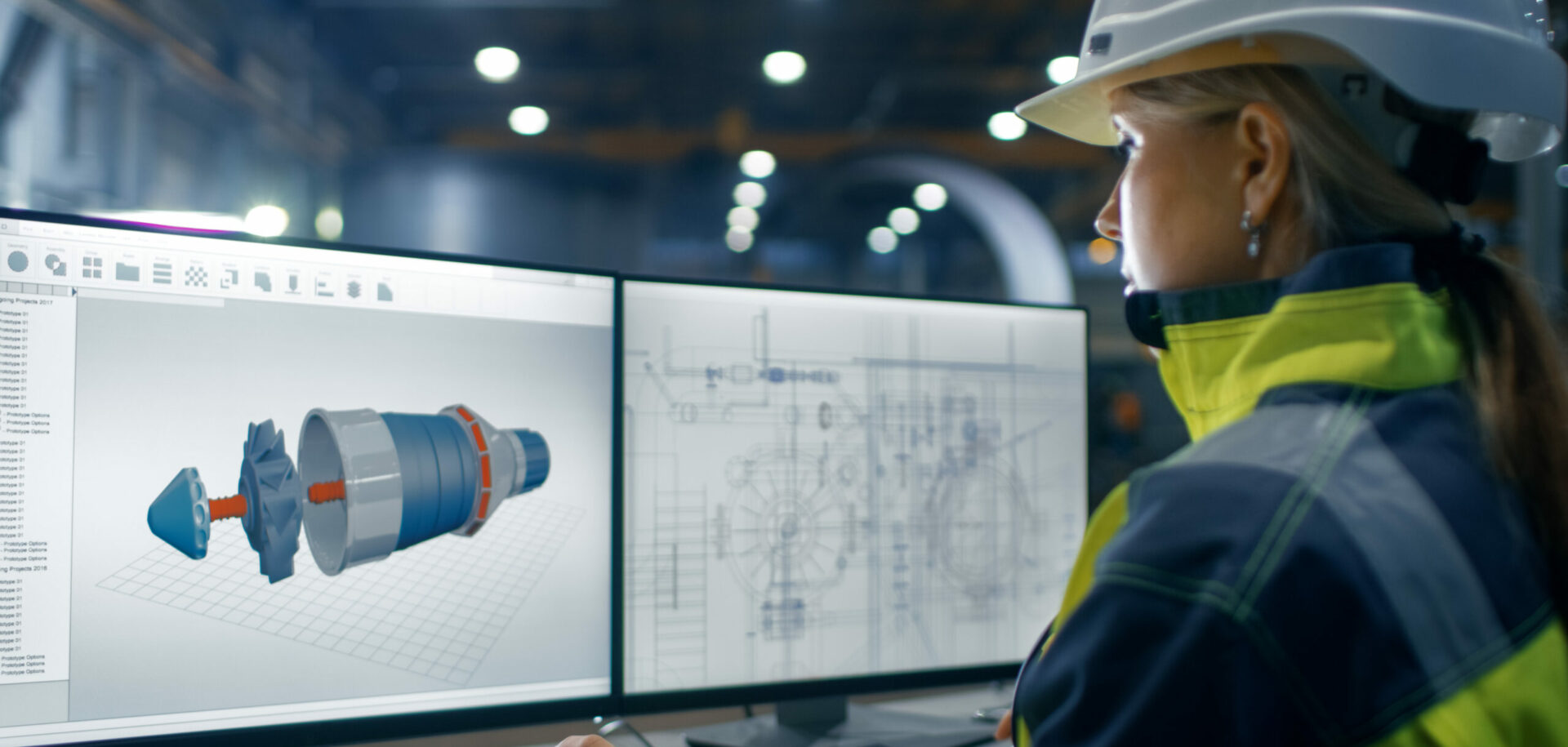
Polymer bearings to the rescue
Only one company responded when Belimed Technik called for help to solve a problem. The solution took the form of polymer bearings.
Only one company responded when Belimed Technik called for help to solve a problem. The solution took the form of polymer bearings.
The high-performancecleaning machines that the pharma-ceutical industry uses to wash glassware, hoses, tubes, containers, fittings and many other types of process equipment are rather like your domestic dishwashers but much bigger. Outside they are up to three times as high, four times as wide and three times as deep as the one in your kitchen. Inside, all gleaming stainless steel, they retain the look of your dishwasher at home, with roll-out racks to hold the dishes and utensils to be cleaned, and rotating spray-jet arms to wash them.
“Equipment cleaning is a vital component of infection control in the pharmaceutical industry and its laboratories, just as in hospitals and other health-care establishments,” says Dieter Henke, Product manager for Belimeds Pharma branch, in Mühldorf am Inn in southeastern Germany. “We have more than 30 years of experience designing and making these cleaning machines. As regulatory requirements for the pharmaceutical industry become increasingly more severe, we work hard to make sure that our machines stay a step ahead of the industry’s stringent demands.”
Belimed launched a new range of cleaning machines, the PH 8xx.2 type, in 2003, partly in response to requests from pharmaceutical firms for machines with greater loading capacity within limited external dimensions. This range comprises five models of different sizes that offer various layout choices and optional extras. All are designed specifically for pharmaceutical process envir-onments, and they meet the latest technical requirements of all major regulatory bodies, including the Current Good Manufacturing Practice standards issued by the US Food and Drug Administration.
In Belimed’s new design, the slide-out racks that hold the equipment to be cleaned originally rested on plain, non-lubricated bearing sheaves that rolled on rails, as in earlier models. Some customers found that when the racks were heavily loaded it took a lot of force to slide them into the cleaning chamber and to pull them out after the cleaning cycle. They complained that loading and unloading operations were simply too hard, especially for female staff.
Lubrication of the sheaveswould have been difficult because grease could leak out from the bearing into the super-clean environment of the washing chamber unless the bearings were hermetically sealed – a solution requiring more space than was available. Redesign of the whole machine was out of the question. So Belimed looked to various sources for a remedy to the problem of the hard-to-move racks. “A lot was at stake for us because machines like these cost more than 150,000 euros,” Henke points out. “We sent requests for help to various potential suppliers with identical descriptions of the problem to be solved, but we got no response at all, except from SKF.
“They reacted promptly and positively,” he says, “and together we got down to developing a solution.”
Jürgen Althammer, who heads development at Belimed Technik, explains the situation. “We pres-ented a tough problem,” he says. “We needed new sheaves that had to have exactly the same dimensions and geometry as the former unsatisfactory ones but that had much lower rolling resistance. They had to retain this feature even at high temperatures, because our machines wash at 85 degrees Celsius, and the drying process is at 120 degrees Celsius. The bearing had to be either hermetically sealed or else easy to rinse out, and the whole part had to withstand exposure to aggressive chemicals, including nitric and sulphuric acids and alkalis such as caustic soda.”
Faced with this set of constraints, SKF developed a customized solution. To reach the maximum load-carrying capacity together with axial guidance in the very limited headroom available, SKF designed a cageless polymer track runner ball bearing with two full-complement, asymmetric sets of stainless steel balls. The rings are made of polyetheretherketone (PEEK). Polymers have a low coefficient of friction, so these bearings do not need lubrication. As there is no cage, the bearings are easy to rinse out – an essential feature in such a critical application. The solution does not require any change of the abutments.
“SKF gave usa perfect function-integrated solution that required absolutely no modifications in the existing machines,” Althammer says, “and they were remarkably fast in developing it. Our first meeting to discuss the problem was in the final days of 2005. Within four months we were testing the first sheaves with SKF’s polymer bearings, and a month later they were being fitted on our machines in pharmaceutical establishments. What’s more, we have not had a complaint since then about hard-to-slide equipment racks.”
SKF’s low-friction polymer ball bearings
Polymers are not as strong as steel; nevertheless, they are useful for ball bearings for several reasons: They are much lighter than steel, they withstand exposure to chemicals and moisture, and they have a low coefficient of friction in the absence of lubrication.
In polymer ball bearings, various poly-mers can be used for the rings and the cage, while balls can be made of stainless steel, glass or polymer. Function-integrated designs are possible. For any given application the combination of materials is chosen to match the operating conditions, which include bearing load, rotational speed, operating tem-perature and chemical exposure.
In the polymer track runner ball bearings SKF supplies to Belimed Technik, the rings are made of polyetheretherketone (PEEK), and the balls are made of stainless steel.