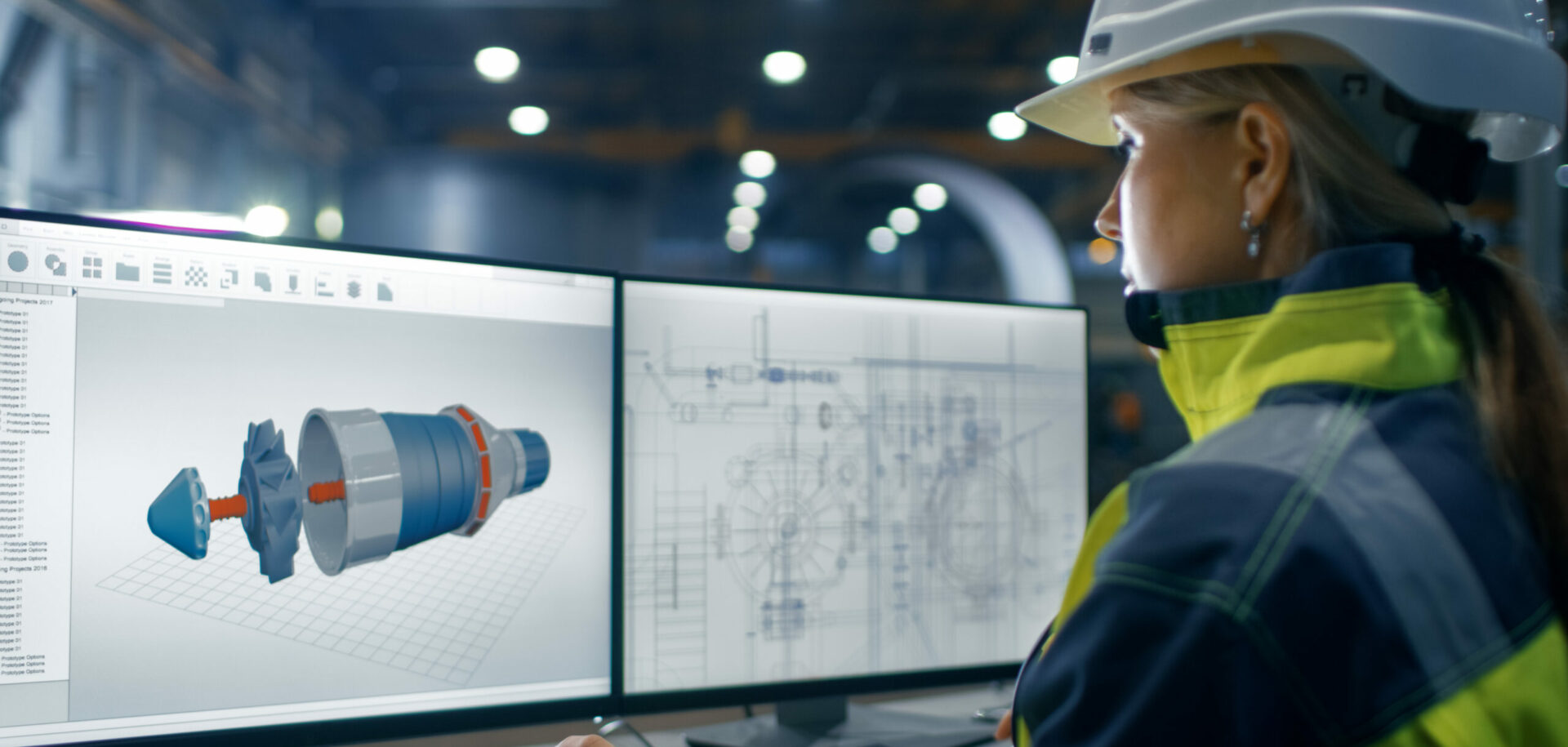
New sealing solutions for deep groove ball bearings
RSL and RSH seals now introduced by SKF are designed to offer longer service life as well as energy savings in bearing applications.
For more than 50 years SKF has offered “for life” solutions by integrating the sealing function into deep groove ball bearings. This is in line with industry trends towards reduced maintenance requirements in bearing applications. Factors that contribute to longer service life are good sealing efficiency, contamination exclusion and grease retention. An additional requirement is energy saving, which requires low-friction seals.
Consequently, SKF has developed various sealing types that meet most of the application requirements – namely, shields (Z), low-friction seals (RZ) and contact seals (RS1).
Operating conditions for bearings today are increasingly severe in terms of speed, temperature and contamination. In addition, the use of high-pressure cleaning is becoming popular. Such requirements are particularly hard on smaller-sized deep groove ball bearings used in a wide range of applications, such as electrical equipments for the automotive industry, power tools, household appliances, two-wheelers and many types of outdoor equipment.
Solutions for ball bearings
SKF has developed specific seals for deep groove ball bearings, such as the RSL and RSH seals. Initially, bearings fitted with these seals were offered to customers for advanced applications and have been extensively field-tested. The seals are now introduced as standard solution for smaller-sized deep groove ball bearings, being mass produced and available in numerous sizes, enabling SKF users to benefit from solutions originally developed for advanced applications.
The RSL and RSH seals replace, as a first step, the previous RZ and RS1 ones respectively in bearings in the 60, 62 and 63 series with a bore diameter of 6 to 25 mm and an outside diameter of up to 52 mm.
RSL designs
Depending on bearing size and available space, there are two different seal designs. Bearing with an outside diameter up to
25 mm use a non-contact seal as shown in .1, and bearings with an outside diameter greater than 25 mm and up to 52 mm inclusive have a light contact seal as shown in .2.
Under the same operating conditions and compared with the previous RZ seal, the new RSL seal provides improved grease retention and contaminant exclusion.
RSH designs
There are also two RSH designs, depending on the bearing size and available space, and they differ slightly in the position of the primary seal lip. Bearings with an outside diameter up to 25 mm have a seal as is shown in .3. Bearings with an outside diameter greater than 25 mm and up to 52 mm inclusive have a seal as shown in .4.
Compared with the RSL seals, the new RSH seals have the following additional features:
- A secondary seal lip that withstands high-pressure cleaning and protects against water entry. The contact pressure between this seal lip and the seal counter face increases when the pressure is applied to the outside of the bearing.
- Radial slots in the tapered attachment. These enable the seal lip and the counter face to be properly lubricated, enabling the grease to act as a third protection.
Finite element analysis based on a program developed by SKF was used to evaluate and optimize the seal design. The program analyses the seal-lip contact force, stress and strain. The aim was to avoid excessive changes of the lip contact force, regardless of the lip interference with its counterface inside the tolerance range set. Part of this work is illustrated in .5(strain distribution inside a RSL seal lip area) and .6(contact force versus axial interference).
Sealing test program
The seals have been evaluated by extensive tests based on their performance against measured parameters, including friction torque, speed, grease retention, dust exclusion, static and dynamic water exclusion and high-pressure water exclusion.
The friction torque, breakaway and stable, is evaluated at low, moderate and high speeds. An initial speed test is performed for 24 hours, at moderate and high speeds and light load. Grease loss or residual grease quantity is evaluated, and the outer ring temperature is recorded for all the test times.
A second speed test is performed under conditions similar to the first test. In this case, however, friction torque is recorded instead of the outer ring temperature. The test rig is shown in the .7.
To measure dust-exclusion capabilities, the bearing is placed in a closed chamber containing Arizona dust. Two-rod impellers rotating at the same speed as the bearing move the dust. The bearing runs at moderate speed for a defined time period. The content of dust inside the bearing is a measure of seal performance.
For the static water exclusion test, the bearing is heated in an oven at 100° C (212° F) and then immediately immersed in water at ambient temperature. The increase of the bearing weight after the test indicates the amount of ingress of water.
To make a dynamic water exclusion test, the bearing runs at moderate speed with two water jets directed towards one side of the housing face, for few hours with low radial load. As for the static water exclusion test, the quantity of water found inside the bearing is an indication of seal performance.
A high-pressure water test, sometimes also called the Kärcher test, is performed both with a horizontal and a vertical shaft. The bearing is washed with a hot water flow at more than 100 bars from the pump. The distance between bearing and nozzle depends on axis position, horizontal or vertical. Bearing performance is evaluated as above.
Improved performance
The RSL and RSH seals have been tested on the basis of the above test regimen on a variety of bearing sizes. Compared with the original RZ seal, under the same operating conditions, the RSL seal for bearings with outside diameter greater than 25 and up to 52 mm inclusive provides improved grease retention and improved exclusion of moisture and contaminants ( table 1). The performances of the RSL seal for bearings with with outside diameter up to 25 mm shows an improvement in grease retention and dust exclusion compared with the RZ seal.
Under the same operating conditions, when compared with the RS1 seal, the RSH seal provides increased grease retention and improved water exclusion, specifically under high-pressure water impact and contaminants. See table 2for all the bearing sizes.
The test was performed mainly on “standard” bearings, i.e., with NBR (acrylonitrile butadiene rubber) seal material, a normal grease quantity and grease for a medium temperature range.
The change of one of these parameters could partially modify the results.
The RSL low-friction seal and the RSH contact seal have features to meet technical needs of a variety of applications and should be chosen according to the specific requirements of each application.
Application tests
While longer service life is one of the primary targets, SKF has also focused on other customer requirements. Minimal power loss and a lower running temperature in combination with a dusty environment is one particular feature. For many customers, power loss is less important than maintaining the seal performance in harsh environments, including the presence of water and mud.
Two typical cases highlighted here detail the special tests that have been performed to satisfy such operating conditions.
The first example is that of a power-tool manufacturer who wanted products to achieve a longer service life to meet regulations for a warranty period of more than one year. Good bearing protection is vital because power tools such as angle grinders ( .8) or hammer drills work in very dusty environments. In addition, a very low running temperature (or low friction or low power losses) is very important, as excessive temperature on the handles can create problems for end users ( .9). The RSL seal is the solution for power tools or similar applications. Also, it has a better performance than the RZ seal in the dust exclusion test as shown in .10.
The efficiency of the RSL against dust does not affect the running temperature at the speed in the application. The bearing outer ring temperature has been just a few degrees (°C) above the ambient temperature for both RSL and RZ seal executions.
In the second application, bearings are used in the wheels of a snowmobile. Sealing is important, particularly in slushy conditions when there is a risk that splashes of water and mud can reach the bearing face, enter and destroy the lubricant. Bearings with RSH seals have been selected for this heavy-duty application after testing in a dedicated rig ( .11) compared its performances to the RS1 seal.
The bearings have been tested under the following conditions:
- Rotating outer ring at 2,000 min-1, fitted into the snowmobile wheel;
- Test duration of 15 hours;
- Low radial wheel load;
- Wheel partially immerged in the mud;
- A mud composition of water, clay and small stones.
Water content inside the bearing has been the way to judge seal performances. This testing ( .12) shows that the RSH seal performs better than the RS1.
Overall, the new seals offer enhanced performance packaged in a standard range for deep groove ball bearings for tough applications.