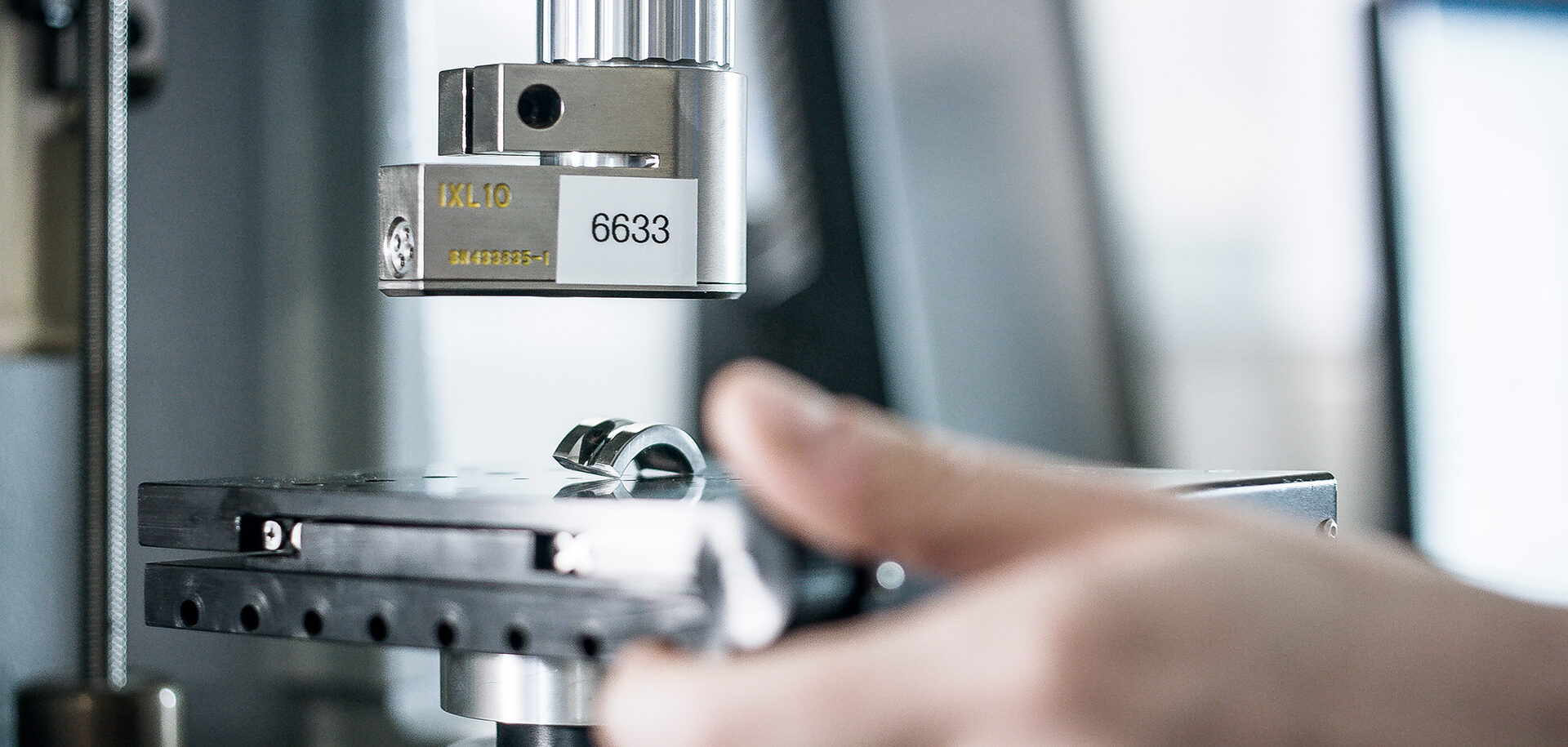
Alterazione della microstruttura dell’acciaio dei cuscinetti nella fatica da contatto di rotolamento
Il deterioramento dei materiali è la causa principale dei cedimenti dei cuscinetti volventi. Sviluppare una profonda comprensione di questo fenomeno è il modo migliore per prevedere le prestazioni dei cuscinetti e scegliere l’acciaio e i trattamenti termici più idonei ad applicazioni specifiche. Questo consente inoltre di determinare in modo più accurato la durata residua dei cuscinetti.
Il contatto di rotolamento sulle piste dei cuscinetti causa sollecitazioni cicliche che si estendono dalla superficie fino al di sotto di essa. Se le sollecitazioni superano localmente il limite di resistenza del materiale, la microstruttura si danneggia e si deteriora, dando origine a sfaldature della superficie delle piste in seguito alla fatica da contatto di rotolamento.
In condizioni di scarsa lubrificazione (rapporto di viscosità, κ < 1) il contatto metallo su metallo in corrispondenza dei picchi di rugosità può generare stress superficiale elevato. La trazione superficiale, indotta da strisciamenti anche minimi nei contatti, può anch’essa causare elevate sollecitazioni superficiali. Tali sollecitazioni possono determinare danneggiamenti da fatica superficiale, che spesso si manifestano sotto forma di sfaldature o cavità di dimensioni microscopiche.
Nei cuscinetti volventi che operano in condizioni di lubrificazione ottimali (κ > 2 ) le massime sollecitazioni di taglio si verificano a una certa profondità sotto la superficie della pista. Le sollecitazioni di taglio cicliche derivanti dal contatto di rotolamento possono causare danneggiamenti da fatica con conseguenti sfaldature della superficie della pista innescate al di sotto di essa (fig. 1). In condizioni di fatica da contatto di rotolamento si possono verificare due tipologie di deterioramento del materiale. Se le massime sollecitazioni di contatto superano un determinato limite, noto come limite di shakedown elastico, il materiale nell’area sotto la superficie subisce un progressivo flusso plastico che causa la graduale alterazione della microstruttura, che, nel tempo, può dare origine a sfaldature della pista. A sollecitazioni di contatto sotto il limite di shakedown elastico, tuttavia, danneggiamenti localizzati (a seconda delle condizioni delle sollecitazioni locali) potrebbero comunque essere causati da imperfezioni del materiale, quali le inclusioni non metalliche, a causa dell’aumento delle sollecitazioni. Questo tipo di danneggiamento è caratterizzato dalla cosiddetta “farfalla”, con cricche singole o multiple innescate da un’inclusione o da una porosità. La propagazione delle cricche si accompagna allo sviluppo di aree di white etching (WEA). In determinate condizioni la propagazione delle cricche sotto la superficie può anche portare alla sfaldatura della superficie della pista.
I danneggiamenti da fatica localizzati derivanti da imperfezioni dell’acciaio dei cuscinetti sono stati trattati in un precedente articolo [1]; queste tipologie di danneggiamento sono particolarmente rilevanti per cuscinetti a rulli di dimensioni medio-grandi. Basato su una relazione pubblicata di recente dagli autori [2], il presente articolo intende sintetizzare gli studi pubblicati in letteratura sull’alterazione microstrutturale dell’acciaio dei cuscinetti, ovvero il deterioramento del materiale al cuore in condizioni di fatica da contatto di rotolamento. L’ultima tipologia di deterioramento del materiale è particolarmente rilevante per cuscinetti di dimensioni medio-grandi che operano in condizioni di pressione di contatto elevata.
Microstruttura dell’acciaio dei cuscinetti
Carbone e cromo sono gli elementi in lega di base degli acciai per cuscinetti, utilizzati per ottenere la durezza richiesta mediante trattamento termico. Sono necessari leganti aggiuntivi per aumentare la durezza dell’acciaio per componenti dei cuscinetti di dimensioni medio-grandi.
I componenti dei cuscinetti temprati in genere sono sottoposti a trattamento termico per produrre una struttura martensitica o bainitica. Il presente articolo si concentra sulla struttura martensitica dell’acciaio per cuscinetti.
La tempra a struttura martensitica prevede l’austenitizzazione, seguita dalla tempra in bagno d’olio o di sale e dal rinvenimento a bassa temperatura per bilanciare le proprietà contrastanti. Durante l’austenitizzazione una frazione della cementite sferoidale si dissolve, determinando un contenuto di carbonio pari allo 0,6-0,65 del peso percentuale dell’austenite. Dopo la tempra la martensite si forma con una frazione dell’austenite residua. Il rinvenimento successivo causa la precipitazione dei carburi di transizione e la trasformazione dell’austenite residua in martensite, con la conseguente riduzione del contenuto di austenite residua, che diminuisce con la temperatura di rinvenimento e può arrivare a zero se tale temperatura raggiunge i 220 °C. In figura 2 è riportata una rappresentazione schematica della struttura martensitica dopo il trattamento termico. Nel grano iniziale di austenite vi sono dei pacchetti di martensite, cementite residua e austenite residua. Ciascun pacchetto contiene dei blocchi in cui si formano i listelli di martensite. I carburi di transizione precipitano nei sottograni di martensite durante il rinvenimento.
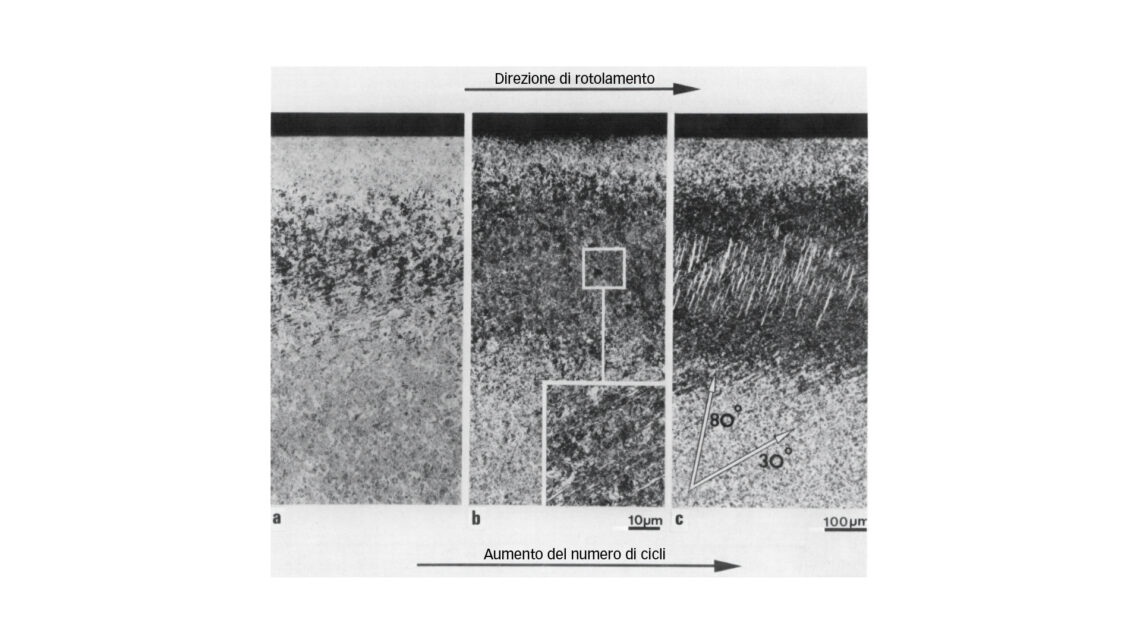
Risposta del materiale alla fatica da contatto di rotolamento
Se la pressione di contatto massima supera il limite di shakedown elastico, nell’acciaio del cuscinetto nell’area sotto la superficie si verifica una progressiva alterazione microstrutturale in seguito all’accumulo di microplasticità. Tale processo di deterioramento è visibile mediante microscopia ottica come un’area di intacco scuro (DER, dark etching region). Con l’avanzare della fatica da contatto di rotolamento nell’area di dark etching si sviluppano bande di intacco bianco (WEB, white etching band) con due orientamenti diversi. Alla formazione di bande a basso angolo con un orientamento di circa 30° rispetto alla direzione di rotolamento segue lo sviluppo di bande ad alto angolo, che sono orientate con un angolo di circa 80° rispetto alla direzione di rotolamento. La figura 3 mostra un’immagine al microscopio dell’alterazione microstrutturale sotto la superficie.
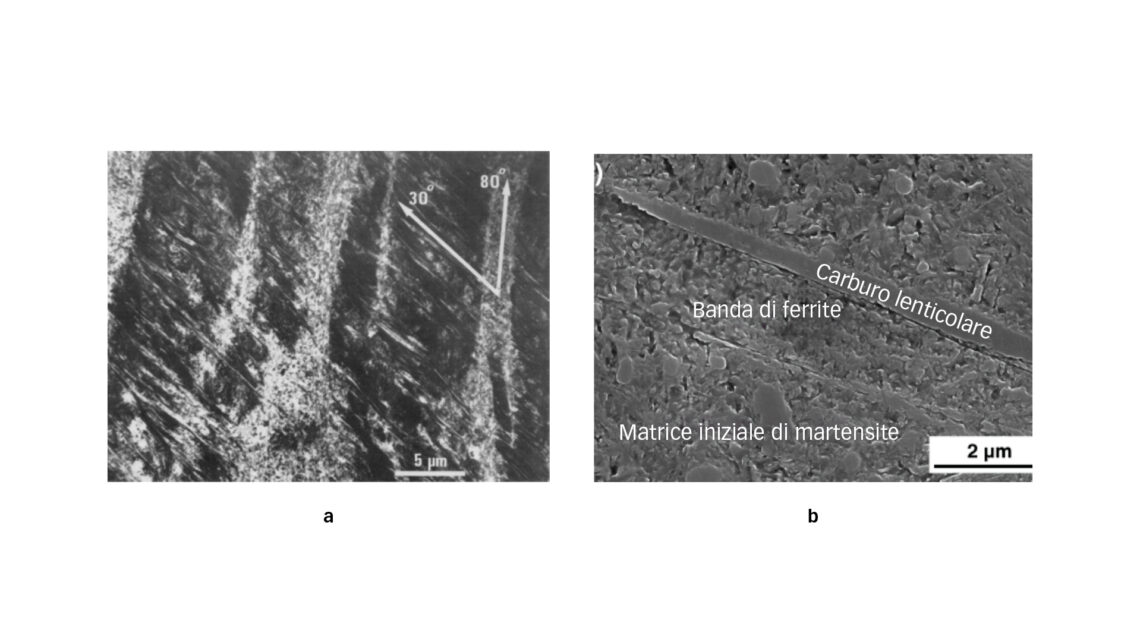
La caratterizzazione dell’area di dark etching mediante microscopia elettronica in trasmissione indica che le microbande di ferrite [3, 4] si formano nella matrice di martensite (fig. 4). Se osservate dalla sezione circonferenziale, le microbande sono densamente ravvicinate o raggruppate. Le microbande in ogni gruppo hanno lo stesso orientamento, ma possono avere un orientamento diverso rispetto a quelle in altri gruppi. Sulla sezione trasversale (di un anello), tuttavia, le microbande appaiono parallele alla superficie della pista. Queste osservazioni suggeriscono che le microbande sono piastre sottili il cui orientamento cambia solo rispetto alla direzione di rotolamento. Inoltre, le microbande si possono estendere lungo i bordi della piastra di martensite [5].
Un’altra caratteristica rilevante visibile nelle aree di dark etching è la ferrite allungata, che si forma nella struttura della matrice di martensite in seguito a fatica da contatto di rotolamento, ma appare come elemento isolato e non in gruppo come le microbande di ferrite. È evidente che la ferrite allungata cresce fino a formare grani di ferrite di grandi dimensioni nelle bande a basso angolo e in quelle ad alto angolo [5]. In modo analogo alle microbande di ferrite, la ferrite allungata ha una forma simile a una piastra sottile e si trova a un angolo di 30° o 80° rispetto alla superficie della pista, se osservata dalla sezione circonferenziale (fig. 5a). Dalla sezione trasversale le bande appaiono invece parallele alla superficie della pista. Le bande a basso e ad alto angolo sono bianche se osservate al microscopio ottico (si veda fig. 3). Ecco perché in genere sono denominate bande di white etching. La loro struttura interna può essere molto eterogenea lungo lo spessore. Le bande a basso e ad alto angolo possono essere costituite da ferrite allungata e ferrite policristallina di dimensioni nanometriche [6].
L’aspetto delle bande di white etching dopo circa 109 cicli di sollecitazione in genere si osserva in combinazione con i carburi lenticolari [7], che si formano sul lato e parallelamente alle bande di white etching di grandi dimensioni. Una banda di white etching completamente formata può essere lunga 50-60 µm e larga 10 µm, mentre lo spessore di un carburo lenticolare può arrivare a misurare 1 µm. La formazione di carburi lenticolari è correlata alla dissoluzione parziale della cementite residua, ma non alla sua dissoluzione completa [4-8]. In figura 5b è mostrata una struttura a sandwich nell’area delle bande di white etching, in cui una banda di ferrite e un carburo lenticolare si trovano vicino alla matrice iniziale di martensite [9].
La cementite residua è molto più dura della matrice di martensite temperata e pertanto si ritiene che abbia una maggiore resistenza alla deformazione plastica. Tuttavia, la ferrite allungata e le microbande di ferrite crescono grazie alla cementite residua, causandone la dissoluzione [3, 10]. Dopo numerosi cicli di sollecitazione le particelle di cementite residua nell’area maggiormente sollecitata mostrano spesso bordi non omogenei, il che suggerisce che la cementite si stia dissolvendo nel processo di fatica da contatto di rotolamento.
Vi sono diversi fattori che influenzano o regolano l’alterazione microstrutturale nella fatica da contatto di rotolamento, incluse la struttura iniziale, le sollecitazioni residue e le condizioni di esercizio, quali la pressione e la temperatura. Essendo un processo termico-meccanico, il tasso di alterazione microstrutturale aumenta con la pressione di contatto e/o la temperatura.
L’alterazione microstrutturale è un processo di migrazione del carbonio dovuto allo scorrimento di dislocazione indotto dalla plasticità (fig. 6). Per l’acciaio dei cuscinetti con tempra a struttura martensitica la struttura iniziale consiste di martensite temperata contenente precipitati di dimensioni nanometriche (carburi di transizione), austenite residua e cementite residua. La formazione di aree di dark etching comporta la trasformazione della martensite temperata in ferrite sotto forma di microbande di ferrite e ferrite allungata, in seguito alla migrazione del carbonio dalla matrice di martensite dovuta alla dislocazione. Nel frattempo l’austenite residua si trasforma parzialmente in martensite in seguito alle trasformazioni di fase indotte dalle sollecitazioni e dalle deformazioni; la cementite residua invece rimane intatta nella fase iniziale, ma si dissolve gradualmente in alcune aree con plasticità fortemente localizzata. Con l’avanzare della fatica da contatto di rotolamento le microbande di ferrite e la ferrite allungata si sviluppano ulteriormente in bande di ferrite, che vengono visualizzate come bande a basso angolo (LAB, low-angle band) e bande ad alto angolo (HAB, high-angle band). Gli atomi di carbonio dalla matrice e i carburi dissolti si separano fino a formare carburi lenticolari tra le bande di ferrite.
È controverso se gli atomi di carbonio migrino nella fase di formazione delle aree di dark etching. Nello specifico si tratta di stabilire se gli atomi di carbonio nella martensite vengano trasportati verso i carburi di transizione [9], causandone il cosiddetto ingrossamento, o altrove, come ai bordi delle microbande di ferrite o dei grani di ferrite allungata appena formati [11].
I danneggiamenti da fatica della martensite temperata a bassa temperatura nel contatto di rotolamento si accompagnano alla decomposizione dell’austenite residua e all’accumulo di sollecitazioni residue compressive, che si possono analizzare mediante diffrazione a raggi X [12–14]. Sebbene la trasformazione mediante sollecitazione da austenite residua a martensite si verifichi nella fase iniziale e continui con l’avanzare della fatica da contatto di rotolamento, tale processo è correlato alla formazione di aree di dark etching e al conseguente sviluppo di aree di white etching [12, 13]. Dopo un numero sufficiente di cicli di sollecitazione la decomposizione completa dell’austenite residua può aver luogo nell’area maggiormente sollecitata.
Il degrado microstrutturale si riflette anche nella variazione della durezza. Si è scoperto che la durezza media della struttura alterata è decisamente inferiore a quella della struttura iniziale [9, 13, 15]. Inoltre si è osservato che un aumento iniziale minimo della durezza è seguito da una diminuzione significativa della durezza nella microstruttura degradata dopo diversi cicli di sollecitazione [10, 16]. L’aumento iniziale della durezza è una conseguenza dell’incrudimento. Con l’avanzare della fatica da contatto di rotolamento la migrazione del carbonio dovuta alla dislocazione porta a un degrado sempre più disomogeneo della microstruttura con aree a ridotto contenuto di carbonio e aree arricchite di carbonio. La riduzione del carbonio nella matrice di martensite causa un graduale aumento della durezza della microstruttura degradata.
Considerazioni finali
Il cedimento di un cuscinetto volvente è essenzialmente una conseguenza del deterioramento dei materiali in determinate condizioni di esercizio. Comprendere questo fenomeno è fondamentale per prevedere le prestazioni dei cuscinetti, consentire la scelta ottimale dell’acciaio e dei trattamenti termici per applicazioni specifiche e determinare la durata residua dei cuscinetti. Pronosticare le prestazioni dei cuscinetti, e valutare quindi la loro durata residua, può essere utile per validare la scelta dei cuscinetti o per segnalare eventuali modifiche nel loro impiego o nella relativa manutenzione, due fattori che possono prolungarne la durata in esercizio.