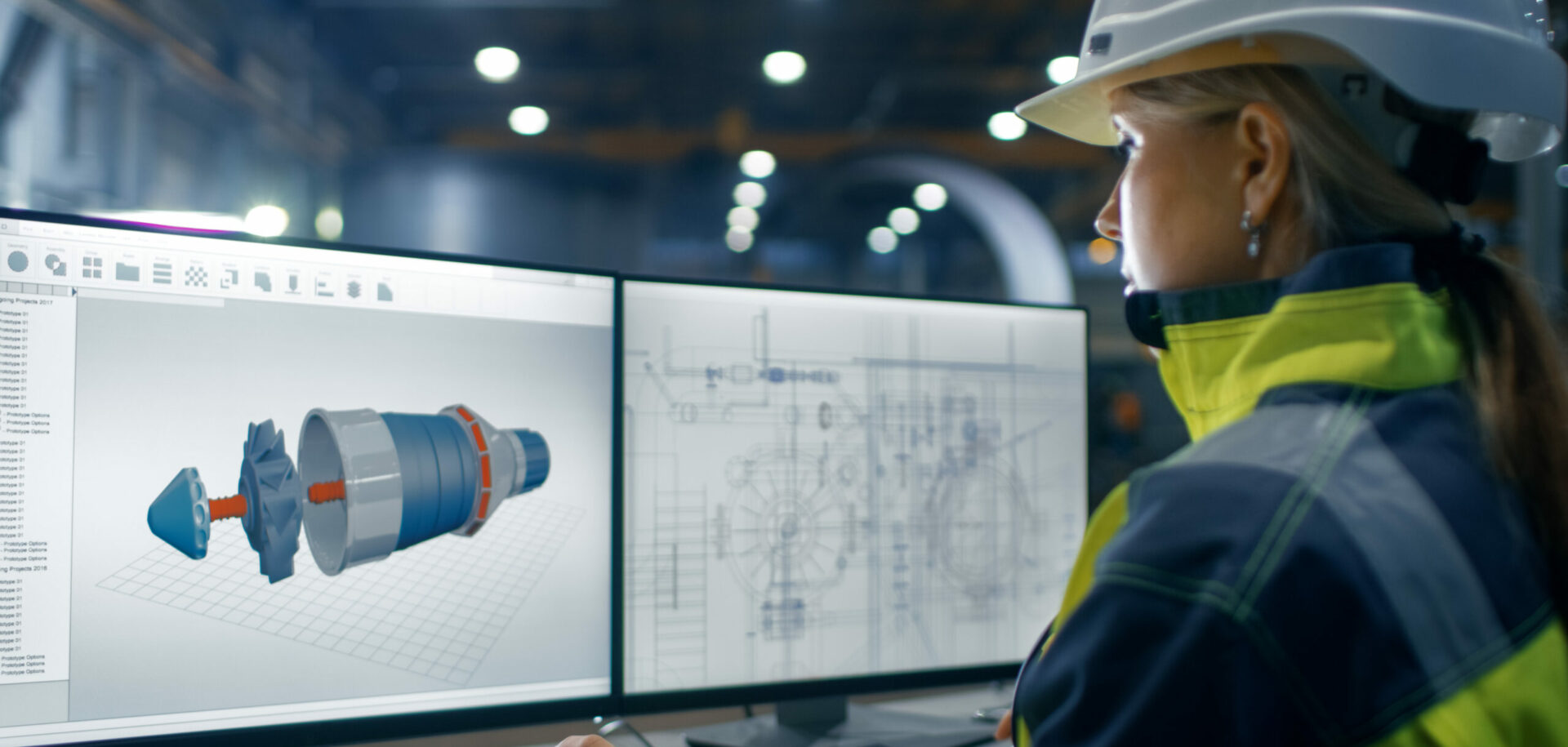
Summary
The latest in bearing technology
When German company DeWind designs a wind power unit, its suppliers are highly integrated in the process. This has some advantages. Since SKF was involved in developing the bearing concept of the entire power train, the bearings could be optimised for their function to an unusually high degree. This was accomplished using SKF software, which calculates which bearings are appropriate on the basis of a unit’s inner contact geometry.
The rotor for DeWind’s one-megawatt unit is carried on an SKF 230/630 CA spherical roller bearing. SKF bearings are also used in the gearbox. Some of them feature a loose guide ring, centred on the inner ring, which allows for a favourable distribution of the internal bearing loads.
The gearboxes from Jahnel-Kestermann (JaKe) employ some of the most recent SKF developments. They are cylindrical roller bearings with the new ML cage, which has improved resistance against vibration, and CARBTM toroidal roller bearings, which will be used a the non-locating bearings on the gear shafts in the 600-kW unit.
As offshore wind parks become the norm, new challenges will arise and the need for remote control and monitoring will grow. SKF and JaKe are working together on sensors to measure untoward vibrations that will damage the gearbox. In the case of other problems, self-learning software can go through a series of options and determine which is the right one to use to put the matter right.
When DeWind of Germany designs a wind power unit, the company’s suppliers become deeply involved in the process. The result is the optimal selection of components.With the prospect of offshore wind parks, wind power is moving into the big leagues. Until recently European wind parks have been situated on land, and for environmental reasons they have been fairly small-scale operations. Wind power generator manufacturers had to concern themselves with limiting the intrusiveness of their windmills so that the neighbours wouldn’t complain.
Now the race is on to find ever larger, ever more efficient generators that will make the high cost of building foundations and infrastructure off shore profitable. Most of the manufacturers are working on designs for units of 2.5 to three megawatts, which is a big step up from the current range, where one megawatt is big and 1.5 megawatts is gigantic.
DeWind of Lübeck, in the windy north of Germany, is no exception. It’s a relative newcomer in the field, having been founded only three years ago with a staff of five. It started with a 600-kilowatt unit. Now it has introduced a one-megawatt unit and is in the process of developing a three-megawatt unit. All of these are variable-pitch, variable-speed units, which, in conjunction with the dual-feed generator with its inverter, have the important advantages of limiting stress on the rotors and providing a smoother and more reliable supply of current to the grid, starting from low wind speeds. In each case, the basic design is adaptable for different wind circumstances, using varying rotor sizes and generator profiles to take best advantage of prevailing conditions.
Hugo Schippmann, managing director of DeWind, describes the company’s way of working as a coordinated effort using the expertise and experience of the partners it has chosen. Schippmann says DeWind recognises that bearing or gearbox manufacturers may well know more about their particular field than DeWind does itself, and thus it makes sense to use that knowledge. So instead of designing a windmill and telling others to build it, DeWind asks others to help it design the windmill, and, says Schippmann, ends up with a better product – more efficient and better value for the money than the competition.
Take the development of the one-megawatt unit. The company knows what the loads are at the rotor hub. It gives them to the manufacturer of the main rotor bearing. The manufacturer then finds a solution whose values DeWind applies to the propeller shaft. Those loads in turn are given to the gearbox manufacturer, who works out how the gearbox should be built. Then the same process moves on to the generator. The various proposals are coordinated by DeWind until a solution has been found that turns the whole assembly into a single machine.
The right partners
DeWind also carries this principle into the production phase. It doesn’t make the unit itself, but has it made by Krupp Fördertechnik’s Lübeck factory.
But for DeWind to work in this cooperative fashion, it needs partners who will play along. Among them are the gearbox manufacturer Jahnel-Kestermann of Bochum and SKF.
Jahnel-Kestermann (JaKe) is the sole supplier of gearboxes for DeWind’s 600-kilowatt unit and one of two suppliers of the gearboxes of the one-megawatt unit. The company is known for its innovative approach to gearbox design. One example is its huge, one-off gearboxes, such as that for one of the world’s largest dredgers. Wind power has become an ever-more important part of the company’s work. In 1997, 15 percent of turnover was from the wind industry; in 1998 it was about 30 percent, and in 1999 it will grow even more, as a result of a contract with the Danish wind generation company NEG Micon.
Although some prominent and very successful companies build excellent windmills without gearboxes, both Demtröder and Schippmann are convinced that the use of a gearbox has advantages that are not to be overlooked. Firstly, it allows the generator to be kept small, so that it can be sealed against the elements. Secondly, the whole unit ends up lighter, resulting in lower costs and greater efficiency in relation to the area swept by the rotor. And thirdly, it means the unit can be dismantled more easily, which is especially important for offshore maintenance. The three-megawatt unit will have a built-in crane, so that the gearbox or generator can be dismounted and lowered onto a service ship. That will minimise the use of floating cranes, which are expensive.
Gearbox specialist
Jens Demtröder, JaKe product manager for wind power, says the company specialises in exactly the kind of work that DeWind requires. “A company doesn’t need to give us drawings,” he says. “Give us the parameters, and we’ll build the gearbox. After all, we have 15 years of research and development behind us.” JaKe designed the 600-kilowatt gearbox from scratch, and, says Demtröder, it was a pleasure to have DeWind as customer. “Usually a company wants a product that emerges from its previous products. Since DeWind was a new company, we had a blank piece of paper, and they were very open to new ideas.” The result was an elegant windmill that won the Industrie Forum Design Award at the Hannover Fair in Germany in 1997.
JaKe didn’t have such a free hand in the case of the one-megawatt unit, says Demtröder, since JaKe had to fit its solution into a casing designed by another company. But, he says, they were still able to introduce some of their own ideas into their version.
JaKe has the same attitude towards its bearing supplier as DeWind has towards its gearbox supplier. “We send our suggestions for bearings to the manufacturer, and they usually come back substantially changed,” Demtröder says. “After all, they know more about bearings than we do.” That’s how it was with SKF and the one-megawatt gearbox. Werner Göbel, who’s the wind power specialist at SKF Schweinfurt, and his colleague Stephan Buch from the gearbox application team call this the wave of the future. “It’s still often the case with other customers,” says Göbel, “that we simply get an order for bearings, and we may not really even know precisely what the total context is in which those bearings will be used.”
SKF supplies 90 percent of the bearings for the one-megawatt unit, as direct supplier to DeWind for the main rotor bearing and the blade pitch bearings, and as supplier to JaKe for the gearbox. As a result, Göbel and Buch have been able to consider the entire power chain, from wind to generator, as one process: “We can ensure a proper balance between the characteristics of the individual parts against the characteristics of the whole,” says Göbel.
This way of working has the advantage that it combines expertise and experience with a view to producing a product that is better than any one of the partners could produce on their own. Its disadvantage is that one could end up with a series of insular solutions to separate problems. That’s where DeWind has to provide the synergistic input. It has to coordinate the debate, to ensure that each partner does not just answer its own questions, but provides a contribution to the main challenge of providing the best solution to the customer’s needs.
Michael Lawton
a journalist based in Cologne
photosThomas Müller and DeWind