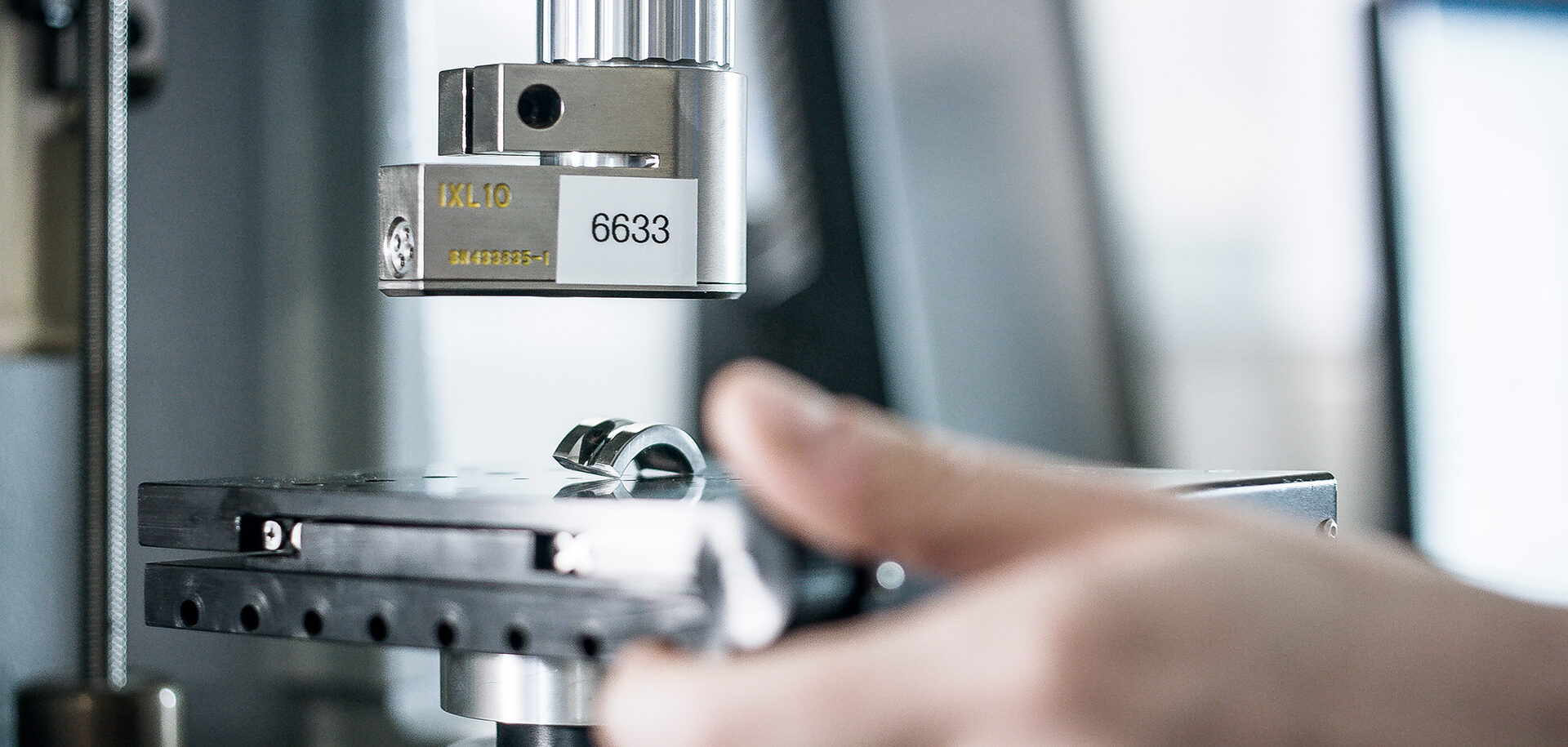
轴承钢在滚动接触疲劳中的微观结构变化
材料退化是滚动轴承失效的主要原因。预测轴承故障的最佳方法是深入了解材料退化机制。这不仅有助于为具体应用选择最佳钢材和热处理工艺来达到轴承预期的性能,还可以更准确地预测轴承剩余寿命。
轴承滚道上的滚动接触会产生从表面延伸到次表面区域的循环应力。如果循环应力超过材料的局部强度极限,微观结构就会发生损坏或退化,最终可能会因滚动接触疲劳 (RCF) 而导致滚道表面剥落。
在润滑不良的条件下(粘度比 κ < 1),粗糙表面的金属与金属接触会产生很高的表面应力。即使是由接触面的少量滑动引起的表面引力,也会导致较高的表面应力。这种应力可能导致表面疲劳损坏,通常表现为微剥落或凹坑。
在良好润滑条件下 (κ > 2 ) 运行的旋转轴承,最大剪切应力存在于滚道表面以下一定深度处。滚动接触产生的循环剪切应力会引起疲劳损坏,最终导致滚道发生次表面起源型剥落(图 1)。在滚动接触疲劳条件下,可能会发生两种类型的材料退化。如果最大接触应力超过某个极限(称为弹性安定极限),则次表面区域的材料会发生渐进的塑性流动,引起渐进的微观结构改变,最终导致滚道剥落。
然而,当接触应力低于弹性安定极限时,由于应力集中效应,局部损伤(取决于局部应力条件)仍可能由非金属夹杂物等材料缺陷发展而来。这种类型的损伤具有所谓的蝴蝶状损伤特征,即从夹杂物或孔隙处萌生单条或多条裂纹。裂纹的扩展伴随着白色蚀刻区 (WEA) 的发展。在某些条件下,次表面裂纹的扩展也可能导致滚道表面剥落。
轴承钢材料缺陷导致的局部疲劳损伤已在之前的文章 [文献1] 中讨论过;这些类型的疲劳损坏与大中型滚子轴承密切相关。本文基于作者最近发表的一篇综述论文 [文献2],旨在总结文献中发表的关于轴承钢微观结构变化的研究,即滚动接触疲劳下的大面积材料退化。后一种材料退化类型与较高接触压力下运行的中小型轴承密切相关。
轴承钢的微观结构
轴承钢中掺入碳和铬等基本合金元素,并通过热处理达到所需的硬度。对大型轴承部件,还需要掺入其他的合金元素来提高钢的淬透性。
整体硬化轴承部件时通常进行热处理以产生马氏体或贝氏体结构。本文重点介绍轴承钢的马氏体结构。
马氏体硬化包括奥氏体化,然后在油浴或盐浴中淬火,再进行低温回火以平衡其不稳定的性能。在奥氏体化过程中,部分球状渗碳体溶解,致使奥氏体中的碳含量达到0.6-0.65 %重量。淬火后,马氏体形成,残留部分奥氏体。随后的回火导致过渡型碳化物的析出和残余奥氏体进一步转变为马氏体,使得残余奥氏体含量降低。 可见,残余奥氏体含量是随回火温度的升高而降低,如果回火温度达到 220 °C ,残余奥氏体含量可降至零。 图 2 显示了热处理后马氏体结构的示意图。在原奥氏体晶粒内部有马氏体板条束、残余渗碳体和残余奥氏体。 每个板条束都包含若干板条块,其中有形成的马氏体板条。在回火过程中,马氏体亚晶粒内部析出过渡型碳化物。
滚动接触疲劳的材料响应
如果最大接触压力超过弹性安定极限,次表面区域的轴承钢由于塑性微变形的积累发生渐进的微观结构变化。这种退化过程在光学显微镜 下表现为暗蚀区的出现。随着滚动接触疲劳的加剧,在暗蚀区内部生长出具有两种不同取向的白蚀带。先在过度碾压约 30 º方向形成低角度带,然后是在过度碾压约80 º方向逐渐生长出高角度带。图 3 显示了次表面微观结构改变的显微照片。
使用透射电子显微镜对暗蚀区进行研究表明,铁素体微带 [文献3、4] 在马氏体基体中形成(图 4)。从圆周截面看,微带呈密集排列或成簇分布。每个簇中的微带具有相同的取向,但有时与其他簇中的微带具有不同的取向。然而,在横截面(轴承套圈的横截面)上,微带平行于滚道表面。这些观察结果表明,微带是薄板条,其取向仅相对于过度碾压方向发生变化。此外,微带可以延伸穿过马氏体板条边界 [文献5]。
暗蚀区中可见的另一个显著特征是细长铁素体。在滚动接触疲劳过程中,在马氏体基体结构中也形成了细长铁素体,但表现为单独的特征,而不是像铁素体微带那样成组分布。有迹象表明,细长铁素体会生长,在低角度带和高角度带处形成较大的铁素体晶粒 [文献5]。与铁素体微带一样,细长铁素体呈薄板状,在圆周截面上观察时与滚道表面成约 30°或 80°角度(图 5a)。从横截面看时,微带与滚道表面平行。在光学显微镜下观察时,低角度带和高角度带呈白色(见图 3)。正因如此,它们通常被称为白蚀带。其内部结构在厚度上可能非常不均匀。低角度带和高角度带都可以由多晶纳米级尺寸的铁素体和细长铁素体组成 [文献6]。
在大约109次应力循环后 ,白蚀带的出现通常与透镜状碳化物 (LC) 的形成一起被观察到 [文献7]。 透镜状碳化物在侧面形成,并与较大白蚀带平行。生长完成后的白蚀带长度达50-60µm,宽度达10µm,而透镜状碳化物的厚度可以达到1 µm。 透镜状碳化物的形成与残余渗碳体的部分溶解有关,但并不需要残余渗碳体完全溶解[文献4-8]。图 5b显示了白蚀带区域的夹层结构,其中铁素体微带和透镜状碳化物位于初始马氏体基体旁边 [文献9]。
残余渗碳体比回火马氏体基体硬得多,因此被认为具有更高的抗塑性变形能力。然而,观察到细长铁素体和铁素体微带均通过残余渗碳体生长,导致其溶解 [文献3, 10]。经过大量的应力循环后,发现高应力区域残留的渗碳体颗粒往往边缘模糊,表明渗碳体在滚动接触疲劳过程中发生了溶解。
有几个因素会影响或决定滚动接触疲劳的微观结构变化,包括初始结构、残余应力,以及接触压力和温度等运行条件。作为热学和机械过程,微观结构变化的速率随着接触压力或温度的升高而增加。
微观结构改变是由塑性诱导的位错滑移驱动的碳迁移过程,如图6所示。对于马氏体硬化轴承钢,初始组织由含有纳米级析出相(过渡型碳化物)的回火马氏体、残余奥氏体和残余渗碳体组成。白蚀区的形成涉及回火马氏体以铁素体微带和细长铁素体的形式转变为铁素体,这是位错驱动的碳从马氏体基体迁移的结果。
同时,由于应力和应变引起的相变,残余奥氏体部分转变为马氏体,而残余渗碳体在早期完好无损,但在一些局部高度塑性变形的区域逐渐溶解。随着滚动接触疲劳的加重,铁素体微带和细长铁素体晶粒进一步生长为铁素体带,表现为低角度带和高角度带。来自基体的碳原子和溶解的碳化物偏聚在铁素体带之间,形成透镜状碳化物。
关于在暗蚀区形成阶段碳原子迁移到哪里存在争议。具体问题是马氏体内部的碳原子是否被转移到过渡型碳化物 [文献9],导致所谓的碳化物粗化,或者转移到其他地方,例如新形成的铁素体微带或细长铁素体晶粒的边界 [文献11]。
滚动接触下低温回火马氏体的疲劳损伤伴随着残余奥氏体的分解和残余压缩应力的积累,这可以通过X射线衍射进行系统研究 [文献12-14]。尽管在应力辅助下从残余奥氏体到马氏体的转变从一开始就发生,并在滚动接触疲劳过程中持续进行,但这样的过程被发现与暗蚀区的形成和白蚀带的后续生长相关 [文献12, 13]。在足够多的应力循环次数之后,残余奥氏体可以在高应力区域发生完全分解。
微观结构的退化也能从硬度的变化中体现出来。研究发现,改变后结构的平均硬度明显低于初始结构的平均硬度 [文献9, 13, 15]。还观察到,在经过大量应力循环后,硬度最初略有增加,随后退化微观结构的硬度明显降低 [文献10, 16]。 硬度的初始增加是加工硬化的结果。随着滚动接触疲劳的加重,位错驱动的碳迁移导致越来越不均匀的退化微观结构,其特征是贫碳区与富碳区混合。马氏体基体中的碳耗尽导致退化微观结构的硬度逐渐降低。
结语
滚动轴承失效本质上是轴承在给定运行条件下发生材料退化的结果。了解材料退化机制是预测轴承性能的基础,以便为特定应用选择最佳的钢材和热处理工艺,并预测轴承的剩余寿命。轴承寿命预测有利于验证轴承的选型,揭示轴承运行或维护中可能发生的变化,进而延长设备中后续轴承运行的寿命。