning that at least one condition indicator is used for each bearing in the machine. If an alarm occurs, Protean recalculates the threshold level according to the situation that led to the alarm. Therefore, new alarms will be generated only if the condition is getting worse. Also, one condition indicator value violating the threshold level will not trigger an alarm. It is required that “M out of the N” last condition indicator values are above the threshold level to trigger the alarm (M and N are set according to Best Practices). When maintenance has been performed, Protean detects a decrease in condition indicator level and recalculates the threshold level automatically to reflect the new situation.
To give an idea, creating a wind farm CMS set up for 20 turbines would mean adjusting some 1,000 indicators – doing this manually is just impossible. So applying diagnosis rules from SKF @ptitude software and linking to Protean and its artificial intelligence approach allows the CMS to be set up quickly and simply.
SKF CMS software allows diagnosis automation by enabling the user to build up a mathematical model of the wind turbine drivetrain from the drag-and-drop library of components, such as electric rotor, bearings, gears, planetary stage and impellers (fig. 1). The diagnostic rules, or condition indicators, have traditionally been calculated as an absolute value using frequencies that are significant for the defect to be detected. A diagnostic rule combines the amplitudes at defined frequencies based on kinematic data. In addition, the condition indicator value can also be calculated as a percent of the background noise in the measurement. Then noise that earlier led to a false positive detection can be avoided. Condition indicators are designed to react upon a defined defect in a machine component such as shaft misalignment, bearing defect, gear defect or rotor imbalance.
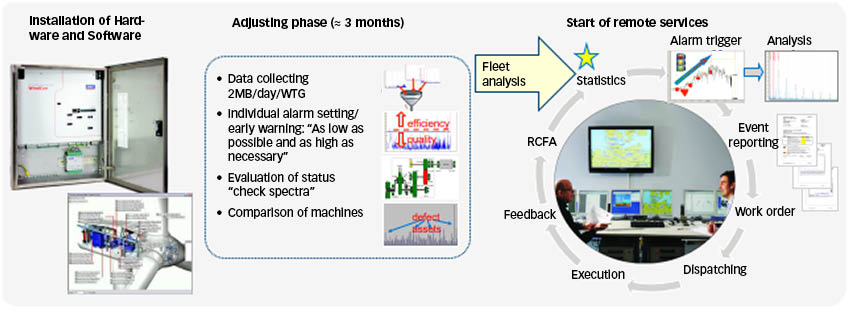
The difference Protean can make
For a possible looseness defect in a mechanical shaft, the diagnosis rules are largely applied allowing predefined condition indicators extraction (fig. 3). The library allows the usual set-up, and the user simply adjusts the alarm and danger level or chooses “auto” to let the software calibrate the alarms’ level according to the machine’s behaviour during the first run. Without Protean (fig. 4) the system reacts to the increase in mechanical looseness, but manual intervention will be needed to adjust the alarm levels.
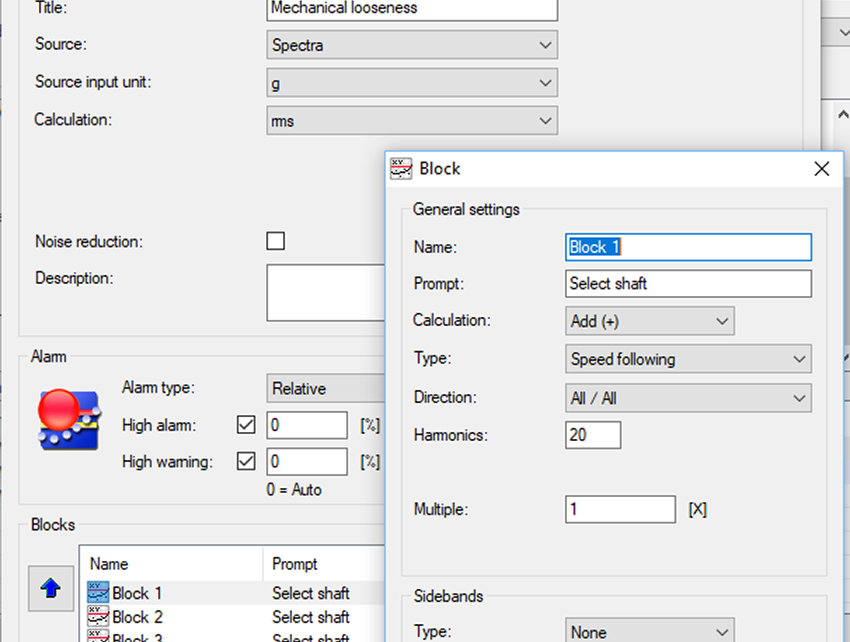

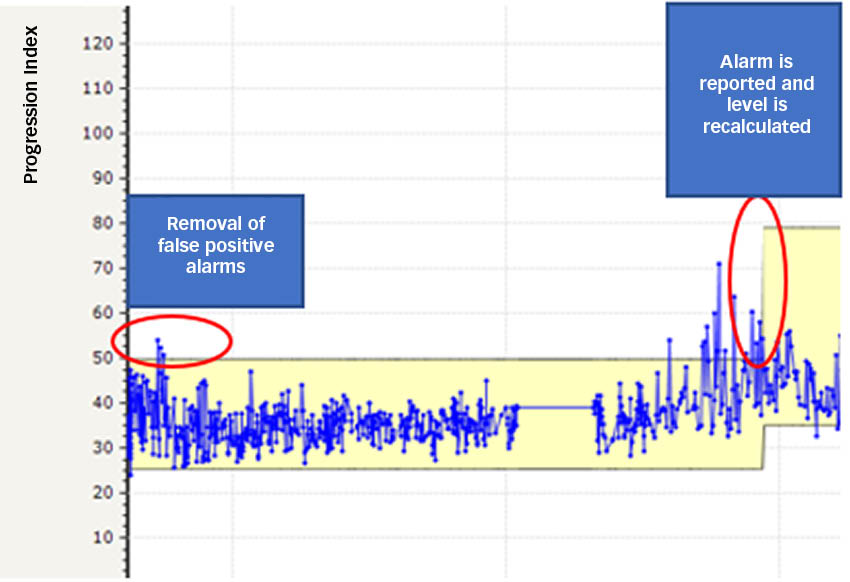
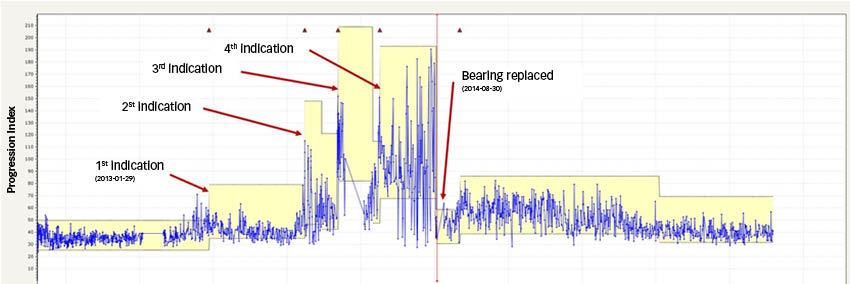

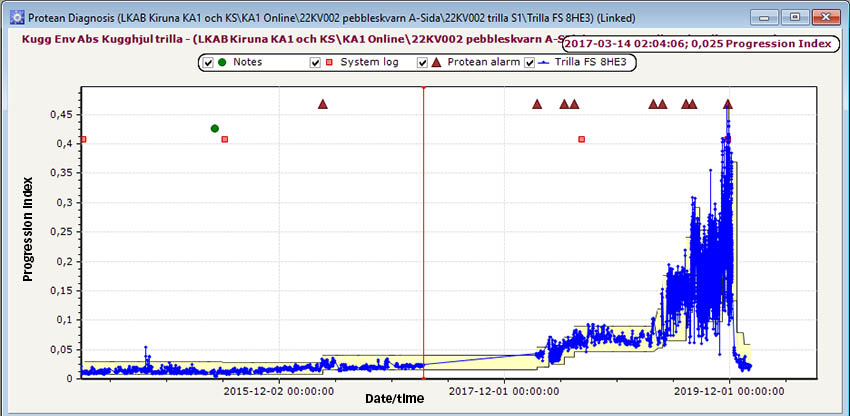
Protean is a very reliable auto diagnosis solution offering a significant reduction in false alarms without the increased risk of missing defects. It relieves CMS technicians from tedious repetitive tasks and allows them to concentrate on more difficult cases. It supports and enhances the benefits of a well-functioning CMS that detects faults and other unwanted conditions at an early stage. It allows remedial actions to be planned and performed in a timely manner and with the right quality, and it avoids consequential damage to a machine.
SKF regards Protean as a big step forward in improving detectability, accuracy and efficiency of machine condition monitoring, not only for wind turbines but for all kinds of rotating machinery. Continuous developments and new tools are crucial to make CMS a smarter technology and to help customers run their operations and maintenance processes in a more effective way.