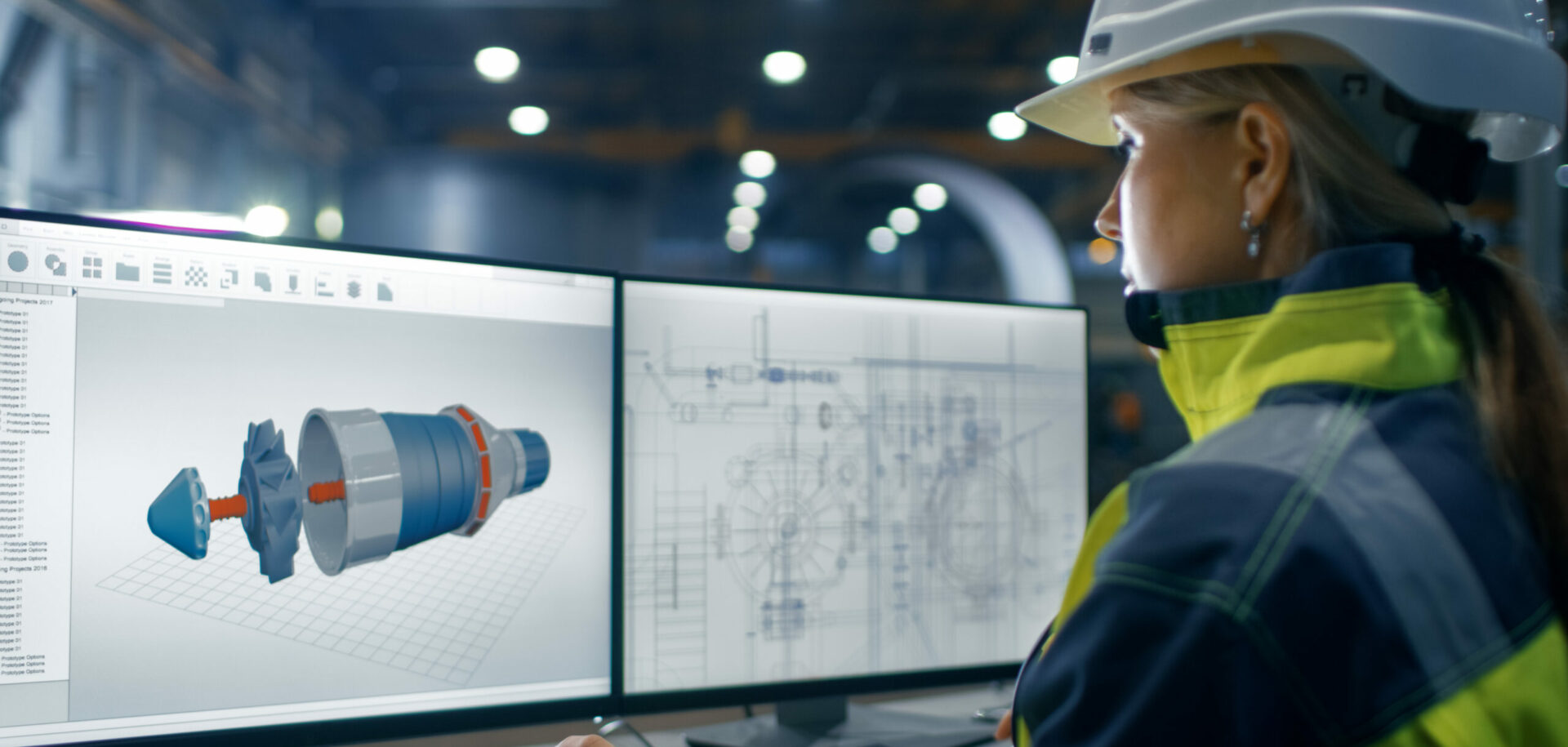
Re-engineering the hub unit and halfshaft
Vehicle component manufacturer GKN, and SKF have created a compact combined hub unit and halfshaft. This is in response to vehicle designers’ desire for further weight reduction coupled with modular design concepts.
Vehicle corner assemblies comprise many elements: wheel and tyre, springing, damper, bearing arrangement and, for a driven corner, an articulated halfshaft. GKN is the dominant world player in articulated halfshafts; all major constant velocity (CV) joint designs found on modern vehicles have been developed by GKN. Similarly, SKF has been the leader in integrated wheel bearing technology since the earliest developments in the late 1930s.
The intimate relationship between a halfshaft’s outboard CV fixed joint and the integrated wheel bearing (hub bearing unit) had not escaped notice. A joint development project was established between GKN Automotive Driveline Division and SKF Automotive Division to look at opportunities for re-engineering the hub unit and halfshaft to create a single hub halfshaft module . The result of this work – the Compact HHM – was presented to the public for the first time at the 1999 IAA Motorshow in Frankfurt, Germany.
Focus on modules
Developments in sub-systems and modules and the continual sharp focus on weight reduction defined the overall direction this development project would follow. While sub-assembly supply and module approaches to vehicle assembly have been heralded for several years in motor-industry trade publications, it is only in the past 18 months or so that the change has really been seen on any large scale in vehicle manufacturing plants. This approach, with the added flexibility it allows in assembly regimes, has provided new avenues for the project team to explore.
Reduction in vehicle weight has been a constant goal driving vehicle designers for years. As vehicle economy and vehicle emission levels have become more important, this focus has intensified. While overall vehicle weight is important, reductions in unsprung weight are as crucial as ever in promoting good vehicle handling and ride characteristics.
Most of today’s cars are front wheel drive. Packaging the suspension, steering and drive arrangement in a vehicle’s front corner assembly is an extremely complex engineering compromise. Designers welcome any additional flexibility offered in this area.
The development was driven by certain requirements – how to reduce weight, how to take advantage of the new opportunities in vehicle assembly techniques and the additional flexibility that could be offered to the designers of driven corner assemblies.
Weight reduction
A new interface between the halfshaft’s CV fixed joint and the hub bearing unit has been created. Current practices in CV fixed joint to hub bearing unit attachment, with stub shaft and elongated bolt or nut, add weight to the corner in the critical un-sprung area. The Compact HHM removes this additional weight by improving the connection between the hub bearing unit and the CV fixed joint. The connection is made by a large diameter spline and circlip or by permanent attachment relying on an orbital-formed closure.
Ride quality and overall vehicle dynamics are all strongly influenced by what may seem to be only small reductions in unsprung weight. In a re-engineering exercise incorporating the Compact HHM on a mid-class front wheel drive saloon, more than three-quarters of a kilogram was saved on the front corner assembly. On the rear driven wheels of a large sedan, the weight savings were more dramatic – almost five kilograms were saved in the bearing and halfshaft assemblies alone.
The complete package of hub bearing unit, CV fixed joint, interconnecting shaft and CV plunging joint is available in non-detachable and detachable variants. The Compact HHM has been tested against rigorous standards, using the extensive test facilities available at both companies’ engineering development centres. Additionally, both the non-detachable and detachable variants of the Compact HHM have been road and proving ground tested in a broad range of vehicle types, including extensive NVH (noise, vibration and harshness) assessment. While the interconnection between CV fixed joint and hub bearing unit is novel, the technology employed for the CV joints, the interconnecting shaft and the hub bearing unit are proven state-of-the-art designs, employing the recognised skills of the two collaborating companies.
Reduced maximum working angle
Few if any of today’s front drive suspension designs allow for optimum positioning of the CV fixed joint centre and the kingpin index. Every millimetre closer to the optimal position that the CV fixed joint centre can be positioned relative to the kingpin index provides the designer with greater freedom to resolve the suspension and steering system packaging within the vehicle’s platform. This benefit can be exploited in one of three ways.
- Use of a CV joint with a reduced maximum articulation angle, without penalty on the application’s minimum turning circle.
- Full optimisation of the halfshaft length and plunging joint travel length.
- Reduction of the minimum turning circle. (Providing the suspension and steering arrangement has the freedom.)
Arrangements that could incorporate reduced angle CV fixed joint designs would also offer possibilities for further weight savings, as the joint would be a more compact unit.
The service life of a hub bearing unit is strongly influenced by the maintenance of the initial bearing assembly preload during vehicle life. The Compact HHM maintains this preload with a much higher precision than is achieved when the clamping forces rely on the elongated bolt or a nut retention acting on the CV fixed joint’s stub shaft. An orbital-formed closure of the hub bearing unit frees the CV joint from its traditional clamping role. This clamping system together with the optimisation of the hub bearing unit’s internal structural design provides significant gains in stiffness and guarantees that this stiffness will not deteriorate during the vehicle’s life. Current state-of-the-art practices in the manufacture, lubrication and sealing of both hub bearing unit and halfshaft joints mean that the Compact HHM will normally provide a life longer than the vehicle to which they are fitted.
Full optimisation
Today’s vehicle production routines follow a wide range of approaches in bringing the various sub-assemblies together to make a complete vehicle. The detachable variant of the Compact HHM provides all the flexibility of assembly and servicing offered by today’s solution, while retaining improved weight and overall axial compactness in the hub bearing unit and CV fixed joint assembly.
The fully integrated design, where the CV fixed joint is permanently attached to the hub bearing unit optimises the design further. Weight reduction is at its maximum and CV fixed joint position relative to kingpin index and tyre contact centre can be optimised, and several design approaches have been fully vehicle tested with this fixed approach.
As the trend towards modular systems solutions becomes ever stronger, re-engineering is taking place not only in vehicle design but also in production and assembly techniques. The advantages offered by the non-detachable Compact HHM is such that a wide-ranging review can go far beyond just the halfshaft and hub bearing unit.
Greater freedom
The interplay between the driven wheel assembly, suspension and steering arrangements is extremely complex. The designer has to pay careful attention to the complete suspension, steering system and driveline to minimise dynamic changes of forces to the steering linkage. The Compact HHM can help reduce unfavourable conditions by providing greater packaging freedom.
Separately, GKN and SKF hold worldwide patents on many aspects of halfshaft, CV joint and hub bearing unit designs. Specific patents cover the connection method and snap-ring system that are features of the Compact HHM’s design.
David Worth
SKF Automotive Division, UK