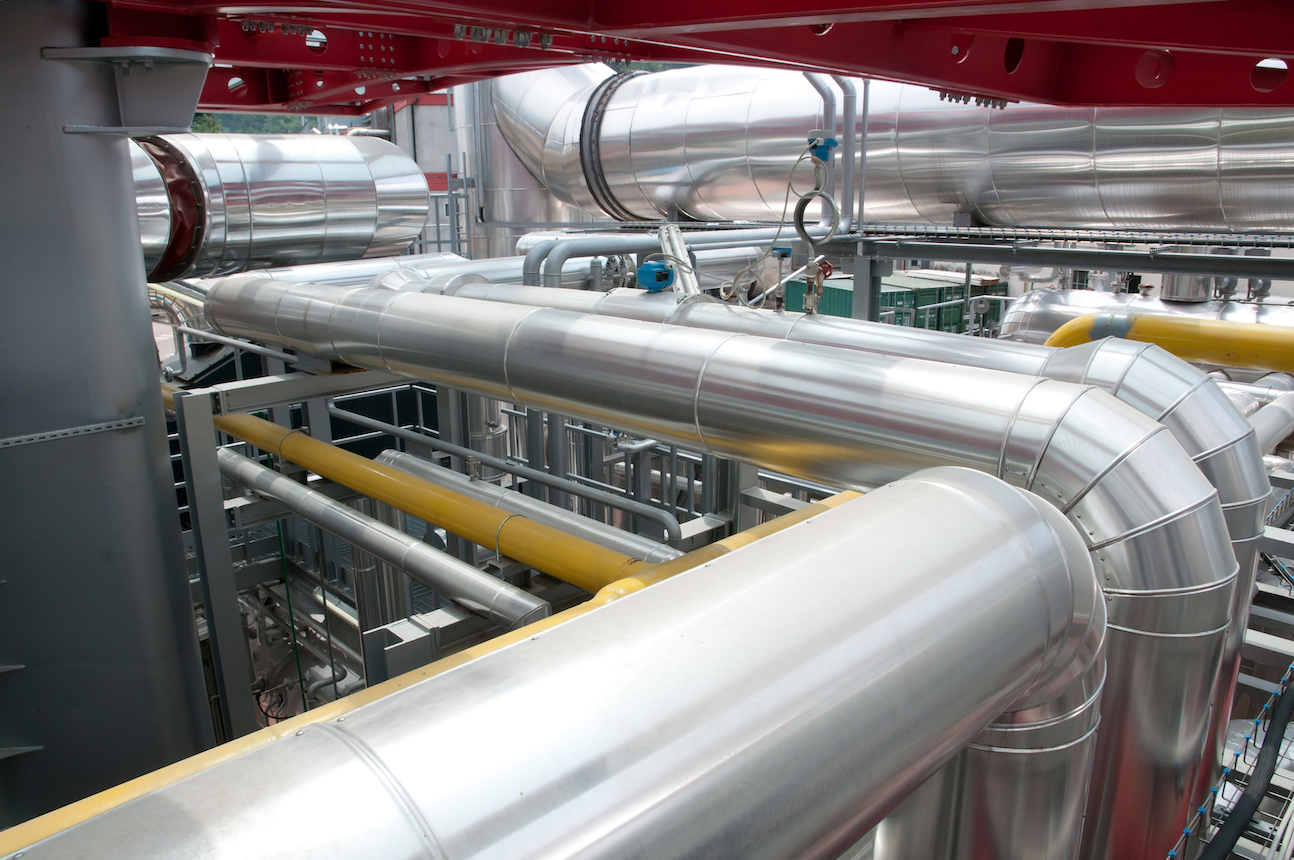
Unioni resistenti
Con sede a Giessen, in Germania, la STANLEY Engineered Fastening impiega un mandrino elettromeccanico per applicare rivetti autoperforanti sull’alluminio.
Fatti
STANLEY ENGINEERED FASTENING
Quartier generale: Giessen, presso Francoforte
Numero dipendenti: 750 in Germania, 5.000 in tutto il mondo
Fatturato complessivo: 1 miliardo di euro
Prodotti: sistemi di fissaggio e giunzione, principalmente per l’industria automobilistica, ma anche per l’industria elettronica e altre.
www.stanleyengineeredfastening.com
Link correlati
Contatto vendite
Swen Wenig Torsten Krause
Dal lancio nel 1994 dell’Audi A8, la prima automobile con telaio in alluminio, questo materiale ha conquistato un’importanza crescente nell’industria automobilistica – soprattutto ora che i costruttori cercano di migliorare le credenziali ambientali dei propri veicoli. Per ridurre efficacemente i consumi di carburante, e quindi le emissioni di anidride carbonica, occorre diminuire i pesi e l’alluminio ben si presta allo scopo.
Non mancano però le controindicazioni: una fra tutte è la difficoltà di saldatura, in particolare nella combinazione con l’acciaio. Ed è qui che entra in gioco la STANLEY Engineered Fastening.
Consociata del colosso statunitense produttore di utensili Stanley Black & Decker, l’azienda è ancora ricordata in Europa con il suo vecchio nome, Tucker. L’area di specializzazione è la produzione di sistemi di giunzione, in particolare per il settore automobilistico, con un vasto assortimento che va dai sistemi di saldatura dei prigionieri agli elementi di fissaggio in plastica, dai rivetti ciechi a quelli auto perforanti (Self-Piercing Rivets, SPR).
Secondo Manfred Müller, president Global Automotive, i rivetti SPR sono la scelta più idonea per l’unione di materiali nella combinazione alluminio-alluminio o alluminio-acciaio. “Il rivetto penetra attraverso il materiale superiore e successivamente si espande sulla superficie di quello inferiore”, spiega. “Poiché non occorre forare preventivamente il materiale, come avviene invece con i rivetti ciechi, questo sistema assicura una tenuta molto resistente, totalmente impermeabile a liquidi e gas, ed è idoneo per produzioni automatizzate”.
La prima applicazione di questo sistema è stata l’Audi A8. Alla Tucker era stato chiesto di adattare il sistema di alimentazione dei prigionieri nella macchina per saldatura affinché potesse essere utilizzato per i rivetti autoperforanti. “È stato in quel momento che ne abbiamo capito le potenzialità”, ricorda Müller.
Fino ad allora, i rivetti SPR venivano applicati idraulicamente. La Tucker, come riconosce Müller, aveva poca dimestichezza con quel metodo: “Provenendo dalla saldatura, sapevamo tutto sull’elettricità, quindi decidemmo di sviluppare un sistema elettromeccanico”. In questo caso la scarsa esperienza è stata provvidenziale, poiché la soluzione elettromeccanica si è rivelata molto vantaggiosa sotto vari aspetti.
Attraverso la collaborazione con la SKF è stato sviluppato un mandrino che consente la pressione dei rivetti in modo altamente controllato ed efficiente. Il motore elettrico e la trasmissione a ingranaggi provvedono a far ruotare la vite a rulli satelliti SKF che esercita la pressione sui rivetti.
“È possibile determinare in modo molto preciso sia la pressione sia la velocità”, osserva Müller. Swen Wenig, manager della sales unit for Precision Business SKF in Germania e Svizzera, sottolinea che la massima pressione si raggiunge anche quando l’unità è ferma. “In qualsiasi posizione e velocità del dispositivo di spinta si ha il 100 percento della pressione. È anche efficiente, poiché l’energia viene utilizzata solo quando il motore è in esercizio”.
I primi sistemi per rivettatura sono stati realizzati nei primi anni novanta e, da allora, STANLEY e SKF hanno perfezionato il progetto. Dice Müller: “Abbiamo sempre concorso allo sviluppo delle viti a rulli satelliti, con l’apporto del nostro settore R&S”. Wenig aggiunge: “Uno dei punti principali è stato migliorare l’economicità dell’intero sistema”.
Anche al sistema di alimentazione dei rivetti e al software, che controlla la forza e la corsa, sono stati apportati notevoli miglioramenti. Le unità sono idonee per l’integrazione con robot. Le linee di produzione dei telai in alluminio vedono la presenza di circa 250 robot preposti all’applicazione massima di 3.500 rivetti per vettura. Ogni mandrino deve essere progettato in funzione dello scopo al quale è preposto ed esiste un’ampia varietà di dimensioni e forme delle strutture a C (C-frame) nelle quali vengono posizionate le lamiere, così da soddisfare requisiti fisici differenti. Possono esserci elementi sagomati che richiedono l’adattamento della struttura prima che l’operazione di rivettatura possa avere inizio. In quel caso, il mandrino deve essere libero per permettere all’unità di raggiungere la superficie, ma poi, quando il rivetto viene applicato, il movimento iniziale sarà minimo per risparmiare tempo ed energia.
Le strutture sono componenti del progetto estremamente importanti. “Sono realizzate in uno speciale acciaio e devono reggere sforzi elevati”, spiega il responsabile degli impianti Burkhard Butz. Quando il sistema è in funzione, le estremità superiore e inferiore della struttura a C devono essere perfettamente allineate, nonostante le forze elevate che tendono a disallinearle. “Arrivano a pesare anche 600 chilogrammi”, fa notare il responsabile degli acquisti Carsten Hess.
È possibile che in futuro gli sforzi possano ancora aumentare. “Il maggiore impiego di acciaio ad alta resistenza per ridurre i pesi rappresenta una sfida particolare”, commenta Müller. “L’acciaio, che è molto sottile e resistente, è sempre la superficie superiore che il rivetto deve penetrare. Il mandrino deve quindi gestire le forze elevate applicate in modo da controllare il rivetto. Quest’ultimo deve essere abbastanza resistente per penetrare l’acciaio, ma abbastanza duttile per espandersi nell’alluminio”.
Viti a rulli satelliti SKF
Le viti a rulli satelliti della SKF permettono un controllo molto preciso del movimento lineare. Sono composte da un albero filettato e da una madrevite, anch’essa filettata internamente secondo analogo profilo, contenente un determinato numero di rulli a loro volta filettati. La rotazione della madrevite produce il movimento lineare dell’albero senza gioco assiale. La configurazione della filettatura consente di ottenere un’ampia area di contatto per una maggiore capacità di carico. L’estrema precisione delle viti a rulli satelliti consente anche un’elevata precisione della pressione e della velocità del movimento lineare.