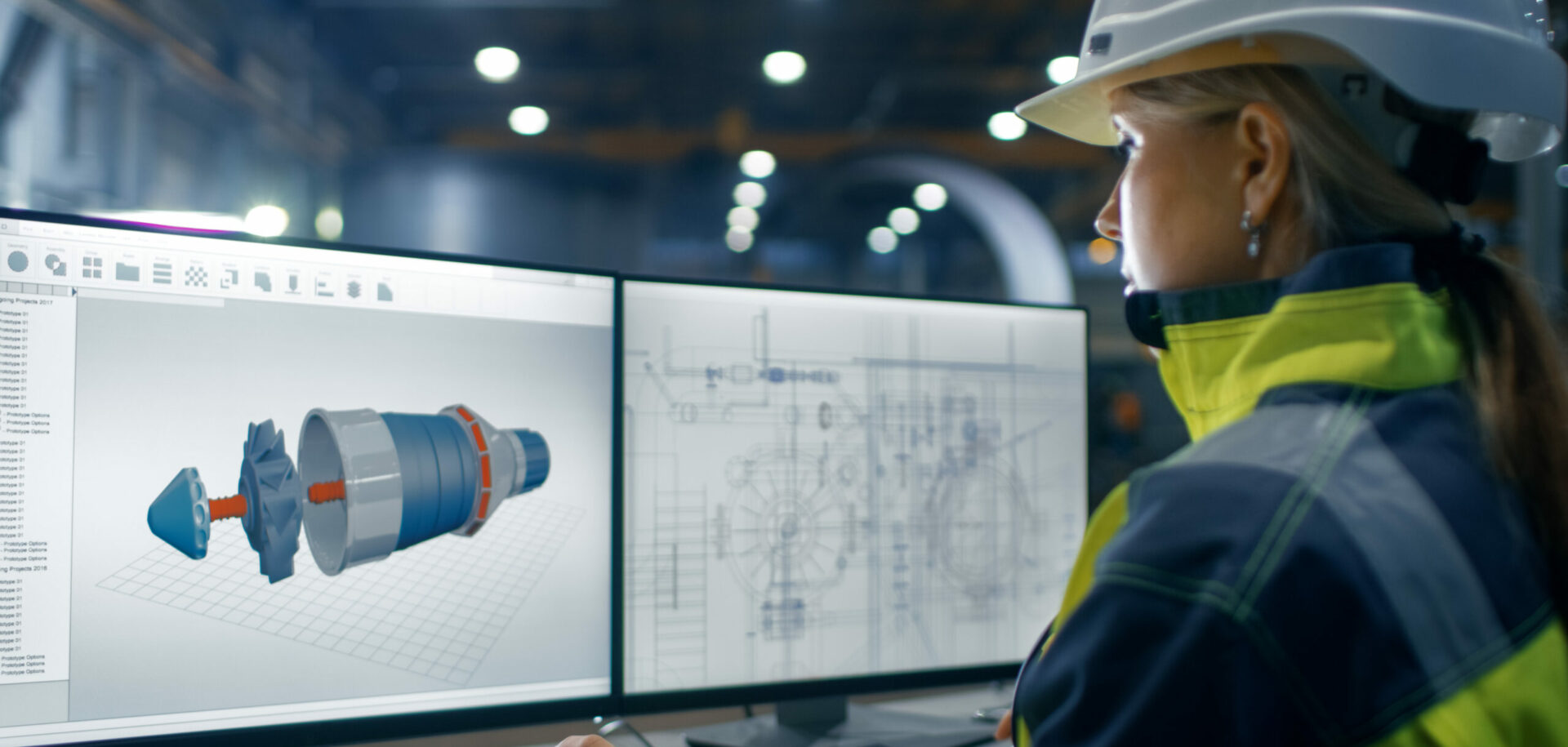
Ovako – a feel for steel
What does a bridge, a windmill, a power tool, a rolling bearing and a rack and pinion steering column have in common? Answer: They could all be made from Ovako steel.
What does a bridge, a windmill, a power tool, a rolling bearing and a rack and pinion steering column have in common? Answer: They could all be made from Ovako steel.
Ovako isa leading European producer of long steel products (bars, wire, bright bars, tubes and rings). These products, further milled, stretched, drawn, cut or rolled, are the backbone of just about every heavy industry in the world.
But for historical reasons, the rolling bearing industry is one of Ovako’s biggest customer segments. And the reason for this, besides the high quality of Ovako’s products, is that SKF owned Ovako in one form or another between 1916 and 2006.
In late 2006, SKF, together with the Finnish steel group Rautaruukki and the Finnish industrial conglomerate Wärtsilä, sold its stakes in Ovako to a company owned by the Dutch Hornbergh Holdings and WP de Pundert Ventures, and Germany’s Pampus Industrie Beteiligungen GmbH & Co. Kg (PIB).
And then, in August 2007, Werner Pampus’ company PIB bought out the Dutch partners for a reported 600 million euros to become Ovako’s sole owner. Pampus also owns another steel company, Westfälische Drahtindustrie GmbH, which specializes in wire, cutting steel and construction steel and which, in turn, is 30 percent owned by ArcelorMittal, the world’s biggest steel company.
So Ovako is in good hands. What was once a company with a complicated ownership structure throughout the years – including the acquisition of other steel mills such as Imatra Steel, Fundia, Forsbacka, Boxholm and Alblasserdam, among others – has now become a focused and specialized steel consortium keeping company with the best of the best.
Today, Ovako hassales of around 1.4 billion euros, 16 steel mills, nine sales offices in Europe and Russia, and a total of 4,300 employees. Annual production of long special steel products, focused on demanding product segments, is about 2 million tonnes. While a majority of Ovako’s steel mills are in Sweden and Finland, the company also has production facilities in France, Holland, and Italy. Ovako is headquartered in Stockholm.
Ovako’s organizational structure is divided into four divisions – bar, wire, bright bar (i.e., shiny), tube and ring.
One of Ovako’s most important steel mills is the Hofors plant, west of Gävle, in middle Sweden, located in the province of Gästrikland.
The Hofors Bruk, as it is called, produces steel tubes, rings and bars in low-alloyed and carbon steels.
Together with neighbouring Sandviken, home of the metalworking tool giant Sandvik, this area of Sweden, with its forests and gently rolling hills, is often cited as the heartland of Swedish heavy industry.
In late 2007,Ovako announced plans to invest upwards of 55 million euros in the Hofors plant by 2010 for, among other things, a new forge, new gas cleaning equipment and a new ring rolling mill. The hot rolling tube programme was also upgraded.
While the community of Hofors is small, the Hofors steel mill is about the size of a large college campus and employs 1,400 people.
There 550,000 tonnes of metal scrap is smelted down on a yearly basis to produce approximately 500,000 tonnes of new steel bars, rings, and tubes, primarily for the rolling bearing and automotive industries.
While the Hofors plant gets about 90 percent of its raw materials from recycled Swedish scrap steel, the other 10 percent comes from a variety of sources.
“The steel industry in general has a bad environmental profile,” says Tommy Lindmark, raw material buyer for the Ovako Hofors plant. “But if you look at the
volumes we recycle, it is easy to change your mind.”
Indeed, the mountains of brown, rusty scrap metal that arrive daily at the Hofors plant, while hard to ascertain their exact origin, look to be made up of parts from trucks, automobiles and trains that otherwise would be left unused.
Scrap metal costsaround 0.20 euros per kilogram. The scrap is carefully screened before smelting in order to make sure to have a proper steel quality at the other end. In general, a rule of thumb in the steel industry is that the cleaner the steel is to begin with, the longer the life of the component made from it will be.
“Our steel is used in everything from high-performance bearings to state-of-the-art diesel fuel pumps, and the quality of the steel has to be top-notch to withstand all the pressures, stresses, fatigue resistance and torques that manufacturers have to deal with,” says Leif A G Johansson, head of development projects at the Hofors plant.
“By carefully controlling all the processes in the mill, and through the use of a number of key technologies, like magnetic induction stirring and vacuum degassing, we can achieve a consistent and accurate composition – steel of the best quality and performance,” he says.
Gearbox capabilities – the gold standard
One of SKF’s key strengths is the capability to work closely with customers to find long-term solutions, taking the process and systems perspective into
consideration.
This approach enabled SKF to tackle the kind of challenges drivelines and gearboxes were increasingly subjected to at the Ovako steel mill in Hofors.
The approach isn’t new. Over the past couple of years, SKF has developed its 18K (18 carat gold) concept gear unit to help OEM customers and users get the most out of their gearboxes.
The 18K concept gear unit exploits SKF’s capabilities and offers advantages at any stage in the driveline or gearbox life cycle: commissioning, repair, renovation, upgrade or during normal operation.
“The 18 carat concept gear unit shows that there are golden nuggets for all of us,” says Hans Kjellberg, SKF key account and segment manager in the Nordic countries.
A vibration story
A steel mill is, to say the least, an aggressive environment for machinery.
Back in 2003, one of the bloom mills at Ovako’s Hofors steel mill was experiencing problems with short service life of the pinion gear, which basically divides the torque to the rolls that do the heavy work of shaving blooms into heavy square or round bars. These require enormous amounts of torque.
“These broke and had to be replaced every three years or so,” says Leif A G Johansson, head of development projects at the Hofors plant. “And they cost hundreds of thousand of euros.”
After some unsuccessful attempts by subcontractors to fix the problem, Johansson contacted SKF for help. “No one looked at the big picture, except SKF,” says Johansson. “We could not have done it without them.”
“After a root cause analysis performed by SKF Nordic Region with the support of SKF Engineering Consultancy Services over a seven-month period, we discovered in add-ition that there were very high vibration and acceleration levels in the whole drivetrain, from the electric motor through the pinion stand and into the drive spindles,” says Hans Kjellberg, SKF key account and segment manager in the Nordic countries. “This caused mill fatigue, bad grip of the blooms and excessive maintenance costs on auxiliary machinery and severely impacted the service life of the bearings.”
The solution involved rebuilding and renova-ting most of the drivetrain over a nine-month period, which is very fast considering the size and complexity of the equipment.
And the advantages are multiple – increased service life of the pinion gear and bearings due to lower acceleration levels, which have decreased from 190 rad/s2 to 30 rad/s2 (a rad/s2 is a unit of acceleration).
In addition, in the four years since the work was done, there has been a drastic improvement in the reliability of all the surrounding equipment.