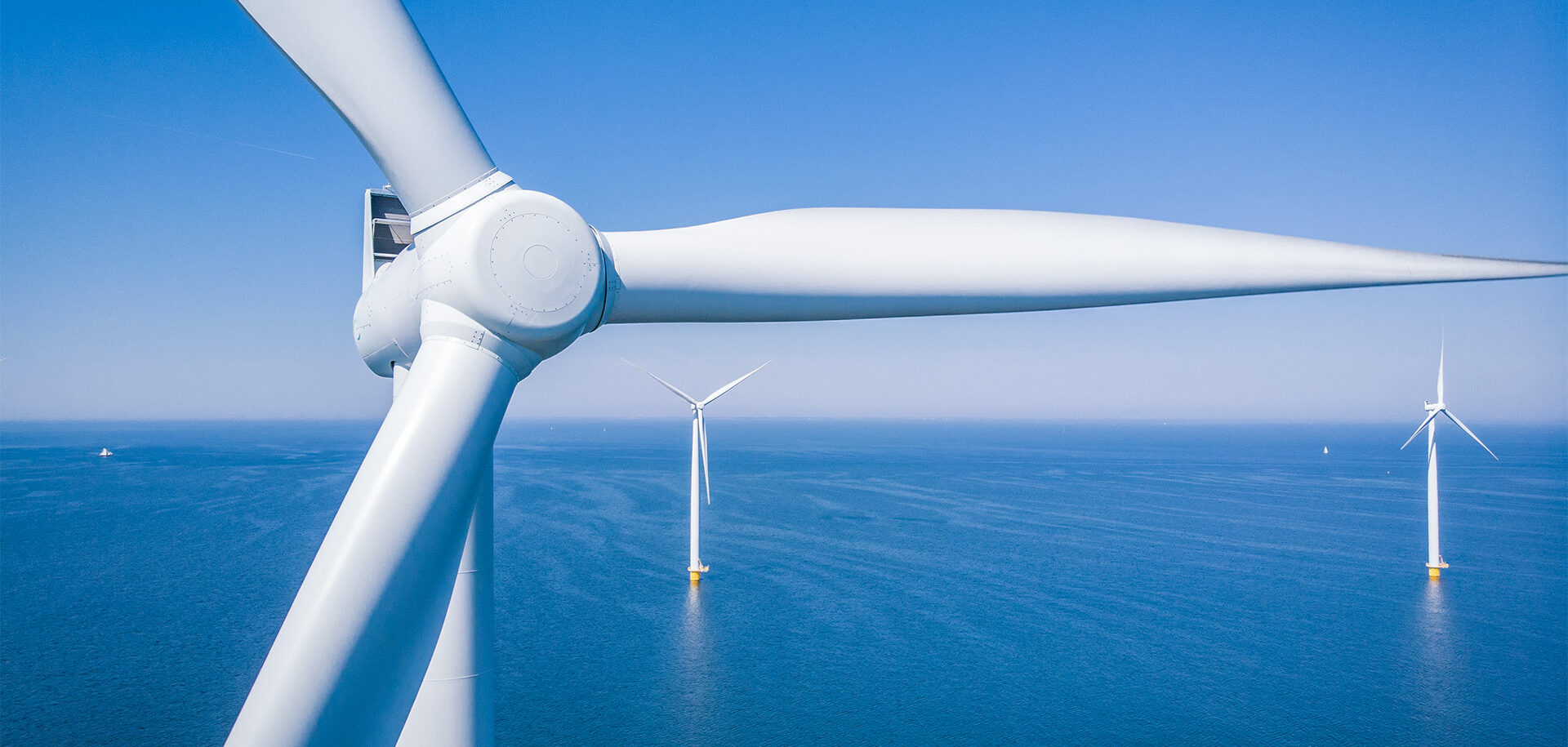
New bearing design for wind turbine gearboxes
Say hello to a new bearing for wind turbine gearboxes. SKF DuraPro for wind turbine gearboxes have a longer endurance life, higher life rating and increased robustness.
The wind industry is facing continual pressure to reduce the levelized cost of energy (LCoE), resulting in new drivetrain designs. Increasing gearbox torque density is required to limit the weight uptower and to limit the size of the largest components for transport [1]. All components, including roller bearings, are therefore required to further downsize without jeopardizing the field performance.
Modern wind turbine gearboxes consist of two or more planetary gear stages. To achieve a higher torque density, the number of planet gears is increased. That way, the torque is split over more gear contacts, which allows reduction of the planet gear and ring gear diameter. These new design trends resulted in significant reduction of gearbox size; however, they also resulted in less space for the bearing supporting the planets (Fig. 1).
Strong roller bearings solutions are needed
One enabler to further reduce the size of planetary gears is the use of hydrodynamic plain bearings. However, depending on the operating conditions, rotational speed and planet gear geometry such as width over diameter ratio, roller bearings are a cost-competitive and well-proven reliable solution. Therefore, new roller bearing solutions are needed that are capable of taking higher loads and contact pressures to support the torque density increase.
These new design trends resulted in significant reduction of gearbox size.
Another important driver in the development of new bearing solutions for wind turbine gearboxes is the need to increase reliability and robustness against typical failure modes in the field, such as premature failures with white etching cracks (WECs) [2] or micropitting [4].
This article presents the SKF DuraPro for wind turbine gearboxes, which is the result of a development project focusing on a new bearing design with:
- increased bearing rating life to enable downsizing of bearings.
- higher robustness against typical failure modes in wind gearboxes.
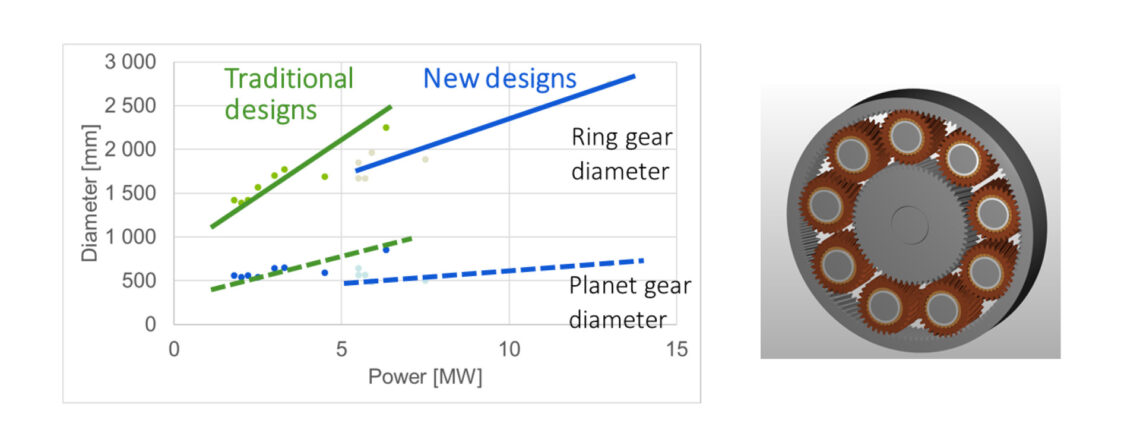
SKF DuraPro for wind turbine gearboxes
The SKF DuraPro for wind turbine gearboxes was developed to meet the high demands on rolling bearings in wind turbine gearboxes. This bearing combines a selected bearing-quality steel with a thermochemical heat-treatment process that enriches the surface and subsurface of the bearing components.
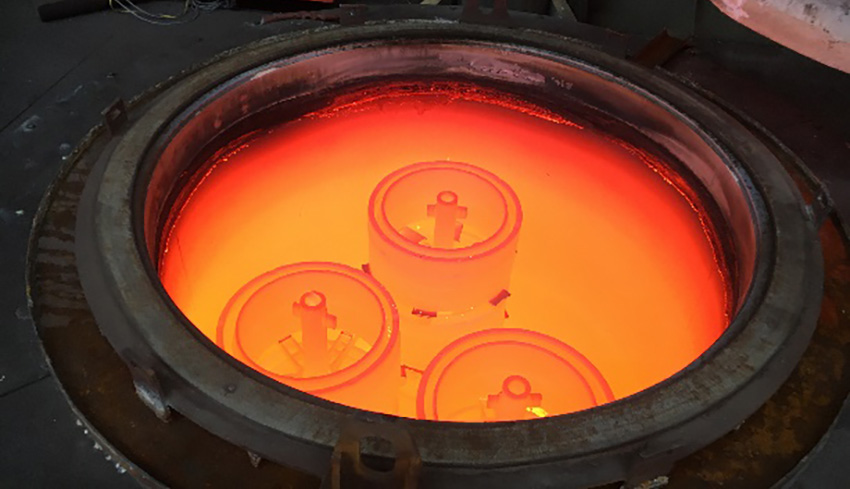
Performance evaluation
Bearing life tests
A testing campaign was executed in which very high load, pre-dented raceway, full-film and reduced lubrication conditions were addressed. The pre-dents act as local stress raisers on the surface, reducing the effectiveness of lubrication. Testing parameters are summarized in Table 1.
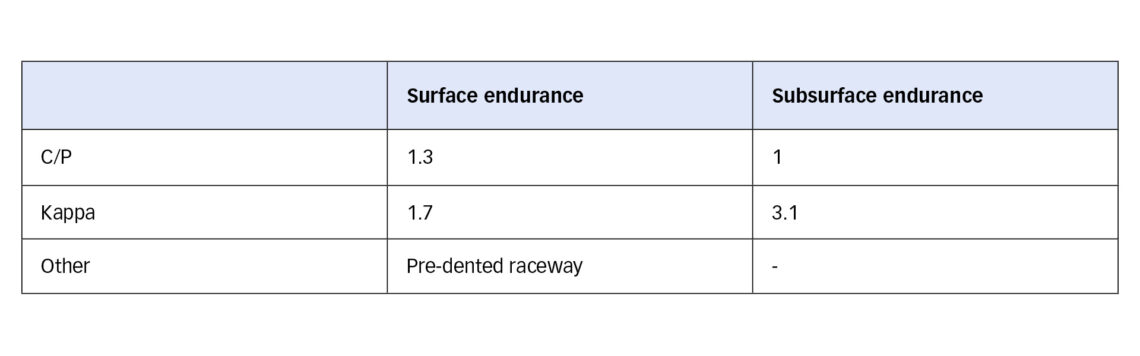
Two bearing variants were tested. The baseline is a state-of-the-art through-hardened series bearing, including SKF Explorer [3] features and black oxide coating. It is compared with the SKF DuraPro for wind turbine gearboxes.
All endurance testing results have been pooled on a single normalized Weibull chart, presented in Fig. 3. This figure highlights the significant performance increase of the SKF DuraPro gearbox bearing versus the baseline. The star shows the modified ISO/TS 16281:2008 life for the SKF DuraPro gearbox bearing (see section 4). The model parameters are selected so that the calculated rating life is close to the lower limit of the confidence interval of the L10h.
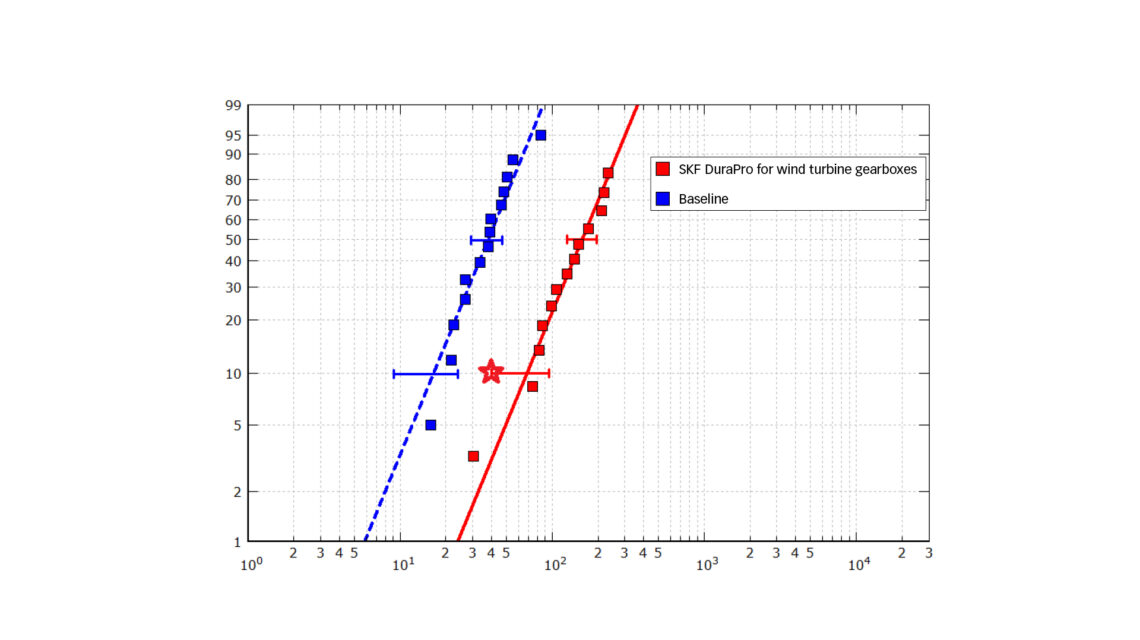
Robustness against premature failures with WECs
Although the introduction of robustness-increasing measures such as black oxide coating has reduced the number of premature bearing failures significantly [6], there is still a market need for more robust solutions. This is valid both for aftermarket, as a problem solver for older designs suffering from premature failures, and for new gearbox designs, because the exact limits of operating conditions when bearings suffer from premature failures are not fully understood [6].
Several drivers for premature failures with WECs have been identified [4]. Different tests have been developed to verify the robustness of bearing solutions. SKF uses a test rig where premature failures are reproduced by introducing high tensile stresses [7]. In the application, high tensile stresses can arise from inadequate fits, radial runout of the shaft diameter or deformation of the bearing seating. On this rig, the bearing is mounted on a shaft with artificial waviness, resulting in high tensile stresses in the raceway at the top of the waves (Fig. 4). Even at contact pressures around 1.5GPa in the rolling contact, which are representative for normal operating conditions in wind turbine gearboxes, premature failures are generated after relative short testing time with a very similar appearance as failures seen in the field (Fig. 4).
The bar chart in Fig. 5 shows that six SKF DuraPro gearbox bearing have been tested under identical conditions and none of them have failed. All tests were suspended after 1,600 hours or more. Bearings of standard steel and heat treatment failed on average after 178 hours.
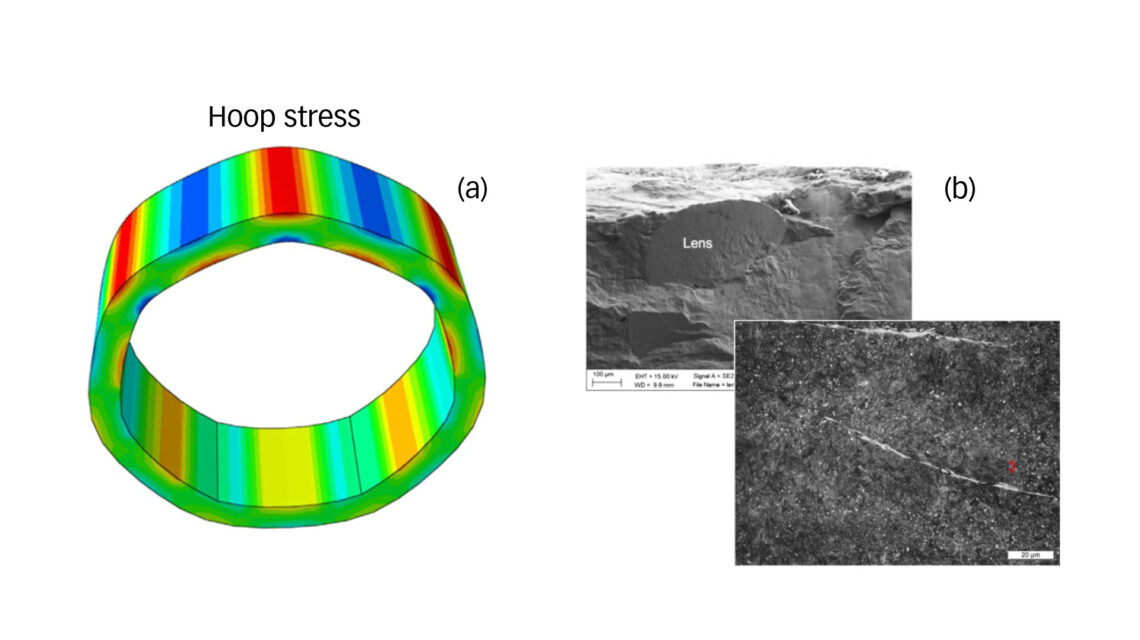
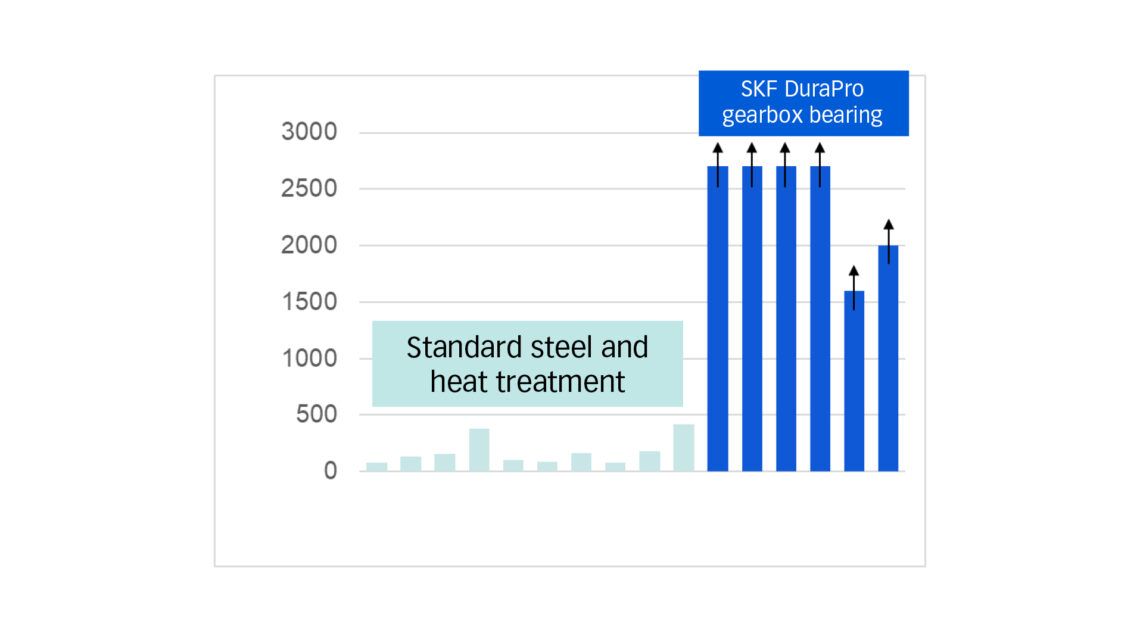
New rating life models for SKF DuraPro for wind turbine gearboxes
The wind industry requires an evaluation of the bearing rating life using ISO/TS 16281:2008 [10]. ISO/TS 16281:2008 as well as ISO 281:2007 do not allow the calculation of the bearing life provided by advanced bearing solutions. Therefore, SKF has developed a methodology to incorporate SKF DuraPro gearbox bearing performance into ISO/TS 16281:2008 modified rating life. It combines an increase of the dynamic load rating and an increase in the life modification factor αISO.
According to ISO 281:2007, αISO is calculated as:
As shown in Ioannides et al. [11], the beneficial effect of advanced heat treatments and improved surface finish can be accounted for in the ISO model by adding proper characteristic numbers in aISO. To incorporate the performance improvement of the SKF DuraPro gearbox bearing, the factors Ψbrg, reflecting the Explorer effect, and ΦHDB, reflecting the additional effect of the improved steel and heat treatment, have been included in αISO:
Based on endurance testing presented previously, the adjustment function Ψbrg and ΦHDB can be determined.
SKF DuraPro gearbox bearings have improved material properties in both the subsurface and the surface. Therefore, the SKF generalized bearing life model (GBLM) [8] is the rating life model best suited to reflect the increased performance as realistically as possible, which separates the surface and subsurface effects (see Fig. 6). The basis of the SKF GBLM can be written as:
The subsurface term of the equation, represented by the volume integral, can be solved using established rolling contact fatigue methods [8]. However, the surface term, given by the area integral, accounts for failure modes related to surface fatigue. The surface term also incorporates modelling of the bearing design feature that can enhance the strength of the surface as in the present application. This approach was already successfully applied to the rating life calculation of hybrid bearings [9] and will be rolled out to more and more SKF products.
Once the different factors of the new rating life model are defined based on the previously described life tests, the rating life of SKF DuraPro gearbox bearings can be evaluated.
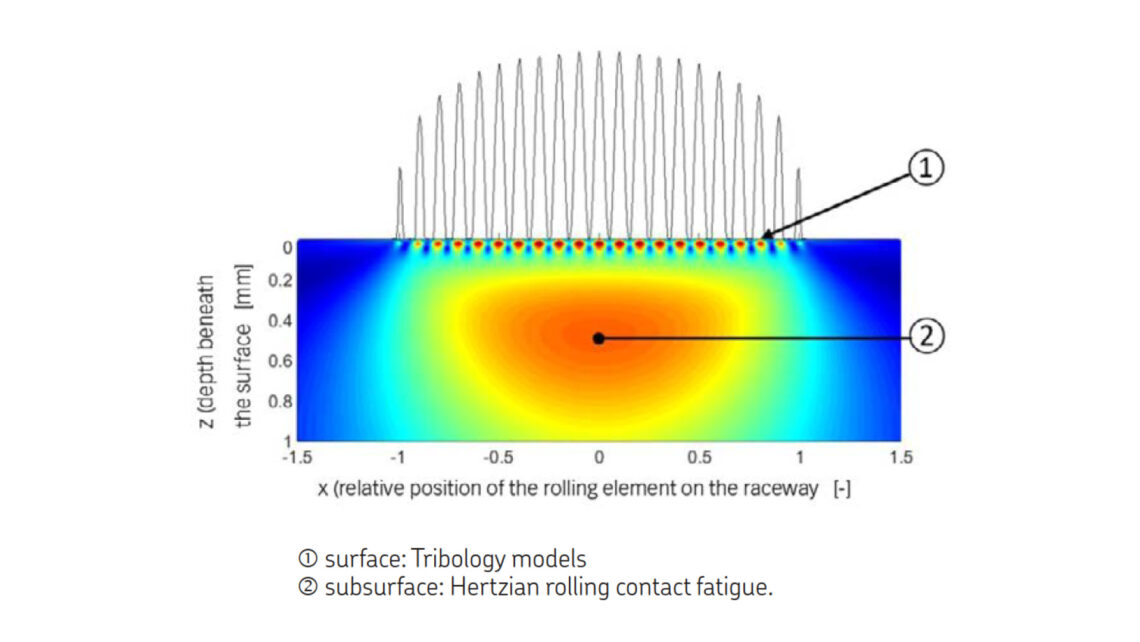
The increase of the bearing rating life depends on the actual operating conditions. Fig. 7 gives an indication of the average life increase achieved in several calculation examples of the different stages of typical gearboxes. The life increase achieved is more than a factor of four. Thanks to the combined improvement of the surface and the subsurface performance, a significant rating-life increase is achieved over a wide range of operating conditions.
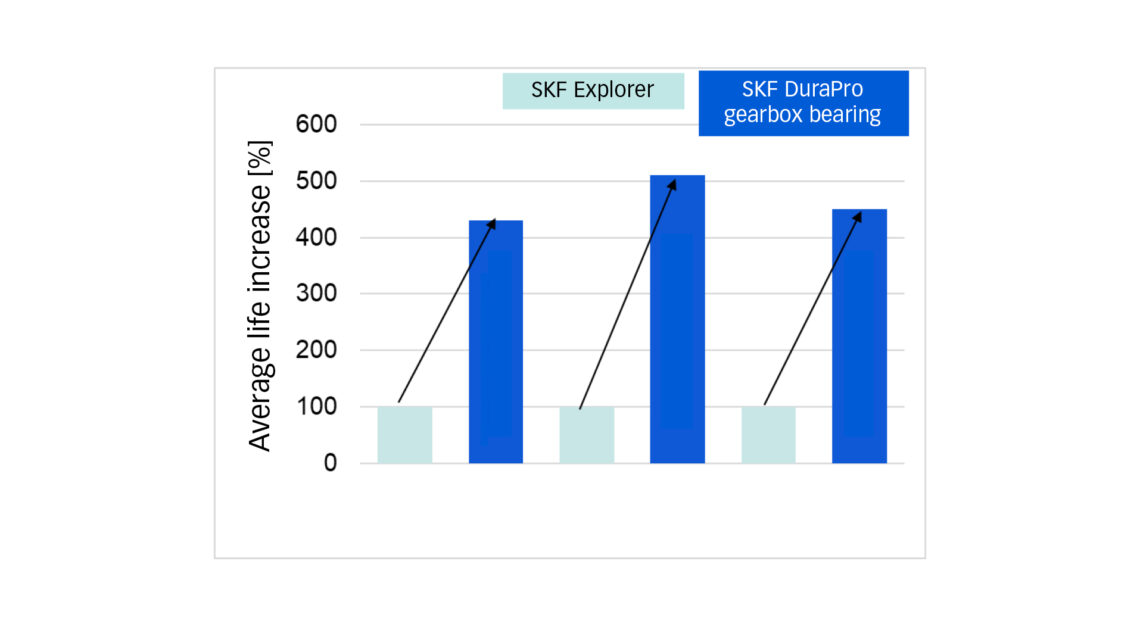
How SKF DuraPro for wind turbine gearboxes can support torque density increase
The dimension of the bearing supporting the planet gear often determines the minimum size of the planet gear. Therefore, a potential downsizing of this bearing will directly influence the planet gear dimensions and hence the size of ring gear and consequently the torque density of the gearbox.
This section shows with an application example how SKF DuraPro gearbox bearings can support this torque density increase by downsizing the planet bearing while keeping the same bearing rating life. It is based on a state-of-the-art 6 MW wind turbine gearbox, supported by a 4-row cylindrical roller bearing with the outer raceway integrated in the gear wheel. The customer requirement is to achieve a rating life of 30 years, fulfil the requirements of IEC 61400-4 [10] and minimize the outer raceway diameter.
Fig. 8 shows how the bearing size can be reduced while keeping the same bearing rating life. The first bar shows the bearing rating life of the original bearing selection. The second bar shows how the rating life would increase if this bearing were changed to an SKF DuraPro gearbox bearing. The third bar shows the rating life of the optimized bearing design using SKF DuraPro gearbox bearings. The outer raceway diameter is reduced by 25 %, from 460 mm to 350 mm, while the rating life is still fulfilling the customer requirements.
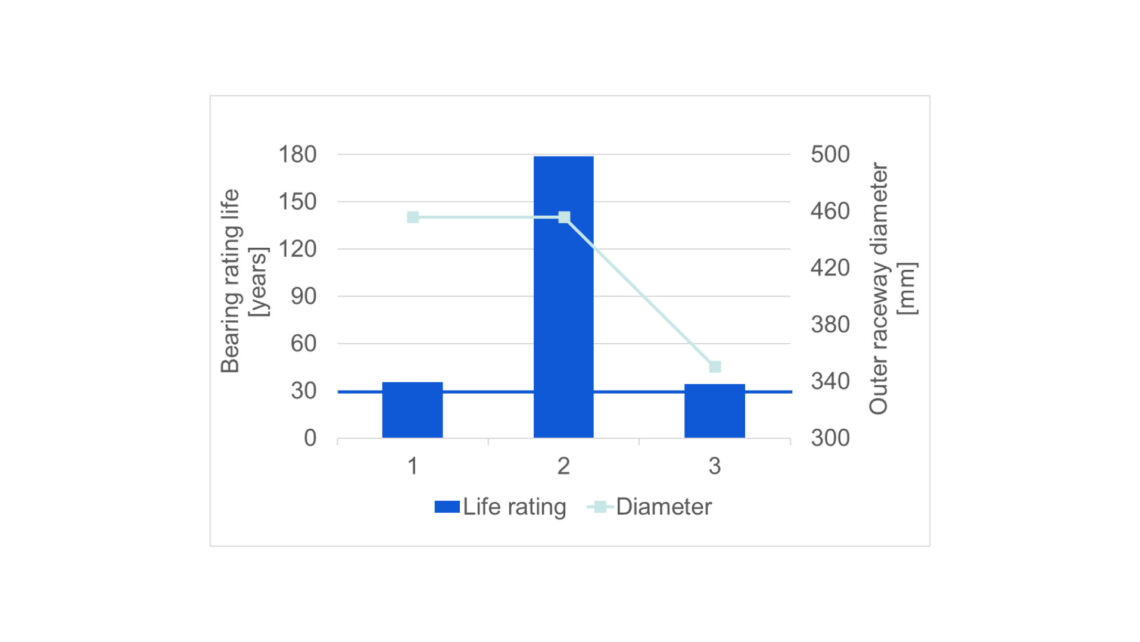

Similar size reductions can be achieved on different positions in the gearbox:
- Depending on the gear stage, the gearbox manufacturer requires a size reduction focusing on diameter or on bearing width (more relevant for higher speed stages).
- On the high-speed shaft, downsizing with SKF DuraPro for wind turbine gearboxes will contribute to a reduced risk for slip-related damages, where roller (set) inertia plays an important role.
Conclusions
The optimized steel and heat-treatment process applied for SKF DuraPro for wind turbine gearboxes results in following proven benefits:
- Confident downsizing of up to 25 % in bearing and gear dimension at the same loads enabled through five-times-longer life on surface and subsurface fatigue.
- Satisfy the increased design-reliability requirements and design-life demands of 30 to 40 years with bearing rating life at the forefront of the industry, included in a modification of ISO/TS 16281:2008 and soon as well in SKF GBLM, successfully audited by DNV.
- Increased field reliability by higher robustness against tough operating conditions in wind gearboxes.
Moreover, the increased robustness of SKF DuraPro for wind turbine gearboxes against typical failure modes in wind turbine gearboxes lead to less unplanned turbine standstill and repair cost. It’s a problem solver in the field to increase the reliability in case of premature bearing failures.