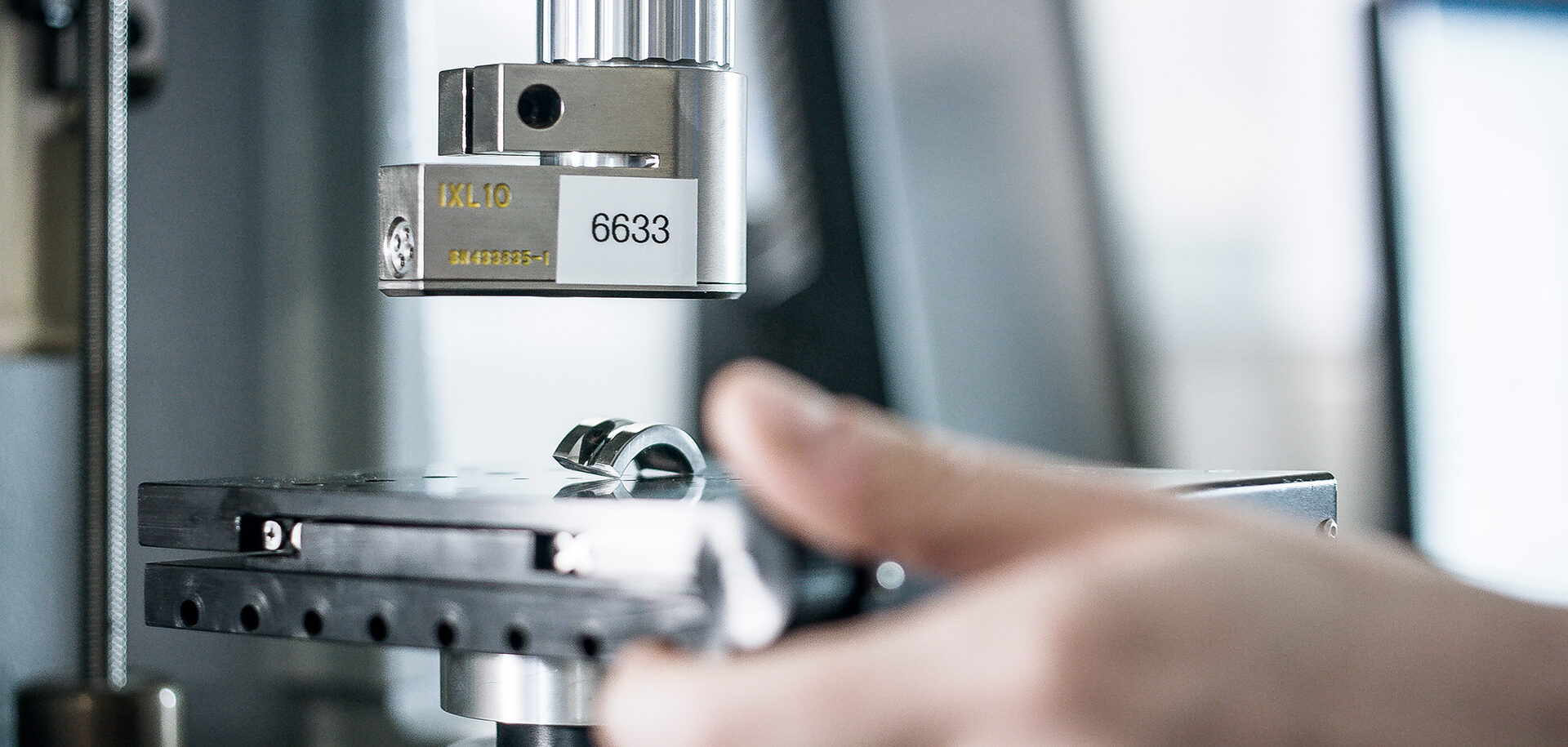
Gefügeänderung von Lagerstahl bei Wälzermüdung
Die Hauptursache für den Ausfall von Wälzlagern ist Materialverschleiß. Um Lagerausfälle möglichst genau prognostizieren zu können, muss man ein gutes Verständnis für Materialschädigungsmechanismen entwickeln, damit man in der Lage ist, die Lagerleistung für bestimmte Anwendungen durch Auswahl des optimalen Lagerstahls und der optimalen Wärmebehandlung vorauszuberechnen. Auch lässt sich die verbleibende Lagerlebensdauer so genauer bestimmen.
Der Wälzkontakt auf den Laufbahnen eines Lagers erzeugt zyklische Spannungen, die sich von der Oberfläche in die darunter liegenden Bereiche ausbreiten. Übersteigen die Spannungen die lokale Festigkeitsgrenze des Werkstoffs, tritt eine Schädigung des Stahlgefüges ein, die schließlich zu Ausbrüchen an der Laufbahnoberfläche infolge von Wälzermüdung (RCF) führen kann.
Unter schlechten Schmierbedingungen (Viskositätsverhältnis, κ < 1) kann der Metall-Metall-Kontakt an den Rauheiten hohe Spannungen an der Oberfläche hervorrufen. Auch auf die Oberfläche einwirkende Belastungen, die schon durch geringes Gleiten im Kontakt entstehen, können hohe Spannungen an der Oberfläche hervorrufen. Diese können zu Oberflächenermüdungsschäden führen, die sich häufig als Mikroausbrüche oder Mikrogrübchen zeigen.
Bei umlaufenden Lagern, die unter guten Schmierbedingungen arbeiten (κ > 2), treten die Höchstschubspannungen in einer bestimmten Tiefe unterhalb der Laufbahnoberfläche auf. Die aus dem Wälzkontakt resultierenden zyklischen Scherspannungen können letztendlich Ermüdungsschäden verursachen, die zu unterhalb der Laufbahnoberfläche beginnenden Ausbrüchen führen (Bild 1). Unter RCF-Bedingungen können zwei Arten von Materialschäden auftreten. Übersteigt die maximale Kontaktspannung einen bestimmten Grenzwert, der als elastische Shakedown-Grenze bezeichnet wird, kommt es unterhalb der Oberfläche zu einem fortschreitenden plastischen Fließen des Materials, das eine fortschreitende Gefügeänderung zur Folge hat, die schließlich zu Laufbahnausbrüchen führt. Bei einer Kontaktspannung unterhalb der elastischen Shakedown-Grenze könnten jedoch immer noch lokale Schäden (je nach den lokalen Spannungsbedingungen) durch Materialfehler wie nichtmetallische Einschlüsse aufgrund des Spannungserhöhungseffekts entstehen. Diese Schadensart ist durch sogenannte Butterflys gekennzeichnet, d. h. strukturelle Änderungen, die Schmetterlingsflügeln ähneln, wobei einzelne oder mehrere Risse von einem Einschluss oder einer Pore ausgehen. Das Risswachstum wird begleitet von der Entstehung weiß anätzender Zonen (White Etching Areas, WEA). Unter bestimmten Bedingungen kann das Wachstum eines unterhalb der Oberfläche liegenden Risses auch zu Ausbrüchen an der Laufbahnoberfläche führen.
Lokale Ermüdungsschäden infolge von Materialfehlern bei Lagerstahl wurden bereits in einem früheren Artikel [1] behandelt; diese Arten von Ermüdungsschäden sind vor allem bei mittelgroßen und großen Wälzlagern relevant. Auf der Grundlage einer kürzlich von den Autoren veröffentlichten Übersichtsarbeit [2] zielt der vorliegende Artikel darauf ab, die in der Literatur veröffentlichten Studien über die Gefügeänderung bei Lagerstahl, d. h. die Materialschädigung durch Wälzermüdung, zusammenzufassen. Diese Art von Materialschädigung ist insbesondere bei kleinen und mittelgroßen Lagern von Bedeutung, die unter relativ hohen Kontaktdrücken betrieben werden.
Das Gefüge von Lagerstahl
Kohlenstoff und Chrom sind die grundlegenden Legierungselemente von Lagerstahl; sie sorgen dafür, dass bei der Wärmebehandlung die erforderliche Härte entsteht. Weitere Legierungselemente werden benötigt, um die Härtbarkeit von Lagerstahl für große Lagerteile zu verbessern.
Durchgehärtete Lagerteile werden normalerweise wärmebehandelt, damit entweder ein martensitisches oder ein bainitisches Gefüge entsteht. Der vorliegende Artikel behandelt das martensitische Gefüge von Lagerstahl.
Beim martensitischen Härten erfolgt eine Austenitisierung, gefolgt von einem Abschrecken in Öl- oder Salzbädern und einem anschließenden Anlassen bei niedrigen Temperaturen, um ausgewogene Eigenschaften zu erzielen. Beim Austenitisieren löst sich ein Teil des kugelförmigen Zementits auf, was zu einem Kohlenstoffgehalt von 0,6-0,65 Gew.-% im Austenit führt. Beim Abschrecken bildet sich Martensit, wobei ein Teil des Austenits erhalten bleibt. Beim anschließenden Anlassen kommt es zur Abscheidung von Übergangscarbiden und zur weiteren Umwandlung des Restaustenits (RA) in Martensit, was zu einer Verringerung des RA-Gehalts führt. Der RA-Gehalt nimmt mit der Anlasstemperatur ab und kann auf null sinken, wenn die Anlasstemperatur 220 °C erreicht. Bild 2 zeigt eine schematische Darstellung des martensitischen Gefüges nach der Wärmebehandlung. In einem ehemaligen Austenitkorn befinden sich nun Martensitpakete, Restzementit und Restaustenit. Jedes Paket enthält Blöcke, in denen sich Martensitlanzetten gebildet haben. Beim Anlassen kommt es zur Abscheidung von Übergangscarbiden in den Martensit-Unterkörnern.
Werkstoffreaktion auf Wälzermüdung
Übersteigt der maximale Kontaktdruck die elastische Shakedown-Grenze, so kommt es infolge der zunehmenden Mikroplastizität zu einer fortschreitenden Gefügeänderung des Lagerstahls im Bereich unterhalb der Oberfläche. Ein solcher Schädigungsprozess zeigt sich unter dem Lichtmikroskop in Form einer dunkel anätzenden Zone (Dark Etching Region, DER). Bei fortschreitender Wälzermüdung entwickeln sich in diesen DER-Zonen weiß anätzende Streifen (White Etching Bands, WEB) mit zwei unterschiedlichen Ausrichtungen. Auf die Bildung der „Low-Angle Bands“ (LAB) mit einer Ausrichtung von etwa 30º zur Bewegungsrichtung folgt die Entwicklung der „High-Angle Bands“ (HAB) in einem Winkel von etwa 80º zur Bewegungsrichtung. Bild 3 zeigt eine mikroskopische Aufnahme der Gefügeänderung unterhalb der Oberfläche.
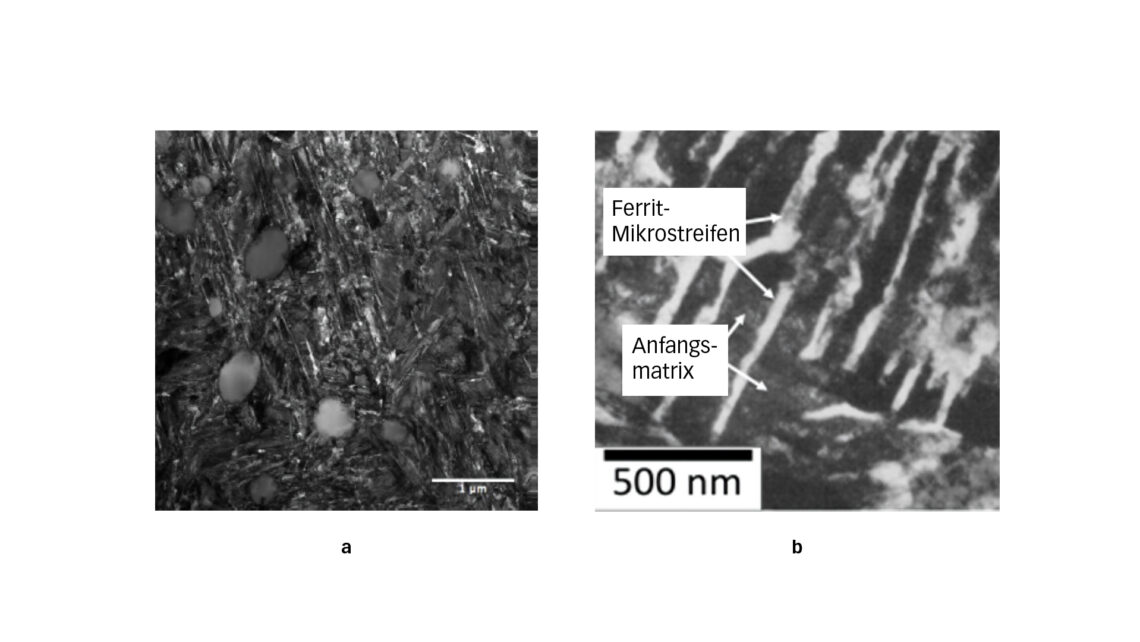
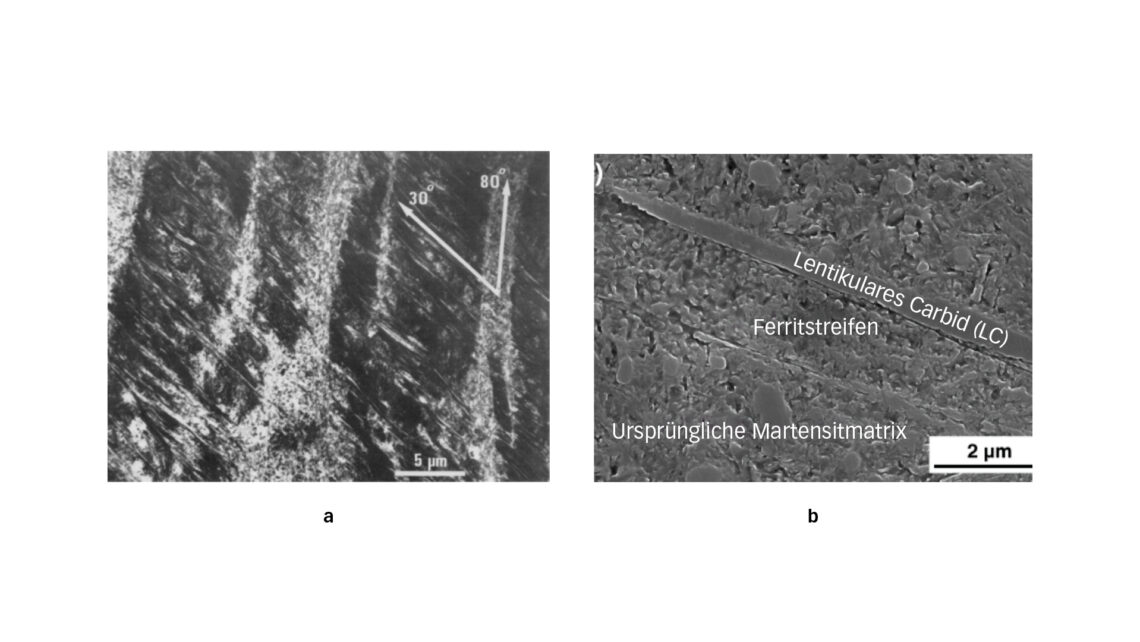
Bei der Charakterisierung der DER-Zonen mithilfe eines Transmissionselektronenmikroskops (TEM) zeigt es sich, dass sich Ferrit-Mikrostreifen [3, 4] innerhalb der Martensitmatrix bilden (Bild 4). Im Umfangsschnitt betrachtet, liegen die Mikrostreifen dicht beieinander oder sind in Clustern angeordnet. Die Mikrostreifen in jedem Cluster sind gleich ausgerichtet, können aber eine andere Ausrichtung haben als die in anderen Clustern. Im Querschnitt (Ringquerschnitt) dagegen sieht es so aus, als ob die Mikrostreifen parallel zur Laufbahnoberfläche verlaufen. Diese Beobachtungen lassen darauf schließen, dass es sich bei den Mikrostreifen um dünne Platten handelt, deren Ausrichtung sich nur in Bezug auf die Bewegungsrichtung ändert. Darüber hinaus können sich die Mikrostreifen über Martensitplattengrenzen hinweg erstrecken [5].
Ein weiteres auffälliges Merkmal der DER-Zonen ist der längliche Ferrit. Dieser bildet sich auch bei Wälzermüdung im martensitischen Matrixgefüge, erscheint aber in Form von Einzelmerkmalen und nicht in Clustern wie die Ferrit-Mikrostreifen. Es gibt Anzeichen dafür, dass der längliche Ferrit zu großen Ferritkörnern heranwächst, die in den LAB und HAB zu finden sind [5]. Im Umfangsschnitt betrachtet (Bild 5a), ist auch der längliche Ferrit wie die Ferrit-Mikrostreifen in Form von dünnen Platten in einem Winkel von etwa 30° oder 80° zur Laufbahnoberfläche angeordnet. Im Querschnitt betrachtet, verlaufen die Streifen parallel zur Laufbahnoberfläche. Unter dem Mikroskop erscheinen die LAB und HAB weiß (siehe Bild 3). Daher werden sie gewöhnlich als weiß anätzende Streifen (WEB) bezeichnet. Deren innere Struktur kann über die Materialdicke hinweg sehr heterogen sein. Sowohl LAB als auch HAB können aus polykristallinem Nano-Ferrit und länglichem Ferrit bestehen [6].
Wenn sich nach etwa 109 Belastungszyklen WEB zeigen, so bilden sich typischerweise auch lentikulare Carbide (LC) [7] seitlich und parallel zu den großen WEB. Ein voll entwickelter WEB kann 50-60 µm lang und 10 µm breit sein, während ein lentikulares Carbid bis zu 1 µm dick sein kann. Die Bildung lentikularer Carbide hängt mit der teilweisen Auflösung des Restzementits zusammen, erfordert jedoch nicht die vollständige Auflösung des Restzementits [4-8]. Bild 5b zeigt eine Sandwich-Struktur in der WEB-Zone, wo ein Ferritstreifen und ein lentikulares Carbid neben der ursprünglichen Martensitmatrix liegen [9].
Der Restzementit ist viel härter als die angelassene Martensitmatrix und hat daher vermutlich eine höhere Beständigkeit gegen plastische Verformung. Allerdings ist zu beobachten, dass sich sowohl der längliche Ferrit als auch die Ferrit-Mikrostreifen durch den Restzementit hindurch ausbreiten und ihn dabei auflösen [3, 10]. Nach einer hohen Anzahl an Belastungszyklen weisen die Restzementit-Teilchen im hochbelasteten Bereich oft unscharfe Ränder auf, was darauf hindeutet, dass sich der Zementit im Laufe des Wälzermüdungsprozesses auflöst.
Es gibt mehrere Faktoren, die die Gefügeänderung bei Wälzermüdung beeinflussen oder bestimmen, darunter das Anfangsgefüge, die Eigenspannungen und die Betriebsbedingungen, wie Kontaktdruck und Temperatur. Da es hierbei um einen thermisch-mechanischen Prozess geht, nimmt die Geschwindigkeit der Gefügeänderung mit dem Kontaktdruck und/oder der Temperatur zu.
Bei der Gefügeänderung handelt es sich um einen Prozess der Kohlenstoffwanderung, der durch plastizitätsinduziertes Verschiebungsgleiten vorangetrieben wird und in Bild 6 zusammengefasst dargestellt ist. Bei Lagerstahl mit martensitischer Härtung besteht das Ausgangsgefüge aus angelassenem Martensit mit Abscheidungen im Nanobereich (Übergangscarbide), Restaustenit (RA) und Restzementit. Die Bildung von DER-Zonen geht einher mit der Umwandlung von angelassenem Martensit in Ferrit in Form von Ferrit-Mikrostreifen und länglichem Ferrit, die aufgrund der Kohlenstoffwanderung aus der Martensitmatrix infolge des Verschiebungsgleitens erfolgt. In der Zwischenzeit wird RA durch spannungs- und dehnungsinduzierte Phasenumwandlungen teilweise in Martensit umgewandelt, während der Restzementit in der Anfangsphase noch intakt ist, sich aber in einigen Bereichen mit stark lokalisierter Plastizität langsam auflöst. Bei fortschreitender Wälzermüdung entwickeln sich die Ferrit-Mikrostreifen und die länglichen Ferritkörner weiter zu Ferritstreifen, die als „Low Angle Bands“ (LAB) und „High Angle Bands“ (HAB) sichtbar werden. Die Kohlenstoffatome aus der Matrix und die aufgelösten Carbide werden getrennt und bilden lentikulare Carbide zwischen den Ferritstreifen.
Es ist umstritten, wohin die Kohlenstoffatome in der Entstehungsphase der DER abwandern. Die konkrete Frage ist, ob die Kohlenstoffatome im Martensit zu den Übergangscarbiden [9] transportiert werden, was die so genannte Carbidvergröberung verursacht, oder an andere Stellen, wie beispielsweise an die Grenzen der neu gebildeten Ferrit-Mikrostreifen oder länglichen Ferritkörner [11].
Der Ermüdungsschaden von bei niedrigen Temperaturen angelassenem Martensit unter Wälzkontakt geht einher mit der Zersetzung von RA und dem Aufbau von Druckeigenspannungen, die mittels Röntgendiffraktion systematisch untersucht werden können [12-14]. Auch wenn die spannungsgestützte Umwandlung von RA in Martensit von Anfang an stattfindet und sich mit dem RCF-Prozess fortsetzt, wird ein solcher Prozess mit der DER-Bildung und der anschließenden Entwicklung der WEB in Zusammenhang gebracht [12, 13]. Nach einer ausreichend großen Anzahl von Belastungszyklen kann es zu einer vollständigen Zersetzung von RA im hochbelasteten Bereich kommen.
Die Transformation des Gefüges zeigt sich auch in einer Veränderung der Härte. Es wurde festgestellt, dass die durchschnittliche Härte des veränderten Gefüges deutlich geringer ist als die des Ausgangsgefüges [9, 13, 15]. Ferner wurde festgestellt, dass auf eine anfängliche leichte Zunahme der Härte nach einer hohen Anzahl von Belastungszyklen eine deutliche Abnahme der Härte im transformierten Gefüge folgt [10, 16]. Die anfängliche Zunahme der Härte ist eine Folge der Kaltverfestigung. Bei fortschreitender Wälzermüdung führt die verschiebungsbedingte Kohlenstoffwanderung zu einem zunehmend inhomogenen transformierten Gefüge, das sich durch eine Mischung aus kohlenstoffarmen und kohlenstoffangereicherten Bereichen auszeichnet. Die Kohlenstoffabnahme in der Martensitmatrix führt zu einer allmählichen Abnahme der Härte des transformierten Gefüges.
Fazit
Der Ausfall eines Wälzlagers ist im Wesentlichen das Ergebnis einer Materialschädigung unter bestimmten Betriebsbedingungen. Das Wissen um eine solche Materialschädigung ist von grundlegender Bedeutung für die Vorausberechnung der Lagerleistung, damit eine optimale Auswahl an Lagerstählen und Wärmebehandlungen für bestimmte Anwendungen möglich ist und die verbleibende Lagerlebensdauer prognostiziert werden kann. Solche Prognosen können für die Validierung der Lagerauswahl hilfreich sein oder auf mögliche Veränderungen im Betrieb oder bei der Wartung eines Lagers hinweisen, die die Lebensdauer der nachfolgenden Lager in einer Anlage verlängern können.