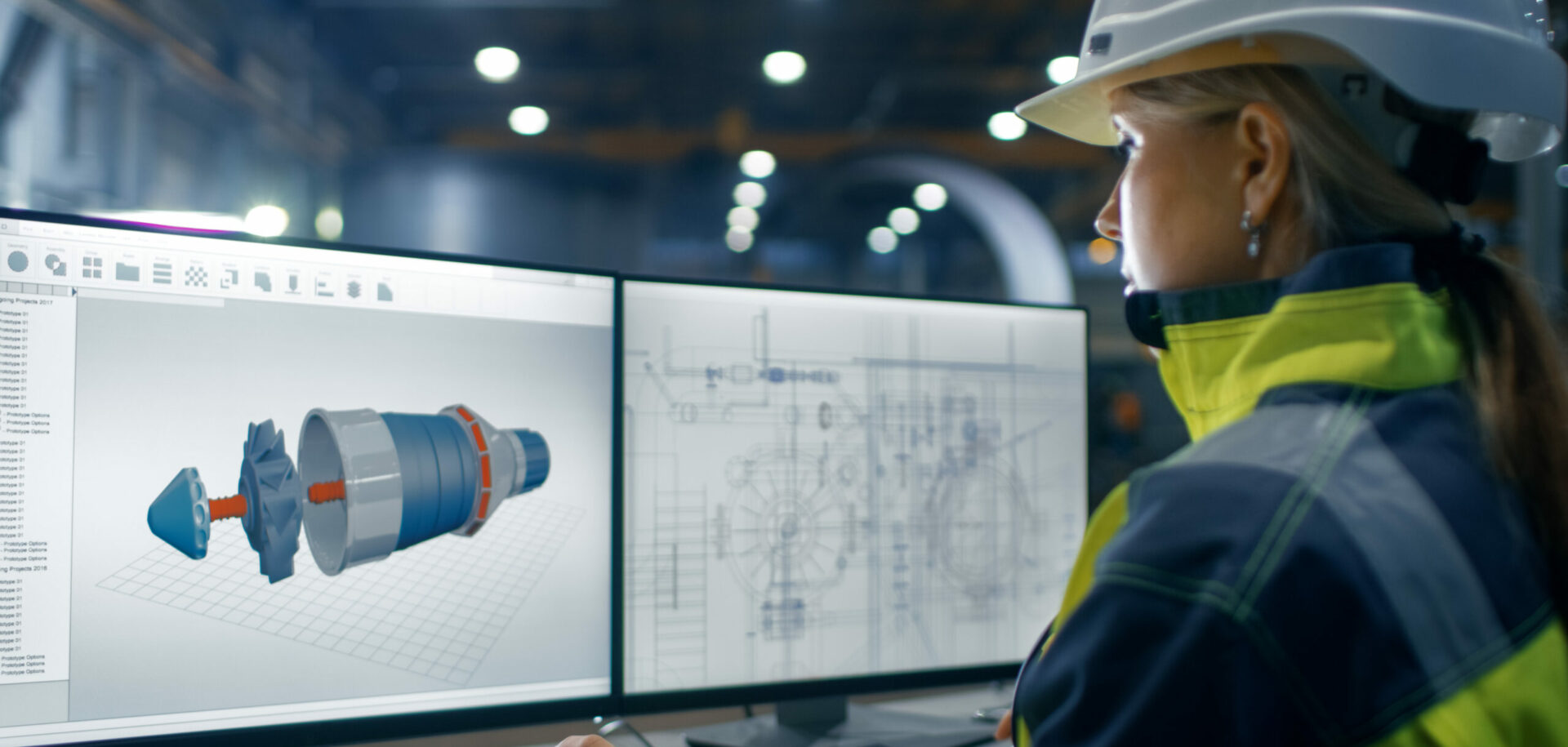
Research up front
Research centres are often regarded as hotbeds of learning with little relevance to the real world. But the researchers at SKF’s international research facility at Nieuwegein near Utrecht in the Netherlands keep their eyes firmly on the end customer.Henning Wittmeyer, managing director of SKF Engineering & Research Centre, ERC, explains that he and his staff exercise up front thinking, evaluating the potential business benefits of any project before work begins. Wittmeyer does point out that while long-term research also has a place within ERC – most importantly, with its close links with universities around the world – emphasis is strongly towards developments which will result in products being on the market within five years.
Summary
ERC is an SKF Group resource, consulted when new solutions or extensive testing is necessary. SKF is set on strengthening its leadership in core products – bearings and seals. ERC is always aware of the commercial implications of its research and the importance of quality, service and cost to the industry.
Improving SKFs own manufacturing processes benefit the customer with improved quality, faster delivery, greater flexibility and cost-effectiveness, coupled with an environmental approach.
Research focuses on materials, bearing materials and treatment, bearing theory and testing, process control and information systems.
Research centres are often regarded as hotbeds of learning with little relevance to the real world. But the researchers at SKF’s international research facility at Nieuwegein near Utrecht in the Netherlands keep their eyes firmly on the end customer.Henning Wittmeyer, managing director of SKF Engineering & Research Centre, ERC, explains that he and his staff exercise up front thinking, evaluating the potential business benefits of any project before work begins. Wittmeyer does point out that while long-term research also has a place within ERC – most importantly, with its close links with universities around the world – emphasis is strongly towards developments which will result in products being on the market within five years.
ERC is an SKF Group resource and much of the work, Wittmeyer says, comes at the request of the various SKF companies world-wide. Product development is normally carried out within SKF’s product divisions but ERC is usually brought into the picture when new solutions are required or when extensive testing is necessary. SKF’s manufacturing development is spearheaded by Technology Development Centres in various parts of the world. ERC is responsible for two such centres and provides knowledge and test data to the others.
Research work at ERC is focused on four broad areas:
- materials
- bearing materials and treatment
- bearing theory and testing
- process control and information systems
Tribology is a particular SKF strength and fundamental research has provided greater understanding of the effects of friction, wear, lubrication and contamination on bearing life.
Heading up this area of work is Stathis Ioannides, who is not only ERC’s technical director of Product Research and Development but also a professor at Imperial College, London. Ioannides was also the main researcher who in 1984 made a significant contribution to the development of the New Life Theory for bearing life prediction which improved the original life theory developed by SKF in 1947.
Bearing grease lubrication is another area of research. This is the performance of the thin lubricating film provided by the oil in the grease, dictates the success of bearing operation.
At ERC, there is a constant search for the optimum grease for a particular application. As a result of this work, SKF has been able to meet customers’ needs by creating a range of proprietary products to meet the specific requirements of the operating conditions.
Quiet running greases
Particular areas of interest are the development and qualification of greases for highly demanding environments such as in Hub Units, compact alternators and high speed traction motor bearings as well as the selection of quiet running greases for electric motor applications. ERC developed a special test rig for assessing the quiet characteristics of greases which is now used by many grease manufacturers.
Research covers the investigation of alternative steel grades and other metallic materials, characterising their behaviour after treatments by mapping phase transformations and relating this to the required structure and properties. Systematic studies of material response to rolling contact loading also provides an opportunity for material and product development. For example, internal friction through micro-plastic deformation is one of the factors that controls the structural degradation of the sub-surface material in rolling contact fatigue.
ERC is also engaged in field studies to assess the performance of bearings in applications, wear patterns, failure modes, metallurgical characteristics etc., which directly impinge upon bearing development.
Hybrid bearings
Among recent developments hybrid bearings, with steel rings and ceramic balls have already found important markets for specific applications. For ceramic materials, mainly silicon nitride, improvement work at ERC is generally focused on process development and quality assurance.
Material quality activities include structural analysis and the assessment of mechanical properties such as toughness and hardness parameters.
Research on bearing theory is based heavily around computational mechanics
– mathematical models which can simulate the various systems and their individual components. These models provide information about the following areas:
- a bearing considered as a system, including the rings, rollers, cages, etc.
- a bearing as a part of a machine, including multiple bearings on a shaft
- complete structures, including bearings, shafts and housings etc.
Finite Element and Multi-Grid are also techniques which are applied to a wide range of analyses from the micro-contacts in a bearing to contamination effect simulation and plastic forming in manufacturing processes.
In addition, these mathematical models have led to the development of a number of bearing programs including CADalog for bearing selection, but also bearing analysis programs for high speed bearing systems and multiple bearing shaft assemblies. Other programs can evaluate flexing of housings and friction torque against load, speed and lubrication conditions.
The real thing
However, the theoretical work also carries through to practical testing carried out by the team in Bearing Theory & Testing. G÷sta Norlander, the team’s manager, describes his laboratory testing work as ôas close as possible to the real thing.ö He and his colleagues are constantly looking for better ways to test bearings and to reproduce in a laboratory the conditions that bearings will experience in real life.
Seals are vital to the overall performance of bearings in many applications. ERC has technology to analyse sealing pressures and temperature distribution and the effects of sealing surface roughness on film formation and friction. Using advanced non-linear finite element and stability analysis, ERC carries out seal modelling to predict seal life, rubber ageing, leakage and film formation. Supporting theoretical work on seals, ERC has developed a range of sophisticated rigs capable of testing seal lip contact forces, seal wear, and oil flow through seals. Water and dust ingress can also be measured by special test rigs designed to reproduce application environments such as for railway axle boxes and car wheel hub units.
Strengthen leadership
SKF has set its sights on strengthening its leadership in its core products – bearings and seals. This then puts the pressure on ERC to be continually aware of the commercial implications of its research and to understand the factors that drive the industry as a whole such as quality, service and cost.
This is why process technologies play an important role for ERC. Increasing emphasis is placed on areas such as computer integrated manufacturing, CIM, and the development of vision systems for use in quality control.
The fine tolerances required for bearings and the very low frequency of flaws from modern bearing manufacturing mean that human inspection alone is no longer sufficiently reliable. ERC’s development work on process control and high speed inspection systems support the SKF Group’s continuous push for higher and higher quality levels.
Environmental care
Of course, the improvement of SKF’s own manufacturing processes have substantial spin-offs for the customer in terms of improved quality, faster delivery, greater flexibility and cost-effectiveness coupled with an environmental approach.
For example, researchers at ERC contributed to a team effort that led to the development within SKF of environmentally-friendly manufacturing processes. Herman Lankamp, department head of Non-Metallics, explains that SKF wished to implement an “emission free concept throughout its operations, thereby removing all materials that damage the ozone layer or promote the greenhouse effect.”
Starting in 1985, ERC helped develop a water-based washing system proposed by SKF in Sweden, which eliminated the need for substances such as white spirit and Freon.
At the time, SKF was far ahead of its competition and has been steadily introducing the system to its factories world-wide. Lankamp explains that SKF is committed to achieving the same high standards of environmental care everywhere, not just in those countries where legislation demands.
SKF felt that such technology, which had so obvious benefits to the environment, should not remain solely for its own use. Therefore industrial partners have developed a commercial system which is available to other manufacturing concerns.
The SKF companies regard ERC as an important tool in developing customer relations, offering unmatched facilities, for example, in the testing of bearings for the automotive industry, a major consumer of bearings.
Bearings in automotive applications are increasingly being regarded as part of a system solution. The other components – the shaft, housing and gears – which make up a wheel hub, drive shaft or gear box assembly, influence the performance of a bearing itself. This means ERC is frequently asked to look at the implications of the overall system. System solutions also mean that, ideally, both SKF’s product companies and ERC need to be brought into the design of a new car or truck at the earliest possible stage if the final bearing design is to be fully optimised.
Exact road conditions
Some of the facilities at ERC for automotive applications include DYANA, a dynamic road simulator which can reproduce exact road conditions in terms of dynamic lateral and vertical wheel force, rotation speed, drive torque and suspension displacements. DYANA can evaluate new hub units and help resolve dynamic problems such as fretting corrosion and flange fatigue.
Structural stress analysis using both strain gauge measurement and Finite Element techniques are applied to both car and truck hub units for the optimisation of hub unit flanges with regards to strength and low weight, for example.
This broad range of activities provided by ERC helps SKF to serve the many industries in which it operates. In future issues we will cover these techniques in more depth.
Elaine Williams