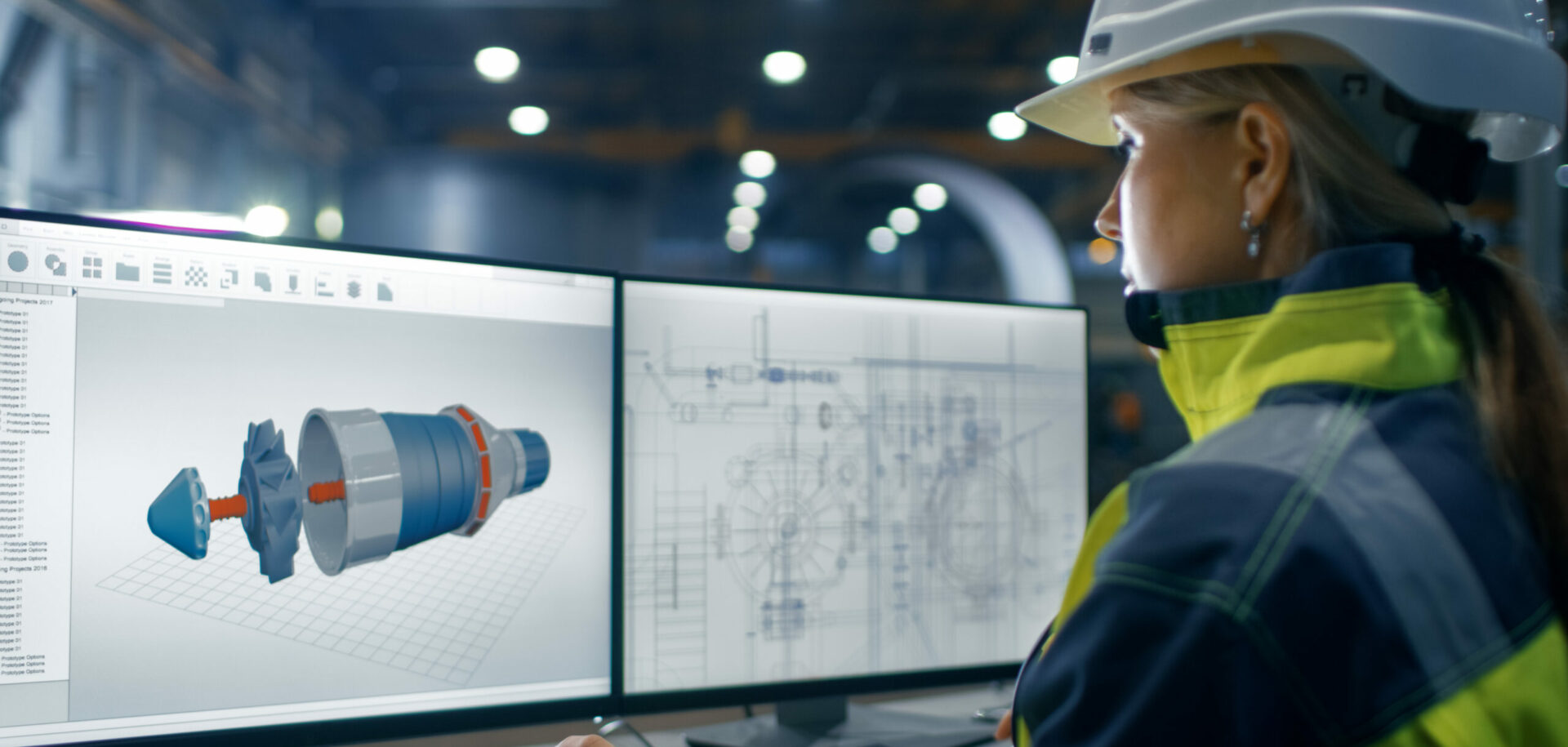
New solution, new future
The solution to an old maintenance problem highlights a new way of doing business for SKF and its mining partner LKAB. It may also herald new life for one of Sweden’s northernmost cities.
The solution to an old maintenance problem highlights a new way of doing business for SKF and its mining partner LKAB. It may also herald new life for one of Sweden’s northernmost cities.
Kiruna is Sweden’snorthernmost city. It is also the site of one of the world’s largest underground iron ore mines. The town has grown up around this one industry. A third of the town’s workforce is employed here, and nearly everybody is dependent on the mine in some way or other. Iron ore deposits extend over four kilometres, even under where the town is situated, and it is likely that in the future, parts of the town will have to move as mining operations expand. Everyone knows this, so it’s not an issue in daily life.
Mining has been conducted in the Kiruna area for centuries. In 2005 LKAB, the company that runs the mines in Kiruna and Malmberget, extracted some 36 million tonnes of crude ore from depths of some1,000 metres underground. Once the ore is mined it is pro-cessed (“upgraded”) and exported to steel industry customers in Europe, North Africa, the Middle East and Southeast Asia.
LKAB prides itself on the quality of its products, a factor that gives the company its vital competitive edge, according to Ola Johnsson, vice-president and head of the mining division. Yet, it accounts for just three percent of the world total of exported iron ore. “The big three,” as Johnsson calls BHP Billiton of Australia, Rio Tinto of the UK and Companhia Vale do Rio Doce of Brazil, between them account for more than 70 percent of the world’s iron ore export market.
Product quality andmaximum automation of the mining process are vital, if LKAB is to maintain a competitive position, so the company is examining a number of initiatives with a view to improving product-ivity, efficiency and the environment in its operations.
All these factors go hand-in-hand, particularly at the company’s ore-concentrating operations in Kiruna and 50 kilometres south, in Svappavaara. At these two centres, and at a third, Malmberget, LKAB operates 33 mills – huge, horizontal ore grinding mills. Iron ore passes through the mill and is gradually broken down to very small sizes. At the discharge end the particles are roughly 45µm (thousandths of a millimetre) in size. The ore is then moved on to the next processing step.
Each mill is supported by two large bearings, fitted to a trunnion at each end. The design of the bearing arrangement is nearly 30 years old. The bearings are subject to damage due to ingress of contaminants, such as the fine-milled product and water used in the milling process. Appropriate grease is constantly pumped through each bearing (as much as 900 kilograms a year), not only to provide lubrication but also to repel contaminants. This also means that the same grease quantity is being squeezed out each year, with the result that it drips down from the bearing housings and needs to be physically removed to prevent environmental hazards. A specialist cleaning company undertakes the task, using high-pressure water hoses – an activity that brings further corrosion risks to the bearing environment.
In 2002,a discussion began between LKAB and SKF to find a way to overcome the problem. A project team was established with the objectives to improve the sealing arrangement, to reduce the grease consumption, and to reduce inspection and maintenance requirements and costs. SKF drew on parallels between this type of bearing arrangement and new arrangement designs that had been developed for the pulp and paper industry, where similar problems with contamination and corrosion had been encountered.
SKF proposed a new bearing arrangement design, which was then implemented on a test basis at the processing plant in Svappavaara in October 2004. The design featured a new sealing arrangement incorporating a revised double grease labyrinth. The new bearing arrangement proved able to meet the original design requirements in everyday operation. “Unit mainten-ance time has been cut from some 10 hours per year to less than two, and grease consumption has been slashed to 20 kilograms a year,” says Yvonne Björnström, maintenance manager at Svappavaara. “That’s a considerable saving.” Björnström has been a member of the new bearing arrangement development team from the outset. Today, LKAB is evaluating plans for the gradual replacement of all existing bearing arrangements.
“Our aim is to maintain our position as a world-class producer, to be an integral part of our customers’ production line,” says Ola Johnsson. “And that’s what we want from our suppliers. We can’t do everything ourselves, so we need partners that we can rely on – long-term partners.” An ideal partner, he says, is one that takes the problem from LKAB, solves it and develops solutions for the future.
MCC (Mining Control Centre) AB
Another example of the close strategic cooper-ation between LKAB and SKF is MCC (Mining Control Centre) AB, a joint venture established together with Sandvik. The company, based in Kiruna, was founded in 2003 and has grown to a staff of 16 technicians and development engin-eers and an annual turnover of 1.4 million euros. They are responsible for collating, measuring and analyzing on-line vibration data from the plants, in order to help improve LKAB’s preventive maintenance capability.
MCC uses key performance indicators developed with LKAB to demonstrate how many hours of production would be lost if the work weren’t undertaken. The indications are that, so far, LKAB is increasing its profit by about 10 times the cost of its involvement with MCC.
MCC’s business idea is to work with condition monitoring and maintenance development, mainly in the mining and minerals processing industry (it has been involved with the new bearing arrangement project from the start). Today, LKAB provides around 95 percent of the business, but as the business grows over the coming three to five years, that figure should represent about 50 percent. The intention is to develop into a global centre for competence and excellence.
“This is a fairly new business model for all of us,” says Jonas Kemi, managing director of MCC, although he points out that SKF and LKAB have been working together closely for more than 90 years. “It is a real business partnership, not an outsourcing arrangement, and it is the best way of achieving an open-book collaboration and genuinely open cooperation.”
But there is another reason why this cooper-ation is important. At the beginning of the new millennium, LKAB executives started discussing concepts that they called “value-adding services.” They looked at what represented the biggest future threats to LKAB and determined that it was from the development of society in Northern Sweden, rather than other problems. During the past 30 years, a third of the population has moved away. Kiruna had 30,000 people in the late 1970s; today the population is around 20,000. This has a knock-on effect, not just on the future workforce, but also on issues such as health care, transport and so on.
The underlying intention of these cooperation concepts is that they should help create new businesses and services in the region, thus attracting and retaining people to the area (and, of course, benefiting the key businesses behind the initiative). Already, there are exciting new tourism concepts on display at Kiruna airport, with plans to turn the old mine works into extensive leisure facilities.
Long-term relationship
The cooperation between LKAB and SKF extends back over nearly a century. The first trials with SKF self-aligning ball bearings were made in 1913 at the Malmberget mine, where the ore was loaded in Norberg wagons equipped with SKF bearings. In an article in the SKF Ball Bearing Journal in 1927, LKAB testified that not a single bearing had failed since the Norberg wagons were equipped with SKF bearings. In 1914, LKAB was facing the introduction of a third shift in order to meet the requirements of the increased export trade. Instead, the company decided to use wagons that were slightly larger and to equip them with SKF self-aligning ball bearings. The result was that the same locomotive that previously could haul a train of 35-tonne wagons could now, with the same quantity of energy and staff, haul the same number of 55-tonne wagons. The idea of an extra shift was abandoned and, thanks to SKF bearings, considerable money was saved each year.