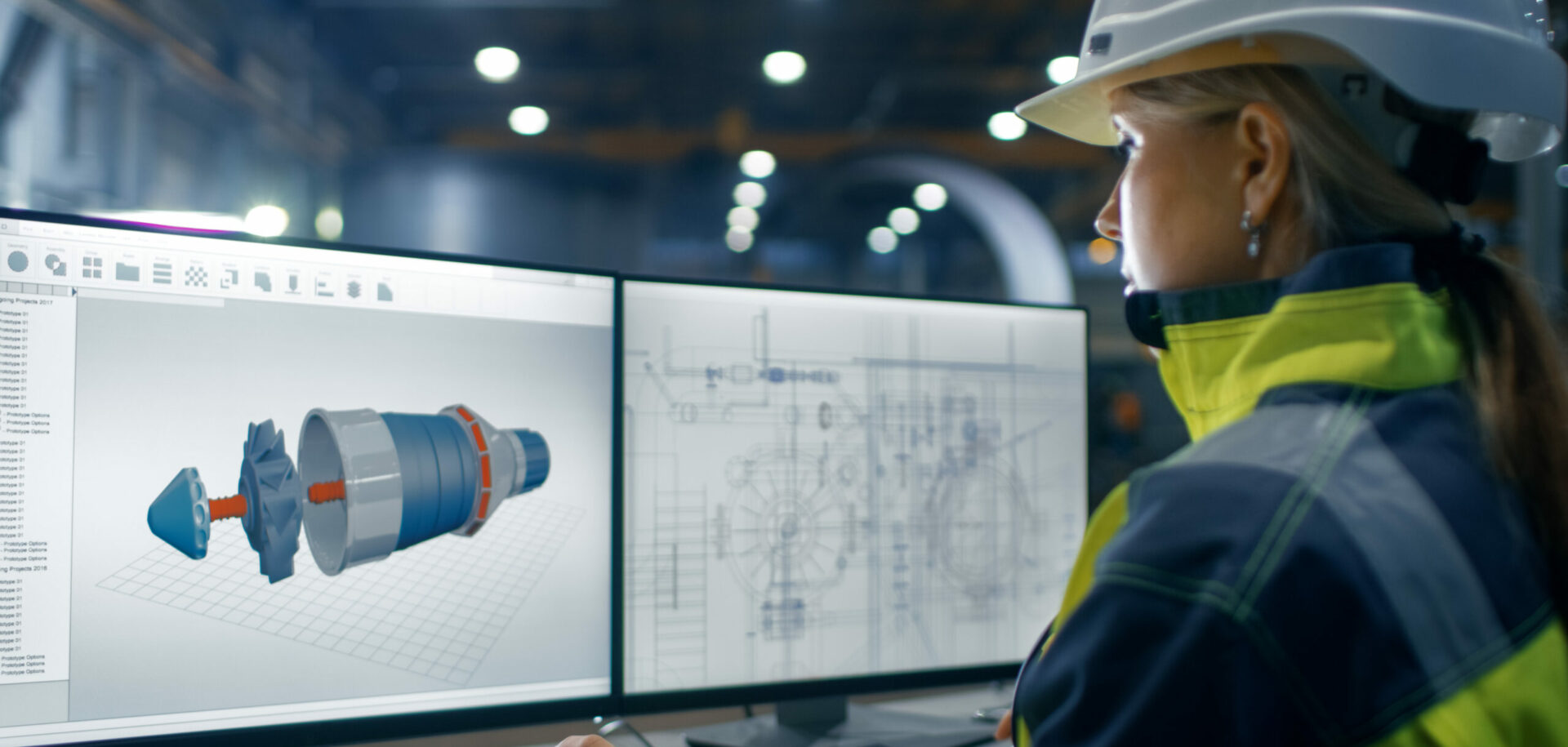
Pumping for survival
This is where Saudi Mechanical Industries of Riyadh comes in. SMI was founded in 1982, initially to import and assemble components for the technology-heavy water pump and gear drive elements of pump stations and to manufacture the stations’ more straightforward pipe, tube and shaft sections. Since then, however, SMI has used its experience to transform itself into a pump station manufacturing power in its own right.
Summary
It’s all in the numbers, and a right-angle gear drive in operation is subject to all sorts of numbers.
Central to the gear drive are a minimum of five SKF angular contact bearings and ball thrust bearings. Bearing types are single and double row angular contact ball bearings and spherical roller bearings.
Hanging below the bearings is a column shaft anywhere from 30 to 440 metres long, connecting the gear drive to a 1.5 tonne pump. During operation, forces exerted upon these bearings are phenomenal.
The weight of the shaft (as much as five tonnes), stretch factors and the power of water thrust in the opposite direction all inflict force on the bearings.
Bearings in an agricultural gear drive, which rotate at 1,750 revolutions per minute for an uninterrupted 90-day season, have to operate flawlessly for more than 226 million non-stop revolutions. In a climate where daytime highs top 55 degrees Celsius, and the spread between day- and night-time temperatures can exceed 40 degrees, it’s little wonder that the bearings are key to the reliability of the entire gear drive.
Samir Kalisse is SKF’s regional technical manager. He is based in Cairo, but visits Saudi Arabia every six weeks.
“In any given 12-month period, SKF supplies over 40 tonnes of bearings and seals to SMI, shipped direct from Antwerp (Belgium) in 20-foot containers,” Kalisse says. “We work very closely with SMI to ensure that supply issues never interfere with their production schedules and that every aspect of SMI’s demand for top-quality bearings and seals is satisfied.”
The history of manufacturing is peppered with case studies illustrating the immutable power of market demand and showing how demand for a product can shape, situate and drive the production of goods within a geographically distinct market.
Saudi Arabia is a land of climatic extremes. Rainfall is scarce, there are no permanent rivers or lakes, and only 1 percent of the country’s 2 million square kilometres is arable. For this reason, the pumps and gear drives that draw water from far beneath the ground are fundamental to survival in large sections of the country.
This is where Saudi Mechanical Industries of Riyadh comes in. SMI was founded in 1982, initially to import and assemble components for the technology-heavy water pump and gear drive elements of pump stations and to manufacture the stations’ more straightforward pipe, tube and shaft sections. Since then, however, SMI has used its experience to transform itself into a pump station manufacturing power in its own right.
SMI did its homework before selecting this business area. If ever a market and its environment were created to drive the development of pump stations, it is Saudi Arabia. The capital, Riyadh, gets only 80 millimetres of rainfall annually, and huge swathes of the country get considerably less.
For Saudi agriculture to exist at all, irrigation is essential, and farmers must draw the water for this irrigation from the deep underground. They do that via pump stations. Today, throughout Saudi Arabia, some 25,000 pump stations are in operation.
The stations are powered by diesel engines that put out as much as 450 kilowatts. The wellhead contraption is a precision-engineered right-angle gear drive that converts the horizontal rotation of the diesel’s crankshaft to rotation in a vertical plane, which powers the pump at the bottom of the well, anywhere from 60 to 440 metres below ground level.
In rural Saudi Arabia, a single pump station can be used for the irrigation of 250 hectares of farmland. But this places extraordinary demands on the station, which may produce as much as 10,000 litres of water per minute – 24 hours a day, seven days a week, for an agricultural season lasting 90 days or more. And this takes place in a climate where daytime temperatures routinely hit 55 degrees Celsius.
In Saudi Arabia, 15 percent of the country’s 23 million inhabitants live outside urban areas. The more isolated inland townships, far from the desalination plants of the bigger cities, are entirely dependent upon pump stations, not only for agricultural irrigation, but also for all their water needs.
Dependability a necessity
“In irrigation uses, as in all our pump and gear drive applications, quality and reliability are everything,” says SMI’s operations manager, Randy Birkelbach. “Consider that, in a 55-degrees-Celsius climate, a breakdown of the water supply for only one day will result in the complete loss of a farmer’s 250-hectare crop. Our machinery has to be utterly dependable.” All the more so when many pumps are installed 100 or more kilometres from the nearest large town and are accessible only by four-wheel-drive vehicles.
Nowadays SMI is involved in the manufacture of the entire pump station. At the wellhead is the crucial right-angle gear drive, manufactured under license from Johnson Gear of the United States.
In its early days, SMI imported the gear drives in component form and assembled them; today, it manufactures the entire drive, using raw materials from Saudi and abroad. Getting to this stage, Birkelbach says, has required extensive commitment to the future as well as considerable
investment.
“We could never have achieved this without investing heavily,” he says. “The build-up of advanced facilities, the introduction of cast iron and bronze casting operations, and the installation of computer numerically controlled manufacturing equipment have all been essential to our progress.” The company now conforms to ISO 9002 and has implemented a complete quality management system throughout its operations.
At the underground end of the Vertical Turbine Pump station is the pump itself, manufactured by SMI under licence from US-based National Pump Company. Because of the depths at which the pumps operate, SMI’s pumps have a number of stages, each comprising a pump bowl and impeller.
A typical 300 millimetre SMI pump may have up to 18 stages. In the world of pumps, this is extraordinary; in other countries, four or five stages would be normal. The pump alone, not taking into account the column shaft (which SMI also manufactures) that connects it to the gear drive above, can weigh in excess of
1.5 tonnes.
At the Riyadh factory, SMI produces around 5,500 gear drives and 1,500 pumps per year. An increasing number of these are destined for markets in the Middle East, Europe and the United States.