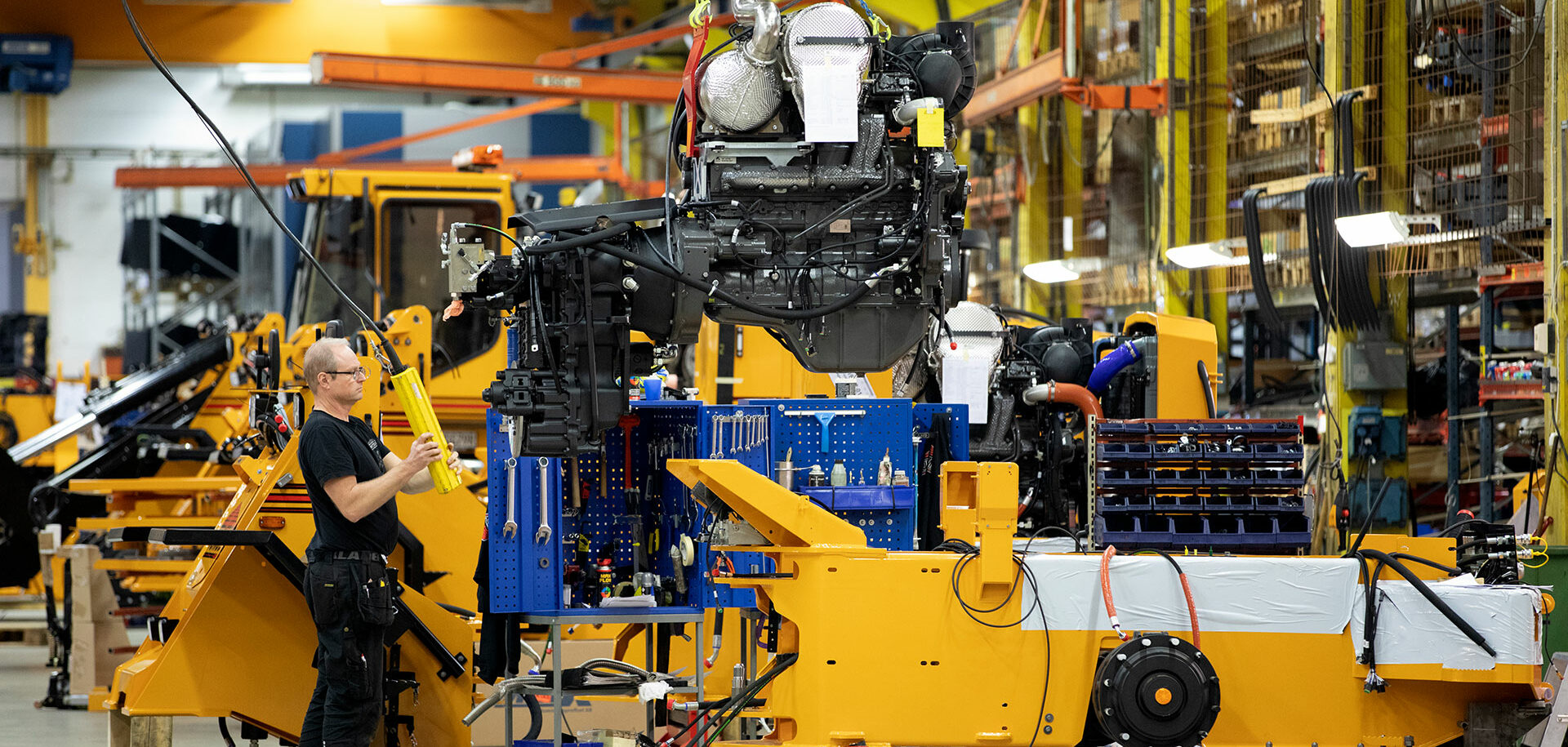
Mission to exceptional comfort
Ljungby Maskin is a manufacturer of wheel loaders based in Ljungby, Sweden. The company’s customers look for high quality, performance and comfort. Rune Andersson, the company’s founder and driving force, was not completely satisfied with the level of comfort provided by foam seat cushions, which used to be the only option. He came to the idea of using a real spring system in the cab. He assigned the company’s designers and SKF’s sealing experts to find a solution, and they did not disappoint. Today, Ljungby Maskin has their very own cab suspension cylinders which are manufactured at the firm’s plant in Ljungby.
Hearses had sprung seats way back in the nineteenth century – so why on earth shouldn’t there be springs in the cab of a
loader, where you sit all day.So says Rune Andersson, who founded Ljungby Maskin in 1983. As he puts it, the company is now: “the world’s smallest, but best manufacturer of loaders”.
With high flexibility to another level of comfort
Each year, just shy of 200 vehicles roll off the line at the company’s plant in Ljungby. Most manufacturing processes take place on-site in the town. Everything from sheet metal working and bending, to paintwork and assembly. This gives a unique degree of flexibility and enables the company to design and equip each individual vehicle according to the customer’s wishes, ensuring Ljungby Maskin’s loaders continue to be considered one of the best on the market.
Among the things that sets Ljungby Maskin ahead of the competition is the exclusive comfort system that they introduced in 2013 – it remains the only manufacturer to offer this option to its customers. The technology is based on a hydraulic system that allows the cab to float freely thanks to four so-called cab suspension cylinders, which are enabled as soon as the parking brake is released. “Spring systems have been around forever”, says Rune Andersson, “so of course we think that loaders – which run on everything from rough terrain to smooth asphalt – should have sprung suspension,”.
The cab suspension cylinders they were so far buying, did not do the job. The positioning was sub-optimal, and there was leakage from the cylinders that it was impossible to remedy. That is why Ljungby Maskin decided to produce their own cab suspension cylinders. “If we can make loaders, we can make our own cab suspension cylinders,” said Rune. The challenges they faced included dealing with frequent, short, rapid movements and relatively low operating pressure and high pressure peaks. It was also necessary to adapt it to work with the existing fittings and to suit the entire after market. At the same time, there was also a requirement for the sealing solution to be able to withstand environmentally-friendly oils that are more aggressive when they come into contact with many types of sealing materials. Daniel Wikman, a designer a Ljungby Maskin, began to draw up plans for a new system and contacted SKF in Landskrona at an early stage in order to seek assistance with the seals.
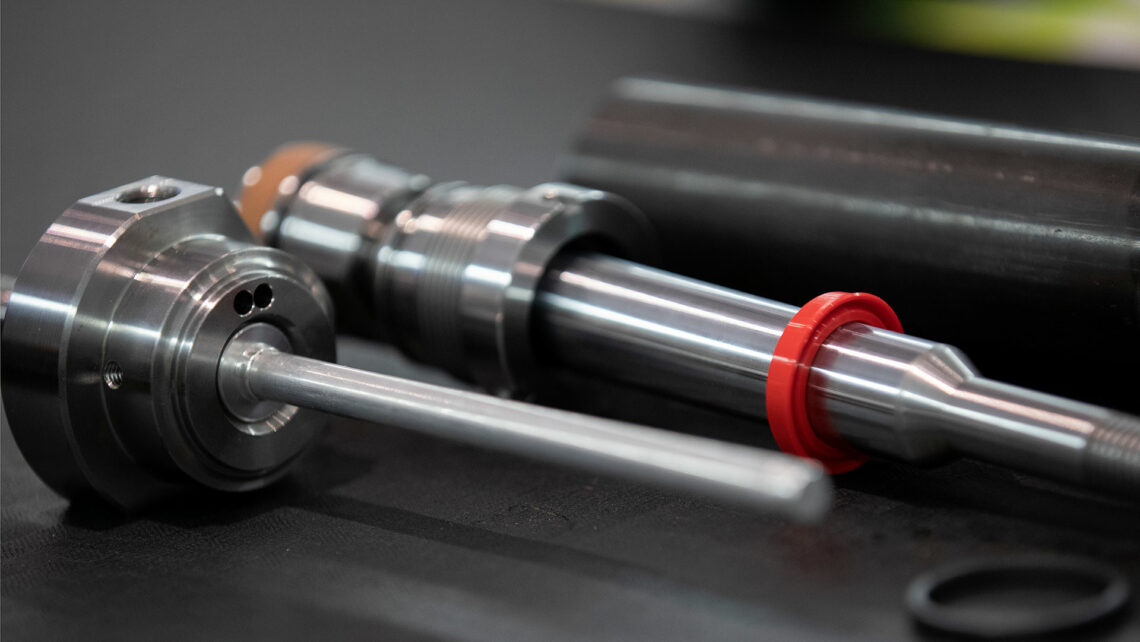
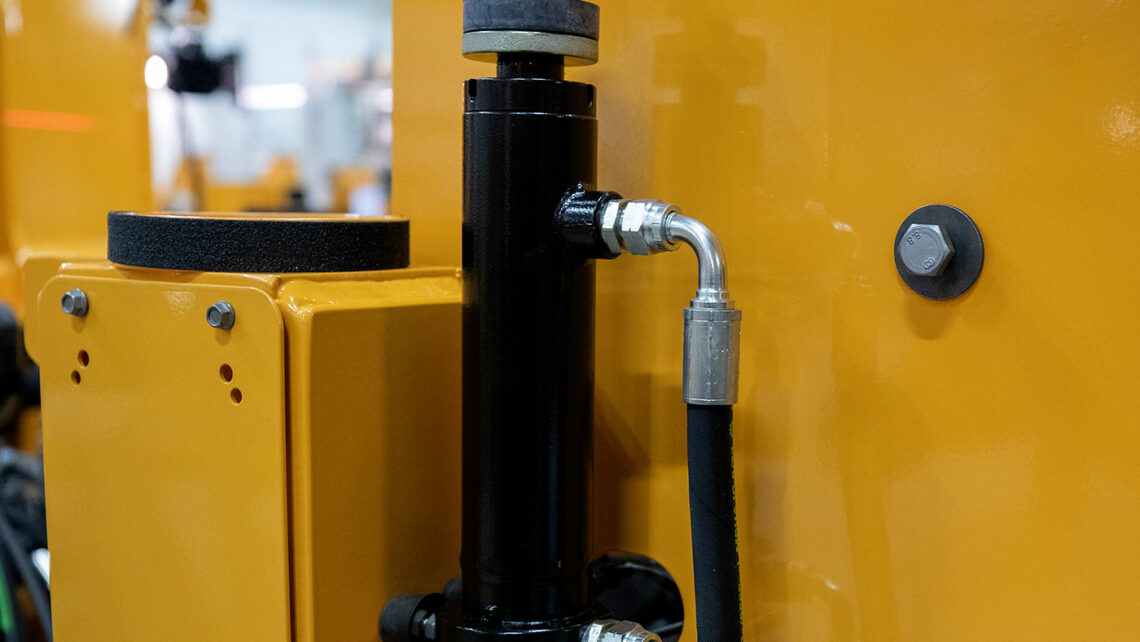
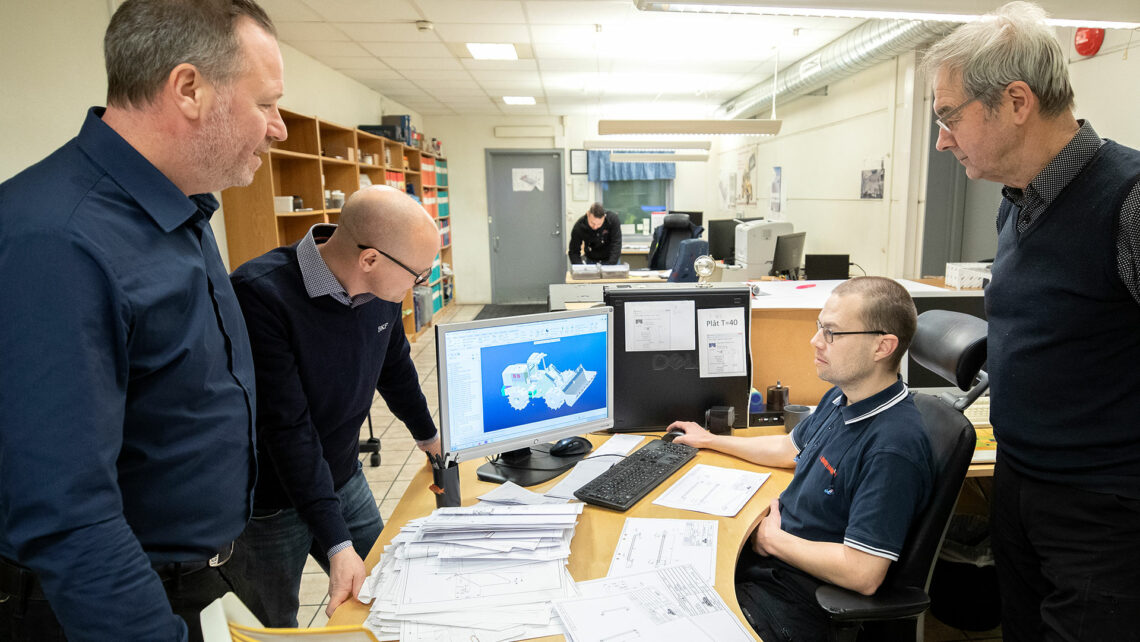
Following a few minor adjustments, the cylinder was ready in the space of just four months. ‘We always pick the best suppliers, and the more closely you work together with your component manufacturers, the better the results you achieve. They know their own fields better than anyone else out there,’ says Rune Andersson.