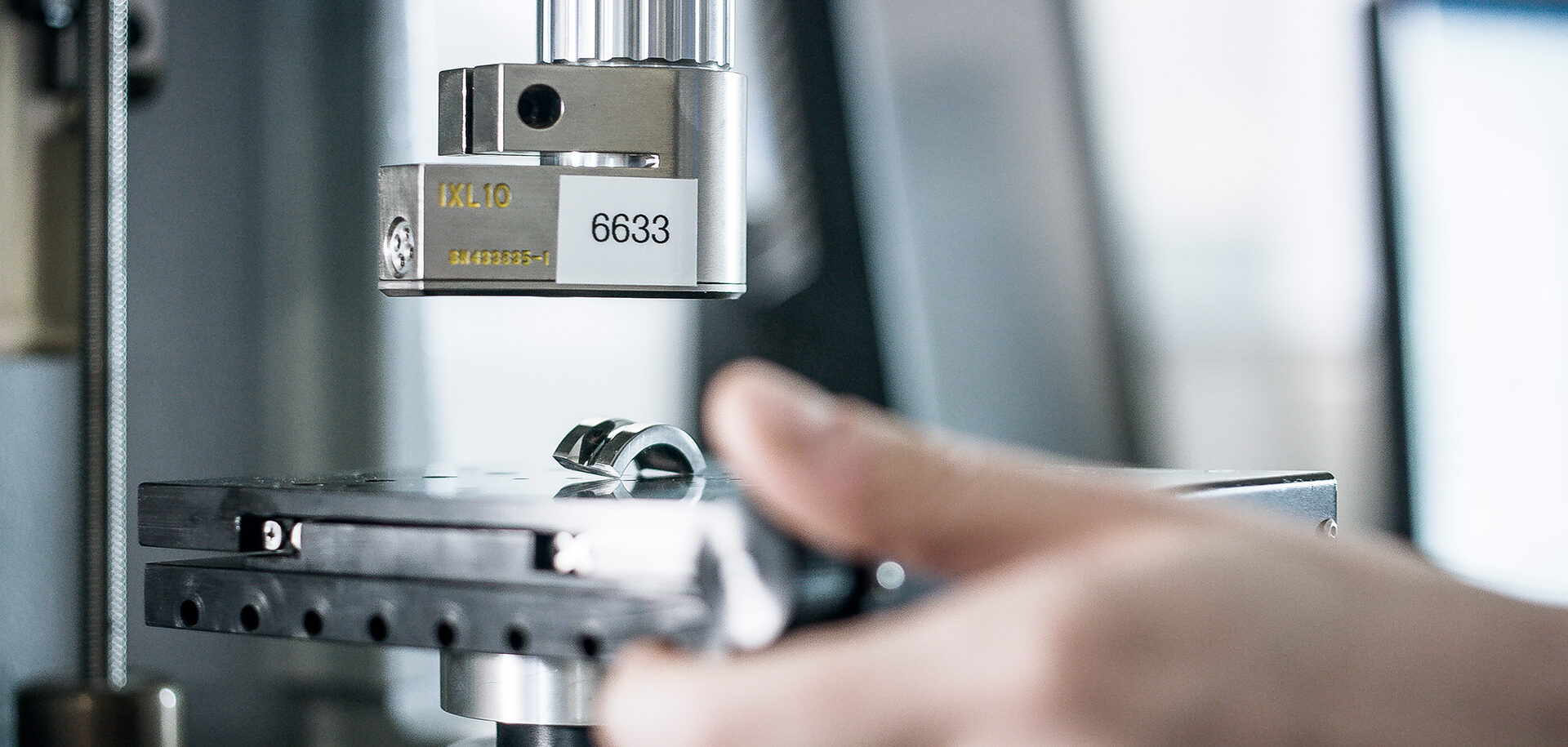
Alteración microestructural de los aceros de rodamientos por fatiga por contacto rodante
La degradación del material es la principal causa de fallas en los rodamientos. La mejor manera de predecir las fallas es tener unos profundos conocimientos de la degradación del material. Entonces se puede predecir el rendimiento de los rodamientos seleccionando el acero y los tratamientos térmicos óptimos para cada aplicación específica. Esos conocimientos también proporcionan predicciones más exactas de la vida útil restante del rodamiento.
El contacto rodante en los caminos de rodadura de un rodamiento genera tensiones cíclicas que se extienden de la superficie a las zonas subsuperficiales. Si la tensión supera el límite de resistencia local del material, se producirán daños o degradación de la microestructura, lo que conducirá gradualmente al desconchado de la superficie del camino de rodadura como resultado de fatiga por contacto rodante (RCF).
En condiciones de lubricación deficientes (relación de viscosidad, κ<1), el contacto entre metales de las asperezas puede generar tensiones altas en la superficie. La tracción, inducida en la superficie por pequeños deslizamientos en los puntos de contacto, también puede generar tensiones altas. Estas tensiones en la superficie pueden causar daños por fatiga, lo que se manifiesta frecuentemente como microdesconchado o picaduras.
En los rodamientos que trabajan en buenas condiciones de lubricación (κ>2), la máxima tensión de corte existe a una cierta profundidad debajo de la superficie del camino de rodadura. La tensión de corte cíclica producida por el contacto rodante puede causar gradualmente daños por fatiga que lleven a un desconchado del camino de rodadura iniciado en la subsuperficie (fig. 1). En condiciones de fatiga por contacto rodante (RCF), pueden producirse dos tipos de degradación del material. Si la tensión por contacto máxima excede de un cierto límite, conocido como límite de prueba elástica (elastic shakedown limit), el material de una zona de la subsuperficie sufre una deformación plástica progresiva que comporta la alteración paulatina de la microestructura, que conduce gradualmente al desconchado de los caminos de rodadura. Sin embargo, con una tensión de contacto inferior al límite de prueba elástica, el daño localizado (según las condiciones de tensión locales) puede desarrollarse, a pesar de todo, por imperfecciones en el material, como inclusiones no metálicas, debido al efecto de aumento de tensiones. Este tipo de daños se caracteriza por lo que se denomina mariposa, con grietas individuales o múltiples iniciadas por una inclusión o un poro. El crecimiento de las grietas va acompañado del desarrollo de zonas blancas de corrosión ácida (WEA). En ciertas condiciones, el crecimiento de una grieta subsuperficial también puede conducir al desconchado de la superficie del camino de rodadura.
Los daños por fatiga localizados producidos en los aceros de rodamientos por imperfecciones en el material se han tratado en un artículo anterior [1]; estos tipos de daño por fatiga son especialmente relevantes en rodamientos de tamaño mediano y grande. Partiendo de un trabajo publicado recientemente por los autores [2], el presente artículo pretende resumir los estudios publicados en la bibliografía sobre la alteración microestructural de los aceros de rodamientos, es decir, la degradación del material interior por RCF. Este último tipo de degradación del material es sobre todo importante en los rodamientos de tamaño pequeño y mediano que funcionen bajo presiones de contacto relativamente altas.
Microestructura de los aceros de rodamientos
El carbono y el cromo son elementos de aleación básicos en los aceros de rodamientos, y se usan para obtener la dureza requerida mediante tratamiento térmico. Para aumentar la templabilidad de los aceros para componentes de rodamiento de gran tamaño, se precisan elementos de aleación adicionales.
Normalmente los componentes de rodamiento sometidos a templado total reciben tratamiento térmico para producir una estructura martensítica o bainítica. El presente artículo se concentra en la estructura martensítica de los aceros de rodamientos.
El templado martensítico implica austenitización, seguida por enfriamiento en baño de aceite o sal, y luego revenido a baja temperatura para equilibrar propiedades conflictivas. Durante la austenitización, se disuelve una fracción de la cementita esferoidal, lo que genera en la austenita un contenido en peso de carbono del 0,60 al 0,65 %. Al enfriarse, se forma martensita con una fracción de la austenita retenida. El revenido subsiguiente origina la precipitación de carburos de transición y la ulterior transformación de la austenita retenida (RA) en martensita, que ocasiona una reducción del contenido de RA. El contenido de RA se reduce con la temperatura de revenido y puede disminuir a cero si llega a los 220 °C. La fig. 2 muestra una representación esquemática de la estructura martensítica después del tratamiento térmico. Dentro de un grano previo de austenita, hay paquetes de martensita, cementita residual y RA. Cada paquete contiene bloques en los que se forman listones de martensita. Durante el revenido, los carburos de transición se precipitan dentro de los subgranos de martensita.
Respuesta del material a la RCF
Si la presión de contacto máxima excede del límite de prueba elástica, el acero de rodamientos en la región subsuperficial sufre una alteración progresiva de la microestructura como resultado de la acumulación de microplasticidad. Este proceso de degradación se manifiesta bajo microscopía óptica por luz (LOM) en forma de una región de corrosión oscura (DER). El progreso de la RCF hace que, dentro de la DER, se desarrollen bandas de corrosión blanca (WEB) con dos orientaciones diferenciadas. La formación de las bandas de ángulo pequeño (LAB) con una orientación de unos 30° respecto de la dirección de rodadura va seguida del desarrollo de las bandas de gran ángulo (HAB), que están orientadas con un ángulo de unos 80° respecto de la dirección de rodadura. La fig. 3 muestra un micrográfico de la alteración microestructural de la subsuperficie.
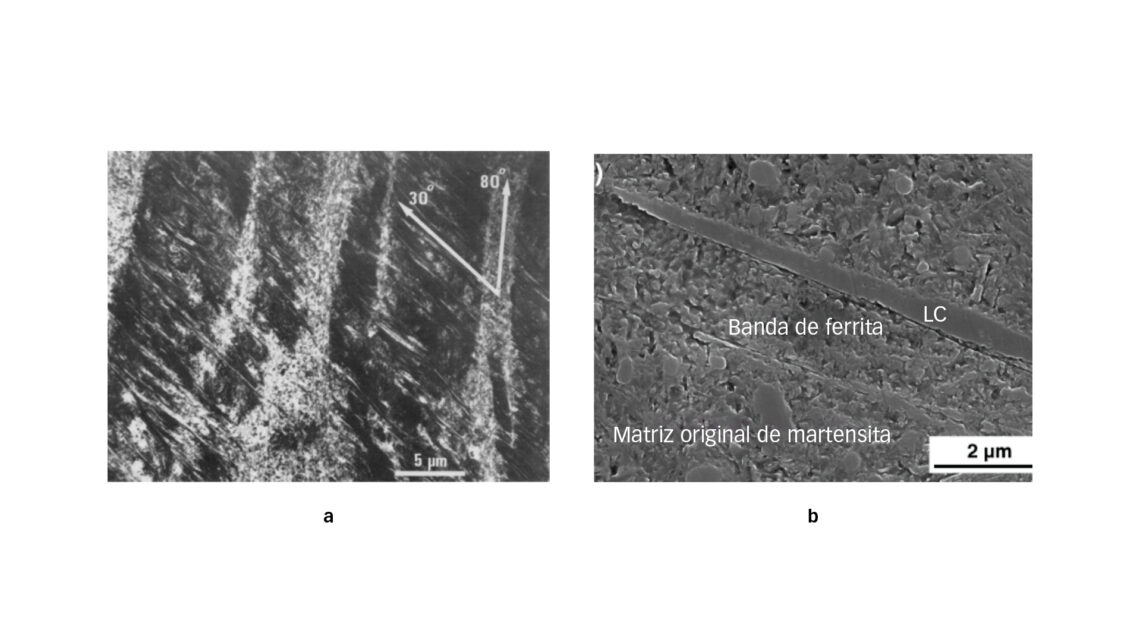
Otra característica prominente visible en las DER es la ferrita alargada. También se forma ferrita alargada en la estructura de la matriz martensítica durante la RCF, pero aparece como característica individual y no se agrupa como las microbandas de ferrita. Hay una indicación de que la ferrita alargada se desarrolla para formar granos de ferrita grandes presentes en las LAB y HAB [5]. Al igual que las microbandas de ferrita, la ferrita alargada es en forma de placas finas y está orientada unos 30° u 80° respecto de la superficie del camino de rodadura cuando se observa en la sección circunferencial (fig. 5a). Cuando se observa en la sección transversal, las bandas son paralelas a la superficie del camino de rodadura. Las LAB y HAB aparecen blancas cuando se observan en el microscopio óptico (ver la fig. 3). Es por ello que, comúnmente, se denominan bandas de corrosión blanca (WEB). Su estructura interna puede ser muy heterogénea a lo largo del espesor. Tanto las LAB como las HAB pueden estar formadas por ferrita policristalina de tamaño nanométrico y ferrita alargada [6].
El aspecto de las WEB tras unos 109 ciclos de tensión se observa, por lo general, junto con la formación de carburos lenticulares (LC) [7]. Se forman carburos lenticulares al lado y en paralelo a las WEB grandes. Una WEB plenamente desarrollada puede tener entre 50 y 60 µm de longitud y 10 µm de ancho, mientras que el espesor de un carburo lenticular puede llegar a 1 µm. La formación de carburos lenticulares está relacionada con la disolución parcial de cementita residual, pero no requiere su completa disolución [4–8]. La fig. 5b muestra una estructura sándwich en la región de WEB donde una banda de ferrita y carburo lenticular están junto a la matriz martensítica original [9].
La cementita residual es mucho más dura que la matriz martensítica revenida y, por ello, se cree que su resistencia a la deformación plástica es mayor. No obstante, se observa que tanto la ferrita alargada como las microbandas de ferrita aumentan a través de la cementita residual, lo que hace que se disuelva [3, 10]. Después de una gran cantidad de ciclos de tensión, se observa que las partículas de cementita residual en la región de tensiones muy altas frecuentemente tienen bordes borrosos, lo que sugiere que se disuelve durante el proceso de RCF.
Hay varios factores que influyen o dominan la alteración microestructural en la RCF, incluidas la estructura inicial, las tensiones residuales y las condiciones de funcionamiento, como la presión de contacto y la temperatura. Como un proceso termomecánico, el ritmo de alteración microestructural aumenta con la presión de contacto y/o la temperatura.
Esta alteración es un proceso de migración del carbono impulsado por desplazamiento de dislocación inducido por la plasticidad, que se resume en la fig. 6. En los aceros de rodamientos con templado martensítico, la estructura inicial consta de martensita revenida que contiene precipitados de tamaño nanométrico (carburos de transición), austenita retenida (RA) y cementita residual. La formación de DER implica la transformación de la martensita revenida en ferrita, en forma de microbandas de ferrita y ferrita alargada, como resultado de la migración del carbono impulsada por la dislocación de la matriz martensítica. Mientras, la RA se transforma parcialmente en martensita como resultado de transformaciones de fase inducidas por tensión y deformación, mientras que la cementita residual está intacta en la etapa inicial pero se disuelve gradualmente en algunas regiones de plasticidad altamente localizada. Con la progresión de la RCF, las microbandas de ferrita y los granos de ferrita alargados continúan desarrollándose en bandas de ferrita, que se visualizan como bandas de ángulo pequeño (LAB) y de gran ángulo (HAB). Los átomos de carbono de la matriz y los carburos disueltos se segregan para formar carburos lenticulares entre las bandas de ferrita.
Existe una controversia sobre dónde migran los átomos de carbono en la etapa de formación de la DER. La cuestión específica es si los átomos de carbono dentro de la martensita se transportan hacia los carburos de transición [9], causando lo que se denomina engrosamiento del carburo, o a algún otro lugar, como a los límites de las microbandas de ferrita recientemente formadas o granos de ferrita alargada [11].
Los daños por la fatiga de martensita revenida a baja temperatura durante el contacto rodante van acompañados por la descomposición de RA y la formación de tensiones residuales de compresión, que pueden estudiarse sistemáticamente mediante difracción de rayos X [12–14]. Aun cuando la transformación de RA a martensita favorecida por tensiones se produce desde el principio y continúa con el proceso de RCF, se ha comprobado que este proceso tiene correlación con la formación de DER y el subsiguiente desarrollo de las WEB [12, 13]. Después de una cantidad lo suficientemente grande de ciclos de tensión, puede producirse una descomposición completa de la RA en la región altamente afectada.
El deterioro microestructural también queda reflejado por un cambio de dureza. Se ha comprobado que la dureza media de la estructura alterada es sensiblemente inferior a la de la estructura inicial [9, 13, 15]. También se ha observado que el ligero aumento inicial en dureza va seguido por una significativa disminución de esta en la microestructura deteriorada después de una gran cantidad de ciclos de tensión [10, 16]. El aumento inicial de la dureza se produce como resultado del endurecimiento por deformación. Con la progresión de la RCF, la migración del carbono impulsada por dislocación conduce a una microestructura deteriorada cada vez menos homogeneizada, que se caracteriza por regiones desprovistas de carbono mezcladas con otras enriquecidas de carbono. La merma de carbono en la matriz martensítica causa una disminución gradual de la dureza en la microestructura deteriorada.
Observaciones finales
La falla de un rodamiento es, básicamente, el resultado de la degradación del material bajo unas condiciones de funcionamiento determinadas. Comprender la degradación del material es fundamental para predecir el rendimiento de los rodamientos y permitir una selección óptima de los aceros y tratamientos térmicos para aplicaciones específicas, al igual que para pronosticar su vida útil restante. El pronóstico puede ser útil para validar la selección del rodamiento, o indicar posibles cambios en su funcionamiento o mantenimiento, que puedan prolongar la vida útil de posteriores rodamientos en el equipo.