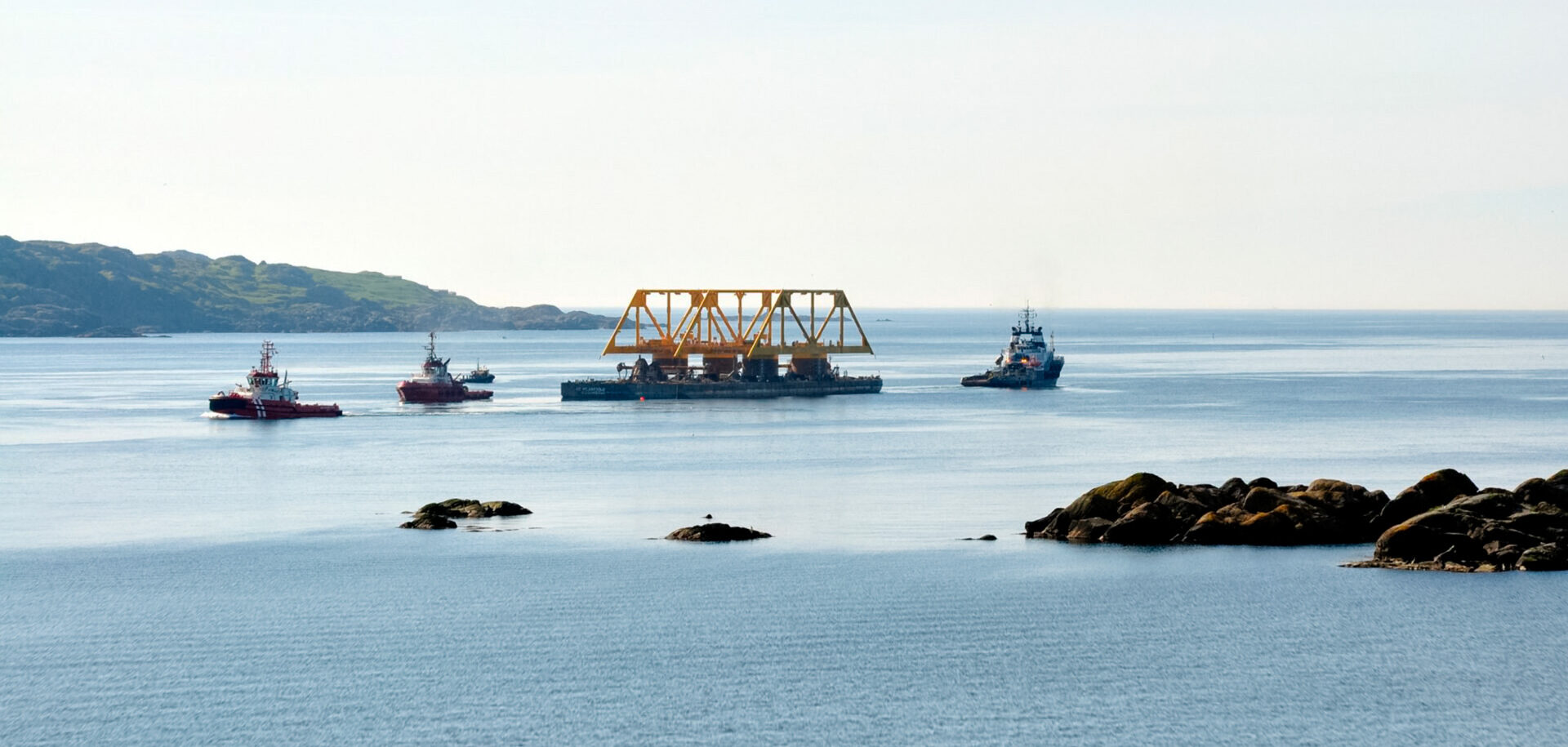
I cuscinetti magnetici superano tutte le prove
Il funzionamento di turboespansori, motori elettrici ad alta velocità e compressori in ambienti gravosi rappresenta una sfida. Assicurarne l’affidabilità operativa sott’acqua, nel deserto e a temperature estreme può risultare difficile con un’esecuzione tradizionale. I cuscinetti magnetici si avvalgono di una tecnologia matura e idonea allo scopo, ma sono ancora poco impiegati. La loro efficacia è stata dimostrata in una delle applicazioni più impegnative del mondo, l’impianto sottomarino di compressione del gas di Åsgard, nel Mare di Norvegia, dove hanno funzionato senza problemi per più di cinque anni e 90.000 ore.
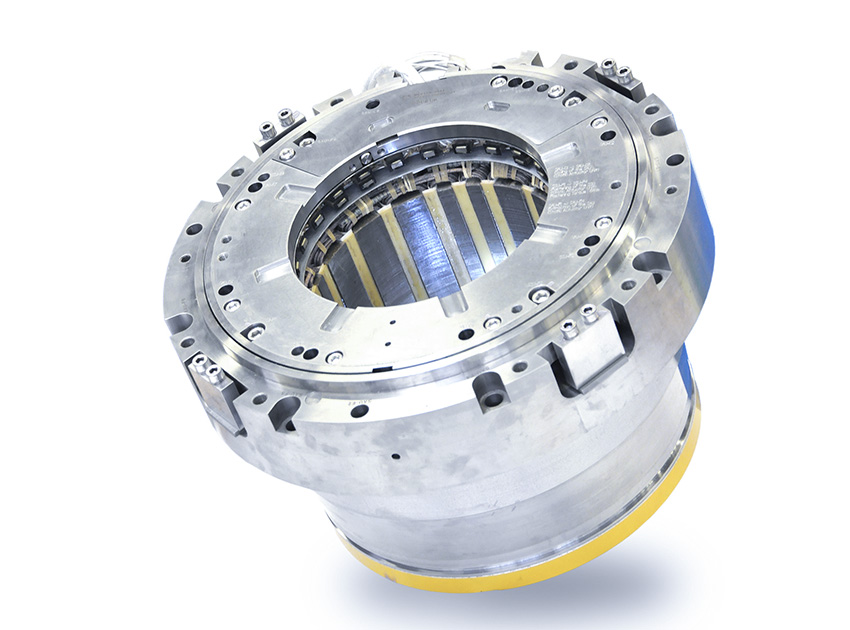
Queste caratteristiche li rendono idonei nelle applicazioni dei settori dell’energia, del petrolio e del gas, in ambienti particolarmente gravosi: dai deserti dell’Arabia Saudita alle piattaforme del Mare del Nord e ai giacimenti siberiani oltre il Circolo Polare Artico.
“I nostri cuscinetti magnetici sono attualmente impiegati in oltre 750 turboespansori, 200 compressori indipendenti e 150 compressori a tenuta stagna in tutto il mondo”, dichiara Alexandre Kral, Business Development Oil and Gas di SKF. “Trovano inoltre impiego nelle applicazioni di turbine a gas, generatori, pompe e molte altre”.
L’unica soluzione realmente praticabile
Per quanto riguarda i compressori a tenuta stagna, i cuscinetti magnetici sono l’unica soluzione veramente praticabile, poiché non richiedono i dispositivi Dry Gas Seal. “Nei cuscinetti magnetici si crea un campo magnetico che elimina l’attrito da contatto tra le parti o l’usura meccanica”, spiega Kral.
L’assenza di usura elimina virtualmente i fermi. Nelle applicazioni onshore e offshore, l’unico a necessitare di manutenzione è il sistema di controllo dei cuscinetti magnetici, che essendo costituito in gran parte da elettronica, ventilatori e filtri, riduce di molto il numero di apparecchiature da manutenere. Un altro vantaggio è dato dal fatto che il sistema di controllo è più compatto rispetto a un tradizionale sistema di lubrificazione a olio. E lo si apprezza in particolare quando lo spazio è ridotto, come in piattaforme e unità galleggianti di produzione, stoccaggio e scarico (Floating Production Storage and Offloading, FPSO), o in zone remote.

Una notevole riduzione del consumo di energia
I cuscinetti magnetici, inoltre, sono ambientalmente più puliti di quelli lubrificati a olio. Questo contribuisce a una notevole riduzione del consumo energetico, poiché questi cuscinetti non necessitano di complessi sistemi di lubrificazione, compresi tubi di collegamento per serbatoio olio, filtraggio e raffreddamento. “I cuscinetti magnetici consumano circa 10 volte meno energia rispetto ai tipi lubrificati a olio”, commenta Kral. “C’è anche un minor numero di dati da monitorare, visto il minor numero di apparecchiature. E di conseguenza serve anche meno spazio”.
I cuscinetti magnetici consumano circa 10 volte meno energia rispetto ai tipi lubrificati a olioAlexandre Kral, Business Development Oil and Gas di SKF.
Eppure, nonostante tutti questi vantaggi, Kral ha riscontrato una certa esitazione quando si tratta di sostituire i cuscinetti tradizionali con quelli magnetici. Un’obiezione riguarda il costo iniziale più elevato.
“Alcuni pensano che i cuscinetti magnetici siano più costosi, ed è vero che le parti meccaniche, la centralina e forse il design della macchina costano un po’ di più”, afferma Kral. “Ma la differenza si recupera facilmente grazie alla semplificazione di installazione della macchina in loco”. La riduzione del peso della macchina porta inoltre a un minore ingombro. Ciò riduce la necessità di costruire strutture, come sulle piattaforme offshore, e consente di risparmiare sui costi. Al contempo c’è un enorme vantaggio in termini di spese operative in virtù del minor numero di misurazioni e apparecchiature, nonché dell’assenza di usura e della maggiore disponibilità”.
A seguito del progetto sottomarino di Åsgard, SKF e i suoi partner hanno nuovamente messo alla prova i cuscinetti magnetici. “Con cinque anni di riscontri positivi, il progetto di Åsgard ha dimostrato tutta la sua efficacia”, commenta Kral.
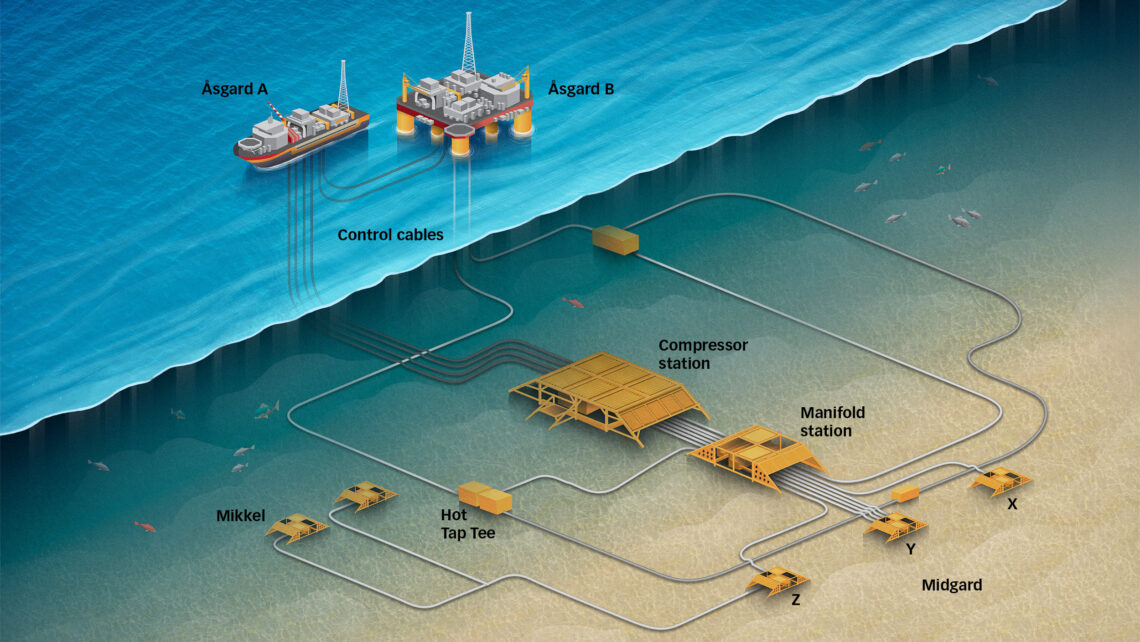
Maratona sott’acqua, cinque anni e non sentirli
Il primo impianto sottomarino al mondo di compressione del gas, equipaggiato con i cuscinetti magnetici SKF, è in funzione dal settembre 2015 nel giacimento di Åsgard, nel Mare di Norvegia. Sono passati più di cinque anni e 90.000 ore di esercizio, ma funziona ancora perfettamente a circa il 100 percento di disponibilità.
I cuscinetti magnetici SKF sono il cuore del sistema di compressione, il quale contiene due unità a tenuta stagna che operano a una profondità di 300 metri. Questi motocompressori ad alta velocità (7.000 giri/min) sono stati realizzati grazie alla tecnologia dei cuscinetti magnetici SKF.
I compressori sono di solito installati su piattaforme in mare aperto e in superficie, ma l’installazione sul fondo marino di Åsgard ha offerto molti vantaggi, tra cui un incremento del tasso di recupero del gas, dal 50-60 percento a oltre l’80, riducendo al contempo i costi operativi e di produzione. Il sistema è di beneficio per l’ambiente, poiché offre una riduzione delle emissioni di CO2.
Scoperto nel 1981, il giacimento di gas di Åsgard è un elemento importante dell’infrastruttura energetica nel Mare di Norvegia. La produzione è iniziata nel 1999 e le esportazioni un anno dopo. SKF ha dedicato un team formato da 20 ingegneri, che hanno lavorato al progetto nel corso dei cinque anni.