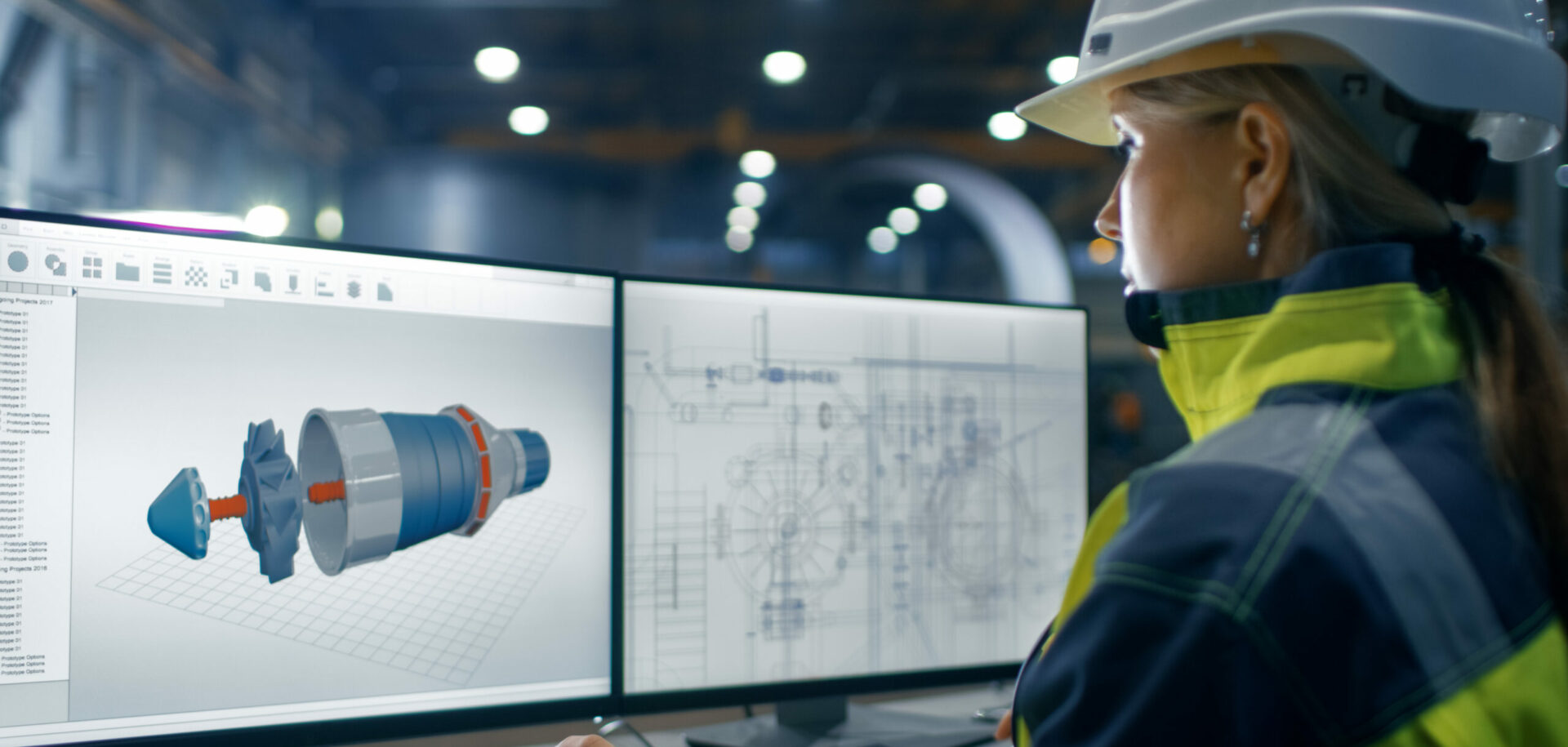
Pass the paper – not the lubricant
Increased workplace safety and fewer production stops are important benefits of a new, improved design for the rope sheave units used in paper machines.
Summary
Stora Enso sales totalled 12.2 billion euros in 2003. The group has some 44,000 employees in more than 40 countries in five continents and an annual production capacity of 15.7 million tonnes of paper and board and 7.4 million cubic metres of sawn wood products, including 2.8 million cubic metres of value-added products.Stora Enso’s Kvarnsveden mill is a modern paper mill situated on the Dalälven River, in the town of Borlänge, in central Sweden. The paper mill was founded in 1900 and during the first five years, no less than six paper machines were put into operation. Today, the mill has an annual production capacity of approximately 710,000 tonnes on four paper machines.The company’s history goes hand in hand with the history of the surrounding community, and many of today’s approximately 900 employees come from families that have been connected to the mill for several generations.The mill’s production is newsprint, improved newsprint and uncoated magazine paper. The focus within each product area is to supply high-quality products tailored to meet the specific requirements of individual customers. The product range is well adapted to suit the majority of printing methods.
Increased workplace safety and fewer production stops are important benefits of a new, improved design for the rope sheave units used in paper machines.
Despite talks of the paperless office and the advent of electronic media, the world is as hungry for paper and printed media as ever before – and the demand has grown continuosly since paper making first began in China around 100 AD, when the basics of the process of turning pulp into paper were first put to use. That the same principles apply today – almost 2,000 years later – testifies to the ingeniousness of the innovation.
One of the world’s leading suppliers of paper is Stora Enso, a global market leader in integrated paper, packaging and forest products. It also has an equally impressive history – at least as far as companies go – as it traces its roots back to the Swedish mining operation Stora Kopparberg, which was founded in 1288. Stora Enso’s paper mill in Swedish Kvarnsveden was founded in 1900 and is constantly refining its production processes and finding new solutions to old problems, sometimes with the help of SKF.
One recent example of a crucial paper machine component that has been modified by SKF to better meet safety and maintenance demands is the rope sheave, which is used to thread the tail of a new batch of paper through the paper machine whenever production is resumed following web breaks or scheduled shuts.
The mechanical parts of a paper machine are subject to tough conditions, given the heat and humidity produced when water in the paper web is removed by loaded pressrolls and steam-heated driers, coupled with the speed at which the paper web moves through the 100-metre-long facility – 1,500 metres per minute or 90 km/h, 24 hours a day. Peter Amundsson, technician at the Kvarnsveden mill, explains that the harsh environment made the ball bearings inside the rope sheave units break down occasionally, forcing a halt in production. Sometimes, the breakdown made the entire unit come off its shaft, falling through the interior of the machine and ending up in the basement, where personnel might run the risk of getting hit.
“While no-one has been injured so far, this is obviously a risk we want to avoid,” Amundsson says. “We have lived with these problems for a long time, so we were really happy when SKF came up with a new design of the rope sheave unit, which makes it impossible for it to break free from the rest of the equipment. Plus, it needs no lubrication for several years.”
The lubrication requirements of traditional rope sheave units were a particular headache in paper production, Amundsson points out: “The need for frequent re-lubrication increases the risk of grease leaking from the rope sheave unit and onto the paper wire, contaminating both the wire and the finished product in the process. Overly generous greasing also leads to a higher risk of bearing breakdown and production interruptions.”
And production stops are costly in an industry as capital intensive as pulp and paper. Amundsson estimates the average cost of one hour’s worth of downtime on a single machine at 4,000 to 8,000 euros.
The new rope sheave unit devised by application engineers at SKF implies a turnaround of the concept, since it features a ball bearing with inner ring rotation instead of outer ring rotation. “The new solution developed by SKF is much better technically, and it’s the kind of bearing arrangment we now want to have throughout all our paper machines, since the one-time lubrication means it’s practically maintenance-free,” says Amundsson.
The redesigned rope sheaves incorporating bearings with inner ring rotation have the advantage of retaining the lubricant more easily.
Consequently, whenever a rope sheave unit on paper machine 11 at Kvarnsveden needs a tune-up, it is sent to SKF, where it is modified in accordance to the new construction. In the last quarter of 2002, the mill decided to go ahead and successively replace units of the older model with the new, improved design.
A single paper machine may contain up to 70 rope sheaves. But where exactly are they situated – and how do they function? Let’s start from the beginning, for the benefit of those who have never entered inside the giant construction that constitutes a modern paper machine. Most people have a rudimentary idea of what pulp is and how it is turned into paper, but we are so used to it that it’s easy to forget that the paper of the magazine you are reading right now originates from a huge tank of slurry that resembles oatmeal and contains 99 percent water and a mere 1 percent fibre.
Consequently, it takes a lot of pressing and drying before the “oatmeal” turns into something fit to print or write on. At the starting point of the production line – called the “wet section” – slurry containing fibre, water and additives such as clay is pumped from a tank and distributed across a fine wire mesh 8 to 11 metres wide, which runs in an endless loop. The water is successively removed by pressure pulses and is filtered through the wire and the paper gradually takes on more solid form. The paper is then pressed between loaded rolls until it is no longer possible to mechanically remove any more water.
Then the first rope sheave goes to work in a process called tail-threading, which means inserting and guiding a tail made up of a 20-centimetre-wide strip of paper throughout the series of steam-heated cylinders that transport the paper web through a number of drying groups, where humidity is successively removed from the paper and the surface assumes desired characteristics. The tail is fastened between two
9-millimetre-thick ropes that run along the entire paper web, hence the name “rope sheave.”
The threading is not required each time a paper roll is finished and leaves the dry end of the production line; rather it is used only when the paper breaks and also following scheduled maintenance shuts. On a bad day, however, the paper may break several times, sometimes due to the condition of the pulp, dirt build-ups or various other reasons. Production must be discontinued in order for a new paper tail to be fed into the loop or when it is time to clean the machine.
The length of a finished paper log varies, but many run to at least 75,000 metres and may weigh in excess of 21 tonnes. The log is cut to the ordered length and width, since each roll is made to order. While the principles of paper making have remained much the same since 100 AD, the scale has certainly changed.
SKF’s solution
A falling rope sheave can easily damage a paper machine but – more importantly – it represents an unacceptable risk of personal injury. In addition, conventional rope sheaves are prone to grease leakage and premature bearing failures.
To virtually eliminate the possibility of personal injury, damage to the paper machine and contamination of the paper due to leaking grease, SKF has developed a new rope sheave unit. This unit, which contains an efficient security locking system, is designed to provide a maximum level of safety. Moreover, this maintenance-free unit is greased and sealed for life to provide superior bearing service life. The seals on this unit were specially selected to protect the bearings from contaminants and to prevent grease leaks.
Safety and security were the reasons why Stora Enso chose the new SKF rope sheave for paper machine 11 in Kvarnsveden, Sweden.
These units, which have been tested under real conditions, provide real solutions for any application where rope sheaves are used.