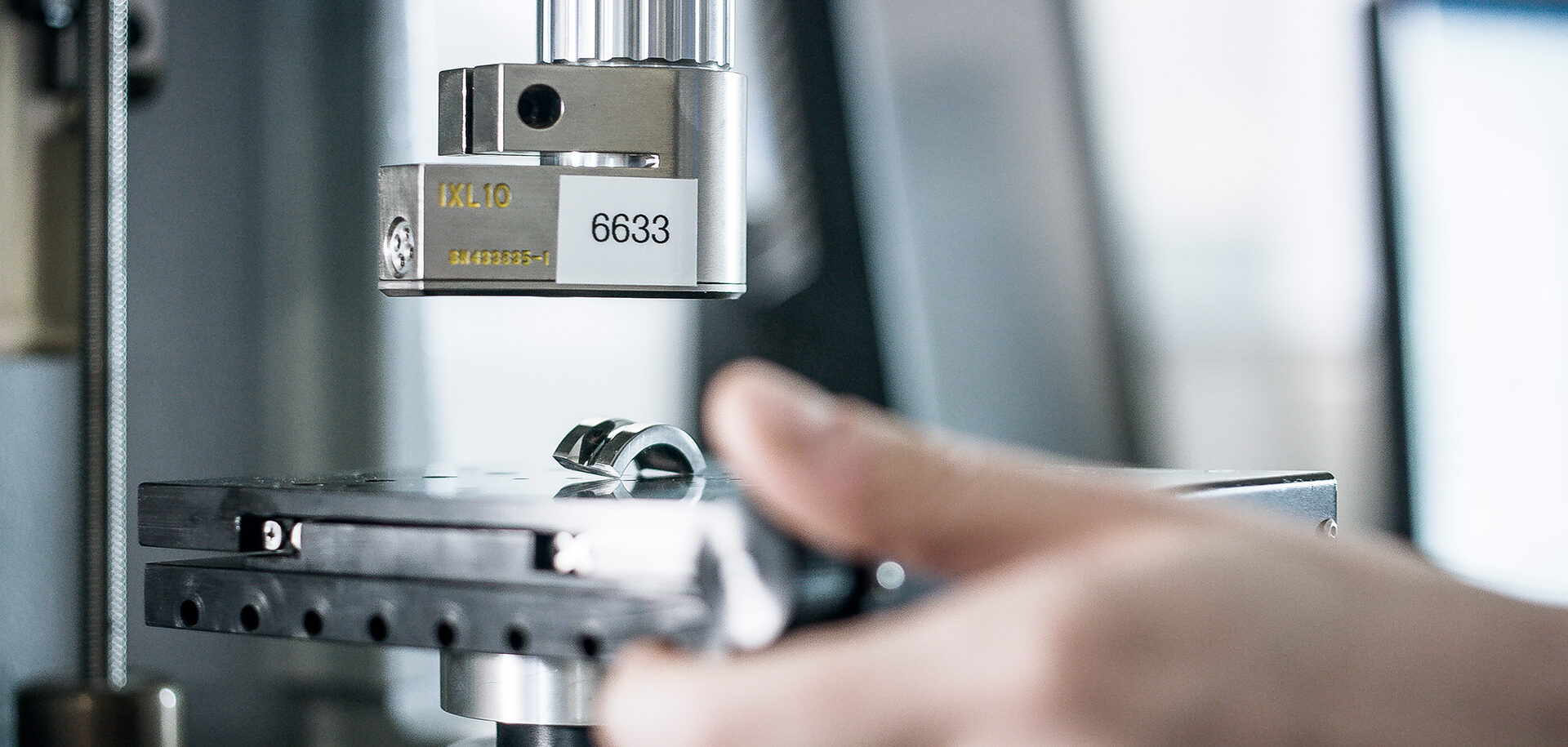
Altération microstructurelle des aciers pour roulements dans la fatigue de contact roulant
La dégradation du matériau constitue la principale cause de défaillance des roulements. La meilleure approche de la prédiction de ces défaillances repose ainsi sur l’acquisition d’une compréhension approfondie de la dégradation du matériau qui permet de sélectionner l’acier et les traitements thermiques les plus appropriés pour une application donnée. Outre les performances des roulements, cette compréhension permet également de prédire de façon plus précise leur durée de vie restante.
Un contact roulant sur les pistes d’un roulement génère des contraintes cycliques qui se propagent de la surface vers la sous-couche. En cas de contrainte supérieure à la limite de contrainte locale du matériau, des dommages ou une dégradation de la microstructure se développent, évoluant vers un écaillage de la surface des pistes par fatigue de contact roulant (FCR).
Dans des conditions de lubrification médiocres (rapport de viscosité κ < 1), une contrainte en surface élevée peut découler d’un contact métal sur métal au niveau d’aspérités. La traction en surface induite par des glissements même minimes dans les contacts est également susceptible d’entraîner une contrainte en surface élevée. Cette contrainte élevée peut être à l’origine de dommages par fatigue en surface, qui se manifestent souvent par un micro-écaillage ou un micropitting.
Dans les roulements fonctionnant dans des conditions de lubrification satisfaisantes (κ > 2), la contrainte de cisaillement maximale se situe à une certaine profondeur sous la surface des pistes. La contrainte de cisaillement cyclique due au contact roulant peut, à la longue, causer des dommages par fatigue conduisant à un écaillage des pistes initié sous la surface (Fig. 1). Dans des conditions de FCR, deux types de dégradations du matériau peuvent se produire. En cas de contrainte de contact supérieure à une certaine limite, dite d’accommodation élastique, le matériau dans une région donnée sous la surface subit un écoulement plastique progressif qui entraîne une altération progressive de la microstructure conduisant à un écaillage des pistes. Même si la contrainte est inférieure à la limite d’accommodation élastique, des dommages localisés peuvent également se développer (en fonction des conditions de contraintes locales), à partir d’imperfections du matériau telles que des inclusions non métalliques, sous l’effet de l’augmentation de la contrainte. Ce type de dommage se présente sous forme d’ailes de papillon, avec des fissures simples ou multiples initiées au niveau d’une inclusion ou d’un pore. La propagation des fissures s’accompagne de l’apparition de zones de phase blanche (WEA). Dans certaines conditions, la propagation d’une fissure sous la surface peut également causer un écaillage de la surface des pistes.
Les dommages par fatigue localisés résultant d’imperfections du matériau dans les aciers pour roulements ont fait l’objet d’un précédent article [1]. Ces types de dommages par fatigue concernent particulièrement les roulements à rouleaux de moyennes et grandes dimensions. Basé sur un article publié récemment par les auteurs [2], le présent article dresse la synthèse des études disponibles dans la littérature sur l’altération microstructurelle des aciers pour roulements, autrement dit l’endommagement du matériau de base par FCR. Ce type de dégradation du matériau concerne particulièrement les roulements de petites et moyennes dimensions soumis à des pressions de contact relativement élevées.
Microstructure des aciers pour roulements
Le carbone et le chrome sont des éléments d’alliage de base des aciers pour roulements qui sont utilisés pour obtenir la dureté requise par traitement thermique. Des éléments d’alliage supplémentaires sont nécessaires pour accroître la trempabilité des aciers pour les éléments de roulement de grandes dimensions.
Les composants de roulement trempés à cœur sont normalement soumis à des traitements thermiques de manière à obtenir une structure martensitique ou bainitique. Le présent article se penche sur la structure martensitique des aciers pour roulements.
Le durcissement martensitique consiste en une austénitisation, suivie d’une trempe de refroidissement en bain d’huile ou de sel, puis un revenu à basse température afin d’équilibrer des propriétés en conflit. Au cours de l’austénitisation, une partie de la cémentite sphéroïdale se dissout, ce qui se traduit par une teneur en carbone de l’austénite de 0,6-0,65 % en poids. Lors de la trempe de refroidissement, la martensite se forme avec une fraction d’austénite retenue. Le revenu suivant entraîne la précipitation des carbures de transition et une nouvelle transformation de l’austénite retenue (AR) en martensite. La teneur en AR s’en trouve ainsi réduite. Elle diminue avec la température de revenu et peut devenir nulle si la température de revenu atteint 220 °C. La Figure 2 fournit une représentation schématique de la structure martensitique après traitement thermique. À l’intérieur d’un ancien grain austénitique se trouvent des paquets de martensite, de la cémentite résiduelle et de l’AR. Chaque paquet contient des blocs dans lesquels se sont formées des lattes de martensite. Les carbures de transition précipitent à l’intérieur des sous-grains de martensite pendant le revenu.
Réponse du matériau à la FCR
En cas de pression de contact supérieure à la limite d’accommodation élastique, l’acier dans la région sous la surface subit une altération microstructurelle progressive en raison de l’accumulation de microplasticité. Un tel processus de dégradation se manifeste par l’apparition d’une région sombre (DER) observable sous microscopie optique légère (MOL). Au fil de la progression de la FCR, des bandes de phase blanche (WEB) se développent à l’intérieur de la région sombre selon deux orientations distinctes. La formation de bandes faiblement inclinées (LAB), orientées à environ 30° par rapport au sens de roulement, est suivie par l’apparition de bandes fortement inclinées (HAB), orientées à environ 80° par rapport au sens de roulement. La Figure 3 montre une micrographie de l’altération microstructurelle sous la surface.
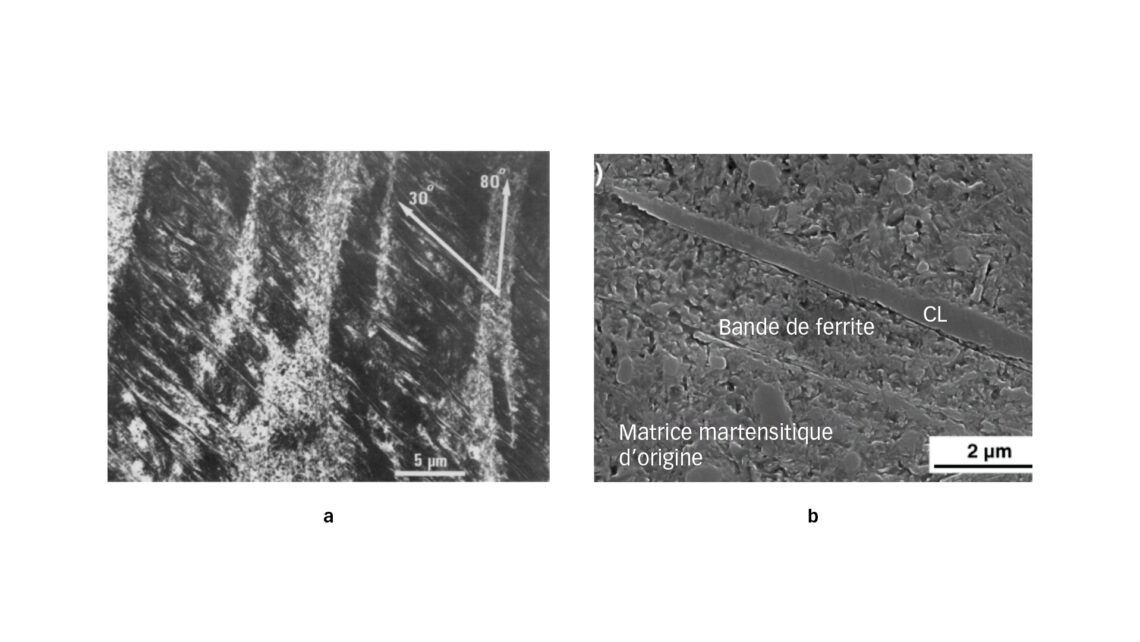
La caractérisation de la région sombre avec la microscopie électronique à transmission (MET) révèle que des microbandes de ferrite [3, 4] se sont formées dans la matrice martensitique (Fig. 4). Sur la vue en coupe circonférentielle, les microbandes apparaissent densément réparties ou regroupées. Dans chaque groupe, les microbandes présentent la même orientation, qui peut différer de celles des autres groupes. En coupe transversale (section d’une bague), cependant, les microbandes apparaissent parallèles à la surface des pistes. Il ressort de ces observations que les microbandes sont de fines plaques dont l’orientation ne varie que par rapport au sens de roulement. En outre, les microbandes peuvent s’étendre au-delà des limites de la plaque martensitique [5].
Une autre caractéristique importante observable dans la région sombre est la ferrite allongée. De la ferrite allongée se forme également dans la structure de la matrice martensitique sous l’action de la FCR, mais apparaît comme des caractéristiques individuelles sans regroupement, contrairement aux microbandes de ferrite. Il a été constaté que la ferrite allongée évolue vers la formation de gros grains présents dans les bandes LAB et HAB [5]. Comme les microbandes de ferrite, la ferrite allongée, observée en coupe circonférentielle, se présente sous forme de plaque mince orientée à 30° ou 80° par rapport à la surface des pistes (Fig. 5a). En coupe transversale, les bandes sont parallèles à la surface des pistes. Les bandes LAB et HAB ont un aspect blanc au microscope optique (voir Fig. 3), d’où leur appellation courante de bandes de phase blanche. Leur structure interne peut être très hétérogène sur l’épaisseur. Les bandes LAB comme HAB peuvent être constituées de ferrite polycristalline de taille nanométrique et de ferrite allongée [6].
L’apparition des bandes WEB après environ 109 cycles de contraintes s’accompagne généralement de la formation de carbures lenticulaires (CL) [7]. Les carbures lenticulaires se forment sur le côté et parallèlement aux grandes bandes WEB. Une bande WEB entièrement développée peut être longue de 50 à 60 µm et large de 10 µm, tandis que l’épaisseur d’un carbure lenticulaire peut atteindre 1 µm. La formation de carbures lenticulaires est liée à la dissolution partielle de la cémentite résiduelle mais ne nécessite pas sa dissolution complète [4–8]. La Figure 5b montre une structure sandwich dans la région des bandes WEB avec une bande de ferrite et un carbure lenticulaire alternant avec la matrice martensitique d’origine [9].
La cémentite résiduelle est beaucoup plus dure que la matrice martensitique trempée et l’on considère, par conséquent, que sa résistance à la déformation plastique est plus élevée. On observe cependant que la ferrite allongée et les microbandes de ferrite se développent à travers la cémentite résiduelle, entraînant sa dissolution [3, 10]. Après un grand nombre de cycles de contraintes, les particules de cémentite résiduelle dans la région soumise à de fortes contraintes présentent souvent des bords flous, ce qui indique que la cémentite se dissout pendant le processus de FCR.
L’altération microstructurelle par FCR est déterminée par plusieurs facteurs, parmi lesquels figurent la structure initiale, les contraintes résiduelles et les conditions de fonctionnement, comme la pression de contact et la température. S’agissant d’un processus thermomécanique, le taux d’altération microstructurelle augmente avec la pression de contact et/ou la température.
L’altération microstructurelle est un processus de migration du carbone dû au glissement de dislocations induit par la plasticité. Il est résumé par la Figure 6. Pour les aciers pour roulements martensitiques, la structure initiale est constituée de martensite trempée contenant des précipités nanométriques (carbures de transition), de l’austénite retenue (AR) et de la cémentite résiduelle. La formation de régions sombres implique la transformation de la martensite trempée en ferrite, sous forme de microbandes de ferrite et de ferrite allongée, due à la migration du carbone de la matrice martensitique par dislocation. Parallèlement, l’AR se transforme partiellement en martensite, sous l’effet des transformations de phase induites par les contraintes et déformations, tandis que la cémentite résiduelle reste intacte dans un premier temps, avant de subir une dissolution progressive dans certaines régions de plasticité hautement localisée. À mesure que la FCR progresse, les microbandes de ferrite et les grains de ferrite allongés poursuivent leur développement pour former des bandes de ferrite de deux types : faiblement inclinées (LAB) et fortement inclinées (HAB). Les atomes de carbone de la matrice et les carbures dissous sont séparés pour former des carbures lenticulaires entre les bandes de ferrite.
La destination vers laquelle les atomes de carbone migrent au stade de la formation de régions sombres fait débat. La question précise est de savoir si les atomes de carbone à l’intérieur de la martensite sont transportés vers les carbures de transition [9], provoquant ledit grossissement des carbures, ou vers un autre endroit comme les limites des microbandes de ferrite ou des grains de ferrite allongés nouvellement formés [11].
L’endommagement par fatigue sous contact roulant de la martensite trempée à basse température s’accompagne d’une décomposition de l’AR et d’une accumulation de contraintes résiduelles compressives, ce qui peut être étudié de façon systématique au moyen de la technologie de diffraction des rayons X [12–14]. Bien que la transformation martensitique de l’AR, favorisée par les contraintes, se produise dès le début et se poursuive avec le processus de FCR, ce processus est corrélé avec la formation de régions sombres et le développement consécutif des bandes WEB [12, 13]. À partir d’un certain nombre de cycles de contraintes, une décomposition complète de l’AR peut se produire dans la région soumise à de fortes contraintes.
La décomposition microstructurelle se traduit également par un changement de dureté. Il a été montré que la dureté moyenne de la structure altérée est nettement inférieure à celle de la structure initiale [9, 13, 15]. Il a également été observé qu’une légère augmentation initiale de la dureté est suivie d’une diminution significative de la dureté de la microstructure décomposée après un grand nombre de cycles de contraintes [10, 16]. Cette augmentation initiale de la dureté résulte de l’écrouissage. À mesure que la FCR progresse, la migration du carbone induite par la dislocation produit une microstructure décomposée de moins en moins homogénéisée, caractérisée par des régions appauvries en carbone et d’autres, enrichies en carbone. L’appauvrissement en carbone de la matrice martensitique provoque une diminution progressive de la dureté de la microstructure décomposée.
Remarques de conclusion
La défaillance d’un roulement résulte essentiellement de la dégradation du matériau dans des conditions de fonctionnement données. La compréhension de cette dégradation du matériau est essentielle pour pouvoir prédire les performances des roulements. Elle permet de sélectionner les aciers et les traitements thermiques les mieux adaptés aux applications spécifiques et de prédire la durée de vie restante des roulements. Ce pronostic peut être utile pour valider la sélection d’un roulement ou recommander d’éventuels changements dans l’utilisation ou l’entretien des roulements afin de prolonger la durée de vie des prochains roulements montés sur l’équipement.