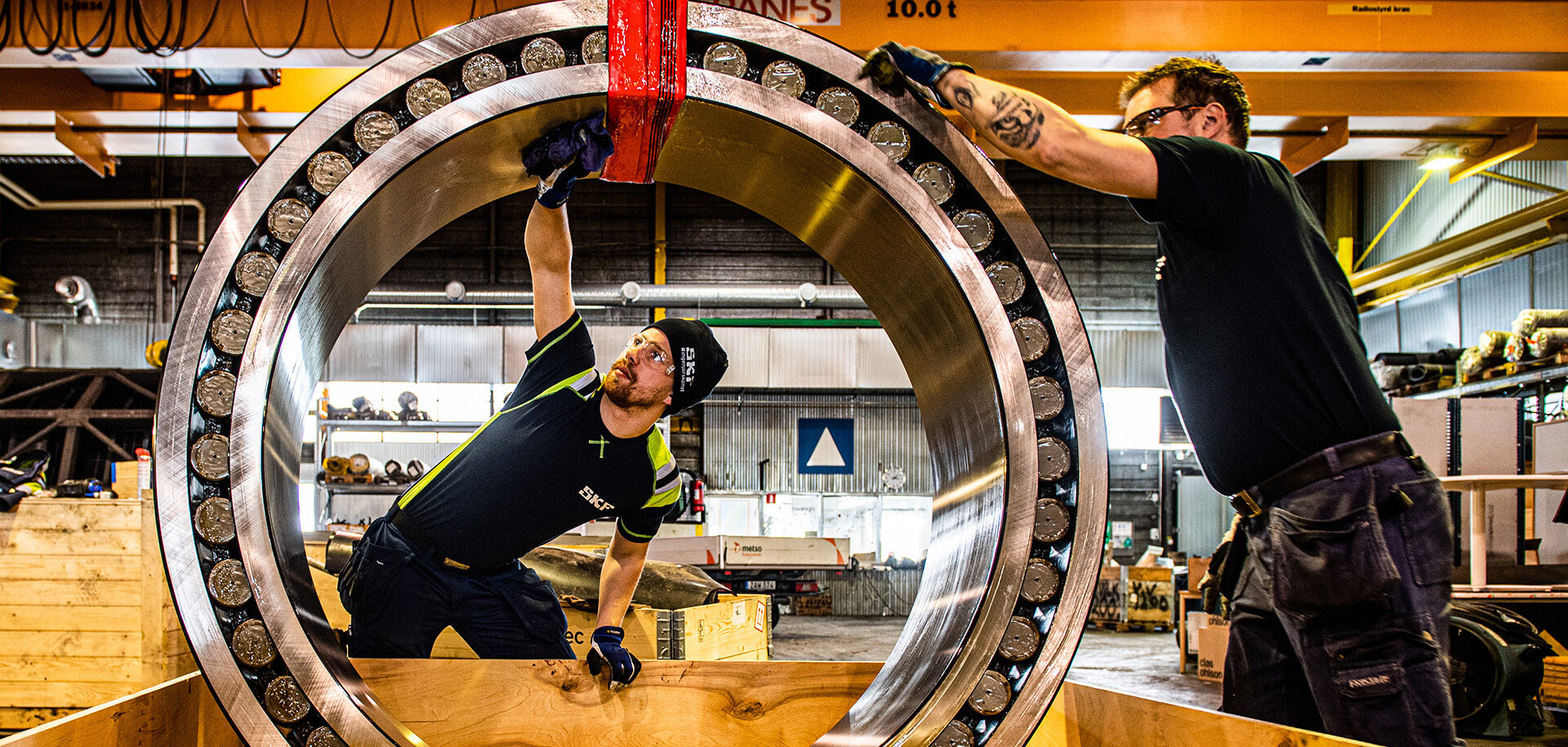
Remanufacturing – a growing trend
More and more manufacturers are turning to remanufacturing to significantly contribute to their sustainability and circularity goals. With this trend comes an increased demand for remanufactured bearings.
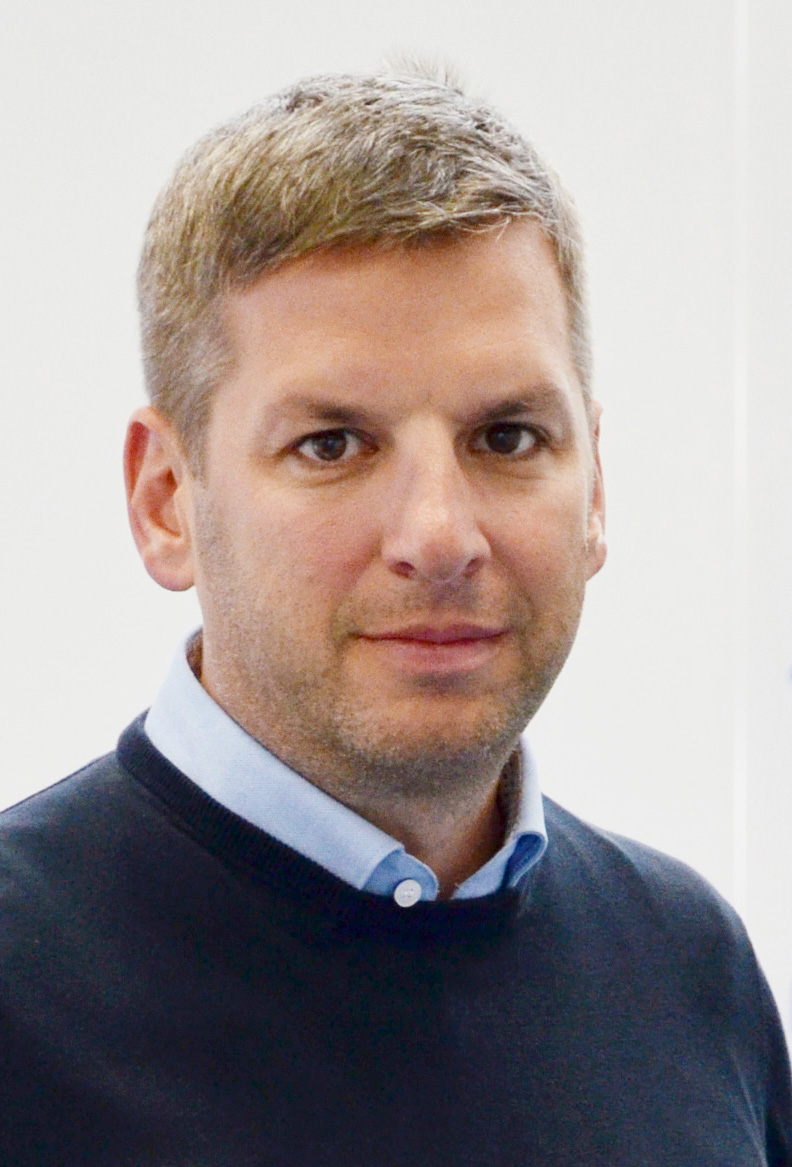
business unit manager,
SKF Industrial Services
Centre in Steyr, Austria.
The demand for remanufactured bearings is constantly growing. Initially the driving forces were the need for lower costs and shorter lead times. Today, however, sustainability and circularity goals contribute to the demand.
Hannes Leopoldseder, business unit manager of the SKF Industrial Services Centre in Steyr, Austria, one of SKF’s more than 15 remanufacturing centres around the world, points out that remanufacturing of bearings is not a new process; in heavy industry it has been a practice for 25 years.
“There is a trend for some industries more than others to adopt bearing remanufacture to improve sustainability and embrace circularity,” says Leopoldseder. “However, in almost all cases, it tends to be those manufacturers or operators where the goals of sustainability are already top of their agenda who have a greater acceptance of bearing remanufacture and who act the quickest.
“In these companies we find we are engaging with new contact people,” Leopoldseder says. “Not just buyers and engineers, but also those who oversee sustainability. Their KPIs are not necessarily financial but connected to a company’s carbon reduction and circularity.”
The demand for remanufactured bearings is constantly growing. Initially the driving forces were the need for lower costs and shorter lead times. Today, however, sustainability and circularity goals contribute to the demand.
Hannes Leopoldseder, business unit manager of the SKF Industrial Services Centre in Steyr, Austria, one of SKF’s more than 15 remanufacturing centres around the world, points out that remanufacturing of bearings is not a new process; in heavy industry it has been a practice for 25 years.
“There is a trend for some industries more than others to adopt bearing remanufacture to improve sustainability and embrace circularity,” says Leopoldseder. “However, in almost all cases, it tends to be those manufacturers or operators where the goals of sustainability are already top of their agenda who have a greater acceptance of bearing remanufacture and who act the quickest.
“In these companies we find we are engaging with new contact people,” Leopoldseder says. “Not just buyers and engineers, but also those who oversee sustainability. Their KPIs are not necessarily financial but connected to a company’s carbon reduction and circularity.”

New centre in northern Sweden
In 2020, as a response to this trend, SKF established its first Circular Economy Centre in Gothenburg, Sweden. It’s a local unit enabling circular solutions close to the customers. The demand for the centre’s services increased by a factor of four over just two years, and in April 2022 the company broke ground for a new centre in Kiruna, in northern Sweden.
Leopoldseder says the choice to remanufacture rather than buy new often requires a change of mindset. “I see the move to remanufactured bearings picking up, for sustainability reasons,” he says. “The remanufacturing process has huge potential.”
More standards are being put in place by global and national governing bodies to improve manufacturers’ sustainability, and these will accelerate remanufactured bearing use. However, says Leopoldseder, it has to be a joint movement, based not just on standards but also on customers’ demand for more sustainable options.
“Increasingly, buyers consider not only if a product is manufactured in a sustainable way but also if at the end of its life there is a sustainable means of disposal and if its components can be reused,” he says. “This will move us from a linear economy based on take, make and consume, to a circular economy based on reduce, reuse and recycle.”
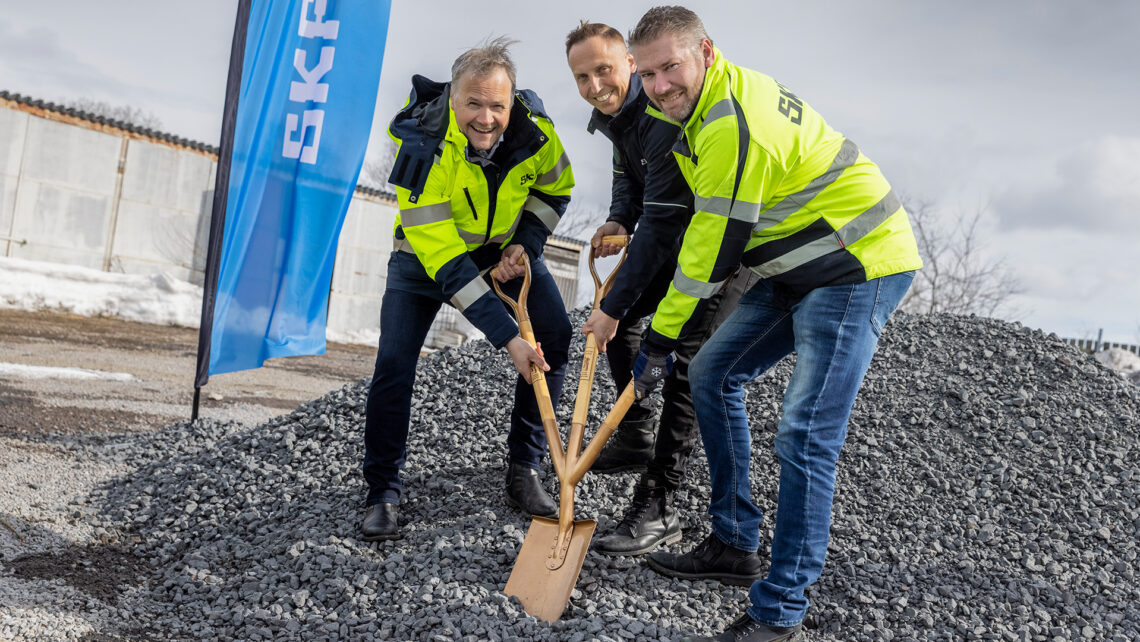
Remanufacturing of turbine bearings
The wind industry is one of the newer industries to turn to remanufacturing, in this case turbine bearings.
“With its focus on sustainability this shift by wind energy producers is understandable,” says Leopoldseder. “Although the industry has for many years used remanufactured components such as electronics and plates, the use of remanufactured bearings has lagged behind.
“Wind turbines have evolved, grown in size and increased in service life and are now undergoing additional maintenance,” he says, “so remanufactured bearings have become more viable.”
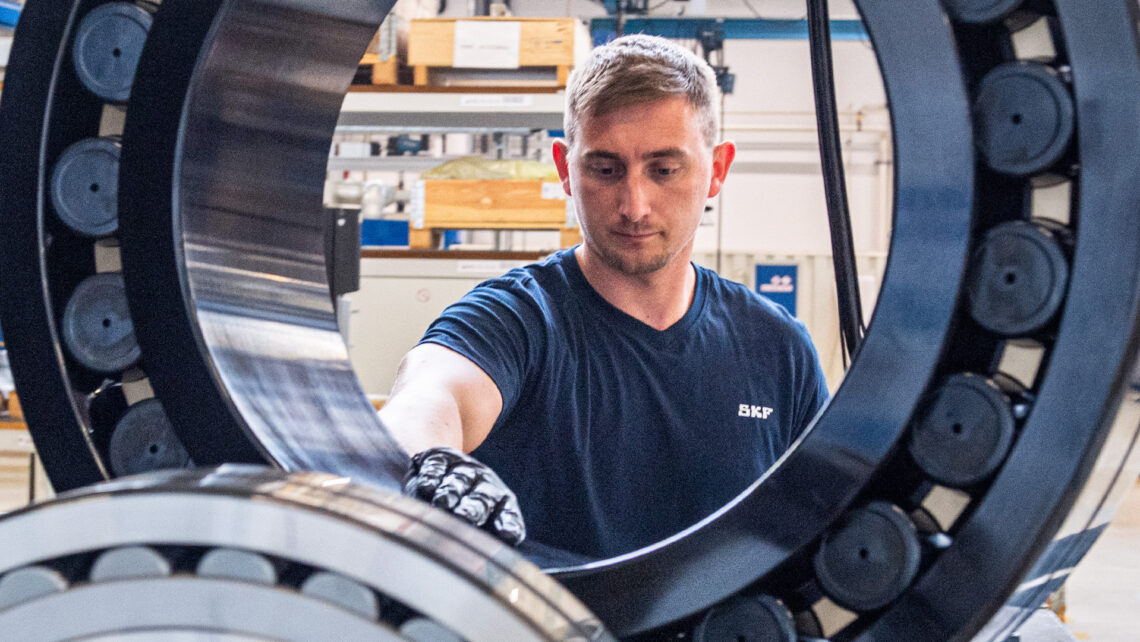
Heavy industries driving the trend
Early adopters of remanufacturing have been those manufacturers who traditionally have high CO2 emissions and are under the most pressure to reduce them.
I see the move to remanufactured bearings picking up, for sustainability reasons. The remanufacturing process has huge potential.
Hannes Leopoldseder, business unit manager, SKF Industrial Services Centre in Steyr, Austria.
“You would perhaps think that such manufacturers would look for the big savings, but for those in heavy industries such as mining, metal and cement production every saving adds up,” Leopoldseder says. He cites a couple of success stories within the steel industry.
SKF has been working with one steelmaker for more than 10 years and has remanufactured more than 39,000 bearings used in continuous casting machines (CCMs), he explains. Remanufacturing has helped the company reduce CO2 emissions by more than 65 tonnes per year and has led to zero equipment failures due to bearings, at the same time cutting annual costs associated with CCM bearings by an average of around 500,000 US dollars.
Another steel company wanted to reduce its CO2 emissions by a third. It looked at prominent emission generators, such as its blast furnaces, but focused on making reductions everywhere it could.
The company’s slab caster machines require the replacement of about 2,000 bearings each year. Remanufacturing half of these each year saves 10 tonnes of steel and some 62,000 kWh of energy and eliminates almost 30 tonnes of CO2 emissions.
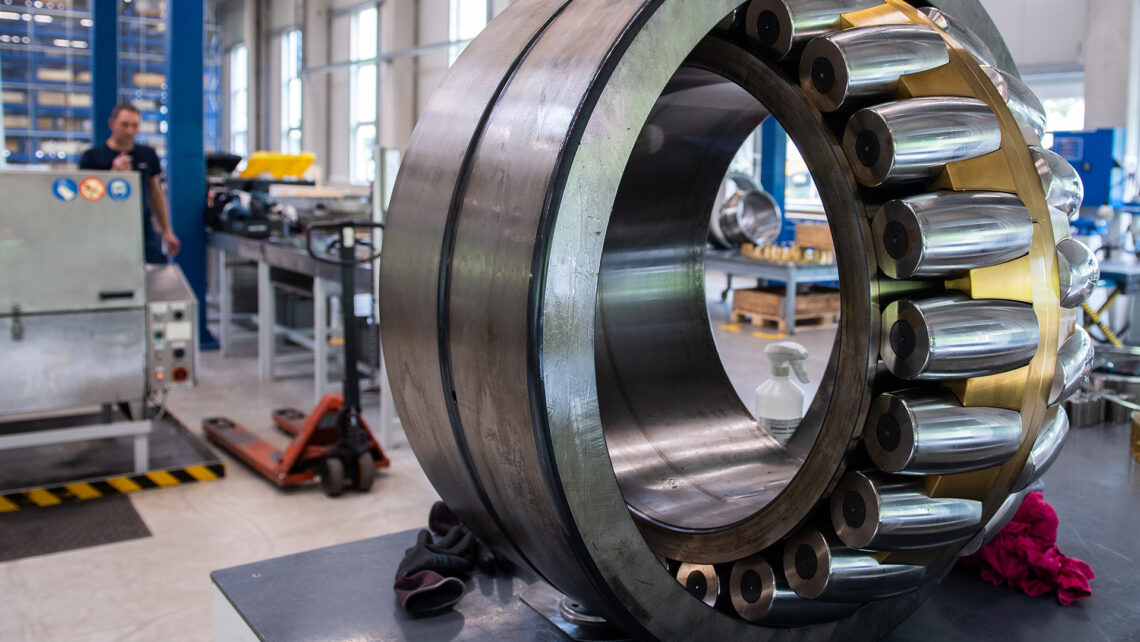
A tool for calculating saved emissions
To achieve these types of savings, remanufacturing needs to be embedded into maintenance regimens. SKF also uses an Avoided Emission Calculator, an internal app that shows the amount of CO2 emissions that are saved by purchasing remanufactured services instead of new ones. Opting for remanufacturing services reduces CO2 emissions by an average of 90 percent. But for maintenance regimens, identifying the optimum point for remanufacture of a bearing is also vital.
“The bearing cannot be worn too much,” says Leopoldseder. “Once it has failed it cannot be repaired. It must be remanufactured at a level of wear when it can be remanufactured to an ‘as new’ condition. This is a critical balancing act. Repair a bearing too soon and you’ve wasted usable life. Leaving it too long so that the bearing fails means the original product is scrap. The trick to maximizing sustainability is to remanufacture the bearing at the optimum time.”
Leopoldseder sees condition monitoring and artificial intelligence combining with remanufacturing to find this balance.
“This is happening already,” he says. “At one pulp and paper mill, large-diameter bearings incorporate sensors that monitor 700 process points. Detecting defects before they cause damage, they indicate the correct point for remanufacturing to take place.”
For the future, Leopoldseder thinks we should look to the automotive industry as an example. “When a truck engine fails, purchasers will source a remanufactured engine without any questions about quality or as-new condition,” he says. “It’s not their own engine remanufactured, but one built up of parts from different vehicles, possibly even globally sourced.
“Currently we remanufacture a customer’s own bearing and it is returned to them after remanufacturing,” continues Leopoldseder. “If remanufactured bearings were a ‘product’ like truck engines, then costs could potentially be lower and short lead times, one of the most important original drivers behind remanufacturing, could be effectively achieved.”
Cutting CO2 emissions
Remanufacturing and reusing bearings with a total weight of 600 kilograms can reduce CO2 emissions by one tonne and lower a manufacturer’s carbon footprint by up to 90 percent when compared with buying new bearings.
From a sustainability point of view, it is not just about reuse and recycle but also a reduction in the manufacturing processes required. Whereas manufacturing a new bearing involves 100 processes, remanufacturing takes just 10.
Global remanufacturing increases
In April 2022, SKF began building its second Circular Economy Centre in Kiruna, Sweden. It will serve customers in northern Sweden in the mining, steel, railway and paper industries. The reason for the new centre was the increasing demand for remanufactured bearings.
SKF’s first Circular Economy Centre opened in Gothenburg, Sweden, in 2020. It’s a local unit enabling circular solutions close to the customers, with a capacity of remanufacturing 13,000 bearings per year. It focuses not only on the remanufacturing of bearings but also, importantly, on the remanufacturing of bearing units, bearing housings, sealings and lubrication management. Sales have quadrupled in two years and demand continues to increase.
The remanufacturing centres offer customers a comprehensive service that quantifies green value, such as reduced energy consumption, CO2 impact and lubricant consumption, as well as economic value, such as increased productivity and reduced costs.
SKF has more than 15 remanufacturing centres globally.
How to know your CO2 reductions
As more and more customers consider environmental footprint when they choose suppliers, SKF Remanufacturing Services comes with a technical inspection report of the product, documented CO2 emission reduction and a warranty that is virtually the same as for a new bearing.
SKF has also developed an Avoided Emission Calculator, an app that can easily show the amount of CO2 emissions that are saved by purchasing remanufactured services instead of new ones. Opting for remanufacturing services reduces CO2 emissions by an average of 90 percent. And when customers select SKF Remanufacturing Services and send their units to SKF, they receive documentation from the app that shows them how they are contributing to the circular economy.